14 Common Wrong Habits In Construction Machinery Maintenance
For construction machinery, how to better repair faulty construction machinery is an important point. Maintenance is an effective means to restore the technical performance of construction machinery, eliminate faults and eliminate hidden troubles, and extend the service life of machinery.
At present, the domestic automobile maintenance industry has a considerable scale, while the construction machinery maintenance industry started relatively late, and there are still many technical problems in the maintenance. The existence of these problems leads to poor mechanical maintenance and poor equipment reliability, causing consumers to suffer losses and even major construction machinery accidents.
1. Analyze faults by mistake, and blindly dismantle
Some maintenance personnel are not clear about the structure and principle of the construction machinery, do not analyze the cause of the fault carefully, and cannot accurately determine the fault location. They blindly dismantle the machinery with the idea of "approximately, almost". As a result, not only the original fault has not been eliminated, but also Due to poor maintenance skills and craftsmanship, new problems have arisen.
When a machine fails, it needs to be detected by testing equipment. If there is no testing equipment, it can be determined by traditional fault judgment methods and means such as "ask, see, check, and test", combined with the structure and working principle of the construction machinery, to determine the most probable The location where the failure occurred.
When determining the failure of construction machinery, the "removal method" and "comparative method" are generally used, and proceed in the order from simple to complex, first appearance, then internal, first assembly and then parts. Do not "regardless of indiscriminate dismantling and dismantling and dismantling." ".
2. Blindly replace parts, blindly "replace parts and repair"
It is relatively difficult to judge and eliminate construction machinery faults. Some maintenance personnel have always adopted the method of replacement test. Regardless of the large and small parts, as long as they think that the parts that may cause the failure, they are replaced one by one. The result is not only the failure is not eliminated, but also The parts that should not be replaced are replaced at will, which increases consumer spending.
During maintenance, the cause and location of the failure should be carefully analyzed and judged based on the failure phenomenon. Repair methods should be taken to restore the technical performance of the repairable parts, and the practice of blind replacement of parts should be avoided.
3. Do not check the quality of new parts, failures occur after assembly
Before replacing the parts, some maintenance personnel do not perform technical inspections on the new parts, and install them directly on the construction machinery after they are taken. This approach is unscientific. At present, the quality of the parts sold on the market is uneven. Some fake and inferior parts are mixed. Some parts have changed in performance due to long storage time. If they are not tested, they often cause failures after assembly.
Be sure to perform necessary inspections and tests before replacing new accessories, including appearance and performance tests, to ensure that the new accessories are free from malfunctions and to prevent unnecessary troubles caused by them.
4. Do not pay attention to the accessory model, substitute or wrong use of accessory
When repairing construction machinery, substitution or misuse of accessories is still common. Emergency substitution of some accessories is feasible, but long-term use is harmful and unhelpful, affecting the safety and technical performance of the machinery.
Some maintenance personnel have little understanding of mechanical structure and principles, and many parts and accessories do not match the models, but they think that as long as they can be installed, they do not consider whether the technical performance of the machine can be exerted. When repairing construction machinery, you should try to use the original model accessories, not other models of accessories can be substituted, let alone wrong use.
5.Don’t pay attention to the selection of bolts
In the maintenance of construction machinery, the phenomenon of indiscriminate use of bolts is still more prominent. The performance and quality of bolts do not meet the technical requirements, resulting in frequent mechanical failures after maintenance. Special bolts used in construction machinery, such as drive shaft bolts, cylinder head bolts, connecting rod bolts, flywheel bolts, fuel injector fixing bolts, etc., are made of special materials through special processing, which have high strength and strong shear resistance. Ensure reliable connection and fixation.
In actual maintenance operations, when some maintenance personnel find that these bolts are damaged or missing, they cannot find the standard bolts for a while, some randomly take other bolts to replace them, and some process them on their own. These bolts are due to poor material or unqualified processing technology. The later use of construction machinery leaves hidden troubles. When repairing construction machinery, when the bolts are damaged or lost, replace the bolts that meet the requirements in time, and do not use bolts indiscriminately.
6.Improper bolt tightening method
Most of the fixing or connecting bolts in various parts of construction machinery have tightening torque requirements, such as fuel injector fixing bolts, cylinder head bolts, connecting rod bolts, flywheel bolts, etc. Some stipulate tightening torque, some stipulate tightening angle, and also stipulate tightening. order.
Some maintenance personnel think that whoever can tighten the bolts is irrelevant. They do not tighten according to the specified torque and sequence (some do not understand the tightening torque and sequence requirements), do not use torque (kg) wrenches, or use afterburners at will, Tighten by feeling, resulting in a large difference in tightening torque.
