17 Reasons And Control Of Poor Spheroidization
In the 1960s and 1970s, cupolas were mainly used to produce ductile iron, due to the poor quality of coke (large lumpness, low density, low fixed carbon content, and sulfur content); low temperature of molten iron; preparation of nodulizer used The method is not perfect; the pig iron contains high sulfur and phosphorus content, so the quality of the produced nodular cast iron is poor, and the spheroidizing quality is unstable. Nowadays, the production of nodular cast iron is mostly smelted in an electric furnace, and the temperature of the furnace is easy to control; the quality of raw materials such as pig iron is good; there are many types of nodulizers and the quality is good, so the quality of nodular cast iron is easier to control. However, poor spheroidization is still one of the main defects in the production of ductile iron.
Poor spheroidization is manifested on the fracture of the casting (usually observe the fracture of the pouring riser), with large black spots or obvious small black spots; the sound of striking the casting is not clear and crisp; there are many thick pieces on the metallographic microstructure;There are a small amount of spheroidal graphite, agglomerated graphite, or dendritic graphite (sometimes poor spheroidization has a metallographic feature, that is, in thick flake graphite clusters, individual spheroidal graphites are rather rounded).
The causes of poor spheroidization are generally affected by the following three types of factors: the residual magnesium content or the rare earth content is too low (but when the rare earth content is too high, the graphite roundness becomes poor, and the casting is prone to white mouth. And shrinking pine); the inoculation effect is not strong or declining; the interference element is too high.
However, in the actual production process, there are many factors that cause poor spheroidization, including technical problems, operational problems, and management problems.
1. Poor quality of spheroidizing agent
Although the content of Mg and RE in the spheroidizing agent meets the quality requirements through laboratory tests, the MgO content is relatively high due to poor smelting technology (the spheroidizing agent contains MgO>1%, which may affect the quality of spheroidization). MgO can improve The quality of spheroidization has almost no effect, but the ductile iron is prone to slag inclusion defects; the spheroidizing agent contains less elements such as Ca, the reaction is intense during the spheroidizing treatment, and the Mg burns more.
Preventive measures: do not use poor quality nodulizers (suppliers and manufacturers should be inspected, first buy in small quantities, and then buy in bulk after trial). The spheroidizing agent is placed for too long, and it is easy to be damp and oxidized.
2. Improper operation of spheroidization in front of the furnace
The spheroidizing agent is poured into the pit of the molten iron ladle dam, and it is not flattened; the surface covering is small, or the covering layer is thin, or the gap of the spheroidizing agent block is not filled. After rushing into the molten iron, the spheroidization is not only exposed The agent immediately melts and reacts, and at the same time, a large amount of molten iron enters the gap of the spheroidizing agent block, directly melting the spheroidizing agent or washing the spheroidizing agent off the surface of the floating molten iron, the reaction is too early and too fast, and Mg burns more.
Preventive measures: flatten the spheroidizing agent poured into the pit at the bottom of the bag and pound appropriately, then flatten and pound the inoculated ferrosilicon covered on it, and cover the surface with appropriate amount of nodular cast iron filings (pounded) or Ductile iron plate of certain thickness. This not only fills the gaps of the alloy, but also has a certain thickness of covering layer.
3. The original molten iron has high sulfur content
Sulfur is the main de-spheroidizing element, and high sulfur content will seriously affect the quality of spheroidization. When the wS in the original molten iron is greater than 0.06%, it is difficult to obtain qualified nodular cast iron quality even if more spheroidizing agent is added. . During the spheroidizing process, the Mg in the spheroidizing agent first chemically reacts with the S in the molten iron to form a slag of MgS, and the remaining Mg plays the role of spheroidizing, the same is true for RE. Since there are few spheroidizing elements, the quality of spheroidization is affected. The molten iron has a high sulfur content. Even if a large amount of spheroidizing agent is added, if the pouring time is too long and the slag is not clean, the phenomenon of "return sulfur" will occur, which will affect the quality of the castings from the pouring to the later stage. The main source of sulfur in the original molten iron is: the use of coke or nascent iron with high sulfur content.
