7 FAQ In The Mold Manufacturing Field
What is the primary factor that affects the machinability of the material?
The chemical composition of steel is very important. The higher the alloy composition of the steel, the more difficult it is to process. When the carbon content increases, the metal cutting performance decreases.
The structure of steel is also very important for metal cutting performance. Different structures include: forged, cast, extruded, rolled, and machined. Forgings and castings have very difficult surfaces to machine.
Hardness is an important factor affecting metal cutting performance. The general rule is that the harder the steel, the harder it is to machine. High-speed steel (HSS) can be used to process materials with a hardness of up to 330-400HB; high-speed steel + TiN coating can process materials with a hardness of up to 45HRC; and for materials with a hardness of 65-70HRC, you must Use cemented carbide, ceramics, cermets and cubic boron nitride (CBN).
Non-metallic inclusions generally have an adverse effect on tool life. For example, Al2O3 (alumina), which is a pure ceramic, is highly abrasive.
The last one is residual stress, which can cause metal cutting performance problems. It is often recommended to perform a stress relief process after rough machining.
What are the cutting characteristics of cast iron?
Generally speaking, it is:
The higher the hardness and strength of cast iron, the lower the metal cutting performance, and the lower the expected life from the blades and cutters. Most types of cast iron used in metal cutting production generally have good metal cutting performance. Metal cutting performance is related to structure, and harder pearlitic cast iron is also more difficult to process. Flake graphite cast iron and malleable cast iron have excellent cutting properties, while ductile cast iron is quite bad.
The main types of wear encountered when machining cast iron are: abrasion, adhesion and diffusion wear. Abrasion is mainly caused by carbides, sand particles and hard cast skins. Bond wear with built-up edge occurs at low cutting temperature and cutting speed. The ferrite part of cast iron is the easiest to weld to the blade, but this can be overcome by increasing the cutting speed and temperature.
On the other hand, diffusion wear is temperature-dependent and occurs at high cutting speeds, especially when high-strength cast iron grades are used. These grades have high resistance to deformation, leading to high temperatures. This wear is related to the interaction between the cast iron and the cutting tool, which makes some cast irons need to be machined with ceramic or cubic boron nitride (CBN) cutting tools at high speeds to obtain good tool life and surface quality.
Generally, the typical tool properties required for machining cast iron are: high thermal hardness and chemical stability, but it is also related to the process, workpiece and cutting conditions; the cutting edge is required to have toughness, heat fatigue resistance and edge strength. The degree of satisfaction of cutting cast iron depends on how the wear of the cutting edge develops: rapid bluntness means that hot cracks and nicks cause the cutting edge to break prematurely, workpiece damage, poor surface quality, excessive waviness, etc. Normal flank wear, balance, and sharp cutting edges are what generally requires effort.
What are the main and common processing procedures in mold manufacturing?
The cutting process should be divided into at least 3 process types:
Rough machining, semi-finishing and finishing, and sometimes even super finishing (mostly high-speed cutting applications). Residual milling is of course prepared for finishing after the semi-finishing process. In each process, efforts should be made to leave a uniformly distributed margin for the next process, which is very important. If the direction and workload of the tool path rarely change rapidly, the life of the tool may be extended and more predictable. If possible, the finishing process should be carried out on a dedicated machine tool. This will improve the geometric accuracy and quality of the mold in a shorter debugging and assembly time.
What kind of tools should be used in these different processes?
Rough machining process: round blade milling cutter, ball end milling cutter and end milling cutter with large nose arc radius.
Semi-finishing process: round blade milling cutter (round blade milling cutter with diameter range of 10-25mm), ball end milling cutter.
Finishing process: round blade milling cutter, ball end milling cutter.
Residual milling process: round blade milling cutter, ball end milling cutter, vertical milling cutter.
It is very important to optimize the cutting process by selecting a combination of special tool sizes, geometries and grades, as well as cutting parameters and suitable milling strategies.
For the high-productivity tools that can be used, see catalog C-1102:1 for mold making
Is there one of the most important factors in the cutting process?
One of the most important goals in the cutting process is to create a uniformly distributed machining allowance for each tool in each process. This means that tools of different diameters (from large to small) must be used, especially in roughing and semi-finishing operations. The main criterion at any time should be as close as possible to the final shape of the mold in each process.
Providing uniformly distributed machining allowances for each tool ensures constant and high productivity and a safe cutting process. When ap/ae (axial depth of cut/radial depth of cut) does not change, the cutting speed and feed rate can also be constantly maintained at a high level. In this way, the mechanical action and work load changes on the cutting edge are small, so the heat and fatigue generated are also less, thereby increasing the tool life. If the subsequent processes are some semi-finishing processes, especially all finishing processes, unmanned processing or partial unmanned processing can be carried out. Constant material machining allowance is also the basic standard for high-speed cutting applications.
Another beneficial effect of the constant machining allowance is the small adverse effect on the machine tool-guide rails, ball screws and spindle bearings.
Why are round blade milling cutters the most common choice for mold roughing tools?
If a square shoulder milling cutter is used for rough milling of the cavity, a large amount of stepped cutting allowance will be removed in the semi-finishing machining. This will change the cutting force and cause the tool to bend. The result is to leave uneven machining allowance for finishing, thereby affecting the geometric accuracy of the mold. If you use a square shoulder milling cutter (with a triangular insert) with a weaker nose, it will produce unpredictable cutting effects. Triangular or diamond inserts will also produce greater radial cutting forces, and because the number of inserts' cutting edges is small, they are less economical roughing tools.
