Aluminum Sand Casting
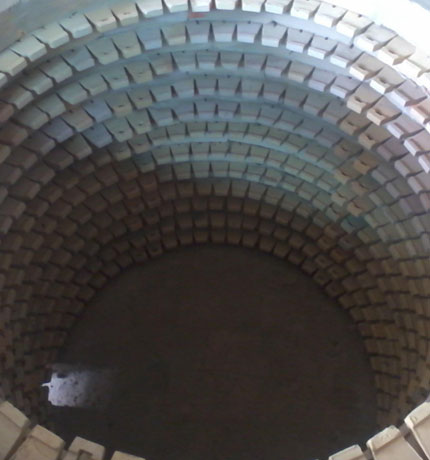
Aluminum Sand Casting – Custom Fabrication with Sand Cast Aluminum
Aluminum is a malleable silver white metal, soft and lightweight, suitable for sand casting. But for aluminum sand casting, it has unique challenges.
Sand casting is a casting method that replaces the wax mold with a sand mold. Usually, the mold is comprised of two halves that, when joined, reflect the exact negative of the shape to be cast. To make the mold, manufacturers begin by placing a die between mold frames called flasks (the top one called the cope and the bottom called the drag). Once in place, they sprinkle it with powder, then bury it under a mixture of clay and finely sifted clay. This mixture helps preserve the piece’s smooth dimensional accuracy. After this, manufacturers immerse both the cope and the drag under the rest of the sand-clay mixture. They follow this up by tightly compacting the sand, aside from at least one opening in the cope, supported by a pipe. When they’re ready, manufacturers access the mold by removing the cope and the rest of the die. With the mold, they proceed through the rest of the casting process.