If the torque is insufficient, the bolts are prone to loosening, causing damage to the cylinder liner, loose bearing bushes, oil leakage, and air leakage; excessive torque may cause the bolts to be stretched and deformed, or even break, and sometimes damage the threaded holes, which affects the repair quality. When repairing construction machinery, the bolts must be tightened according to the specified torque and sequence to prevent mechanical failure due to excessive, small or improper bolt tightening torque.
7. Do not pay attention to detecting the fit clearance of parts
Diesel engine piston and cylinder liner matching clearance, piston ring "triple clearance", piston head clearance, valve clearance, plunger clearance, brake shoe clearance, driving and driven gear meshing clearance, bearing axial and radial clearance, valve stem All types of models have strict requirements on the clearance between the valve guide and the valve guide. Measurements must be made during maintenance, and the parts that do not meet the clearance requirements must be adjusted or replaced.
In actual maintenance work, there are many phenomena of blindly assembling parts without measuring the fit clearance, which leads to early wear or ablation of bearings, diesel engine oil burning, difficulty in starting or deflagration, broken piston rings, mechanical impacts, oil leakage, and air leakage And other failures, sometimes even due to improper parts clearance, resulting in serious mechanical damage accidents.
8. Unpaired, complete replacement of even parts or components
There are many coupling parts in construction machinery, such as the plunger pair, the delivery valve pair, and the injector needle valve pair of the diesel engine fuel system; the driving and driven gears in the main reducer of the drive axle; the valve in the hydraulic control valve Block and valve stem; the valve core and valve sleeve in the full hydraulic steering gear. These mating parts are specially processed and ground in pairs when manufactured in the factory. The coordination is very precise, and they are always used in pairs during the service life. , Must not be interchangeable.
Some inter-cooperating components, such as piston and cylinder liner, bearing bush and journal, valve and valve seat, connecting rod head cover and shaft, etc., are used after a period of running-in, and they are relatively well matched. You should also pay attention to them during maintenance. Assemble in pairs, don't make skewers.
Diesel engine connecting rods, pistons, fan belts, high-pressure oil pipes, excavator central rotary joint oil seals, bulldozer main clutch rubber cloth joints, etc., these machines use a set of accessories at the same time. If they are damaged, they must be replaced as a set, otherwise the quality of the accessories will vary greatly. , Different levels of new and old, different length and size, will cause unstable operation of the diesel engine, oil leakage in the hydraulic system, serious load concentration, and easy early damage to the replaced parts.
In the actual maintenance work, it is not uncommon for some people to replace the above parts in unpaired or complete sets in order to reduce expenses and some people do not understand the technical requirements. This reduces the maintenance quality of construction machinery, shortens the life of parts, and increases the occurrence of failures. Possibility should arouse sufficient attention.
9. Parts are reversed during assembly
When repairing construction machinery, some parts have strict orientation requirements. Only when they are installed correctly can the parts work properly. The external features of some parts are not obvious, and they can be installed positively and negatively. In actual work, the installation is often reversed, resulting in early damage to the parts, failure of the machine to work, and accidents of damage to the construction machinery. When assembling parts, the maintenance personnel must master the structure and installation direction requirements of the parts, and do not install them blindly.
10. Irregular maintenance methods, "treating the symptoms but not the root cause"
When servicing construction machinery, some maintenance personnel do not take correct maintenance methods, believing that emergency measures are omnipotent, replacing "maintenance" with "emergency", and there are many phenomena of "treating the symptoms but not the root cause". For example, the frequently encountered "repair by welding" is an example. Some parts can be repaired, but some maintenance personnel often use the method of "welding to death" in order to save trouble.
These irregular maintenance methods can only be used as an emergency, but cannot be used for a long time. The cause of the failure must be found fundamentally, and regular maintenance methods should be adopted to eliminate the failure, which should attract the attention of maintenance personnel.
11. Irregular use of gaskets
There are many types of gaskets used between the matching surfaces of construction machinery parts. Commonly used are asbestos pads, rubber pads, cardboard pads, cork pads, felt pads, non-ferrous metal pads (copper pads, aluminum pads), copper skin (steel skin) asbestos Pads, insulating pads, spring pads, flat pads, etc.
Some are used to prevent oil, water, air, and electricity leakage between the mating surfaces of the parts, and some are used to tighten and prevent loosening. There are different regulations and requirements for the timing and occasion of the use of each type of gasket. In the maintenance of construction machinery, the phenomenon of non-standard or even messy use of gaskets is still more serious, resulting in frequent leakage between the mating surfaces, and the loosening of bolts and nuts. Loose, affecting the normal use of construction machinery.
