Chromite Sand Application Examples In Casting Production
Chromite sand belongs to the category of special sand in modeling materials. Its main mineral composition is FeO.Cr2O3, density is 4.0~4.8g/cm3, Mohs hardness is 5.5~6, refractoriness is greater than 1900℃, chromite Sand has good resistance to alkaline slag and does not react chemically with iron oxide. Since the thermal conductivity of chromite sand is several times greater than that of silica sand, and solid-phase sintering occurs during molten metal pouring, it is beneficial to prevent the penetration of molten metal. According to these advantages of chromite sand, applying it to the production of various castings can solve the casting quality problems of many products. Our company has achieved many successful applications in many products such as railway vehicle bolsters and side frames, sintering machine fixed screen grate, ball mill liner, electric shovel pushing gear and many other products.
Railway vehicle bolsters and side frames are the main components of the running part of railway vehicles, as well as important stress-bearing parts during the running of the vehicle. The outline size is large, the structure is complex, and the process technology requirements are strict. At some corners), magnetic particle inspection found that there were micro-cracks defects, and anatomical inspection found that there were shrinkage defects at the intersection of the wall and the wall in some parts. According to analysis, compared with other parts, these parts are the "hot spots" formed by the heat of molten steel, and the cooling rate of adjacent parts is different, and the solidification is late, when the cooling and solidification shrinkage is hindered.
When the internal stress is greater than the strength limit of the metal material, the casting will produce micro-crack defects. When these parts cannot be supplemented by molten steel before solidification, shrinkage defects are easily generated. In order to eliminate these defects, the casting technicians of our company stipulate that some sodium silicate chromite sand should be placed in these parts during the process design. Because the thermal conductivity of chromite sand is several times larger than that of silica sand, it can make The solidification speed of this part is balanced with the solidification speed of the adjacent parts, and the microcracks and shrinkage defects generated in these parts are eliminated.
The fixed screen grate is a vulnerable spare part on the sintering machine, and the working condition is to withstand the impact and wear of the sinter at high temperature. The fixed screen grate bar belongs to the plate structure casting. The long, deep and narrow through strip holes are evenly distributed on the casting. When the fixed screen grate bar is produced by the traditional sand casting method, the penetrating strip holes can be formed by the sand core. However, the operation process of this technological scheme is too complicated, and the strip holes on the castings are easily blocked by sticky sand, which is extremely difficult to clean up, resulting in a high rejection rate of the castings. The casting technicians of our company decided to adopt the lost foam casting technology for production. During the process design, it was stipulated that the strip holes on the foam mold of the fixed screen grate should be filled with raw chromite sand during the vibration of the box. Since the chromite sand itself undergoes solid phase sintering during the molten metal pouring process, it is beneficial to prevent the penetration of the molten metal, thereby preventing the strip holes from being blocked by the sticky sand. Using lost foam casting and using the advantages of chromite ore, our company has successfully produced fixed screen grate products. The strip hole wall is smooth and flat, and the size is accurate. After installation and use on the sintering machine, the effect is good, which can meet the needs of sintering production. .
The ball mill liner is the main part of the ball mill used in the beneficiation production of metallurgical mines. It is made of low-alloy steel. The structure is a plate casting with raised wave crests. Two mounting bolt holes are evenly distributed on the liner. The bolt holes have large holes. , The aperture below is small. Because the casting wall around the bolt hole is very thick, the molten steel solidifies slowly after pouring, so that the area around the bolt hole is in a high temperature state for a long time. Sodium silicate sand is used to make the bolt hole sand core. After pouring, the hole is often blocked by sticky sand, which is very clean. It is difficult, and after using the water glass chromite sand core, it takes advantage of its solid-phase sintering during the high-temperature molten metal pouring process and can prevent the penetration of molten metal. The surface roughness and size of the bolt hole of the cast lining board The accuracy meets the specified technical requirements, and the installation effect on the ball mill is good, successfully solving the problem of difficult bolt hole cleaning.
The electric shovel push gear requires that the blank teeth be directly cast. The surrounding area between the teeth and the teeth has a thicker casting wall. After pouring, it is surrounded by high-temperature molten metal. In addition to the heat effect of the upper riser, water glass silica sand is used. During casting, sand sticking at the root of the cast tooth is serious, and the shape and size of the cast tooth cannot be guaranteed after the arc gouging is used. In this regard, the casting technicians of our company decided to use the lost foam casting technology for production. After the white mold of the pushing gear is painted and dried, the chromite sand is pounded with water glass between the casting teeth, and then blow The CO2 is hardened, and then the white mold with sodium silicate chromite sand is packed into the box. After pouring, the chromite sand falls off cleanly, the surface of the cast tooth is smooth and clean, and the shape and dimensional accuracy meet the specified requirements.
Although chromite sand has obvious effects in eliminating micro-cracks, sand sticking and shrinkage defects in castings, improper use can also cause problems. The harmful impurity in chromite sand is carbonate, which decomposes CO2 when it comes into contact with high-temperature molten metal, causing pores on the surface of the casting. Therefore, the chromite ore should be roasted at a high temperature of 900-950°C before preparation and use to decompose the carbonate in it, and then be processed and broken into a certain particle size. The chromite sand that has been stored for a long time and whose ignition loss exceeds the standard should be calcined at a high temperature before use.
In order to ensure the quality requirements of raw chromite ore sand, strict inspection of the chromite ore sand entering the plant is required in accordance with regulations. Firstly, when the chromite ore enters the factory, it is necessary to check its qualified technical documents. If it is unqualified or without technical documents, it is prohibited to enter the factory; the appearance of the chromite ore into the factory should be kept pure and not mixed with any impurities; finally, a sampling inspection of physical and chemical indicators is carried out , The technical conditions that the inspection results should meet are: raw sand particle size 30/50 mesh, Cr2O3≥45%, SiO2≤5%, CaO≤1%, ignition loss ≤1%, refractoriness 1600~1800℃.
