What is Metal Deburring Process - Deburring Services
Deburring is to remove the thorns or flashes formed at the intersection of the part surface and the surface. Some of the burrs on mechanical parts are caused by plastic deformation during the cutting process; some are flash from casting and die forging, and some are leftovers from welding and extrusion. With the improvement of industrialization and automation, the mechanical processing field, especially in the fields of aviation, aerospace, and instrumentation, has increased the manufacturing precision requirements of mechanical parts and the miniaturization of mechanism design. The harmfulness of burrs is particularly obvious, which gradually arouses people’s concerns. General attention, and began to study the generation mechanism and removal methods of burrs.
The machining methods of mechanical parts can be roughly divided into material removal processing, deformation processing, additional processing and so on. In all kinds of processing, the extra part derived from the processed part that does not conform to the required shape and size is the burr. The generation of burrs varies with the processing method. According to different processing methods, burrs can be roughly divided into:
- Casting burr: The excess material generated at the joint of the mold or the root of the gate. The size of the burr is generally expressed in millimeters.
- Forging burr: It is caused by the plastic deformation of the forging material at the joint of the metal mold. Electric welding and gas welding burrs: electric welding burrs are the burrs on the surface of the part that the filler at the weld protrudes; gas welding burrs are the slag that overflows from the incision when the gas is cut off.
- Punching burrs: When punching, there is a gap between the punch on the die and the lower die, or there is a gap between the cutting tools at the cut, and burrs are generated due to die wear. The shape of the punching burr varies according to the material of the plate, the thickness of the plate, the gap between the upper and lower dies, and the shape of the punched part.
- Cutting burrs: machining methods such as turning, milling, planing, grinding, drilling, and reaming can also produce burrs. The burrs produced by various processing methods have different shapes with different tools and process parameters. Plastic molding burr: Like casting burr, burr produced at the joint of plastic mold.
The existence of burrs will cause the entire mechanical system to fail to work normally, reducing reliability and stability. When the machine with burrs performs mechanical motion or vibration, the burrs that fall off will cause the machine's sliding surface to wear prematurely, increase noise, and even cause the mechanism to jam and malfunction; some electrical systems may be caused by burrs when moving with the host. Falling off causes the circuit to be short-circuited or the magnetic field is damaged, which affects the normal operation of the system; for hydraulic system components, if the burr falls off, the burr will exist in the tiny working gap of each hydraulic component, causing the slide valve to jam, and the circuit or filter screen is blocked. As a result, accidents can also cause fluid turbulence or laminar flow, which reduces the performance of the system. Japanese hydraulic experts believe that 70% of the reasons that affect the performance and life of hydraulic parts are caused by burrs; for transformers, the core loss of the burr is 20 to 90% higher than that of the burr removed core, and it increases with the increase in frequency. . The existence of burrs also affects the assembly quality of the mechanical system, the processing quality of the subsequent processing procedures of the parts and the accuracy of the inspection results.
Today, customers utilize our industry leading deburring services even when forming is not needed. For 35 years, we have been evolving our deburring services to provide customers with the right solutions to their specific application. Minghe facility is outfitted with a full range of cryogenic deburring systems to support manufacturers from prototype stages to large production runs.Minghe engineers will review the product specifications, material call outs and volume requirements to select the most cost effective solution for your deburring project.
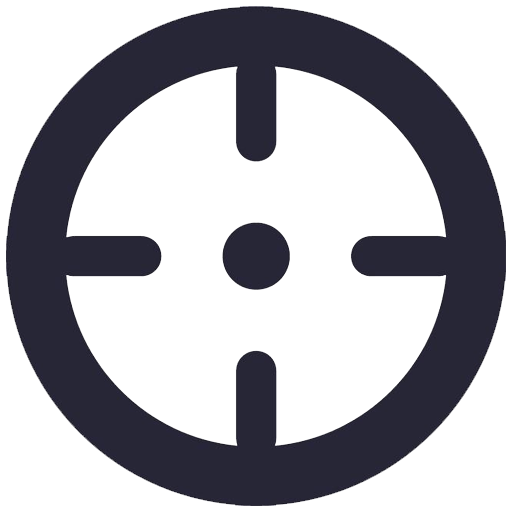
How do we deburr the parts?
