17 common defects in malleable iron castings
Analysis of Causes of Defects in Malleable Iron Castings and Solutions
In the production of malleable iron castings, common casting defects include shrinkage cavity, shrinkage porosity, porosity, pores, cracks, sticky sand, rough casting surface, shrinkage, eccentricity, wrong shape, insufficient pouring, mold leakage, gray mouth, pitting , Anti-white mouth, too thick white edge, deformation, cracks, too thick oxide layer, core fracture, over-burning, loose dendrites, temper brittleness, insufficient annealing, etc. Usually, the cause of these defects is not only the annealing process, but sometimes there are many production process problems such as molding core making, smelting pouring, sand mixing quality, falling sand cleaning, etc. Therefore, specific analysis must be taken in order to take corresponding reasonable measures to solve them. .
In the production of malleable iron castings, some defects of the castings and their cause analysis and prevention methods are as follows:
1.Shrinkage and shrinkage
Features and discovery methods:
Inside the casting, the scattered small holes at the thick wall and hot joints are called shrinkage porosity; the concentrated holes are called shrinkage holes. The surface of the hole is rough
Cause Analysis:
- 1. As the bottom coke drops, the carbon content of the molten iron drops sharply, which increases the shrinkage
- 2. Improper setting of the pouring riser, the cross-sectional area of the riser neck is too small, the distance between the riser and the feeding part is too long, and the casting is insufficiently fed.
- 3. If the pouring temperature is too high, the tendency of shrinkage porosity and shrinkage cavity will increase.
- 4. Moisture content of molding sand is too high, air permeability is reduced, which prevents molten iron from filling the riser, resulting in insufficient feeding
Prevention method:
- 1. Stable chemical composition, control ωc between 2.3% and 2.7%
- 2. Generally, the riser is placed in the final solidified part of the casting. The cross-sectional area of the riser neck should be appropriate, and the length of the riser neck is generally 5~8mm
- 3. Choose a suitable pouring temperature
- 4. Strictly control the moisture of molding sand
2.Dendritic pine
Features and discovery methods:
The outer layer of the casting is dendritic and loose. From the surface of the casting, there are very thin needle-like crystals pointing to the center, so that the crystals have a radiant state. Generally produced near the riser neck, hot joints, sand cores and sharp corners of castings
Cause Analysis:
- 1. Generally, the cause of dendritic porosity is the same as that of shrinkage porosity, which is mainly caused by insufficient feeding. It is related to the thickness of the casting, the chemical composition of the molten iron, the pouring temperature, the amount of aluminum added and the arrangement of the pouring riser
- 2. In addition, because malleable iron castings are hypoeutectic white iron, the distance between liquid and solid phase lines is large, which is easy to form dendrites. A large amount of hydrogen penetrates into the molten iron at high temperatures. When the molten iron solidifies, hydrogen stays on the inner surface of the surface. Formation of dendritic porosity
Prevention method:
- 1. Strictly control ωAl, generally around 0.05%
- 2. Strictly control the moisture of molding sand to improve air permeability
- 3. For castings with thick walls, the pouring temperature should be lowered
- 4. High silicon content plus inoculation to shorten the solidification time
- 5. Reasonably arrange the pouring and riser system to make the feeding well
3.Stoma and pinhole
Features and discovery methods:
The casting has dense or dispersed pores on the surface or under the skin, and the surface of the pores is smooth
Cause Analysis:
- 1. Too much moisture in the molding sand, too high ash content, and too fine particle size, which reduces the air permeability of the molding sand
- 2. The pouring temperature is too low, the solidification is fast, and the bubbles are not easy to escape
- 3. If the content of pulverized coal in the molding sand is too high, the amount of gas will be large
- 4. The sand compaction is too high or the air passage of the sand core is poor
- 5. There is more gas in molten iron
- 6. The cold iron is not clean, or the location is improper
Prevention method:
- 1. Control the moisture of molding sand and improve the air permeability of molding sand
- 2. Appropriately increase the degree of pouring ju
- 3. Control the appropriate amount of coal powder
- 4. Appropriately reduce the binder of molding sand and core sand, and de-ash the old sand
- 5. The compactness of the sand mould should be appropriate, and the ventilation of the sand core should be strengthened
- 6. Dry the hearth, forehearth and ladle
- 7. The cold iron needs to be cleaned and set up reasonably
4.Crack
Features and discovery methods:
