Aluminum Alloy And Auxiliary Materials Management In Die Casting Production
Main Material Management
1. Entry control of aluminum alloy ingots
Due to the gas content and hard point requirements of aluminum alloy, aluminum ingot production plants must do a good job of refining, degassing, and slag removal to prevent defects such as high gas content and many impurities in aluminum ingots from being inherited into die-casting aluminum liquid. After the aluminum alloy ingot enters the factory, the first step is to inspect the appearance. The surface of the aluminum ingot is required to be smooth, free of roughness, free of oil stains, mildew, and oxide scale, and the fracture structure of the aluminum alloy ingot is fine and dense. There should be no serious segregation, shrinkage, or shrinkage. Slag and inclusions. Sampling the composition of each batch and heat number to ensure that the alloy composition used is qualified. In the production of products with special requirements, other testing items need to be added. For example, when producing products with mechanical performance requirements, when the aluminum alloy ingot is delivered for production, it is required to submit a tensile test bar for each furnace; when producing products with airtightness requirements, the pinhole degree of the aluminum alloy ingot must be increased. Detect
The types of aluminum alloys used in actual production are often not limited to one grade, and the chemical composition requirements of each grade of aluminum alloy are quite different. The main elements in one grade of alloy are in another grade of alloy. It may be considered as an impurity. For the coexistence of multiple grades, it is necessary to clearly visually distinguish the alloys of each grade to prevent the occurrence of mixing during use. The general measure is to clearly and uniformly specify the color of the appearance of aluminum alloys of different brands and different manufacturers, and store different materials in different areas after they arrive at the factory.
2. Aluminum alloy melting process control
Production practice shows that improving the quality of alloy melt is a key factor in improving the quality of die castings. Therefore, raw material management should be strictly controlled so that unqualified raw materials are not put into the workshop or put into production. Strictly operate in accordance with the standards required by the alloy melting process, and strengthen the management of various raw materials (new materials, recycled materials, and auxiliary materials).
The aluminum alloy melting process must have clear regulations on the melting temperature, smelting time, and the proportion of re-fired materials, especially the re-fired materials should be strictly classified and managed, and they should not be mixed. The recycled material should be clean and free of oil, rust, silt, moisture, and inserts. The oily contaminants in the recycled material can be remelted by the aluminum ingot manufacturer and cannot be directly put into the melting furnace for use; for the scattered aluminum blocks, they must be screened and the dust, sand and other debris inside can be removed. Use: Where the molten aluminum is used for reheating, the ratio of refining agent and slag remover is larger than that when only aluminum alloy ingot is used for melting. In the production in the weather with high relative humidity, the proportion of the recycled material should not exceed 30%, and the recycled material can be appropriately increased in dry weather, but it should not exceed 40%.
The slagging and degassing of molten aluminum after smelting should be carried out in a timely manner, and the corresponding parameters should be recorded as required. In the centralized melting process, the chemical composition of each pot of aluminum liquid should be tested to ensure that the chemical composition of the product is qualified during the melting process. In addition, long-term smelting should be avoided, otherwise the hydrogen content in the aluminum alloy liquid will increase, which will affect the strength and air tightness of the die-casting product. Generally, it does not exceed 4h from melting to die-casting.
Management Of Auxiliary Materials
1. Control of release agent
The use of mold release agent can make liquid metal filling smoothly, facilitate forming, prevent mold sticking, make castings obtain bright, smooth and flat surface quality, and have a great influence on production rhythm, casting surface and internal quality. At the same time, it can protect the mold, avoid the erosion of high temperature liquid metal on the mold surface, reduce the thermal conductivity and mold temperature of the mold, and extend the life of the mold. When the mold is opened, it is conducive to the smooth ejection of the casting, and it also plays an important role in reducing the friction and wear of the punch, ejector rod, and movable parts. The control of the release agent not only includes the selection and ratio of the release agent itself, but also includes the management of the spraying and blow-drying of the release agent by the operator. Generally, the selection of the release agent has the following requirements.
- It has good lubricity at high temperature and low volatilization point. The water in the release agent can volatilize quickly at 100-150°C.
- It has no corrosive effect on die-casting molds and die-casting parts, and has stable performance. The release agent should not volatilize too fast and thicken in the air.
- No harmful gas will be precipitated at high temperature, and no fouling will occur on the surface of the die-casting cavity.
At present, the spraying of the release agent is mainly a manual operation, and a reasonable spraying operation is an important factor to ensure the quality of the casting, the life of the die-casting mold, and the production efficiency. The spraying time of the mold release agent also changes with the mold release performance, dilution ratio, different die casting shapes, and different mold temperatures of different types of mold release agents. The release agent is sprayed from the spray gun to the surface of the mold to condense into a protective film. It takes a long time. When the process is not completed, the casting operation is carried out, which is often the root cause of the loose defects of the casting. According to the regulations of the die-casting process, a reasonable spraying time range should be adopted for a different type of release agent and different dilution ratios. Die casting workers must understand the meaning of the upper and lower limits of the process parameters and the trend of adjustment influence, and make appropriate adjustments according to the surface conditions of the produced die castings.