In order to ensure the use effect of sodium silicate chromite sand, in addition to the chromite raw sand that meets the specified technical conditions, the technical requirements that the used sodium silicate must meet are: modulus 2.20~2.40, Baume degree 48~52°Be, Water insoluble matter <0.8%. The performance requirements of mixed finishing sand: air permeability ≥250; wet strength 0.05~0.09MPa; moisture ≤5%; dry tensile strength 1.2~3.5MPa.
To achieve the prescribed performance indicators of sodium silicate chromite sand, the following chromite sand preparation process regulations must be strictly implemented.
Before grinding, check whether the operation mechanism of the sand mill is normal. The gap between the grinding wheel and the chassis should be 10-15 mm. Pay attention to frequent observation and adjustment; the water glass chromite mixed in the first mill after the sand mill is washed Special attention should be paid to the control of moisture in the sand. The moisture content of the mill must not exceed the specified 0.5%; the water glass chromite sand preparation operator must often clean the sticky sand on the mill wheel and keep the sand mixer clean to ensure the water glass The chromite sand is evenly mixed and milled; the mixing ratio requirements are: 100% raw sand, 2.5% to 3.5% water glass; mixing time: raw sand + water glass mixing 2 to 3.5 minutes to produce sand; for each preparation All the sodium silicate chromite sands need to be tested for physical properties, and the casting technicians should grasp the test results in order to find problems and deal with them in time.
Please keep the source and address of this article for reprinting: Chromite Sand Application Examples In Casting Production
Minghe Die Casting Company are dedicated to manufacture and provide quality and high performance Casting Parts(metal die casting parts range mainly include Thin-Wall Die Casting,Hot Chamber Die Casting,Cold Chamber Die Casting),Round Service(Die Casting Service,Cnc Machining,Mold Making,Surface Treatment).Any custom Aluminum die casting, magnesium or Zamak/zinc die casting and other castings requirements are welcome to contact us.
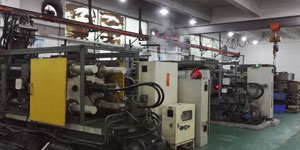
Under the control of ISO9001 and TS 16949,All processes are carried out through hundreds of advanced die casting machines, 5-axis machines, and other facilities, ranging from blasters to Ultra Sonic washing machines.Minghe not only has advanced equipment but also have professional team of experienced engineers,operators and inspectors to make the customer’s design come true.
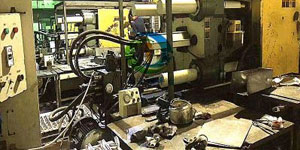
Contract manufacturer of die castings. Capabilities include cold chamber aluminum die casting parts from 0.15 lbs. to 6 lbs., quick change set up, and machining. Value-added services include polishing, vibrating, deburring, shot blasting, painting, plating, coating, assembly, and tooling. Materials worked with include alloys such as 360, 380, 383, and 413.
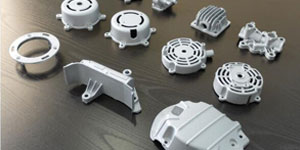
Zinc die casting design assistance/concurrent engineering services. Custom manufacturer of precision zinc die castings. Miniature castings, high pressure die castings, multi-slide mold castings, conventional mold castings, unit die and independent die castings and cavity sealed castings can be manufactured. Castings can be manufactured in lengths and widths up to 24 in. in +/-0.0005 in. tolerance.
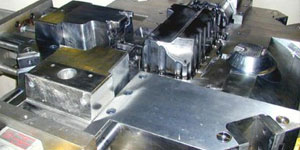
ISO 9001: 2015 certified manufacturer of die cast magnesium, Capabilities include high-pressure magnesium die casting up to 200 ton hot chamber & 3000 ton cold chamber, tooling design, polishing, molding, machining, powder & liquid painting, full QA with CMM capabilities, assembly, packaging & delivery.
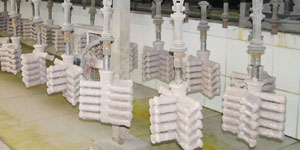
ITAF16949 certified. Additional Casting Service Include investment casting,sand casting,Gravity Casting, Lost Foam Casting,Centrifugal Casting,Vacuum Casting,Permanent Mold Casting,.Capabilities include EDI, engineering assistance, solid modeling and secondary processing.
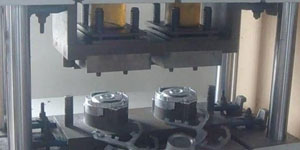
Casting Industries Parts Case Studies for: Cars, Bikes, Aircraft, Musical instruments, Watercraft, Optical devices, Sensors, Models, Electronic devices, Enclosures, Clocks, Machinery, Engines, Furniture, Jewelry, Jigs, Telecom, Lighting, Medical devices, Photographic devices, Robots, Sculptures, Sound equipment, Sporting equipment, Tooling, Toys and more.
What Can we help you do next?
∇ Go To Homepage For Die Casting China
→Casting Parts-Find out what we have done.
→Ralated Tips About Die Casting Services
By Minghe Die Casting Manufacturer |Categories: Helpful Articles |Material Tags: Aluminum Casting, Zinc Casting, Magnesium Casting, Titanium Casting, Stainless Steel Casting, Brass Casting,Bronze Casting,Casting Video,Company History,Aluminum Die Casting |Comments Off