5 Tricks For Mold Cost Control
The first factor, the reasonable design of the product is the biggest factor that affects the cost of the mold.
I believe that many people present will not agree with me. Whether the design of the product is reasonable or not, how could it be the biggest factor affecting the cost of the mold. Let’s take a look. The first kick kicked the ball to our car factory. But think about it carefully. If the product design is unreasonable, it will be a disaster for the mold company. I have been engaged in molds for more than 40 years. I have experienced many such things. Sometimes, in order to achieve an undercut on the product, and the product engineer and the mold designer do not communicate well, the cost of the mold will increase exponentially.
I was fortunate enough to participate in the design of a car interior part suitable for the disabled by a Shanghai automobile company. One of the parts is called the central partition. According to the original design, this part is very large, and the production cost of the mold is about 4 million yuan. The matching injection molding machine is above 4000 tons. Later I suggested to divide it into 2 pieces. The total production cost of the two sets of molds did not exceed 2 million. The matching injection molding machines are all 1500 ton models. Finally, everyone is happy. There are too many such examples. Therefore, a product designer should learn as much as possible about the knowledge of the mold, so that the designed product is as suitable as possible for the progress of the mold project, and do not unreasonably increase the difficulty and cost of the mold. On the premise of meeting the requirements of vehicle assembly, maintaining good communication with the mold department is the most effective and direct measure to reduce mold costs. There is also a philosophical issue of productivity and production relations. Some product engineers think that mold cost is your mold company's business, and has nothing to do with me. However, what if the production relationship is reorganized, and the injection molding company and the mold company are the same? In fact, this is a major social trend. The better companies that operate now are the combination of injection molding companies and mold companies. Companies that exist solely by making molds can hardly survive. Therefore, unreasonable product design will directly increase mold costs.
The second factor that affects the cost of the mold is the design change of the product.
Mold companies often encounter such a situation. In a certain project, the mold has just been designed, and the mold base has just been ordered, and the customer’s design change notification will come. If it is a small change that does not affect the overall structure of the mold, then It does not matter, sometimes the situation is more serious, because the shape of the product changes, the mold must be added with a mechanism, and even the mold base must be re-ordered. This cost increases greatly. Therefore, design changes should be minimized. Now there are many rapid prototyping methods. Before making the mold, the prototype is made in 3D, the whole vehicle is assembled, and the 3D of the product is corrected in time, which can minimize the increase in cost caused by product design changes. I remember I used to participate in the research and development of the Beijing Jeep Cherokee 213. The prototype injection molded in Shenzhen had to go to Beijing for trial assembly, and it took dozens of back and forth on the plane. It is hard to say whether this cost is calculated as a material fee or a processing fee.
The third factor that affects the cost of the mold is whether the mold design is perfect.
There are two situations to analyze here. The first is the rationality and machinability of the mold design.
In general mold companies, there must be old and experienced designers in the design team, as well as young engineers who have just come out of school. We cannot ask young engineers to design high-level molds independently when they first come to the company. Experienced mold engineers, if the mold structure built behind closed doors, it may not be perfect, there will definitely be some ill-considered details. One of the most important and effective methods is collective review. I remember that I bought a German mold book in the 1970s. It seemed to be called Advanced Mold Structure 80 Examples. The most influential thing to me was the mold making process mentioned in the book, which must be repeated many times on the mold structure. Collective review. This has the greatest impact on my tooling career, and it has really benefited a lot. I believe that everyone has a consensus on this issue. There are many simulation methods, such as mold flow analysis, dynamic analysis of mold structure, 3D comparison analysis of tested products and designed products, etc., which can minimize the cost increase caused by unreasonable mold design.
The second case is design waste. If the mold user clearly only needs to produce 500 samples, it is used to develop the market, but if we design the mold with a life of 300,000 molds, the cost will be large and it is a waste of design.
The fourth element of mold cost control is to minimize the number of mold trials.
Many mold companies calculate the mold processing fee based on the number of days after the mold is ordered and the mold is qualified. If the mold cannot be delivered for use after multiple trials, in addition to a fine according to the contract , The more days the mold spends in the factory, the more processing costs. Of course, the cost of mold trial is also very considerable. Therefore, multiple or uncontrollable mold trials are a big blind spot in mold cost control.
Let's analyze the reasons for the high number of mold trials.
The first is that the mold design has not been fully collectively reviewed, and the mold structure is unreasonable, which makes the mold need to be improved many times after the test, making the cost of the mold exceed the budget. If it can be done after several improvements, then Fortunately, there are many cases that are unsatisfactory, and even if the mold has to be scrapped and made again, this cost cannot be controlled. In some cases, the mold design is very good, but the mold processing is not in place, which makes the number of trial molds increase for no reason, which directly increases the cost of the mold. There is no objection to this issue, so many mold companies have increased their investment in measuring equipment.
The second is that the best molding process and model of the injection molding machine were not selected when trying the mold. The mold did a good job, but the injection molded product was not ideal. The number of mold trials is increased for no reason, which directly increases the cost of the mold. This is a common problem in some small mold factories.
The third is that the physical properties of plastics are not fully understood, and even the shrinkage rate is not accurate. Such situations happen from time to time. Therefore, it is necessary to understand the physical properties of the plastic before designing the mold in order to effectively reduce the number of mold trials.