When using water-based release agents, the ratio of release agents must be strictly controlled. If the ratio of release agent to water is too thick, a thicker film will be formed on the mold surface, and release agent accumulation will slowly form on the mold surface. The moisture in the release agent cannot be completely discharged and gas will be generated, which will make the die-casting part. The internal compactness deteriorates. If the ratio of release agent to water is too thin, the effect will not be achieved, and the die-casting parts will suffer from strain and mold sticking.
Therefore, in the quality control of the die-casting workshop, the management of the release agent has a greater impact on the quality of the die-casting parts. It is necessary to strengthen the management in this area, such as appointing a special person to be responsible for the proportion of the release agent, and clearly stipulating various types of different The ratio of release agent and water in the production process of die-casting products is determined and quantified according to the release agent preparation process. When spraying, the operator shall carry out strict training on the spraying action, and the action must be carried out in accordance with the requirements and specifications, and it is not allowed to spray more, less spray, or miss spray.
2. Punch oil management
At present, most of the use of oil-based punch lubricating oil or particle lubrication, no matter what form of punch lubrication, after the aluminum liquid enters the barrel, it must be fully burned in a short time, and the residue must be distributed on the upper layer of the alloy liquid , So that the impact of punch oil on the product will not be too great. Otherwise, the gas generated by combustion and residues after combustion will enter the product, and the result can be imagined.
The simple way to verify the punch oil is to observe the color of the material handle on the mold. Generally, the thickness of the material handle is 1/3 to 1/4 of the diameter of the punch, and the length of the blackening of the punch oil should not exceed 3 of the thickness of the material handle. /5; At the same time, there should be no obvious blackening at the end of the material handle (that is, too much graphite powder residue). Otherwise, after the product is processed, defects such as pores will inevitably increase.
In the production process, we should also pay attention to the working condition of the punch lubrication device at all times. If the lubricant is sprayed too much or too little, it will have a negative impact on the life of the pressure chamber and the punch and the quality of the die casting. When adjusting the amount of lubricant used, it is necessary to consider both the lubricity of the punch and the demoldability of the mold. Especially when using particle lubrication, no matter how the wax pellets are used in the die-casting mold, there will be a problem of volatilization of organic matter. If a large amount of volatile organic matter cannot be discharged well, it will have a great impact on the generation of pores in the die-casting part.
3. Punch management
The punch and the pressure chamber constitute an interdependent system. Under normal circumstances, the life of the pressure chamber can reach 2 to 3 years, and the life of a punch is short, one shift, and the long life can reach more than 10,000 times. The difference in life span will cause fluctuations in product quality and significant changes in production costs. Therefore, good punch management can not only stabilize the quality of die-casting parts, but also greatly reduce the production cost of die-casting.
- Design of punch size. Under normal circumstances, there needs to be a certain clearance between the punch and the pressure chamber. Practice shows that the ideal gap is about 0.1 mm. During injection, if the gap is too large, the aluminum alloy liquid may enter the gap, and aluminum liquid leakage and smoke will occur, which will aggravate the wear of the punch and reduce the life of the punch; if the gap is too small, the punch will move in the process There is jamming, the speed of the punch cannot reach the speed predetermined by the process, the filling time of the mold is prolonged, and the quality problems of the die-casting parts increase. Therefore, the processing and manufacturing of the punch must be carried out strictly according to the drawing, in order to finally control the critical gap, extend the life of the punch, and ensure the quality of the product.
- The cooling of the punch Since the die-casting process determines that the temperature of the punch is constantly changing, with the change of temperature, the gap between the punch and the pressure chamber is also changing. These changes affect not only the service life of the punch, but also the stability of the injection process during the die-casting process. To maintain the ideal gap, it is necessary to cool the punch. In the design, it is considered that the plunger is fully cooled by the water core of the injection rod, and the heat of the punch is taken away to the maximum extent, and the ideal gap between the punch and the pressure chamber can be kept stable. These measures help to ensure the stability of the injection process of each mold and the stability of the quality of the die-casting products. Practice has shown that the injection system with good punch cooling can greatly extend the service life of the punch while ensuring the stability of the injection process. However, it is necessary to do a good job of sealing the cooling water circuit of the punch, and beware of the leakage of cooling water caused by poor sealing between the punch and the injection rod. If sufficient attention is not paid to the leakage of cooling water, it will seriously affect the product. Air tightness.