Minghe Casting is a precision sand casting parts manufacturer from China, our sand casting equipments,CNC lathes, milling, machining equipment, and drilling machines are integrated with our casting, welding, forming, trimming, drilling, deburring, tapping, threading, sandblasting, polishing, vibratory finishing, pressure testing, washing, and assembly facilities, to supply efficient and complete fabrication for your custom aluminum sand casting parts. We can produce complex parts with sophisticated geometries and deep holes through aluminum sand casting and other casting.
The Application Of Aluminum Sand Casting
Sand casting, the most widely used casting process, utilizes expendable sand molds to form complex metal parts that can be made of nearly any alloy. Because the sand mold must be destroyed in order to remove the part, called the casting, sand casting typically has a low production rate. The sand casting process involves the use of a furnace, metal, pattern, and sand mold. The metal is melted in the furnace and then ladled and poured into the cavity of the sand mold, which is formed by the pattern. The sand mold separates along a parting line and the solidified casting can be removed.
Sand casting is used to produce a wide variety of metal components with complex geometries. These parts can vary greatly in size and weight, ranging from a couple ounces to several tons. Some smaller sand cast parts include components as gears, pulleys, crankshafts, connecting rods, and propellers. Larger applications include housings for large equipment and heavy machine bases. Sand casting is also common in producing automobile components, such as engine blocks, engine manifolds, cylinder heads, and transmission cases.
Process Of Our Custom Aluminum Sand Casting Services:
- Cast Aluminum Foundry
- Top Pattern And Bottom Pattern
- Sand Mould--Remove The Pattern
- Fill The Mold Cavity With Molten Aluminum
- Break Away The Sand Mould And Get The Aluminum Casting
- Finished Sand Cast Aluminum
- Complete Process
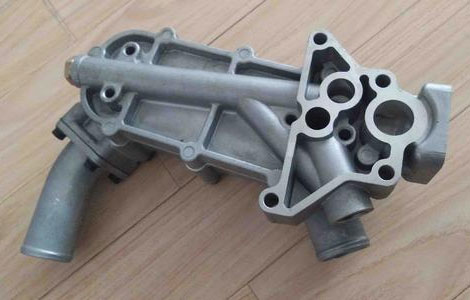
Product Description Of Our Aluminum Sand Casting Services
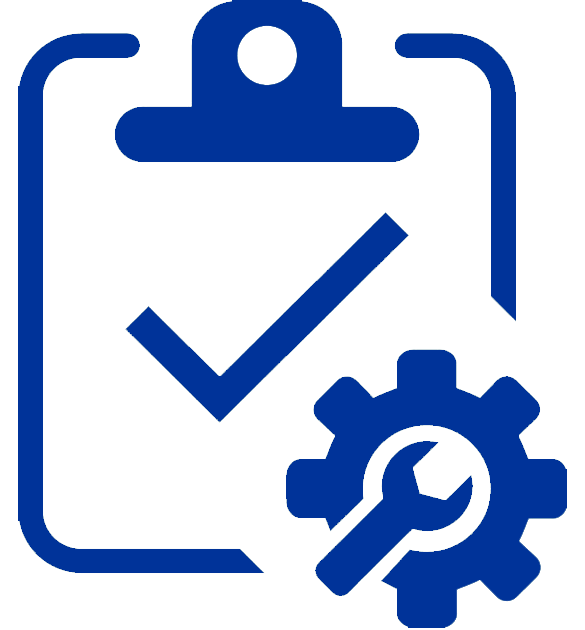
ADC 12, ADC 10,Aluminum Y102,Aluminum Y112, Aluminum Y113,AC3AM,ZLD101,Aluminium A356,
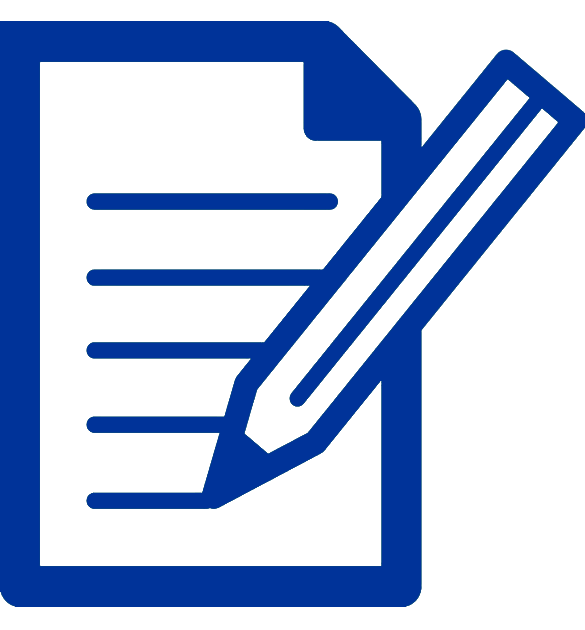
Black, Natural, Blue, Green and different colors as your requirements
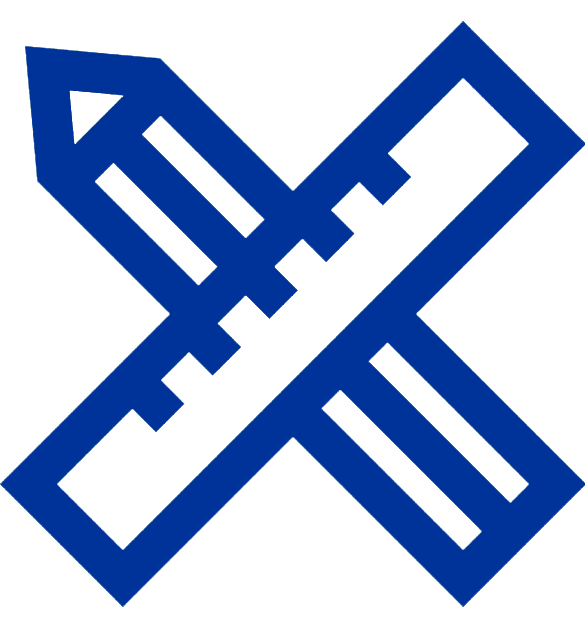
