10 Principles Of Die Design Classification Type
1. Consideration of clamping force
The lateral clamping force of the mold is relatively small, so for large products with a larger projected area, the direction of the larger projected area should be placed in the front and rear mold opening and closing directions, and the smaller side projected area should be used as the side To type.
2. Meet product demoulding requirements
The parting surface is for the product to be removed from the mold smoothly. Therefore, the position of the parting surface should be selected at the part with the largest cross-sectional size of the product, which is the most basic principle.
3. The shape of the parting surface
General products often use a parting surface perpendicular to the opening movement direction of the injection molding machine, and only use other shapes of parting surfaces under special circumstances. The shape of the parting surface is based on the principle of convenient processing and demolding. Like a certain curved product, the parting must be based on its curved curvature.
4. Ensure product appearance and quality
Do not choose the parting surface on the smooth outer surface of the product. Generally speaking, the appearance surface is not allowed to have lines and other lines that affect the appearance; for some products with concentricity requirements, all the parts with concentricity requirements must be placed on the same side, so as to ensure their concentricity.
5. Determination of orientation
When determining the position of the product inside the mold, the selection of the parting surface should try to prevent the product from forming side holes or side buckles, and avoid using complex mold structures.
6. Conducive to demolding
Generally, the demolding mechanism of the mold is in the movable mold, so when selecting the parting surface, the product should be left in the movable mold as much as possible after the mold is opened. Therefore, for some places that may stick to the fixed mold, we often add a fixed mold auxiliary demoulding mechanism.
7. Consider the lateral mold opening distance
Generally, the distance of lateral mechanical mold opening is relatively small. Therefore, when selecting the parting surface, the long direction of the core pulling distance should be selected in the direction of opening and closing of the front and rear molds, and the short direction should be regarded as the lateral parting.
8. Mould parts are easy to process
When selecting the parting surface, the mold should be divided into easy-to-process parts to reduce the difficulty of machining.
9. Conducive to exhaust
When the parting surface is used as the main exhaust, the parting surface should be designed at the end of the plastic flow to facilitate the exhaust.
10. R typing
For many products of mold design parting, there is a full circle of R angle at the parting surface. At this time, the parting must consider the best parting of R, and no sharp side can appear.
Related Page:Mold Manufacturing
Related Articles:
- The Key Points Of Aluminum Alloy Die Casting Design
- Shell Body Die Casting Process Design
- The Design Of Multi-Station Progressive Die
- The Design Detail Of Aluminum Alloy Shell Die Casting Tooling
Please keep the source and address of this article for reprinting: 10 Principles Of Die Design Classification Type
Minghe Die Casting Company are dedicated to manufacture and provide quality and high performance Casting Parts(metal die casting parts range mainly include Thin-Wall Die Casting,Hot Chamber Die Casting,Cold Chamber Die Casting),Round Service(Die Casting Service,Cnc Machining,Mold Making,Surface Treatment).Any custom Aluminum die casting, magnesium or Zamak/zinc die casting and other castings requirements are welcome to contact us.
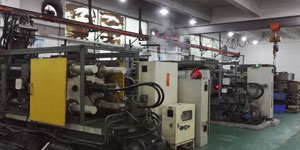
Under the control of ISO9001 and TS 16949,All processes are carried out through hundreds of advanced die casting machines, 5-axis machines, and other facilities, ranging from blasters to Ultra Sonic washing machines.Minghe not only has advanced equipment but also have professional team of experienced engineers,operators and inspectors to make the customer’s design come true.
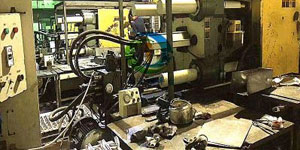
Contract manufacturer of die castings. Capabilities include cold chamber aluminum die casting parts from 0.15 lbs. to 6 lbs., quick change set up, and machining. Value-added services include polishing, vibrating, deburring, shot blasting, painting, plating, coating, assembly, and tooling. Materials worked with include alloys such as 360, 380, 383, and 413.
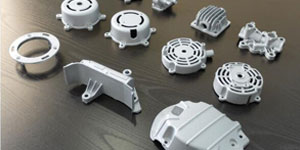
Zinc die casting design assistance/concurrent engineering services. Custom manufacturer of precision zinc die castings. Miniature castings, high pressure die castings, multi-slide mold castings, conventional mold castings, unit die and independent die castings and cavity sealed castings can be manufactured. Castings can be manufactured in lengths and widths up to 24 in. in +/-0.0005 in. tolerance.
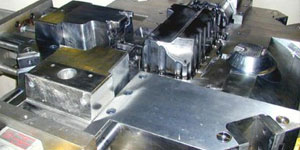
ISO 9001: 2015 certified manufacturer of die cast magnesium, Capabilities include high-pressure magnesium die casting up to 200 ton hot chamber & 3000 ton cold chamber, tooling design, polishing, molding, machining, powder & liquid painting, full QA with CMM capabilities, assembly, packaging & delivery.
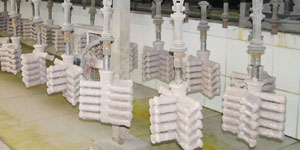
ITAF16949 certified. Additional Casting Service Include investment casting,sand casting,Gravity Casting, Lost Foam Casting,Centrifugal Casting,Vacuum Casting,Permanent Mold Casting,.Capabilities include EDI, engineering assistance, solid modeling and secondary processing.
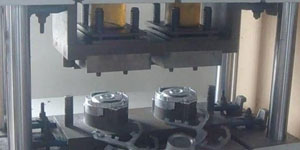
Casting Industries Parts Case Studies for: Cars, Bikes, Aircraft, Musical instruments, Watercraft, Optical devices, Sensors, Models, Electronic devices, Enclosures, Clocks, Machinery, Engines, Furniture, Jewelry, Jigs, Telecom, Lighting, Medical devices, Photographic devices, Robots, Sculptures, Sound equipment, Sporting equipment, Tooling, Toys and more.
What Can we help you do next?
∇ Go To Homepage For Die Casting China
→Casting Parts-Find out what we have done.
→Ralated Tips About Die Casting Services
By Minghe Die Casting Manufacturer |Categories: Helpful Articles |Material Tags: Aluminum Casting, Zinc Casting, Magnesium Casting, Titanium Casting, Stainless Steel Casting, Brass Casting,Bronze Casting,Casting Video,Company History,Aluminum Die Casting |Comments Off