There are penetrating or non-penetrating cracks on the outside or inside of the casting. Hot cracks have a dark or black oxidized surface; cold cracks are relatively clean brittle cracks
Cause Analysis:
- 1. The carbon content is too low and the shrinkage is too large
- 2. Insufficient feeding at the thick wall of the casting or unreasonable setting of chilled iron
- 3. Molding sand or core sand has poor regressivity
- 4. The sulfur content of molten iron is too high, which increases the hot brittleness
- 5. The inner gate is large and concentrated, and the number is small, causing local overheating
- 6. The casting structure is unreasonable and the wall thickness changes too suddenly
- 7. Castings are unpacked too early and cooled too fast
- 8. Castings are exposed to too much impact when they are cleaned by falling sand
Prevention method:
- 1. Control ωc should not be lower than 2.3%. And appropriately increase the temperature of molten iron out of the furnace and reduce the pouring temperature
- 2. Reasonable setting of pouring riser and cold iron
- 3. The sand mold should not be too tight, add appropriate amount of wood chips to improve the concession
- 4. Try to keep the sulfur content of the molten iron as low as possible, or control the appropriate manganese-sulfur ratio
- 5. Improve the casting structure, the wall thickness transition requirements are gradually changed
- 6. Extend unpacking time
- 7. When cleaning the casting, avoid impact
5.Scum eye
Features and discovery methods:
There is slag in the cavities outside or inside the casting
Cause Analysis:
- 1. The slag in the ladle is not cleaned
- 2. Too much slag in molten iron
- 3. The flow is cut off during pouring
- 4. The setting of the gating system is unreasonable and the slag blocking effect is not good
- 5. Incorrect pouring position
Prevention method:
- 1. Remove the residue in the net ladle
- 2. Properly increase the temperature of the molten iron, a small amount of dry sand can be added to the molten iron ladle to facilitate the removal of accumulated slag
- 3. When pouring, take care not to stop the flow and keep the pouring cup full
- 4. A slag collecting bag can be set on the runner to prevent slag
- 5. The important parts of the casting should be placed below or on the side
6.Succulents
Features and discovery methods:
Irregular burrs, drape or protrusions on the casting
Cause Analysis:
- 1. The surface sand is not strong enough to produce cracks, causing molten iron to penetrate
- 2. Bad paint
- 3. Uneven mold compactness or insufficient sand consumption
Prevention method:
- 1. Apply finer surface sand, and appropriately increase the binder and sand mixing time to increase the surface sand arc
- 2. Improve coating
- 3. It is required that the molding sand has a uniform compactness and sufficient amount of sand to eat
7.Iron beans
Features and discovery methods:
There are small iron beads in the stomata
- 1. The molding sand is wet, and the inner runner is too high from the lowest part of the casting, causing molten iron to splash and form iron beans. After the molten iron is full, the iron beans cannot be melted, making it encased in the casting with gas
- 2. The air permeability of the sand core is not good, and the amount of gas generated is large. When a large amount of gas is generated from the molten iron, the molten iron rolls, and iron beans are easily produced on the surface of the casting near the sand core.
Prevention method:
- 1. Reduce the moisture of the molding sand or adopt a bottom injection pouring system to smoothly inject into the cavity to reduce splashing of molten iron
- 2. Appropriately reduce the addenda with large gas content in the core sand, and strengthen the ventilation of the sand core
8.Insufficient cooling and pouring
Features and discovery methods:
There are gaps or partial lack of meat on the castings that are not completely fused, with rounded edges around them
Cause Analysis:
- 1. The pouring temperature of molten iron is too low
- 2. The chemical composition of the molten iron is inappropriate
- 3. The sand mold is too wet
- 4. The setting of the gating system is unreasonable, and the gate section is too small
- 5. Part of the casting wall is too thin
- 6. Improper location of cold rail
- 7. Skew when setting the core
Prevention method:
- 1. Properly increase the pouring temperature
- 2. Control the proper chemical composition of molten iron
- 3. Reduce the moisture in the molding sand
- 4. Enlarge the gate size to speed up the pouring speed; for long castings, the molten iron can be introduced at both ends
- 5. Improve casting structure
- 6. Reasonably set up cold iron
- 7. The sand core is placed correctly
9.Cast numb, gray mouth
Features and discovery methods:
The section of the as-cast casting is pocked or gray
Cause Analysis:
- 1. In the melting of ingredients, the ingredients are not up to the requirements, and the carbon and silicon content is too high
- 2. Uneven blanking during melting, or uneven mixing of molten iron
- 3. The wall thickness of the casting is too different, and the thick wall will cause pitting or gray.