Sand blasting, shot blasting, polishing, anodizing, oxidation, electrophoresis, chromate, powder coating and painting
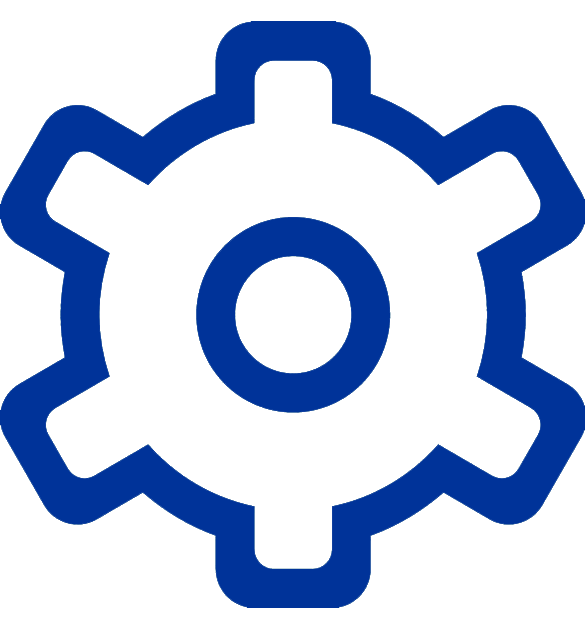
CNC aluminum milling, CNC aluminum turning, CNC aluminum drilling
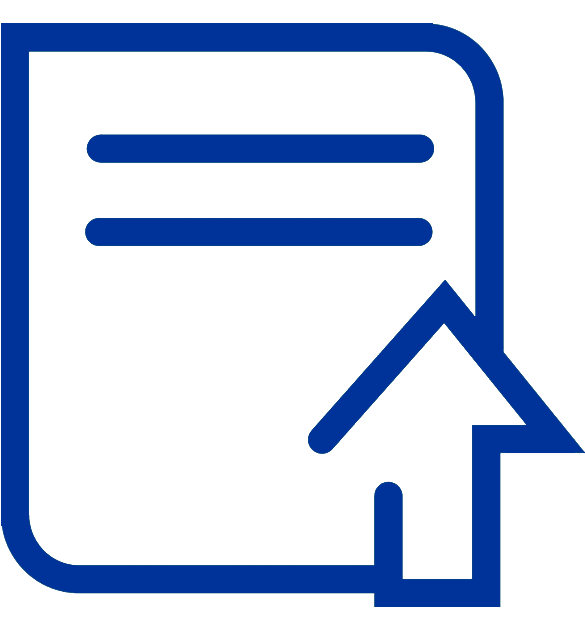
Aluminum Casting parts can be applied to automotive, electrics, military, medical, aircraft, power generation, aerospace, and industrial engineering
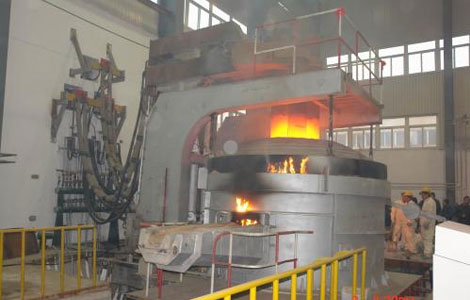
Advantages of Minghe Aluminum Sand Casting Services
- Experience, accuracy, and powerful machinery
- Relatively stable casting of aluminum
- Design and produce complex custom aluminum parts
- High production efficiency and cost saving
- Simultaneously realize various and large quantities of production
- Provides the clients with a high quality part in a comparable timeline
- Timely shipment, one-stop instant service
The Minghe Case Studies Of Aluminum Sand Casting
You have a complex part design, Minghe Casting Company can help you turn it into a reality. With the right equipment, strong technical knowledge, and a focus on quality.. From tool design to finishing and then on to shipment, Minghe Casting ensure that every project is completed to a high standard and that your orders are delivered on time, every time.