Preventive measures: use low-sulfur pig iron and recycle material and coke; grasp the relationship between the amount of nodulizer added and the sulfur content of the original molten iron; take desulfurization measures in front of the furnace and during the spheroidizing process (spray lime on the coke) It is easier to desulfurize with water and electric furnaces, add alkali surface or caustic soda in the spheroidizing bag)
The spheroidization interference elements substituted with the charge are too high, such as Ti, Sb, As, Pb, Al, Sn, etc. Although rare earth elements have a certain ability to weaken or offset anti-spheroidization interference elements, too much interference elements in molten iron will still deteriorate the shape of graphite nodules (deformed graphite); even if spheroidization, the physical properties of nodular cast iron materials are also Will tend to be very brittle. Therefore, in the production of QT400-18 and low-temperature resistant ductile iron, high-purity pig iron should be used.
4. Improper placement of molten iron ladle
When iron is tapped, the molten iron directly rushes to the spheroidizing agent pressed in the pit, which not only washes away the covering, but also makes the alloy block directly subject to the impact of the high-temperature molten iron, or melts prematurely, reacts violently, or quickly floats to the iron The surface of the molten iron melts and burns on the surface of the molten iron and is absorbed by the air, which reduces the absorption rate of the molten iron to Mg.
Preventive measures: place the molten iron ladle to prevent the molten iron from directly impacting the alloy, so that the molten iron can steadily and quickly submerge the alloy and reach a certain depth instantaneously, and extend the distance of the alloy floating so that the alloy can be fully absorbed by the molten iron.
5. Slow iron tapping starts
If the iron tapping is too slow at the beginning, the liquid level will rise slowly in the ladle. When the molten iron floods the alloy, the surface layer of the alloy will begin to melt and then rise. Due to the short distance between the surface of the alloy and the surface of the molten iron, the alloy has no time A large amount of molten iron floats on the surface of the molten iron. Mg melting and burning on the surface of the molten iron are absorbed and lost by air, which reduces the absorption rate of the molten iron to Mg.
Preventive measures: For cupola furnaces, there must be sufficient molten iron in the front hearth. Before tapping, remove the mud that blocks the tap hole and quickly open the tap hole to allow the molten iron to reach quickly. 2/3 of the depth of the molten iron ladle capacity (ie a certain depth). At this time, the spheroidization reaction is due to the large distance from the surface of the alloy to the liquid surface. When the alloy floats in the molten iron, the distance it travels is long, and the alloy floats and melts at the same time. , The edge is fully absorbed by the molten iron, the spheroidizing element Mg in the spheroidizing agent has a high absorption rate, and the quality of nodular cast iron is good. Electric furnace tapping is more convenient, start tapping quickly, slow tapping or stop tapping when the reaction is violent, and continue tapping to the required amount when the reaction is stable. If the response is stable, try to be as fast and then slow as possible (non-stop in the middle) One time out.
6. The spheroidizing agent is installed too early or the molten iron in the pit of the dam has not been poured completely
After pouring, the temperature at the bottom of the red hot ladle is higher than 900°C. If the spheroidizing agent is installed immediately, part of Mg and RE will be lost under high temperature baking (smoke phenomenon); if the molten iron in the dike pit is not cleaned, the loss of Mg will be more; in addition, the overheated preheating temperature will also promote Premature melting of the spheroidizing agent.
Preventive measures: Let the ladle cool down for a period of time, and fill the spheroidizing agent before tapping the molten iron. At the same time, pour out the remaining molten iron in the ladle in time after pouring, and remove the molten slag in the ladle.
7. The temperature of spheroidizing molten iron is too low
When the spheroidizing molten iron temperature is lower than 1390℃, the alloy is not easy to melt, the spheroidizing reaction is incomplete, and the spheroidizing level is difficult to meet the requirements. During the floating process of the spheroidizing agent, due to the low temperature of the molten iron, the spheroidizing agent cannot be melted and absorbed quickly, causing the spheroidizing agent to float to the surface of the molten iron to melt and burn.
