6 Top Modern Mold Manufacturing Technologies
The rapid development of mold manufacturing technology has become an important part of modern manufacturing technology. Such as mold CAD/CAM technology, mold laser rapid prototyping technology, mold precision forming technology, mold ultra-precision processing technology, mold design adopts finite element method, boundary element method for dynamic simulation technology of flow, cooling, heat transfer process, mold CIMS technology, Has developed mold DNM technology and numerical control technology, etc., covering almost all modern manufacturing technologies.
Modern mold manufacturing technology is developing in the direction of accelerating information drive, improving manufacturing flexibility, agile manufacturing and system integration.
1. High-speed milling: the third generation of mold making technology
High-speed milling processing not only has high processing speed and good processing accuracy and surface quality, but also has low temperature rise compared with traditional cutting processing (the workpiece is only increased by 3℃), and the thermal deformation is small, so it is suitable for temperature and thermal deformation sensitive materials (such as Magnesium alloy, etc.) processing; also because of the small cutting force, it can be applied to the processing of thin-walled and poorly rigid parts; the reasonable selection of cutting tools can achieve a series of advantages such as hard material (HRC60) processing. Therefore, high-speed milling processing technology is still a hot topic at present. It has developed in the direction of higher agility, intelligence, and integration, and has become the third generation of mold making technology.
2. EDM milling "green" product technology
From the perspective of foreign EDM machine tools, whether in terms of performance, process indicators, intelligence, and automation, they have reached a very high level. At present, new trends in foreign countries are research and development of EDM machining technology (EDM creation processing technology). A new technology that replaces the traditional use of forming electrodes for cavity machining. It uses high-speed rotating simple tubular electrodes for three-dimensional or two-dimensional contour machining (like CNC milling), so there is no need to manufacture complex formed electrodes. This is obviously in the field of EDM machining. Significant development.
Recently, Japan's Mitsubishi Corporation has launched the EDSCAN8E EDM machine tool and has made new progress. This machine can automatically compensate for electrode loss. A special CAM system has been developed for this machine on Windows 95, which can be linked with general CAD such as AutoCAD, and can measure line accuracy to ensure high-precision machining. In order to confirm whether the processed shape is abnormal or incomplete, the CAM system can also realize simulation processing.
At the same time as the advancement of EDM technology, people pay more and more attention to the safety protection technology of EDM, and many EDM machine tools have considered safety protection technology. At present, the European Community has stipulated that machine tools without the "CE" mark cannot enter the European Community market. At the same time, the international market is paying more and more attention to the technical requirements of safety protection.
At present, the main problem of EDM machine tools is radiation harassment, because it has a greater impact on safety and environmental protection, and the international market is paying more and more attention to "green" products. As the leading equipment for mold processing, EDM machine tools will be used as the "green" product technology. Difficulties must be solved in the future.
3. New generation of mold CAD/CAM software technology
At present, the mold software developed by the United Kingdom, the United States, Germany and other universities and research institutes in my country has the characteristics of a new generation of mold CAD/CAM software intelligence, integration, and mold manufacturability evaluation.
The new generation of mold software should be built on a large amount of knowledge summarized from mold design practice. This knowledge has been systematically and scientifically sorted, and the engineering knowledge base is stored in a specific form and can be easily called by the mold. With the support of intelligent software, mold CAD no longer imitates traditional design and calculation methods. Under the guidance of advanced design theory, full use of the rich knowledge and successful experience of experts in the field, the design results must be reasonable and advanced.
The new generation of mold software uses three-dimensional ideas and intuitive feelings to design mold structures. The generated three-dimensional structure information can be conveniently used for mold manufacturability evaluation and numerical control processing. This requires mold software three-dimensional parameterized feature modeling, molding process simulation, and numerical control processing. Process simulation and information exchange organization and management have reached a fairly complete level and a high level of integration. To measure the degree of software integration, it depends not only on whether the functional modules are complete, but also on whether these functional modules share the same data model, and whether they form a global dynamic database in a unified manner to achieve comprehensive management and sharing of information to support mold design, manufacturing, and The whole process of assembly, inspection, testing and production.
Mold manufacturability evaluation function The role of a new generation of mold software is very important, not only to screen multiple options, but also to evaluate the rationality and economics of the mold design process, and provide a basis for mold designers to modify.