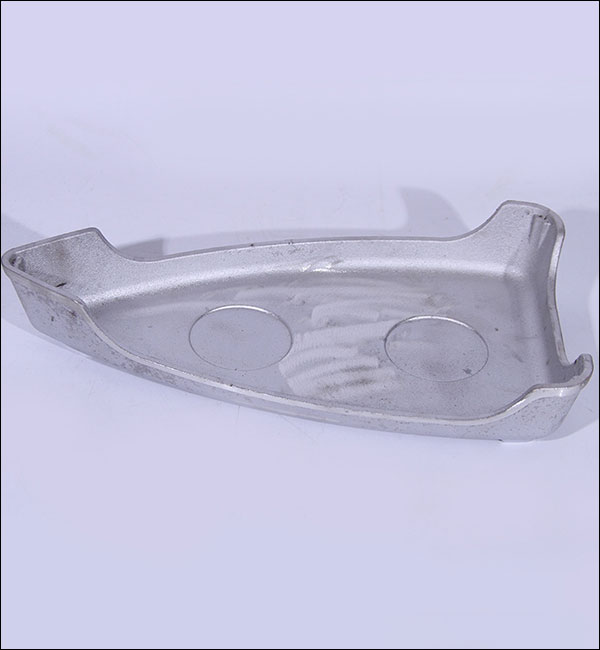
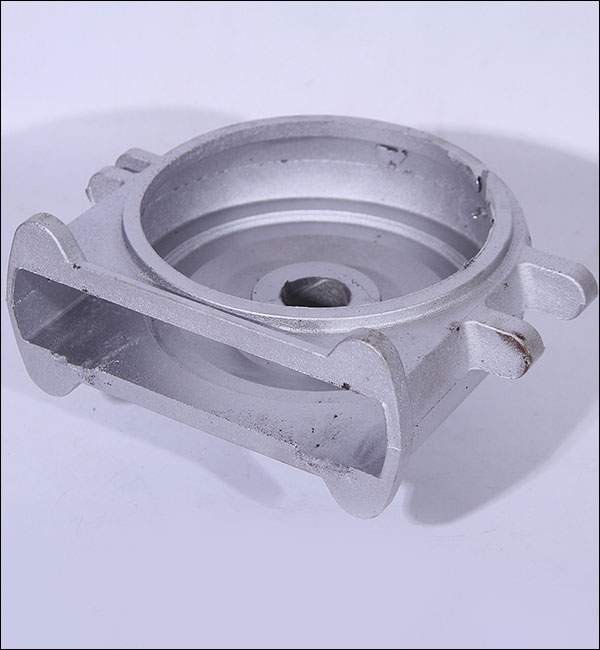
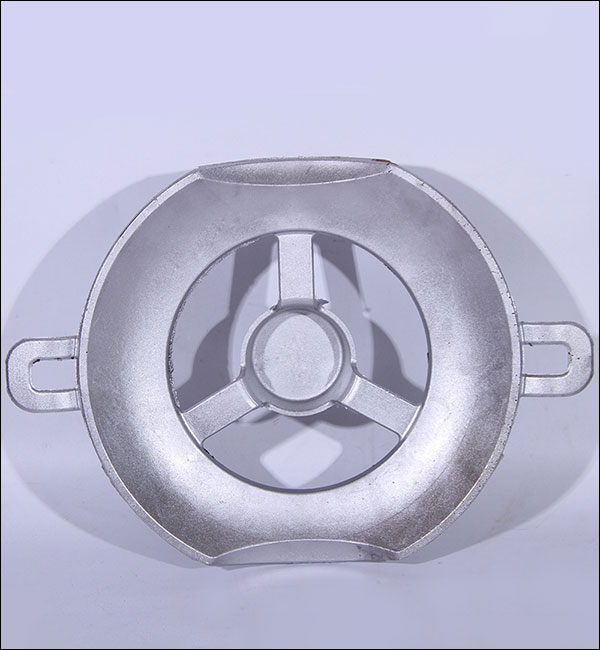
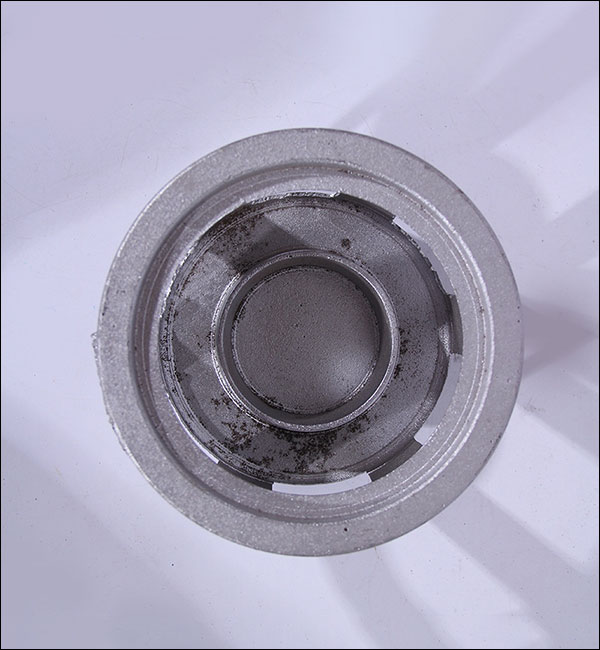
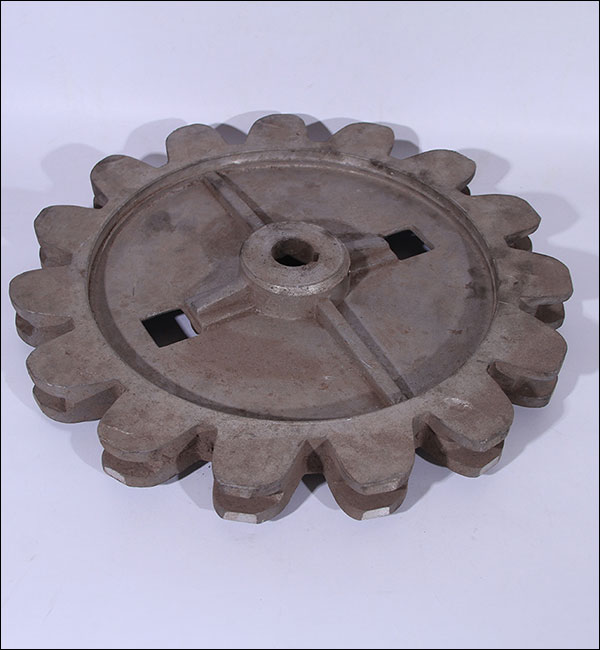
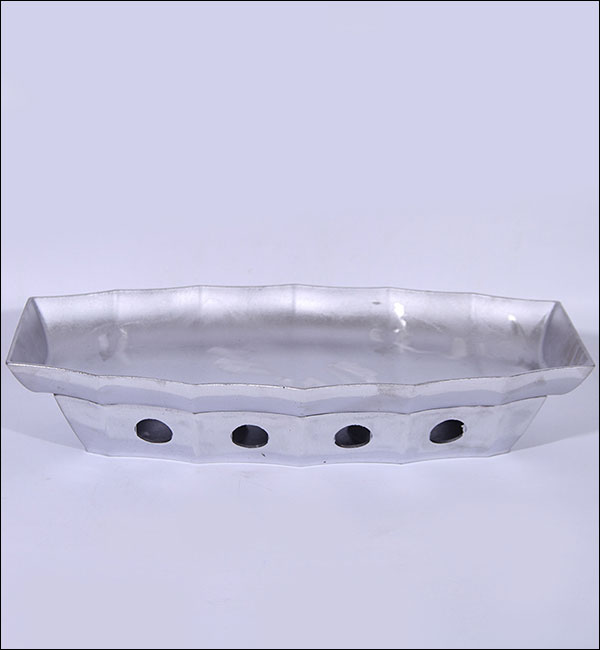
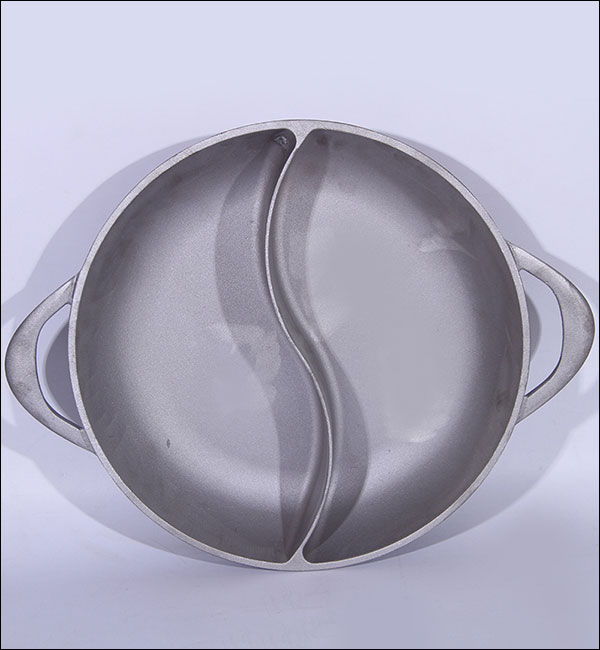
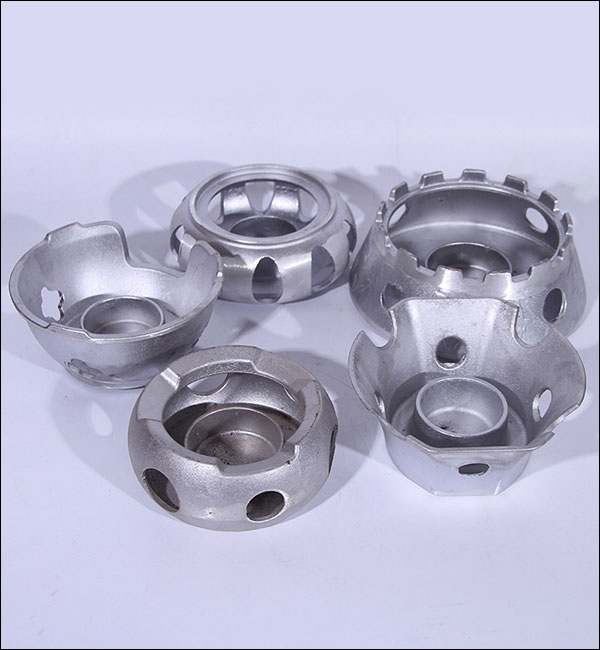
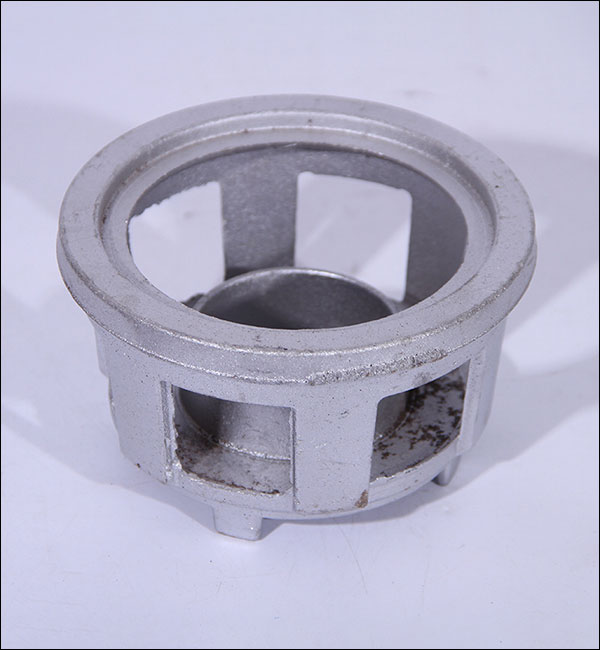
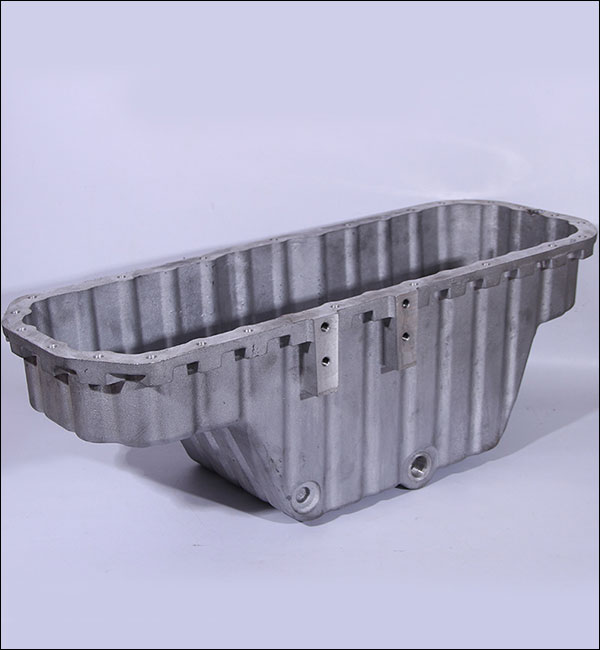
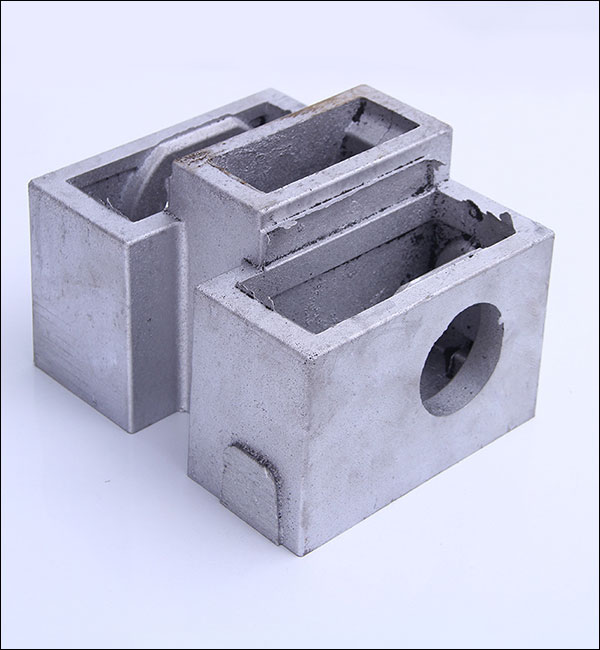
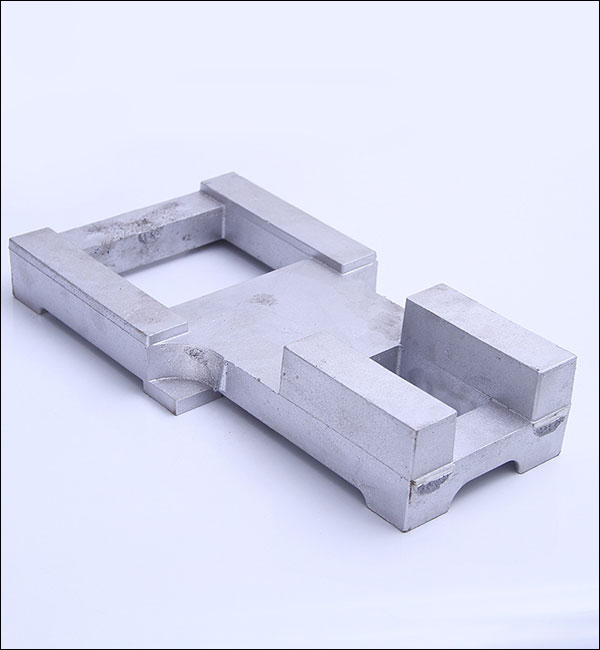
Go To View More Casting Parts Cases Studies >>>
Choose The Best Aluminum Sand Casting Service
Currently, our aluminum sand casting parts are exported to America, Canada, Australia, United Kingdom, Germany, France, Sout Africa, and many other countries all over the world. We are ISO9001-2015 registered and also certified by SGS.
Custom china casting service provides durable and affordable castings that meet your specifications for automotive, medical, aerospace, electronics, food, construction, security, marine, and more industries. Fast to send your inquiry or submit your drawings to get a free quote in the shortest time.Contact us or Email sales@hmminghe.com to see how our people, equipment and tooling can bring the best quality for the best price for your aluminum sand casting project.