- 4. Unpacking too late
Prevention method:
- 1. The correct chemical composition is selected, the ingredients are reasonable, and the carbon and silicon content during the melting process is controlled within the required range
- 2. Install the forehearth to make the molten iron even
- 3. For thick-walled castings, the amount of bismuth should be appropriately increased or the pouring temperature of molten iron should be lowered
- 4. Properly unpack in advance
10.Castings, hard and brittle properties are substandard
Features and discovery methods:
The mechanical properties do not meet the requirements of the grade, especially insufficient toughness and too high hardness; excessive cementite or beads in the metallographic structure
Light body; black-hearted malleable iron castings are often white or fancy-hearted in fracture
Cause Analysis:
- 1. Improper chemical composition of castings, low silicon or high sulfur or high manganese
- 2. The chromium content or oxygen, nitrogen, and hydrogen content of the molten iron exceeds the limit
- 3. The graphitization annealing specification is incorrect or improperly controlled; the first or second stage graphitization is not complete
- 4. Improper control when using low temperature graphitization annealing process
- 5. Decarburization annealing temperature is too low or improper control of decarburization atmosphere
Prevention method:
- 1. Correctly control the chemical composition and gas content of molten iron
- 2. Correctly control the graphitization annealing or decarburization annealing process
11.Casting deformation
Features and discovery methods:
After annealing, the shape and size of the casting have changed significantly
Cause Analysis:
- 1. Improper packing of castings
- 2. The first stage graphitization annealing temperature is too high and the time is too long
- 3. Local temperature in the annealing furnace is too high
Prevention method:
- 1. Pay attention to the packing method, add partitions or packing
- 2. Appropriately reduce the degradation of the first stage graphitization annealing
- 3. Improve the structure and operation of the annealing furnace to make the furnace temperature as uniform as possible
- 4. Switch to low temperature graphitization annealing process
12.Castings are severely oxidized
Features and discovery methods:
Thick oxide scale is formed on the surface of the casting
Cause Analysis:
- 1. Furnace gas has strong oxidation
- 2. The annealing box is not well sealed
- 3. The annealing temperature is too high and the time is too long
Prevention method:
- 1. The annealing box is well sealed
- 2. When the silicon is high, appropriately lower the annealing temperature
- 3. Reasonably control the manganese-sulfur ratio
- 4. Using low temperature graphitization annealing process
13.Overburn
Features and discovery methods:
The surface of the casting is rough, the edges are melted, the fracture crystal is coarse, the graphite is coarse and the shape is poor. The casting becomes brittle and the hardness increases. A layer of oxygen-containing ferrite appears on the surface of the casting, which sometimes melts locally.
Cause Analysis:
- 1. The first stage graphitization annealing temperature is too high and the time is too long
- 2. The temperature difference of the annealing furnace is large, and the furnace temperature in a local area is too high, which greatly exceeds the process regulations
Prevention method:
- 1. Control the first stage graphitization annealing temperature
- 2. Improve the structure and operation of the annealing furnace to make the furnace temperature uniform
- 3. Switch to low temperature graphitization annealing process
14.Tempering brittleness
Features and discovery methods:
The casting has a white fracture, and the impact toughness and elongation are obviously reduced
Cause Analysis:
- 1. After the second stage graphitization annealing or low-temperature annealing, the temperature drop is too slow in the range of 550~400℃, the residence time is too long, and carbide or phosphide precipitates along the ferrite grain boundary
- 2. Cast iron has higher phosphorus content, especially when the silicon content is high, temper brittleness is more likely to occur
- 3. Hot-dip galvanizing in the temperature range (400~550℃) where temper brittleness occurs
Prevention method:
- 1. After annealing, it will be quickly cooled at 600~650℃
- 2. Properly control the content of phosphorus, silicon and nitrogen in molten iron
- 3. The galvanizing operation should avoid the temper brittle temperature zone. When galvanized temper brittleness occurs, the casting can be replated to eliminate brittleness
- 4. Castings that have undergone temper brittleness can be reheated to a temperature above 650℃ (650~700℃) for a short period of time, and then quickly cooled out of the furnace, the toughness can be restored
15 low temperature brittleness
Features and discovery methods:
Low wet brittleness transition temperature rise
Cause Analysis:
The content of silicon and phosphorus in the casting composition is too high
Prevention method:
Control the content of silicon and phosphorus in castings. For malleable iron castings that work at low temperatures and bear impact loads, ωsi should not exceed 1.7%, and ωp should not exceed 0.05%
16.Poor graphite shape distribution
Features and discovery methods:
The graphite shape and distribution are not good, causing the mechanical properties to fail to meet the requirements of standard grades
Cause Analysis:
- 1. Improper selection of the chemical composition of molten iron
- 2. Improper inoculation treatment and graphitization annealing process
Prevention method:
- 1. Control the chemical composition within the specified range to prevent the appearance of as-cast graphite
- 2. The amount of inoculant added should be appropriate. When the mass fraction of boron is more than 0.02%, string-shaped graphite will appear.
- 3. The annealing temperature should not be too high, especially the first stage graphitization annealing temperature should be strictly controlled. If it is too high, the graphite shape will deteriorate and the number of particles will decrease.