8. The temperature of spheroidizing molten iron is too high
The temperature of spheroidizing liquid iron is too high, and the melting speed of the covering agent and the spheroidizing agent is too fast. Because the density of pure Mg is 1.74g/cm3, the melting point is 651°C, and the boiling point is 1105°C. Melting point, but also lower than 1400 ℃, not to mention the spheroidization temperature is often 1490 ~ 1520 ℃, and some may be higher. According to the size of the casting and the thickness of the wall of the casting, when the spheroidizing temperature really needs to be increased, relatively "low temperature treatment and high temperature casting" measures must be taken. In addition, if the temperature of the molten iron is too high, the molten iron is often oxidized seriously. Because Mg and RE easily react with oxides, the high temperature causes a large amount of loss and evaporation of Mg and RE, which reduces the absorption rate.
9. The spheroidizing agent has small lumps and more broken pieces
When the size of the spheroidizing agent is small and there are many pieces, although the spheroidizing treatment method is the same, because there are no gaps between the alloy blocks, the melting reaction can only be peeled slowly and layer by layer. If the same steps are used for pouring, It may happen that the spheroidization of the first few boxes is not good and the spheroidization of the last few boxes is still good.
Preventive measures: Choose the size of the spheroidizing agent based on the size of the molten iron ladle, that is, how much molten iron is spheroidized. If there is too much crushing, it needs to be sieved; if the spheroidization reaction is too slow, a steel drill can be used to smash the loaded alloy through the molten iron for a few times, and the molten iron can be drilled into the alloy to accelerate the spheroidization reaction.
10. The spheroidizing agent is too large
The spheroidizing agent is too large. During the process of floating and melting, it is not absorbed by the molten iron in time, but floats to the surface of the molten iron to melt and burn, and is wasted in the air.
The choice of spheroidizing agent block size is determined according to the size of the molten iron ladle, that is, the amount of nodularizing molten iron.
11. Small amount of spheroidizing agent added
The amount of spheroidizing agent added is related to the requirements of the material, the sulfur content of the molten iron, the quality of the molten iron, the spheroidizing temperature, the size of the casting and other factors. There are two reasons for the small amount of spheroidizing agent: one is that the design requirement itself is small; the other is that the amount of molten iron is not well controlled, and the amount of molten iron exceeds the requirement.
12. Iron liquid oxidation
The oxygen content of molten iron is high after oxidation. Due to the strong affinity between O and Mg, the effective spheroidizing element Mg in the spheroidizing agent is first combined with O to produce MgO slag, and the remaining Mg can spheroidize graphite. Function, because oxygen consumes a large amount of Mg, and the remaining Mg is not enough to ensure that the graphite is spherical, so the spheroidization level is low and the spheroidization quality is poor.
Preventive measures: pay attention to the low coke (char) height of the cupola to prevent molten iron from oxidizing; electric furnace melting, do not use excessively oxidized charge to prevent excessively high temperature of the molten iron or high temperature and long-term heat preservation, especially for the 10t furnace to melt molten iron. Each time the spheroidizing process is 1t, when the spheroidizing process is a few packs later, due to the long residence time of the molten iron in the furnace, not only the molten iron lacks "crystal nuclei", but also is easy to oxidize. When a few packets after the spheroidization process, first carry out "pretreatment" in the furnace, add appropriate amount of silicon carbide, deoxidizer, recarburizer, ferrosilicon, etc. for deoxidation treatment, and appropriately add more spheroidizing agent.
13. The depth-to-diameter ratio of the bag and the bag pit
- (1) The ratio of the depth H of the spheroidization package to the direct D is: H/D=1.5~2. If the spheroidizing bag is used to deal with the half bag, it goes against the original intention of the high economic ratio.