We Provide Casting Services Include:
Minghe Casting services working with sand casting、metal casting 、investment casting lost foam casting, and more.

Sand Casting
Sand Casting is a traditional casting process that uses sand as the main modeling material to make molds. Gravity casting is generally used for sand molds, and low-pressure casting, centrifugal casting and other processes can also be used when there are special requirements. Sand casting has a wide range of adaptability, small pieces, large pieces, simple pieces, complex pieces, single pieces, and large quantities can be used.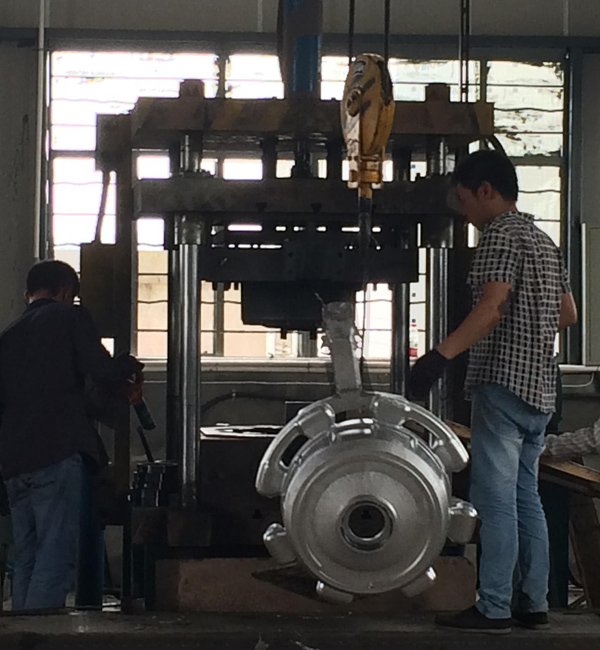
Permanent Mold Casting
Permanent Mold Casting have a long life and high production efficiency, not only have good dimensional accuracy and smooth surface, but also have higher strength than sand castings and are less likely to be damaged when the same molten metal is poured. Therefore, in the mass production of medium and small non-ferrous metal castings, as long as the melting point of the casting material is not too high, metal casting is generally preferred.