If the cylinder gasket of the engine is too thick, the compression ratio will be reduced, and the engine will be difficult to start; the use of copper gaskets between the matching surface of the injector and the cylinder head, if the asbestos gasket is used instead, it will easily cause poor heat dissipation and ablation of the injector; diesel fuel pump The gasket between the joint surface of the fuel injection pump is too thick, resulting in insufficient fuel delivery and fuel delivery pressure, and the power of the diesel engine is reduced.
If the spring gasket, locking gasket, and sealing gasket are not installed, the joint is not tight, and it is prone to loosening or oil leakage; due to the hole in the middle of the gasket and forgetting to open the hole, the oil passage and water passage are blocked, and the engine burns and holds the shaft. The phenomenon of boiling the water tank also often occurs. This reminds the majority of maintenance personnel when repairing construction machinery, remember that "shims are small but useful."
13. The quality of "small pieces" is not valued, because "small" loses "big"
During maintenance operations, some maintenance personnel often only pay attention to the maintenance of fuel injection pumps, fuel delivery pumps, pistons, cylinder liners, piston rings, hydraulic oil pumps, control valves, brakes, steering systems and other components, but ignore the maintenance of filters, For the maintenance of "small parts" such as overflow valves and various instruments, they believe that these "small parts" do not affect the work of the machine. Even if it is damaged, it does not matter. As long as the machine is active, it can be used. Don't know, it is these "small parts". "Lack of maintenance has caused early wear and tear of machinery and shortened service life.
Such as diesel filters, oil filters, air filters, hydraulic oil filters, water temperature gauges, oil temperature gauges, oil pressure gauges, sensor plugs, sensors, alarms, glow plugs, oil Liquid strainer, water tank cap, fuel tank cap, oil filler cap, grease nipple, air reservoir drain switch, battery box, fuel injector return joint, split pin, fan air hood, drive shaft bolt lock piece, etc. "Small parts" are indispensable for the normal operation and maintenance of construction machinery, and are essential for prolonging the service life of the machinery. During maintenance operations, if you do not pay attention to maintenance, you will often "lost big due to small losses", leading to failures of construction machinery happened.
Hidden failures frequently occur after maintenance taboos are forgotten
When repairing construction machinery, some maintenance personnel do not understand some of the problems that should be paid attention to during maintenance, resulting in frequent "habitual" errors in disassembly and assembly, which affects the quality of mechanical maintenance. Such as disassembly and assembly of the engine cylinder head in a hot car, it is easy to cause the cylinder head to deform and crack.
When installing the piston pin, the piston pin is directly driven into the pin hole without heating the piston, resulting in increased piston deformation and increased ovality; the back of the crankshaft main bearing or connecting rod bearing is equipped with copper pads or paper pads, which will easily block the oil passages. This leads to bush burning and axle holding accidents; excessive scraping of the bush during maintenance of the diesel engine will scrape off the anti-friction alloy layer on the surface of the bush, resulting in early wear due to direct friction between the steel back of the bush and the crankshaft.
When disassembling bearings, pulleys and other interference fit parts, do not use tensioners. Hard hits and hard knocks may easily lead to deformation or damage of the parts; when unsealing new pistons, cylinder liners, injectors and plungers and other parts, use them The oil or wax sealed on the surface of the fired parts changes the performance of the parts, which is not conducive to the use of the parts.
14. Incomplete decontamination of parts, premature corrosion often occurs
When repairing construction machinery, correct removal of oil and impurities on the surface of parts is of great significance to improve the quality of repairs and extend the service life of the machinery. Inadequate attention to strengthening the cleaning of parts, unreasonable selection of cleaning agents, improper cleaning methods, etc., lead to early wear and corrosive damage of parts, which occur from time to time in some repair units.
If the cylinder liner steps, the carbon deposits in the piston ring groove, the debris in the bolt holes, and the sand particles in the hydraulic components are not completely removed, the bolt torque is insufficient, the piston ring is easy to break, the cylinder gasket is ablated, and the hydraulic components are early worn. When overhauling the construction machinery, carelessly remove the oil or impurities accumulated in the diesel filter, oil filter, hydraulic oil filter, diesel water jacket, radiator surface, lubricating oil passage, etc., which makes the maintenance work incomplete , Reduce the trouble-free operation time of construction machinery.
When cleaning the parts, the repairer must choose the cleaning agent correctly. For the cleaning of various parts, different cleaning agents should be selected correctly according to their different requirements for cleanliness; second, it is necessary to prevent corrosion and rust of parts. In order to ensure the quality of parts, parts should be prevented from corrosion and rust, especially for precision parts, no corrosion or rust to any degree is allowed.