- (2) The depth of the pit of the spheroidizing bag should be 20~30mm after filling the spheroidizing agent and covering agent. The molten iron enters the pit and the covering agent melts into a semi-solid substance, which delays the premature outbreak of the spheroidizing agent. Can improve the yield of Mg.
- (3) The width of the pit at the bottom of the bag should be 1/4 to 1/3 of the diameter of the bottom of the bag. The pit with a small projected area increases the depth and helps delay the outbreak.
- (4) Clean up the slag in the bag in time after pouring, so that each bag of spheroidizing agent is loaded into the pit in the same way.
14. Spheroidization decline due to long pouring time and other reasons
The characteristics of spheroidization recession are: good spheroidization in front of the furnace but not good spheroidization on the casting; or the same ladle of molten iron, the castings that are poured first have good spheroidization, and the castings that are poured later are not well spheroidized. The spheroidization recession caused by too long pouring time often coexists with the gestational recession. The amount of residual Mg that ensures that the graphite is spheroidized determines the spheroidization quality of the molten iron. Mg has a strong affinity with O and S. Mg combines with O to generate MgO and burn it. Especially S, when S combines with Mg to produce MgS slag, it floats to the liquid surface. After floating to the liquid surface, the Mg in the MgS slag combines with O in the air to produce MgO and burn off, and the separated S It returns to the molten iron again and combines with Mg. The S in the molten iron is like a boat, constantly bringing the Mg in the molten iron into the air and burning it, which is called the "reversion phenomenon". With the prolongation of the pouring time, the residual amount of Mg in the molten iron becomes less and less. According to some information, with the extension of the pouring time, the burning loss of Mg in the molten iron is 0.004% for every 1 min.
Solution: If the pouring time is prolonged for some reason, an appropriate thickness of insulating agent can be covered to reduce the contact between the molten iron and the air, and reduce the amount of Mg burnt in the molten iron. In addition, appropriate follow-up inoculation measures should be taken to decompose or cut off the graphite that has grown and is deformed (it becomes flake graphite when it grows) so that its shape tends to be spherical.
15. Breeding recession
Through the metallographic analysis, it can be seen that in the metallographic photos of the incubation decline, the number of graphite balls is small, the ball diameter is large, the density is thin, and the spheroidization level is low. Generally, the content of ferrite is low, the content of pearlite is increased, and there are carbides. exist. The reason for the inoculation decline is that the inoculant is added in a small amount, or the inoculation process is not perfect. Because the existence of magnesium is a necessary condition for spheroidization, and the elements in inoculation are sufficient conditions for participating in graphitization, so only the spheroidization treatment is not emphasized, and it is impossible to make high-quality ductile iron.
Preventive measures: increase the amount of inoculant added; use long-acting inoculants containing barium and calcium; take compound inoculation measures including secondary inoculation, floating silicon inoculation, and flow inoculation.
16. The spheroidizing bag or pouring bag is wet
When the spheroidizing process is flushed into the molten iron, the water is vaporized and decomposed to produce hydrogen and oxygen. O will neutralize part of the Mg in the spheroidizing agent and become MgO slag, which not only reduces the magnesium content in the molten iron , It is also easy to produce slag holes and pore defects in castings.
17. On-site management
The management and stacking of the spheroidizing agent are not standardized, and ferrosilicon may be mixed; the weight of the spheroidizing agent is inaccurate, or there is no peeling, or misreading, etc. For example, the production quality of ductile cast iron in a certain factory has been very stable. Suddenly, the two furnaces had poor spheroidization before the night shift, and the silicon content in the laboratory analysis exceeded the standard. After research and analysis, it may be that the ferrosilicon scattered on the ground was cleaned during the day. , Sorted into the spheroidizing agent tank. In addition, the storage time of the spheroidizing agent is too long and the storage is not good. The oxidation of the spheroidizing agent will weaken the spheroidization effect and affect the quality of the spheroidization.
Concluding remarks
In daily work, the hard work and effort required to work hard and not work is similar, but there is a big difference in improving and stabilizing product quality and improving the technical level of the operators themselves.