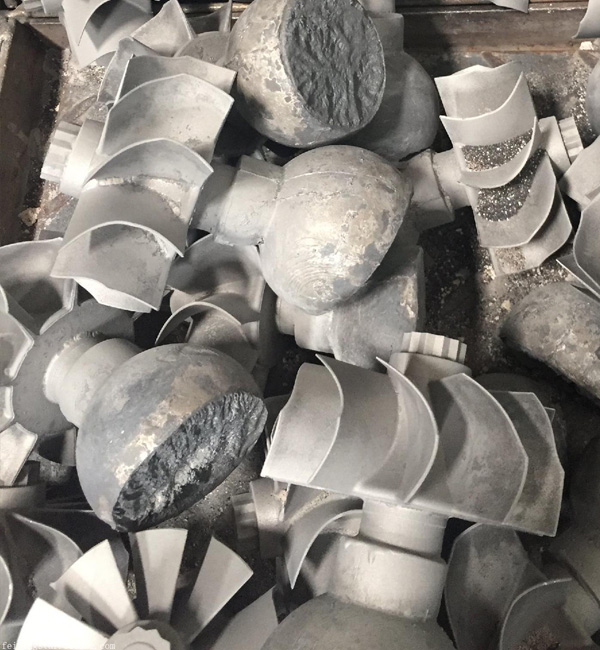
Investment Casting
The biggest advantage of investment casting is that because investment castings have high dimensional accuracy and surface finish, they can reduce machining work, but leave a little machining allowance on the parts with higher requirements. It can be seen that the use of investment casting method can save a lot of machine tool equipment and processing man-hours, and greatly save metal raw materials.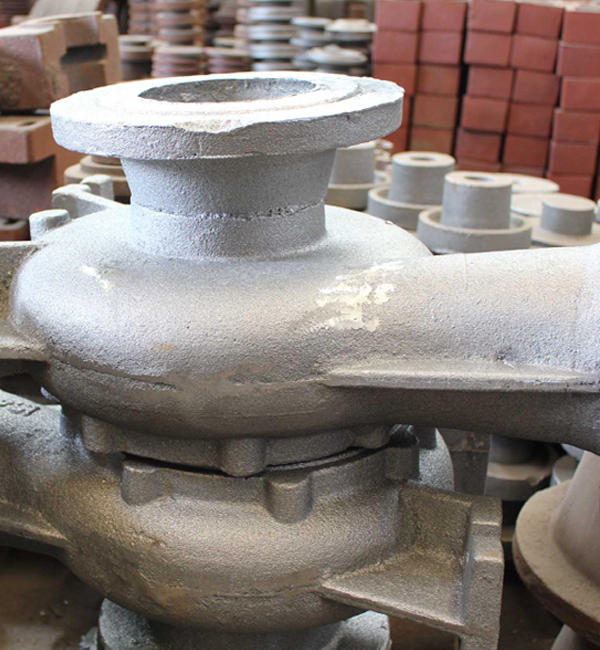
Lost Foam Casting
Lost foam casting is to combine paraffin wax or foam models similar to the casting size and shape into model clusters. After brushing and drying refractory coatings, they are buried in dry quartz sand for vibration modeling, and poured under negative pressure to gasify the model. , The liquid metal occupies the position of the model and forms a new casting method after solidification and cooling.

Die Casting
Die casting is a metal casting process, which is characterized by applying high pressure to the molten metal using the cavity of the mold. Molds are usually made of higher-strength alloys, and this process is somewhat similar to injection molding. Most die castings are iron-free, such as zinc, copper, aluminum, magnesium, lead, tin, and lead-tin alloys and their alloys. Minghe has been China's top die casting service since 1995.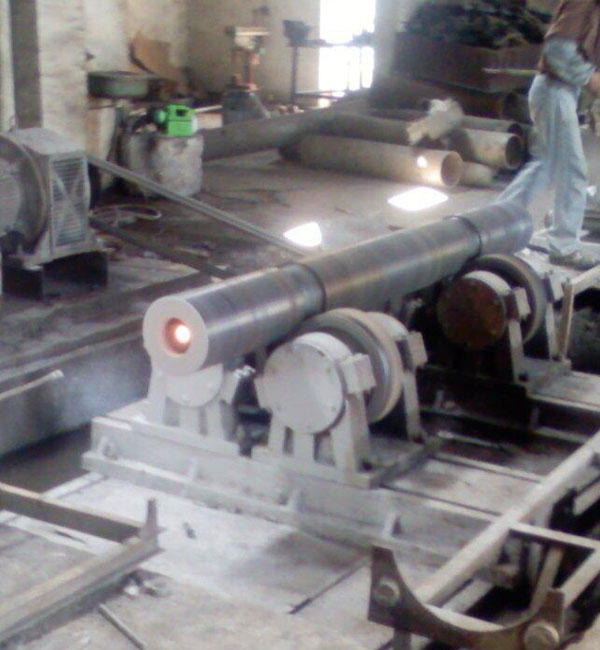
Centrifugal Casting
Centrifugal Casting is a technique and method of injecting liquid metal into a high-speed rotating mold, so that the liquid metal is centrifugal motion to fill the mold and form a casting. Due to the centrifugal movement, the liquid metal can fill the mold well in the radial direction and form the free surface of the casting; it affects the crystallization process of the metal, thereby improving the mechanical and physical properties of the casting.
