Application Status And Development Trend Of Rare Earth Nitriding Process
Since the mid-1980s, in production, some gears generally treated with alloy steel carburizing and quenching process have higher strength requirements, as well as high speed, high power, and high reliability requirements. However, the shape of the steel after carburizing and quenching treatment is relatively large, and subsequent steps such as gear grinding treatment need to be added. It is not easy to achieve gear grinding treatment for non-involute gears. In addition, the rapid development of the aerospace industry in recent years has also promoted the application of large precision rings and thin-walled parts. At present, the surface treatment of these steel parts mostly adopts the carburizing and quenching process, which also has the problem of difficulty in final processing and forming, and large deformation after quenching. Compared with the carburized workpiece, the workpiece after nitriding has less deformation, which can better solve the above problems.
As the two most common surface hardening heat treatment processes, nitriding and carburizing have their own advantages. The wear resistance of the nitriding layer is better than that of the carburized layer, and the hardness is higher, but the process cycle is longer than that of the carburized layer. The nitriding layer is shallower than the carburized layer (0.3~0.5mm), and the bearing and impact load capacity is relatively weak. . Experimental studies have shown that deep nitriding (>0.55mm) treatment can partially replace the carburizing process, and can also effectively improve the impact resistance and bearing capacity of the carburized layer.
Since rare earths have been applied to chemical heat treatment, scholars at home and abroad have conducted many studies on the role of rare earths in the nitriding process, and have achieved remarkable results. That is, adding rare earths in the nitriding process can effectively increase the infiltration rate and hardness of the infiltration layer. , Making the infiltration layer thicker and improving the structure, thus having the dual role of catalysis and microalloying. The development of rare earth nitriding technology depends on its own characteristics, that is, the unique electronic layer structure makes it have strong chemical activity.
The addition of rare earth elements to the nitriding process has many advantages: first, it can speed up the nitriding; second, it can effectively reduce the nitriding temperature; third, it can greatly increase the service life of equipment and workpiece fixtures; fourth, it can improve the bending fatigue of parts, Contact fatigue strength and wear resistance, etc. Therefore, in Chinese gear nitriding, the introduction of rare earth elements into the chemical heat treatment process has improved the process to a new level and greatly improved the product quality, thereby achieving early integration with international standards and enhancing international competitiveness.
1. Application status of conventional nitriding process
Nitriding is a widely used surface chemical heat treatment technology. The purpose of the nitriding process is to obtain a higher surface hardness without basically changing its own properties and the size of the workpiece, and at the same time, it can improve the wear resistance and enhance the fatigue life. . Like other chemical heat treatment processes, the nitriding process includes the decomposition of the nitriding medium, the reaction in the nitriding agent, the diffusion, the phase interface reaction, the diffusion of the infiltrated nitrogen element in the iron, and the formation of nitrides. According to the Fe-N alloy phase diagram, the nitriding temperature is generally lower than 590°C (the eutectoid temperature of nitrogen), and the nitriding layer forms ε phase and α phase from the surface to the inside. Since the diffusion rate of nitrogen atoms in the epsilon phase is the slowest, after the nitriding layer is formed, the epsilon phase will act like a barrier to hinder the inward diffusion of nitrogen atoms. Therefore, under normal circumstances, the growth rate of the nitriding layer will decrease significantly after nitriding for a period of time.