Minghe Casting® Deburring is proud to offer ISO 9001 compliant contract deburring services for the removal of machine burrs in die casting and select metals. as follows:
- – Chemical deburring: Use the principle of electrochemical reaction to automatically and selectively complete the deburring of parts made of metal materials. It can be widely used in the deburring of pump bodies, valve bodies, connecting rods, plunger needle valve parts and other parts of different metal materials in pneumatic, hydraulic, engineering machinery, nozzle oil pumps, automobiles, engines and other industries. It is suitable for hard-to-remove internal burrs, heat-treated and finished parts.
- – We offer multiple cryogenic processes to remove machine burrs. The formation, location and intensity of the burr requiring removal will determine which deburring process is the most ideal fit.
- – Our Cryogenic Deburring process utilizes tumbling, freezing and a cryogenic-grade PC media blasting to remove burrs from CNC machined parts.
- – The Cryogenic Tumble Deburring process removes burrs on the external geometry of machined parts through freezing and tumbling without the use of media blasting.
- – In addition, our Dry Ice Deburring process removes hard to reach burrs via high pressure blasting of dry ice as a media. This form of deburring is used on high value parts since only one part can be processed at a time.
- – Manual deburring
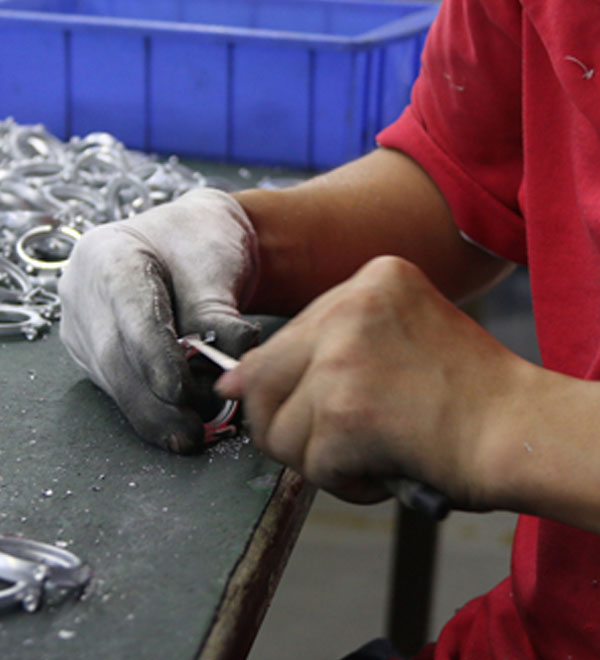
Different Types of Metal Finishes – Surface Treatment Services Available at Minghe
Do you want your die casting parts to be more corrosion-resistant or get a specific look? Metal finishing service is a essential choice to achieve your design perfectly. Minghe is an accomplished finished parts manufacturer, our workers and craftsman are capable to provide precision die casting services and a wide range of finishing services including aluminum anodizing, painting, passivation, electroplating, powder coating, polishing, black oxide, conversion coating, abrasive blasting, etc. Here are the introductions to different types of metal finishes, more details please feel free to contact us.
Powder coating/Powder coat ▶ |
Bead blasting/Bead blast ▶ |
Abrasive blasting/sandblasting▶ |
Choose the Best Deburring Process
After browsing a list of Surface Treatment services, select a process based on essential considerations, like production time, cost-effectiveness, part tolerance, durability and applications. High-tolerance CNC milling, turning parts are not recommended to apply secondary metal surface finish, because the treatment may change the sizes of the finished part through removing or adding a small amount of materials.
Contact us or Email sales@hmminghe.com to see how our people, equipment and tooling can bring the best quality for the best price for your deburring project.