- 4. Use appropriate low temperature pretreatment process
17.Dendritic porosity
Features and discovery methods:
After the casting is annealed, there are tiny cracks that are visible or invisible to the naked eye, and there is a dendritic loose structure with obvious oxidation color, pointing from the surface to the center
Cause Analysis:
When the casting is solidified, due to insufficient solidification feeding and conditions such as structure and crystallization, tiny thermal cracks and loose dendrites are formed. During the annealing process, furnace gas invaded along the cracks and dendrite gaps, causing serious oxidation and further expansion of the loose parts
Prevention method:
Improve the inoculation treatment, refine the grains, eliminate the dendritic structure, and optimize the feeding conditions. Prevent plate-like white mouth tissue and thermal cracking.
Please keep the source and address of this article for reprinting:17 common defects in malleable iron castings
Minghe Die Casting Company are dedicated to manufacture and provide quality and high performance Casting Parts(metal die casting parts range mainly include Thin-Wall Die Casting,Hot Chamber Die Casting,Cold Chamber Die Casting),Round Service(Die Casting Service,Cnc Machining,Mold Making,Surface Treatment).Any custom Aluminum die casting, magnesium or Zamak/zinc die casting and other castings requirements are welcome to contact us.
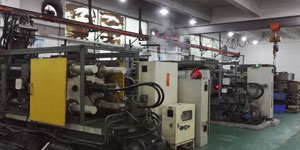
Under the control of ISO9001 and TS 16949,All processes are carried out through hundreds of advanced die casting machines, 5-axis machines, and other facilities, ranging from blasters to Ultra Sonic washing machines.Minghe not only has advanced equipment but also have professional team of experienced engineers,operators and inspectors to make the customer’s design come true.
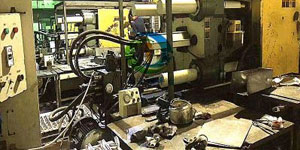
Contract manufacturer of die castings. Capabilities include cold chamber aluminum die casting parts from 0.15 lbs. to 6 lbs., quick change set up, and machining. Value-added services include polishing, vibrating, deburring, shot blasting, painting, plating, coating, assembly, and tooling. Materials worked with include alloys such as 360, 380, 383, and 413.
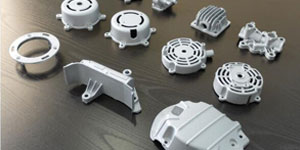
Zinc die casting design assistance/concurrent engineering services. Custom manufacturer of precision zinc die castings. Miniature castings, high pressure die castings, multi-slide mold castings, conventional mold castings, unit die and independent die castings and cavity sealed castings can be manufactured. Castings can be manufactured in lengths and widths up to 24 in. in +/-0.0005 in. tolerance.
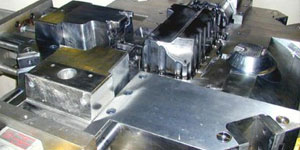
ISO 9001: 2015 certified manufacturer of die cast magnesium, Capabilities include high-pressure magnesium die casting up to 200 ton hot chamber & 3000 ton cold chamber, tooling design, polishing, molding, machining, powder & liquid painting, full QA with CMM capabilities, assembly, packaging & delivery.
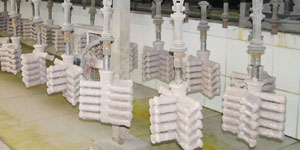
ITAF16949 certified. Additional Casting Service Include investment casting,sand casting,Gravity Casting, Lost Foam Casting,Centrifugal Casting,Vacuum Casting,Permanent Mold Casting,.Capabilities include EDI, engineering assistance, solid modeling and secondary processing.
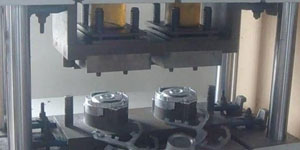
Casting Industries Parts Case Studies for: Cars, Bikes, Aircraft, Musical instruments, Watercraft, Optical devices, Sensors, Models, Electronic devices, Enclosures, Clocks, Machinery, Engines, Furniture, Jewelry, Jigs, Telecom, Lighting, Medical devices, Photographic devices, Robots, Sculptures, Sound equipment, Sporting equipment, Tooling, Toys and more.
What Can we help you do next?
∇ Go To Homepage For Die Casting China
→Casting Parts-Find out what we have done.
→Ralated Tips About Die Casting Services
By Minghe Die Casting Manufacturer |Categories: Helpful Articles |Material Tags: Aluminum Casting, Zinc Casting, Magnesium Casting, Titanium Casting, Stainless Steel Casting, Brass Casting,Bronze Casting,Casting Video,Company History,Aluminum Die Casting |Comments Off