Rare earth nitriding process
2.1 The mechanism of rare earth nitriding
Rare earth is a collective term for 17 elements including lanthanide elements and scandium (Sc) and yttrium (Y). These rare earth elements are relatively active and are located between magnesium (Mg) and aluminum (Al). Because of its unique characteristics, it is widely used in many fields. It is also due to these characteristics that it can be used as a heat treatment accelerator and be used in chemical heat treatment. In chemical heat treatment, lanthanum (La) and cerium (Ce) are often the main elements, because they have a 4f electronic layer structure and strong chemical electronegativity, such as cerium (Ce)-2.48, lanthanum (La)-2.52, Therefore, its chemical properties are relatively active, which in turn enables it to produce better chemical synergy with a variety of non-metals. Scholars from Harbin Institute of Technology believe that rare earth elements with special electronic structure and chemical activity can penetrate into the surface of steel parts. The reason for the many advantages is that once the rare earth element penetrates into the surface of the steel, the atomic radius is about 40% larger than that of the iron atom, which will cause the distortion of the surrounding iron atom lattice, which in turn increases the defect density, that is, the distortion produces more new ones. The crystal defects are conducive to the adsorption and diffusion of nitrogen atoms, so that the interstitial atoms are enriched in the distortion zone. After the rare earth element penetrates into the surface of the steel part, it will form a high nitrogen concentration on the surface of the steel part in a short time, thereby forming a high nitrogen potential and concentration gradient, which makes the nitrogen atoms diffuse inward rapidly, thereby making the chemical heat treatment process obvious Speed up and refine the structure of the infiltrated layer and improve the performance of the infiltrated layer.
The author believes that the substantial increase in the rate of rare earth nitriding is mainly due to the following reasons:
- The infiltration of rare earth elements causes the defect density to proliferate, the diffusion flux J increases, and the transfer coefficient of nitrogen atoms increases greatly.
- The infiltration of rare earth elements induces surface Fe atom lattice distortion, which increases the surface energy, thereby increasing the adsorption energy of capturing interstitial N atoms.
- The enrichment of a large number of N atoms in the distortion zone increases the nitrogen concentration difference, enhances the chemical energy, and accelerates the diffusion rate.
2.2.The characteristics of rare earth nitriding
The catalytic effect of rare earth during nitriding is much greater than that of carburizing, which is an important characteristic of rare earth nitriding. The reason is that the temperature of nitriding is usually in the α-Fe phase zone, and the infiltration resistance of rare earth elements in this phase zone is much smaller than that in the γ-Fe phase zone; in addition, the amount of rare earth infiltration is also the main factor affecting the infiltration effect. . Generally speaking, a large amount of infiltration has a better effect of infiltration, and the amount of rare earth infiltration during nitriding is more than that during carburizing, so the infiltration effect during nitriding is better.
The distribution and morphology of nitride in the nitriding layer are the key to the hardness of the nitriding layer. When the nitride is dispersed and distributed, the hardness is higher, on the contrary, the hardness is lower. In the conventional nitriding process, the flaky nitride is generally produced, and the nitride is coherent or semi-coherent with the parent phase. As the temperature rises, the nitrides continue to accumulate and become larger, desolubilize from the parent phase, and the hardness drops sharply.
In the process of rare earth nitriding, the infiltration of rare earth makes the nitride present a dispersed and uneven distribution state, so that the free energy rises sharply and becomes a trap for interstitial N atoms. At the same time, a metastable Cottrell air mass can be formed, which can reduce the energy there. The formation of nitrides takes rare earth elements as the core, and their distribution becomes finely dispersed. At the same time, it also presents a diffuse quasi-spherical precipitation, thereby avoiding the generation of vein-like structure, and also avoiding the segregation of nitride along the grain boundary. In addition, within a certain temperature range, the morphology of the nitride will not change, and its distribution will not change. Compared with the conventional nitriding technology, the rare earth nitriding technology makes the nitride layer hardness higher and the brittleness can be maintained at 0~ Level 1.
2.3. Requirements of rare earth nitriding process
Rare earth nitriding has the characteristic of higher hardness of the nitriding layer. According to this characteristic, the nitriding temperature can be increased by 10 to 20°C, thereby more effectively promoting the increase of the nitriding rate. According to the results of a large number of experiments, it can be found that with the same temperature, rare earth nitriding can only increase the infiltration rate by 15% to 20%, but after increasing the temperature by 20°C, the infiltration rate can be greatly increased. At the same time, similar to conventional nitriding technology, rare earth nitriding must control the ammonia decomposition rate of nitriding within a reasonable range, that is, a higher nitrogen potential (Np) should be used in the initial stage, and then gradually reduced. Generally, the two-end controlled atmosphere nitriding process with variable temperature and variable nitriding potential is adopted, and the ammonia decomposition rate is reduced at the initial stage, and the nitrogen potential is increased to meet the requirements of accelerating nitriding speed, which greatly increases it.