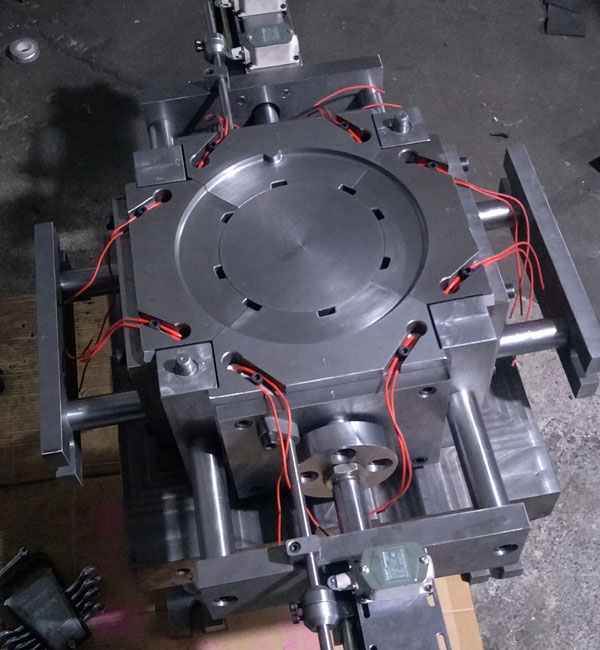
Low Pressure Casting
Low Pressure Casting means that the mold is generally placed above a sealed crucible, and compressed air is introduced into the crucible to cause a low pressure (0.06~0.15MPa) on the surface of the molten metal, so that the molten metal rises from the riser pipe to fill the mold and control Solidified casting method. This casting method has good feeding and dense structure, easy to cast large thin-walled complex castings, no risers, and a metal recovery rate of 95%. No pollution, easy to realize automation.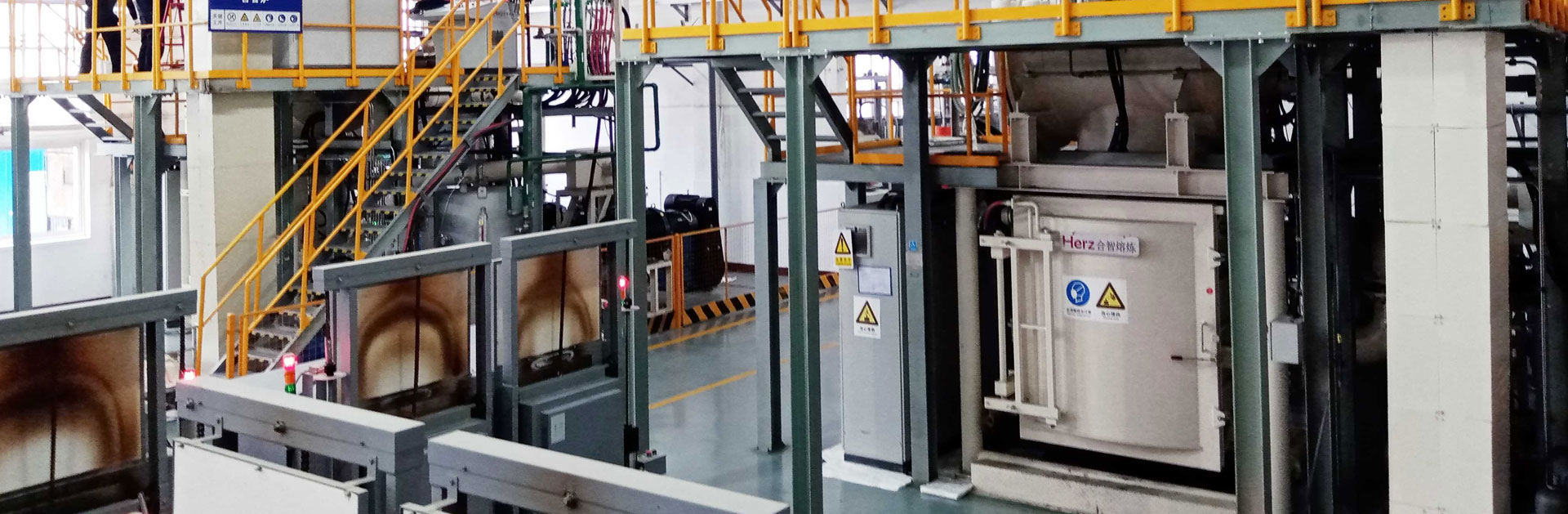