Assembly And Testing
ASSEMBLY AND TESTING
The Advance Of Minghe Assembly
Minghe Die Casting offers flexible, cost-effective turnkey solutions with integrated sub-assembly production and finished production-ready assemblies.
We at MINGHE CASTING have the facilities and expertise to do many types of assembly and testing. Product Assembly is ensured to maintain the highest standard of quality, as well as efficient turn around times utilizing assembly lines for large quantities.
From simple mechanical assembly and pressure testing, to electrical assembly and testing with a network analyzer. This will allow you to purchase a finished product rather than just a component.
Electronic test equipment is used to create stimulus signals and capture responses from electronic Devices. The proper operation of the electronic device can be confirmed or flawed in the device, which can be traced and repaired. Use of electronic test equipment is essential for any type of work on electronics systems.
![]() |
![]() |
![]() |
![]() |
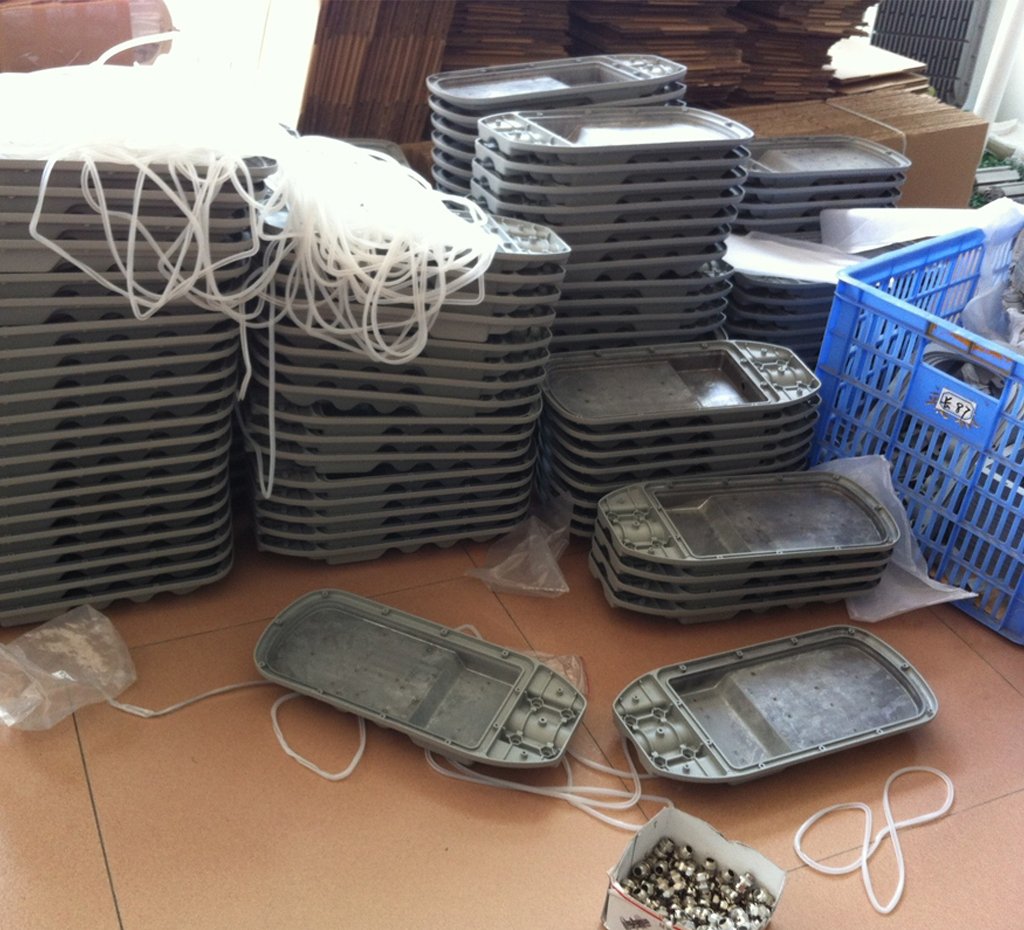
Our Attempts And Efforts For More Convenient Assembly
Whether you need simple hardware insertion or complicated mechanical assembly, Minghe Die Casting can provide time saving, cost effective services for your project. We manage your complete project from prototyping, die casting, machining, stock procurement, and assembly. We can also provide kitting of sub-assembled parts for your production line and repair kits. From small mechanical sub-assemblies to complex electro-mechanical enclosures, we tailor assembly solutions to your exact needs.