For the new generation of mold software, manufacturability evaluation mainly includes mold design and manufacturing cost estimation, mold assembly evaluation, mold part manufacturing process evaluation, mold structure and forming performance evaluation, etc. The new generation of software should also have assembly-oriented functions, because the mold function can only be reflected through its assembly structure. After the assembly-oriented design method is adopted, the mold assembly is no longer simply assembled one by one. Its data structure can not only describe the function of the mold, but also define the assembly characteristics of the relationship between the mold parts, and realize the part association, which can effectively guarantee the quality of the mold.
4.Advanced rapid mold manufacturing technology
- With the rapid development of laser rapid prototyping technology (RPM), my country has reached the international level and is gradually realizing commercialization. The world’s commercialized rapid prototyping processes mainly include SLA (stereolithography), LOM (layered split manufacturing), SLS (selective laser sintering), and 3D-P (three-dimensional printing).Tsinghua University was the first to introduce SLA250 (stereolithography or photosensitive resin laser curing) equipment and technology from the American 3D company and conduct development and research. After several years of hard work, several improvements have been made, perfected, and the "M-RPMS-type multifunctional Rapid Prototyping Manufacturing System" (with layered entity manufacturing-SSM, Melt Extrusion Molding-MEM), this is the only one in the world with independent intellectual property rights of my country to have two rapid prototyping process systems (national patents), which has a good price-performance ratio.
- Dieless multi-point forming technology uses height-adjustable punch groups to replace traditional molds for sheet metal surface forming. Another advanced manufacturing technology. The dieless multi-point forming system uses CAD/CAM/CAT technology as the main means to quickly and economically realize three-dimensional The curved surface is automatically formed. Jilin University of Technology has undertaken the key national scientific and technological projects related to dieless forming, and has independently designed and manufactured dieless multi-point forming equipment with the international leading level.Compared with the Massachusetts Institute of Technology in the United States, the University of Tokyo in Japan, and the Tokyo Institute of Technology in Japan, this technology in our country is in a leading position in terms of theoretical research and practical applications, and is currently developing towards popularization and application.
- The resin stamping die was successfully used for the first domestic car trial production. FAW Mould Manufacturing Co., Ltd. has designed and manufactured 12 sets of resin molds for the trial production of the new Xiaohongqi car modification. These 12 sets of molds are respectively the large and complex drawing molds for the interior and exterior covering parts such as the trunk, the hood, the front and rear fenders, etc. Features The mold surface is based on the CAD/CAM processing main model, and it is formed by Swiss Ciba refined high-strength resin. The convex and concave mold gap is accurately controlled by imported special wax. The mold size is high in precision and the manufacturing cycle can be shortened by half. To two-thirds, the manufacturing cost can be saved about 10 million yuan (12 sets of molds). It has opened up a new way for the trial production of small batches of cars in my country, which is the first in China. Swiss Ciba Fine Chemicals experts believe that it can reach the international level in the 1990s.
5. On-site mold testing technology
With the development of precision molds, the measurement requirements are getting higher and higher. The precision coordinate measuring machine has been limited by the environment for a long time and is rarely used on the production site. The new generation of three-coordinate measuring machines basically have temperature compensation and adopt anti-vibration materials, improve dust-proof measures, and improve the reliability of environmental adaptability, so that they can be easily installed in the workshop to achieve the characteristics of measuring on-site.
6. Mirror polishing mold surface engineering technology
Mold polishing technology is an important part of mold surface engineering, and an important process for post-processing of mold manufacturing process. At present, the domestic mold polishing to Ra0.05μm polishing equipment, abrasives and processes can basically meet the needs, but the polishing to Ra0.025μm mirror polishing equipment, abrasives and processes are still in the groping stage. With the large-scale application of mirror injection mold production, mold polishing technology has become a key issue in mold production. As there are still certain problems in domestic polishing technology and materials, a large part of injection molds such as point-and-shoot camera lens injection molds, CD, VCD discs and tools that require high transparency still rely on imports.
It is worth noting that the mold surface polishing is not only affected by the polishing equipment process technology, but also by the mirror finish of the mold material. This has not attracted enough attention, that is, the polishing itself is restricted by the mold material. For example, when 45# carbon steel is used as an injection mold, when it is polished to Ra0.2μm, obvious defects can be seen with the naked eye. Continue to throw it can only increase the brightness, and the roughness is hopeless. Therefore, the domestic mirror mold production often uses imported Mold materials, such as Sweden ASSAB 136, Japan Datong PD555, etc. can obtain satisfactory mirror finish.