Please keep the source and address of this article for reprinting: 17 Reasons And Control Of Poor Spheroidization
Minghe Die Casting Company are dedicated to manufacture and provide quality and high performance Casting Parts(metal die casting parts range mainly include Thin-Wall Die Casting,Hot Chamber Die Casting,Cold Chamber Die Casting),Round Service(Die Casting Service,Cnc Machining,Mold Making,Surface Treatment).Any custom Aluminum die casting, magnesium or Zamak/zinc die casting and other castings requirements are welcome to contact us.
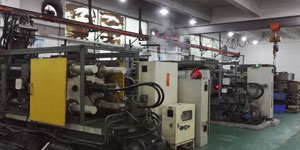
Under the control of ISO9001 and TS 16949,All processes are carried out through hundreds of advanced die casting machines, 5-axis machines, and other facilities, ranging from blasters to Ultra Sonic washing machines.Minghe not only has advanced equipment but also have professional team of experienced engineers,operators and inspectors to make the customer’s design come true.
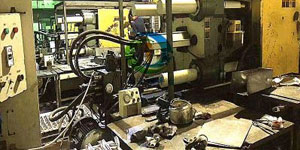
Contract manufacturer of die castings. Capabilities include cold chamber aluminum die casting parts from 0.15 lbs. to 6 lbs., quick change set up, and machining. Value-added services include polishing, vibrating, deburring, shot blasting, painting, plating, coating, assembly, and tooling. Materials worked with include alloys such as 360, 380, 383, and 413.
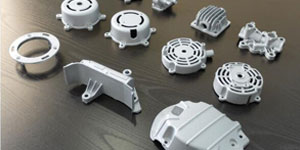
Zinc die casting design assistance/concurrent engineering services. Custom manufacturer of precision zinc die castings. Miniature castings, high pressure die castings, multi-slide mold castings, conventional mold castings, unit die and independent die castings and cavity sealed castings can be manufactured. Castings can be manufactured in lengths and widths up to 24 in. in +/-0.0005 in. tolerance.
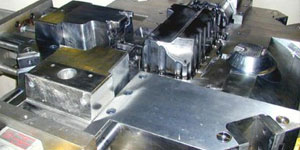
ISO 9001: 2015 certified manufacturer of die cast magnesium, Capabilities include high-pressure magnesium die casting up to 200 ton hot chamber & 3000 ton cold chamber, tooling design, polishing, molding, machining, powder & liquid painting, full QA with CMM capabilities, assembly, packaging & delivery.
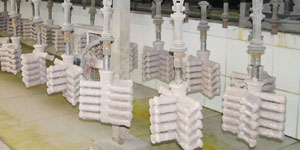
ITAF16949 certified. Additional Casting Service Include investment casting,sand casting,Gravity Casting, Lost Foam Casting,Centrifugal Casting,Vacuum Casting,Permanent Mold Casting,.Capabilities include EDI, engineering assistance, solid modeling and secondary processing.
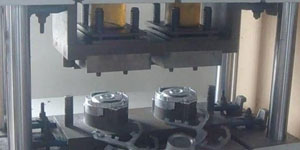
Casting Industries Parts Case Studies for: Cars, Bikes, Aircraft, Musical instruments, Watercraft, Optical devices, Sensors, Models, Electronic devices, Enclosures, Clocks, Machinery, Engines, Furniture, Jewelry, Jigs, Telecom, Lighting, Medical devices, Photographic devices, Robots, Sculptures, Sound equipment, Sporting equipment, Tooling, Toys and more.
What Can we help you do next?
∇ Go To Homepage For Die Casting China
→Casting Parts-Find out what we have done.
→Ralated Tips About Die Casting Services
By Minghe Die Casting Manufacturer |Categories: Helpful Articles |Material Tags: Aluminum Casting, Zinc Casting, Magnesium Casting, Titanium Casting, Stainless Steel Casting, Brass Casting,Bronze Casting,Casting Video,Company History,Aluminum Die Casting |Comments Off