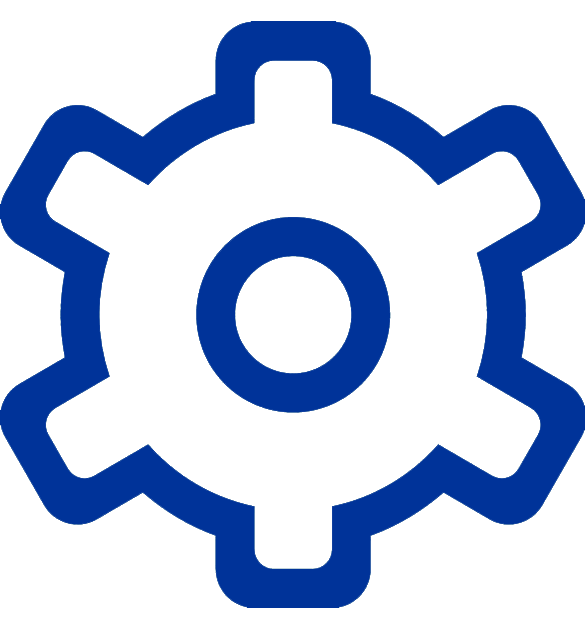
1. The Structure Of Die Casting
With the wide application of CNC machining technology, the complexity of the structure of die castings continues to increase. In the processing of some die castings, positioning and clamping are very difficult, and they are not suitable for multiple positioning and clamping. The one-time forming technology of overall machining is to rotate and turn the worktable according to the angle on the horizontal or vertical-horizontal conversion machining center machine tool to process all the faces and holes of the die-casting part at one time, and then meet all the geometric tolerance requirements of the drawing. The part connected with the process handle is layered and milled to separate the process handle from the workpiece.
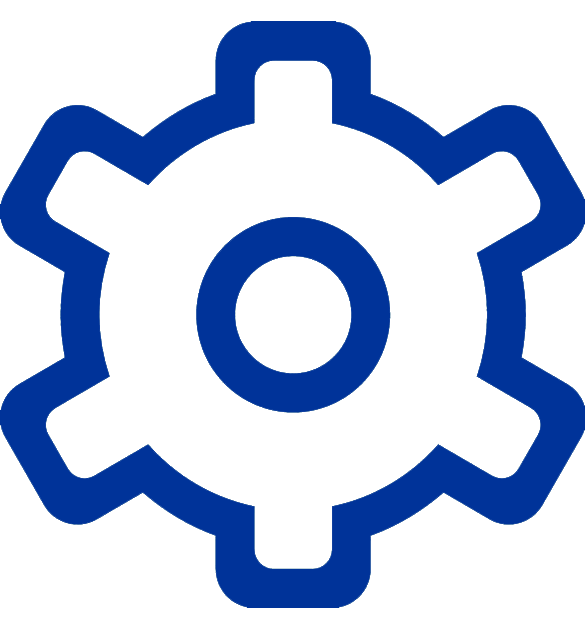
2. Processing Principle
Take full advantage of the multi-angle and omni-directional processing advantages of the CNC machining center, use the characteristics of the carbide milling cutter to process parts with low deformation at high speed and small feed, use the residual part of the profile part as the positioning and pressing process handle, and use the UG software to automatically The programming function ensures the consistency of the overall processed parts and the good cohesion of all sides.
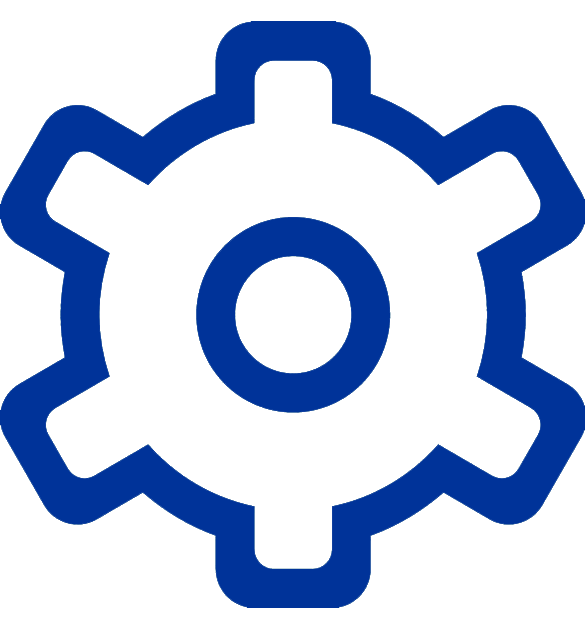
3. Implementation Effect
Die-casting parts adopt integral machining and one-time forming technology. When the die-casting parts are mass produced, after three-coordinate inspection, the statistical data of shape and position accuracy are as follows: K base plane flatness ≤ 0.012mm, M base plane flatness ≤ 0.01mm, M backside parallel The degree of ≤0.015mm, the perpendicularity of φ30mm to the base of M is ≤0.013mm, the perpendicularity of φ32mm to the base of K is ≤0.015mm, the intersection of φ30mm and the axis of φ32mm is ≤0.014mm. In mass production, the shape and position accuracy of parts is stable, and the production efficiency is greatly improved.