On the other hand, the round insert can be milled in various materials and in all directions. If it is used, the transition between adjacent toolpaths is smoother, and it can also leave a smaller and more uniform machining for semi-finishing. margin. One of the characteristics of round blades is that the thickness of the chips they produce is variable. This allows them to use higher feed rates than most other inserts.
The entering angle of the round insert is changed from almost zero (very shallow cutting) to 90 degrees, and the cutting action is very smooth. At the maximum cutting depth, the entering angle is 45 degrees. When cutting along a straight wall with an outer circle, the entering angle is 90 degrees. This also explains why the strength of the round blade tool is large-the cutting load is gradually increasing. Roughing and semi-roughing should always use round blade milling cutters, such as CoroMill200 (see mold manufacturing catalog C-1102:1) as the first choice. In 5-axis cutting, round inserts are very suitable, especially since it has no restrictions.
Through the use of good programming, round insert milling cutters can largely replace ball end mills. The round blade with small runout is combined with the finely ground, positive rake angle and light cutting geometry, and it can also be used for semi-finishing and some finishing processes.
What is the effective cutting speed (ve) and why it is always very important for the basic calculation of the effective cutting speed on the effective diameter of high productivity.
Since the table feed depends on the rotation speed at a certain cutting speed, if the effective speed is not calculated, the table feed will be calculated incorrectly.
If the tool's nominal diameter (Dc) is used when calculating the cutting speed, when the cutting depth is shallow, the effective or actual cutting speed is much lower than the calculated speed. Such as round insert CoroMill200 tools (especially in the small diameter range), ball end mills, large nose arc radius end mills and CoroMill390 end mills and other tools (for these tools, please refer to Sandvik Coromant's mold manufacturing Sample C-1102:1). As a result, the calculated feed rate is also much lower, which severely reduces productivity. More importantly, the cutting conditions of the tool are lower than its capabilities and recommended application range.
Please keep the source and address of this article for reprinting:7 FAQ In The Mold Manufacturing Field
Minghe Die Casting Company are dedicated to manufacture and provide quality and high performance Casting Parts(metal die casting parts range mainly include Thin-Wall Die Casting,Hot Chamber Die Casting,Cold Chamber Die Casting),Round Service(Die Casting Service,Cnc Machining,Mold Making,Surface Treatment).Any custom Aluminum die casting, magnesium or Zamak/zinc die casting and other castings requirements are welcome to contact us.
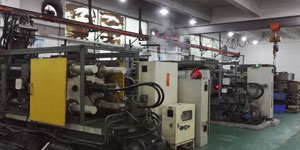
Under the control of ISO9001 and TS 16949,All processes are carried out through hundreds of advanced die casting machines, 5-axis machines, and other facilities, ranging from blasters to Ultra Sonic washing machines.Minghe not only has advanced equipment but also have professional team of experienced engineers,operators and inspectors to make the customer’s design come true.
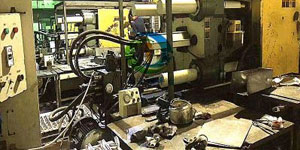
Contract manufacturer of die castings. Capabilities include cold chamber aluminum die casting parts from 0.15 lbs. to 6 lbs., quick change set up, and machining. Value-added services include polishing, vibrating, deburring, shot blasting, painting, plating, coating, assembly, and tooling. Materials worked with include alloys such as 360, 380, 383, and 413.
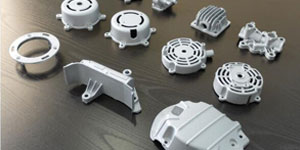
Zinc die casting design assistance/concurrent engineering services. Custom manufacturer of precision zinc die castings. Miniature castings, high pressure die castings, multi-slide mold castings, conventional mold castings, unit die and independent die castings and cavity sealed castings can be manufactured. Castings can be manufactured in lengths and widths up to 24 in. in +/-0.0005 in. tolerance.
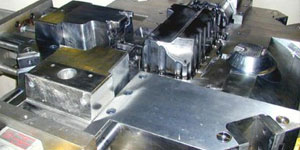
ISO 9001: 2015 certified manufacturer of die cast magnesium, Capabilities include high-pressure magnesium die casting up to 200 ton hot chamber & 3000 ton cold chamber, tooling design, polishing, molding, machining, powder & liquid painting, full QA with CMM capabilities, assembly, packaging & delivery.
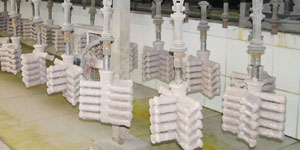
ITAF16949 certified. Additional Casting Service Include investment casting,sand casting,Gravity Casting, Lost Foam Casting,Centrifugal Casting,Vacuum Casting,Permanent Mold Casting,.Capabilities include EDI, engineering assistance, solid modeling and secondary processing.
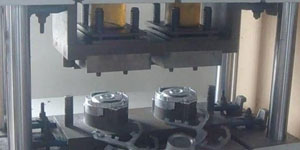
Casting Industries Parts Case Studies for: Cars, Bikes, Aircraft, Musical instruments, Watercraft, Optical devices, Sensors, Models, Electronic devices, Enclosures, Clocks, Machinery, Engines, Furniture, Jewelry, Jigs, Telecom, Lighting, Medical devices, Photographic devices, Robots, Sculptures, Sound equipment, Sporting equipment, Tooling, Toys and more.
What Can we help you do next?
∇ Go To Homepage For Die Casting China
→Casting Parts-Find out what we have done.
→Ralated Tips About Die Casting Services
By Minghe Die Casting Manufacturer |Categories: Helpful Articles |Material Tags: Aluminum Casting, Zinc Casting, Magnesium Casting, Titanium Casting, Stainless Steel Casting, Brass Casting,Bronze Casting,Casting Video,Company History,Aluminum Die Casting |Comments Off