2.4. Economic benefits and energy saving of rare earth nitriding
Using conventional nitriding process, general alloy structural steel, when the layer requires 0.3mm, the holding time generally needs more than 30h. When the infiltration layer requires 0.6mm, the heat preservation time needs more than 90h. After rare-earth nitriding is added to the catalyst, when the normal alloy structural steel requires 0.3mm infiltration layer, if the cyclic heating insulation nitriding process can be used under the same temperature condition, the holding time will only be 14h. Compared with the conventional nitriding technology, the heat preservation time is 16h shorter and 53% of the time is saved. Therefore, it can save 40% of electricity, reduce ammonia consumption by about 35%, and reduce exhaust gas emissions by about 35%. When the penetration layer requires 0.6mm, the heat preservation time can be shortened by about 40%.
China is a major machinery manufacturing country, with thousands of companies using gas nitriding, mainly in machine tool manufacturing, wind power transmission, aerospace equipment, mold manufacturing and other industries. It is estimated that 3000 pit-type nitriding furnaces (calculated at 75kW) will be operated for 100 times a year, and each power-on for 25h will consume 5.625×108kW•h of electricity annually. The use of rare earth permeation agent can increase the permeation rate by 40%, and save electricity by 2.250×108kW•h, which is equivalent to 90,000 tons of standard coal and reduce CO2 emissions by 80,000 tons. Therefore, if the whole industry adopts rare earth infiltration technology in the nitriding process, it will have a better "energy saving and emission reduction" effect.
3. Development of rare earth nitriding technology
3.1. The importance of rare earth nitriding
In recent years, with the general rise in world energy prices, China’s economic development is facing huge challenges. For this reason, it has proposed to establish an innovative and energy-saving country and achieve the goal of sustainable economic development, and issued relevant measures to reduce energy consumption, energy conservation, and emission reduction. And related policies to achieve efficient life extension. According to the preliminary test of rare earth nitriding process, it can be known that rare earth catalyzed infiltration can greatly shorten the time of gas nitriding, and show different catalyzed effects for different steel materials, generally it can be shortened by about 30% to 60%, and the surface hardness is also low. Compared with traditional nitriding, it can increase 50~150HV. Preliminary calculations indicate that the use of this technology will greatly reduce power consumption, which is expected to reduce power consumption by 30% to 40%, reduce nitriding waste gas emissions, shorten working hours, and improve work efficiency. At the same time, the quality of the steel parts is greatly improved, the wear resistance is greatly enhanced, the surface wear resistance is greatly enhanced, the strength and hardness are increased within a certain range, and the efficient use and long life are realized. Rare earth nitriding technology will promote the development of China's nitriding process.
3.2 Prospects of rare earth nitriding
The nitriding process has the characteristics of improving the surface hardness of the parts, improving the wear resistance of the parts, and improving the corrosion resistance and fatigue resistance. It can be widely used in mold production and power machinery industries. Nitriding is an irreplaceable process in mechanical processing, but there are still some problems that need to be solved urgently in the nitriding process. For example, the process time is too long. Taking 0.5mm layer as an example, it will take as long as 50h. If the auxiliary time is added Including the calculation, its process time will reach 3 to 4 days. Therefore, this will waste a lot of man-hours, electricity consumption and ammonia. For this reason, the focus of future research on the nitriding process should focus on the following aspects: one is to shorten the nitriding time; the other is to deepen the infiltration layer; the third is to reduce energy consumption; and the fourth is to shift to the direction of developing a green economy.
In view of China's abundant rare earth resources and the many advantages of the rare earth nitriding process, technological innovation and promotion should be used to give full play to the advantages of resources and technology to form industrial development advantages and economic benefits.
Materials science and technology researchers should take the innovation and promotion of rare earth nitriding process as the research focus, and carry out a deeper discussion on its internal laws and nitriding mechanism. Continuously carry out the research and development of high-efficiency rare earth catalysts, and strive to realize the full replacement of the conventional nitriding process by the rare earth nitriding process, thereby maximizing the effect of energy saving, emission reduction, consumption reduction, and efficiency increase and life extension.