Therefore, when cleaning, alkaline cleaning agents (especially strong alkaline cleaning agents) should not be used to clean aluminum alloy parts (such as aluminum alloy cylinder heads), and strong acid cleaning agents should not be used to clean copper parts (such as thermostats). Main valve) to minimize the corrosion of mechanical parts; third, different parts should be cleaned separately.
Aluminum alloy parts and copper parts should not be cleaned together with alkaline or acidic cleaning agents. Rubber parts should not be cleaned together with other steel parts in gasoline, diesel, acid and alkaline cleaning agents.
Please keep the source and address of this article for reprinting:14 Common Wrong Habits In Construction Machinery Maintenance
Minghe Die Casting Company are dedicated to manufacture and provide quality and high performance Casting Parts(metal die casting parts range mainly include Thin-Wall Die Casting,Hot Chamber Die Casting,Cold Chamber Die Casting),Round Service(Die Casting Service,Cnc Machining,Mold Making,Surface Treatment).Any custom Aluminum die casting, magnesium or Zamak/zinc die casting and other castings requirements are welcome to contact us.
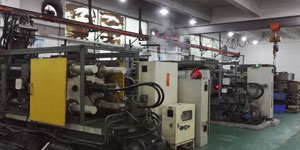
Under the control of ISO9001 and TS 16949,All processes are carried out through hundreds of advanced die casting machines, 5-axis machines, and other facilities, ranging from blasters to Ultra Sonic washing machines.Minghe not only has advanced equipment but also have professional team of experienced engineers,operators and inspectors to make the customer’s design come true.
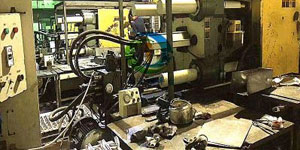
Contract manufacturer of die castings. Capabilities include cold chamber aluminum die casting parts from 0.15 lbs. to 6 lbs., quick change set up, and machining. Value-added services include polishing, vibrating, deburring, shot blasting, painting, plating, coating, assembly, and tooling. Materials worked with include alloys such as 360, 380, 383, and 413.
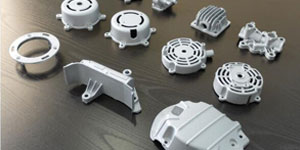
Zinc die casting design assistance/concurrent engineering services. Custom manufacturer of precision zinc die castings. Miniature castings, high pressure die castings, multi-slide mold castings, conventional mold castings, unit die and independent die castings and cavity sealed castings can be manufactured. Castings can be manufactured in lengths and widths up to 24 in. in +/-0.0005 in. tolerance.
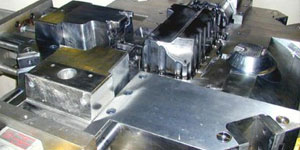
ISO 9001: 2015 certified manufacturer of die cast magnesium, Capabilities include high-pressure magnesium die casting up to 200 ton hot chamber & 3000 ton cold chamber, tooling design, polishing, molding, machining, powder & liquid painting, full QA with CMM capabilities, assembly, packaging & delivery.
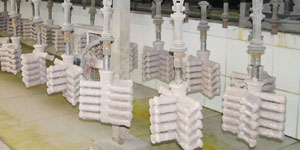
ITAF16949 certified. Additional Casting Service Include investment casting,sand casting,Gravity Casting, Lost Foam Casting,Centrifugal Casting,Vacuum Casting,Permanent Mold Casting,.Capabilities include EDI, engineering assistance, solid modeling and secondary processing.
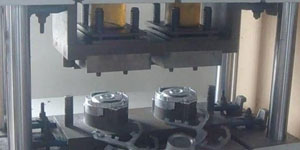
Casting Industries Parts Case Studies for: Cars, Bikes, Aircraft, Musical instruments, Watercraft, Optical devices, Sensors, Models, Electronic devices, Enclosures, Clocks, Machinery, Engines, Furniture, Jewelry, Jigs, Telecom, Lighting, Medical devices, Photographic devices, Robots, Sculptures, Sound equipment, Sporting equipment, Tooling, Toys and more.
What Can we help you do next?
∇ Go To Homepage For Die Casting China
→Casting Parts-Find out what we have done.
→Ralated Tips About Die Casting Services
By Minghe Die Casting Manufacturer |Categories: Helpful Articles |Material Tags: Aluminum Casting, Zinc Casting, Magnesium Casting, Titanium Casting, Stainless Steel Casting, Brass Casting,Bronze Casting,Casting Video,Company History,Aluminum Die Casting |Comments Off