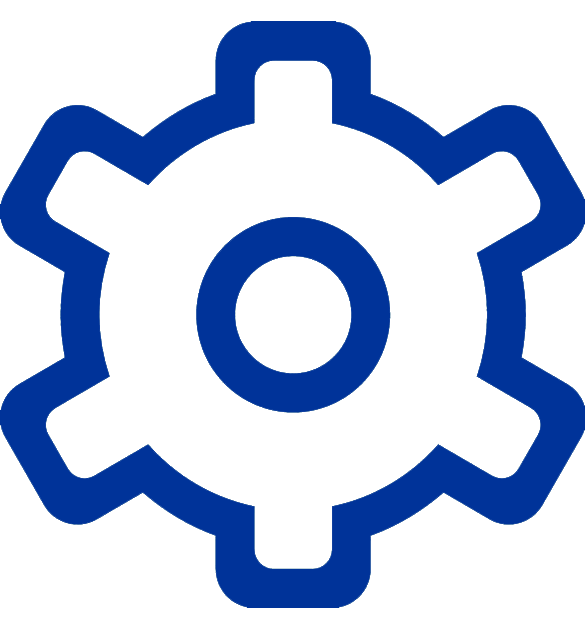
4. Application And Expansion
The one-time forming process technology of integral machining of parts can be used not only in horizontal machining centers, but also in vertical and vertical-horizontal conversion machining centers. Die-casting parts can be processed and formed in one step on a five-axis machining center, and the process handles can be milled in layers; die-casting parts can be processed by an inverted plate on a three-axis machining center. To remove the residual process platform.
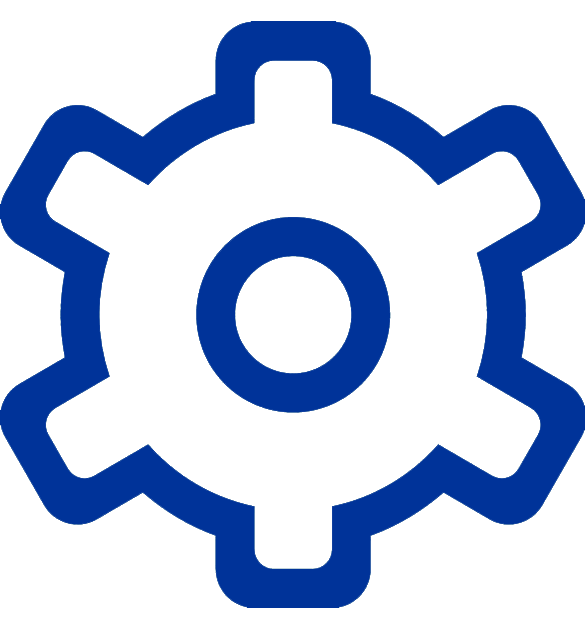
5. The Application Of Overall Machining
The one-time forming process technology of integral machining of parts is mainly used in the processing of parts with difficult positioning and clamping. The processing procedures can be combined to improve work efficiency and ensure the accuracy of shape and position; it can be used for paired cutting of symmetrical structure parts to reduce the number of clamping , Saving tooling production costs; suitable for high-speed and small-feed scanning processing layer by layer, the cutting force is small, the cutting heat is small during processing, and the die-casting parts are not prone to stress deformation. This processing concept is gradually being promoted in die-casting factories.
Our Measuring Equipment List
![]() |
|
![]() |
|
![]() |
|
![]() |
|
![]() |
|
![]() |
|