Please keep the source and address of this article for reprinting: Application Status And Development Trend Of Rare Earth Nitriding Process
Minghe Die Casting Company are dedicated to manufacture and provide quality and high performance Casting Parts(metal die casting parts range mainly include Thin-Wall Die Casting,Hot Chamber Die Casting,Cold Chamber Die Casting),Round Service(Die Casting Service,Cnc Machining,Mold Making,Surface Treatment).Any custom Aluminum die casting, magnesium or Zamak/zinc die casting and other castings requirements are welcome to contact us.
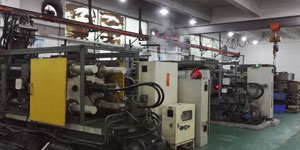
Under the control of ISO9001 and TS 16949,All processes are carried out through hundreds of advanced die casting machines, 5-axis machines, and other facilities, ranging from blasters to Ultra Sonic washing machines.Minghe not only has advanced equipment but also have professional team of experienced engineers,operators and inspectors to make the customer’s design come true.
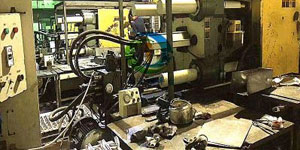
Contract manufacturer of die castings. Capabilities include cold chamber aluminum die casting parts from 0.15 lbs. to 6 lbs., quick change set up, and machining. Value-added services include polishing, vibrating, deburring, shot blasting, painting, plating, coating, assembly, and tooling. Materials worked with include alloys such as 360, 380, 383, and 413.
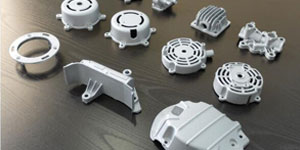
Zinc die casting design assistance/concurrent engineering services. Custom manufacturer of precision zinc die castings. Miniature castings, high pressure die castings, multi-slide mold castings, conventional mold castings, unit die and independent die castings and cavity sealed castings can be manufactured. Castings can be manufactured in lengths and widths up to 24 in. in +/-0.0005 in. tolerance.
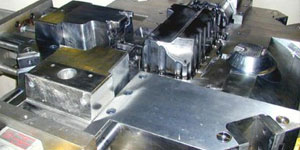
ISO 9001: 2015 certified manufacturer of die cast magnesium, Capabilities include high-pressure magnesium die casting up to 200 ton hot chamber & 3000 ton cold chamber, tooling design, polishing, molding, machining, powder & liquid painting, full QA with CMM capabilities, assembly, packaging & delivery.
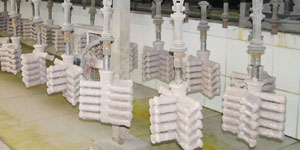
ITAF16949 certified. Additional Casting Service Include investment casting,sand casting,Gravity Casting, Lost Foam Casting,Centrifugal Casting,Vacuum Casting,Permanent Mold Casting,.Capabilities include EDI, engineering assistance, solid modeling and secondary processing.
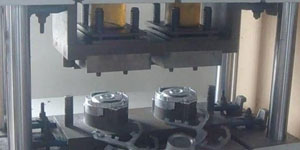
Casting Industries Parts Case Studies for: Cars, Bikes, Aircraft, Musical instruments, Watercraft, Optical devices, Sensors, Models, Electronic devices, Enclosures, Clocks, Machinery, Engines, Furniture, Jewelry, Jigs, Telecom, Lighting, Medical devices, Photographic devices, Robots, Sculptures, Sound equipment, Sporting equipment, Tooling, Toys and more.
What Can we help you do next?
∇ Go To Homepage For Die Casting China
→Casting Parts-Find out what we have done.
→Ralated Tips About Die Casting Services
By Minghe Die Casting Manufacturer |Categories: Helpful Articles |Material Tags: Aluminum Casting, Zinc Casting, Magnesium Casting, Titanium Casting, Stainless Steel Casting, Brass Casting,Bronze Casting,Casting Video,Company History,Aluminum Die Casting |Comments Off