5 Common Defects In Die Carburizing Process
1. Low hardness
The amount of retained austenite is one of the reasons for the low hardness of the stamping die. The amount of retained austenite in the carburized layer is often due to the high carburizing temperature and the high surface carbon concentration, resulting in low hardness of the stamping die. Another reason is that the surface carbon concentration is low. The reasons for the low surface carbon concentration are: the carburizing temperature is too low; the carburizing gas flow is small; a large amount of air is absorbed in the vacuum quenching oil; other oils, such as a large amount of cylinder oil, are mixed Into the vacuum quenching oil medium.
2. The depth of the carburized layer does not meet the technical requirements
The reason why the carburized layer depth of the stamping die exceeds the requirement is that the carburizing temperature is high or the carburizing time is long, and the reason why the depth is lower than the technical requirements is that the carburizing temperature is low or the carburizing time is short.
3.The carburized layer of the stamping die itself is uneven
The reasons for this situation may be: air is mixed in the carburizing gas; pulse carburizing is not used; the pressure of carburizing gas is too low; the amount of furnace installed is too large and dense; the purity of the carburizing gas is low, resulting in more Carbon black and so on.
4.There are many carbon blacks, and carbon black is also attached to the stamping die
When a large amount of carbon black is produced in the carburizing process, it may cause electric short circuit between the heater and the furnace body, the heater and the heater, which will increase the maintenance workload of the equipment; the small holes of the stamping die will be blocked and the carburized layer will not be blocked. Evenly, increase the workload of removing carbon black on the surface of parts.
5. The brightness of the stamping die deteriorates
The stamping die should be silvery white when it is discharged from the furnace after vacuum carburization and air cooling. If the brightness of the parts deteriorates when the furnace is discharged, the reason may be: the furnace has a large leakage; the vacuum quenching oil is mixed with more air; cooling The purity of the gas (such as nitrogen) is not high, and it contains more oxygen; more cylinder oil is mixed into the vacuum quenching oil.
Please keep the source and address of this article for reprinting:5 Common Defects In Die Carburizing Process
Minghe Die Casting Company are dedicated to manufacture and provide quality and high performance Casting Parts(metal die casting parts range mainly include Thin-Wall Die Casting,Hot Chamber Die Casting,Cold Chamber Die Casting),Round Service(Die Casting Service,Cnc Machining,Mold Making,Surface Treatment).Any custom Aluminum die casting, magnesium or Zamak/zinc die casting and other castings requirements are welcome to contact us.
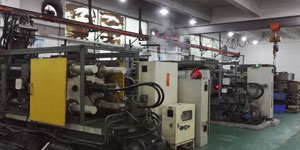
Under the control of ISO9001 and TS 16949,All processes are carried out through hundreds of advanced die casting machines, 5-axis machines, and other facilities, ranging from blasters to Ultra Sonic washing machines.Minghe not only has advanced equipment but also have professional team of experienced engineers,operators and inspectors to make the customer’s design come true.
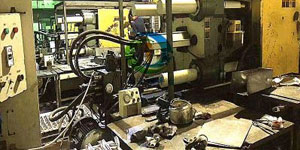
Contract manufacturer of die castings. Capabilities include cold chamber aluminum die casting parts from 0.15 lbs. to 6 lbs., quick change set up, and machining. Value-added services include polishing, vibrating, deburring, shot blasting, painting, plating, coating, assembly, and tooling. Materials worked with include alloys such as 360, 380, 383, and 413.
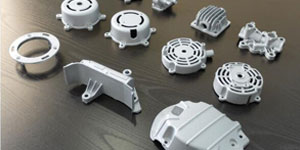
Zinc die casting design assistance/concurrent engineering services. Custom manufacturer of precision zinc die castings. Miniature castings, high pressure die castings, multi-slide mold castings, conventional mold castings, unit die and independent die castings and cavity sealed castings can be manufactured. Castings can be manufactured in lengths and widths up to 24 in. in +/-0.0005 in. tolerance.
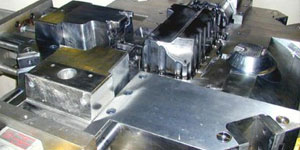
ISO 9001: 2015 certified manufacturer of die cast magnesium, Capabilities include high-pressure magnesium die casting up to 200 ton hot chamber & 3000 ton cold chamber, tooling design, polishing, molding, machining, powder & liquid painting, full QA with CMM capabilities, assembly, packaging & delivery.
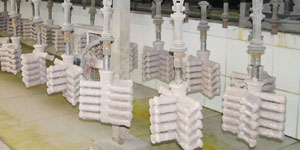
ITAF16949 certified. Additional Casting Service Include investment casting,sand casting,Gravity Casting, Lost Foam Casting,Centrifugal Casting,Vacuum Casting,Permanent Mold Casting,.Capabilities include EDI, engineering assistance, solid modeling and secondary processing.
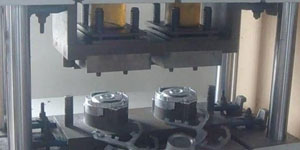
Casting Industries Parts Case Studies for: Cars, Bikes, Aircraft, Musical instruments, Watercraft, Optical devices, Sensors, Models, Electronic devices, Enclosures, Clocks, Machinery, Engines, Furniture, Jewelry, Jigs, Telecom, Lighting, Medical devices, Photographic devices, Robots, Sculptures, Sound equipment, Sporting equipment, Tooling, Toys and more.
What Can we help you do next?
∇ Go To Homepage For Die Casting China
→Casting Parts-Find out what we have done.
→Ralated Tips About Die Casting Services
By Minghe Die Casting Manufacturer |Categories: Helpful Articles |Material Tags: Aluminum Casting, Zinc Casting, Magnesium Casting, Titanium Casting, Stainless Steel Casting, Brass Casting,Bronze Casting,Casting Video,Company History,Aluminum Die Casting |Comments Off