Mirror mold material is not only a problem of chemical composition, but also a series of advanced processes such as vacuum degassing, argon protection ingot, vertical continuous casting and rolling, soft forging, etc. are required during smelting, so that the mirror mold steel has fewer internal defects and fine impurities. , A series of advantages such as high degree of dispersion, fine metal grain size, good uniformity, etc., in order to achieve the requirements of polishing to mirror mold steel.
Please keep the source and address of this article for reprinting: 6 Top Modern Mold Manufacturing Technologies
Minghe Die Casting Company are dedicated to manufacture and provide quality and high performance Casting Parts(metal die casting parts range mainly include Thin-Wall Die Casting,Hot Chamber Die Casting,Cold Chamber Die Casting),Round Service(Die Casting Service,Cnc Machining,Mold Making,Surface Treatment).Any custom Aluminum die casting, magnesium or Zamak/zinc die casting and other castings requirements are welcome to contact us.
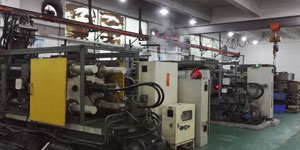
Under the control of ISO9001 and TS 16949,All processes are carried out through hundreds of advanced die casting machines, 5-axis machines, and other facilities, ranging from blasters to Ultra Sonic washing machines.Minghe not only has advanced equipment but also have professional team of experienced engineers,operators and inspectors to make the customer’s design come true.
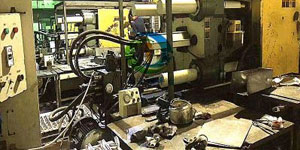
Contract manufacturer of die castings. Capabilities include cold chamber aluminum die casting parts from 0.15 lbs. to 6 lbs., quick change set up, and machining. Value-added services include polishing, vibrating, deburring, shot blasting, painting, plating, coating, assembly, and tooling. Materials worked with include alloys such as 360, 380, 383, and 413.
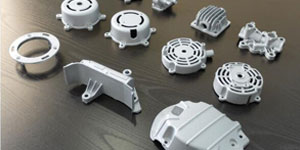
Zinc die casting design assistance/concurrent engineering services. Custom manufacturer of precision zinc die castings. Miniature castings, high pressure die castings, multi-slide mold castings, conventional mold castings, unit die and independent die castings and cavity sealed castings can be manufactured. Castings can be manufactured in lengths and widths up to 24 in. in +/-0.0005 in. tolerance.
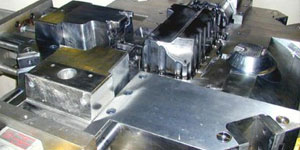
ISO 9001: 2015 certified manufacturer of die cast magnesium, Capabilities include high-pressure magnesium die casting up to 200 ton hot chamber & 3000 ton cold chamber, tooling design, polishing, molding, machining, powder & liquid painting, full QA with CMM capabilities, assembly, packaging & delivery.
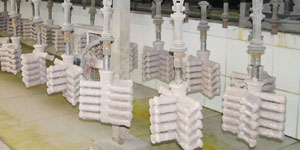
ITAF16949 certified. Additional Casting Service Include investment casting,sand casting,Gravity Casting, Lost Foam Casting,Centrifugal Casting,Vacuum Casting,Permanent Mold Casting,.Capabilities include EDI, engineering assistance, solid modeling and secondary processing.
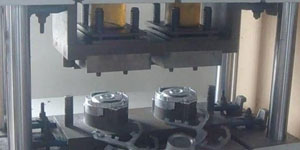
Casting Industries Parts Case Studies for: Cars, Bikes, Aircraft, Musical instruments, Watercraft, Optical devices, Sensors, Models, Electronic devices, Enclosures, Clocks, Machinery, Engines, Furniture, Jewelry, Jigs, Telecom, Lighting, Medical devices, Photographic devices, Robots, Sculptures, Sound equipment, Sporting equipment, Tooling, Toys and more.
What Can we help you do next?
∇ Go To Homepage For Die Casting China
→Casting Parts-Find out what we have done.
→Ralated Tips About Die Casting Services
By Minghe Die Casting Manufacturer |Categories: Helpful Articles |Material Tags: Aluminum Casting, Zinc Casting, Magnesium Casting, Titanium Casting, Stainless Steel Casting, Brass Casting,Bronze Casting,Casting Video,Company History,Aluminum Die Casting |Comments Off