4. Crucible management
The use of crucibles is very important to the die casting of aluminum alloys, especially the use of cast iron crucibles. If the crucibles cannot be operated strictly in accordance with the crucible specifications, the Fe content in the aluminum alloy composition in the subsequent production process may exceed the standard. According to our experience, if the cast iron crucible can be brushed with the crucible paint in strict accordance with the requirements for the use of the new pot, and brushed every 3 days during use, basically the increase in Fe content during the entire die-casting production process will not exceed 0.2% (this is the company's statistical data over the years, there may be some differences between different companies). Under the premise of controlling the incoming inspection of aluminum alloy ingots, it can fully guarantee that the alloy composition of the produced die castings meets the standard requirements. Although there is no concern about increasing iron in the use of graphite crucibles, it should also be paid attention to. The drying process for the first use of graphite crucibles must be strictly implemented. These operations will affect the service life of graphite crucibles in the future and have not been well preheated. The life of graphite crucible will be greatly affected. The high price of each graphite crucible will affect the production cost of die casting.
Conclusion
Among the five major elements of quality management, the above mainly discusses the issues of "materials" and "people". While managing raw materials and auxiliary materials, personnel training and management should be done well, and the technical level of die casting workers needs to be further improved. In order to effectively solve the quality problems in the die-casting production, apply the idea of total quality management to the quality control of the die-casting workshop, and use systematic die-casting production theory knowledge to guide the production, which will surely improve the quality control ability of the die-casting workshop to a new height. .
Please keep the source and address of this article for reprinting: Aluminum Alloy And Auxiliary Materials Management In Die Casting Production
Minghe Casting Company are dedicated to manufacture and provide quality and high performance Casting Parts(metal die casting parts range mainly include Thin-Wall Die Casting,Hot Chamber Die Casting,Cold Chamber Die Casting),Round Service(Die Casting Service,Cnc Machining,Mold Making,Surface Treatment).Any custom Aluminum die casting, magnesium or Zamak/zinc die casting and other castings requirements are welcome to contact us.
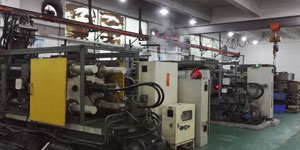
Under the control of ISO9001 and TS 16949,All processes are carried out through hundreds of advanced die casting machines, 5-axis machines, and other facilities, ranging from blasters to Ultra Sonic washing machines.Minghe not only has advanced equipment but also have professional team of experienced engineers,operators and inspectors to make the customer’s design come true.
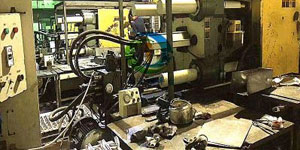
Contract manufacturer of die castings. Capabilities include cold chamber aluminum die casting parts from 0.15 lbs. to 6 lbs., quick change set up, and machining. Value-added services include polishing, vibrating, deburring, shot blasting, painting, plating, coating, assembly, and tooling. Materials worked with include alloys such as 360, 380, 383, and 413.
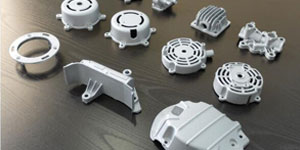
Zinc die casting design assistance/concurrent engineering services. Custom manufacturer of precision zinc die castings. Miniature castings, high pressure die castings, multi-slide mold castings, conventional mold castings, unit die and independent die castings and cavity sealed castings can be manufactured. Castings can be manufactured in lengths and widths up to 24 in. in +/-0.0005 in. tolerance.
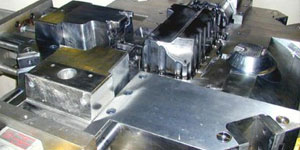
ISO 9001: 2015 certified manufacturer of die cast magnesium, Capabilities include high-pressure magnesium die casting up to 200 ton hot chamber & 3000 ton cold chamber, tooling design, polishing, molding, machining, powder & liquid painting, full QA with CMM capabilities, assembly, packaging & delivery.
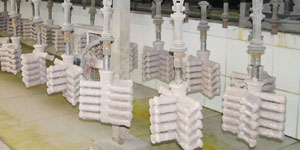
ITAF16949 certified. Additional Casting Service Include investment casting,sand casting,Gravity Casting, Lost Foam Casting,Centrifugal Casting,Vacuum Casting,Permanent Mold Casting,.Capabilities include EDI, engineering assistance, solid modeling and secondary processing.
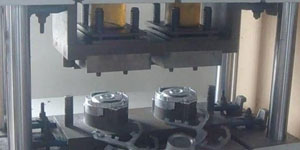
Casting Industries Parts Case Studies for: Cars, Bikes, Aircraft, Musical instruments, Watercraft, Optical devices, Sensors, Models, Electronic devices, Enclosures, Clocks, Machinery, Engines, Furniture, Jewelry, Jigs, Telecom, Lighting, Medical devices, Photographic devices, Robots, Sculptures, Sound equipment, Sporting equipment, Tooling, Toys and more.
What Can we help you do next?
∇ Go To Homepage For Die Casting China
→Casting Parts-Find out what we have done.
→Ralated Tips About Die Casting Services
By Minghe Die Casting Manufacturer |Categories: Helpful Articles |Material Tags: Aluminum Casting, Zinc Casting, Magnesium Casting, Titanium Casting, Stainless Steel Casting, Brass Casting,Bronze Casting,Casting Video,Company History,Aluminum Die Casting |Comments Off