The fifth factor that affects mold costs is the purchase of mold materials and standard parts.
Choose a stable and reputable supplier. It would be a great pity if molds are broken due to greed for cheap and hasty purchases. In fact, there are many such cases. Although the suppliers can be held accountable, the biggest losses are still the mold companies and mold users.
The sixth point may be my personal opinion that is rather extreme. Please criticize and correct me if there is any impropriety. Back to the origin of mold cost, what is mold cost, this issue has been discussed before. So let me continue to ask, what does the company want for this cost? The answer is yes, to get a set of qualified molds. The key to the problem is "qualified."
Suppose we used RMB 100,000 to make a set of molds for the car sundries box. The plastic used is PA+30%GF, the injection cycle is 30 seconds, and the mold life is 300,000 molds. As a result, the mold was made, and the size and physical properties of the sample were also achieved. However, because it was difficult to pick up the parts during injection molding, the injection cycle took 60 seconds, and the mold could not be used after 100,000 parts were produced. In order to catch up with the complete set of vehicles , The mold must be cast again. According to the original mold situation, 3 sets of molds must be cast at once. It also costs so much money, I think the cost of this set of molds is 3 times or 6 times the original budget. Do you have a different view?
Please keep the source and address of this article for reprinting: 5 Tricks For Mold Cost Control
Minghe Die Casting Company are dedicated to manufacture and provide quality and high performance Casting Parts(metal die casting parts range mainly include Thin-Wall Die Casting,Hot Chamber Die Casting,Cold Chamber Die Casting),Round Service(Die Casting Service,Cnc Machining,Mold Making,Surface Treatment).Any custom Aluminum die casting, magnesium or Zamak/zinc die casting and other castings requirements are welcome to contact us.
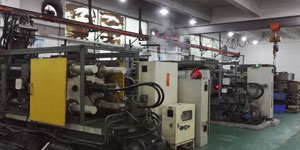
Under the control of ISO9001 and TS 16949,All processes are carried out through hundreds of advanced die casting machines, 5-axis machines, and other facilities, ranging from blasters to Ultra Sonic washing machines.Minghe not only has advanced equipment but also have professional team of experienced engineers,operators and inspectors to make the customer’s design come true.
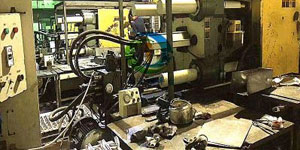
Contract manufacturer of die castings. Capabilities include cold chamber aluminum die casting parts from 0.15 lbs. to 6 lbs., quick change set up, and machining. Value-added services include polishing, vibrating, deburring, shot blasting, painting, plating, coating, assembly, and tooling. Materials worked with include alloys such as 360, 380, 383, and 413.
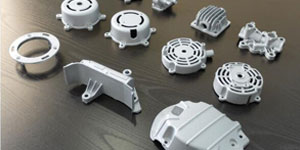
Zinc die casting design assistance/concurrent engineering services. Custom manufacturer of precision zinc die castings. Miniature castings, high pressure die castings, multi-slide mold castings, conventional mold castings, unit die and independent die castings and cavity sealed castings can be manufactured. Castings can be manufactured in lengths and widths up to 24 in. in +/-0.0005 in. tolerance.
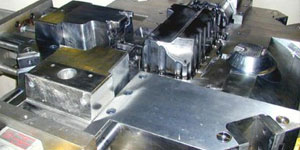
ISO 9001: 2015 certified manufacturer of die cast magnesium, Capabilities include high-pressure magnesium die casting up to 200 ton hot chamber & 3000 ton cold chamber, tooling design, polishing, molding, machining, powder & liquid painting, full QA with CMM capabilities, assembly, packaging & delivery.
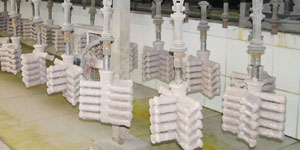
ITAF16949 certified. Additional Casting Service Include investment casting,sand casting,Gravity Casting, Lost Foam Casting,Centrifugal Casting,Vacuum Casting,Permanent Mold Casting,.Capabilities include EDI, engineering assistance, solid modeling and secondary processing.
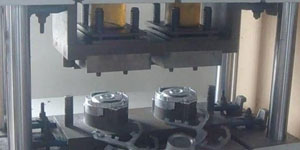
Casting Industries Parts Case Studies for: Cars, Bikes, Aircraft, Musical instruments, Watercraft, Optical devices, Sensors, Models, Electronic devices, Enclosures, Clocks, Machinery, Engines, Furniture, Jewelry, Jigs, Telecom, Lighting, Medical devices, Photographic devices, Robots, Sculptures, Sound equipment, Sporting equipment, Tooling, Toys and more.
What Can we help you do next?
∇ Go To Homepage For Die Casting China
→Casting Parts-Find out what we have done.
→Ralated Tips About Die Casting Services
By Minghe Die Casting Manufacturer |Categories: Helpful Articles |Material Tags: Aluminum Casting, Zinc Casting, Magnesium Casting, Titanium Casting, Stainless Steel Casting, Brass Casting,Bronze Casting,Casting Video,Company History,Aluminum Die Casting |Comments Off