Compressed Air Is Influencing Factor That Determines The Quality Of Die Castings Precision Machining
There are about 12,600 existing die-casting companies and die-casting-related companies in China, of which more than 70% are producing die-casting parts. Companies such as alloys, die-casting machines, molds, melting equipment, coatings, testing equipment, various raw materials, peripheral equipment, and die-casting machine accessories account for about 30%. The output of domestic die-casting parts has long been ranked first in the world, and the GDP has reached 50%. Trillion yuan.
Among the various ownership enterprises, the large-scale annual output of die-casting parts is 10,000 tons, the largest annual output is 60,000 tons, the medium-scaled annual output of die-casting parts is about 5,000 tons, and the small-scale die-casting parts are also several hundred tons. . The proportion of various die castings in the total die castings, aluminum alloy accounted for about 83%, zinc alloy accounted for 15%, and left gold accounted for 2%. Among them, the production of aluminum alloy and other die castings in 2014 was about 5.6 million tons.
The main output of die-casting products is automobile and motorcycle parts. The die-casting parts used on each automobile include gearbox housing, cylinder block, and crankcase quasi-die-casting parts. The average weight of die-casting parts for each automobile is 75 kg. It accounts for more than 50% of the overall domestic production of die castings.
The manufacturing precision requirements of die castings are very high, which mainly include multiple processes such as grinding, cutting, and welding.
In CNC centers, five-axis and three-axis CNC machine tools are mostly used for processing and production. The design of such high-precision machine tools mostly uses a series of high-precision pneumatic actuators such as cylinders. Affected by the traditional technology, the finished products produced by most casting manufacturers often have a high rate of defective products, and the processing accuracy is difficult to meet the requirements, and such problems have not been effectively solved. Many companies are puzzled: Why the machining accuracy of the same imported machine tool in China is far from that of foreign ones?
After searching for the reasons from many sources, it was finally found that the timeliness and accuracy of the movement of a series of pneumatic components such as the cylinders in the original CNC machine tools are crucial to the accuracy of processing, and the movement of pneumatic components is closely related to the quality of the air source. However, in most existing die-casting plants in the configuration of the air compressor system, the most traditional drying method is still used, that is, the post-cooling dryer cooling and drying treatment. The compressed air pressure dew point after cooling and drying is generally +10℃~+15℃ (Higher than the sixth grade requirement of the machinery industry standard JB/T5967-2007);
The pneumatic components used on high-precision CNC machine tools clearly require the pressure dew point to be below +3°C (in line with the fourth-level requirements of the machinery industry standard JB/T5967-2007), and the moisture content in the compressed air seriously exceeds the equipment requirements.
After finding out the reason, the post-processing equipment was rectified immediately, and the original cold dryer was replaced with a core adsorption dryer. After replacement, the pressure dew point can reach -20°C, which fully meets the production requirements. One month later, statistics and analysis of the accuracy of the production of defective products and finished products found that the defective products were reduced by 5% and the accuracy was greatly improved.
Please keep the source and address of this article for reprinting: Compressed Air Is Influencing Factor That Determines The Quality Of Die Castings Precision Machining
Minghe Die Casting Company are dedicated to manufacture and provide quality and high performance Casting Parts(metal die casting parts range mainly include Thin-Wall Die Casting,Hot Chamber Die Casting,Cold Chamber Die Casting),Round Service(Die Casting Service,Cnc Machining,Mold Making,Surface Treatment).Any custom Aluminum die casting, magnesium or Zamak/zinc die casting and other castings requirements are welcome to contact us.
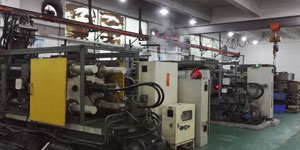
Under the control of ISO9001 and TS 16949,All processes are carried out through hundreds of advanced die casting machines, 5-axis machines, and other facilities, ranging from blasters to Ultra Sonic washing machines.Minghe not only has advanced equipment but also have professional team of experienced engineers,operators and inspectors to make the customer’s design come true.
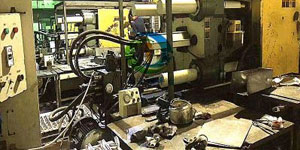
Contract manufacturer of die castings. Capabilities include cold chamber aluminum die casting parts from 0.15 lbs. to 6 lbs., quick change set up, and machining. Value-added services include polishing, vibrating, deburring, shot blasting, painting, plating, coating, assembly, and tooling. Materials worked with include alloys such as 360, 380, 383, and 413.
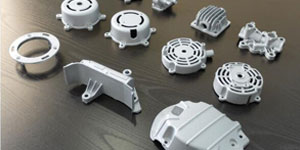
Zinc die casting design assistance/concurrent engineering services. Custom manufacturer of precision zinc die castings. Miniature castings, high pressure die castings, multi-slide mold castings, conventional mold castings, unit die and independent die castings and cavity sealed castings can be manufactured. Castings can be manufactured in lengths and widths up to 24 in. in +/-0.0005 in. tolerance.
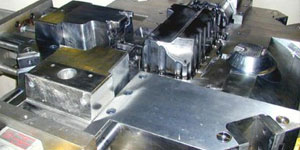
ISO 9001: 2015 certified manufacturer of die cast magnesium, Capabilities include high-pressure magnesium die casting up to 200 ton hot chamber & 3000 ton cold chamber, tooling design, polishing, molding, machining, powder & liquid painting, full QA with CMM capabilities, assembly, packaging & delivery.
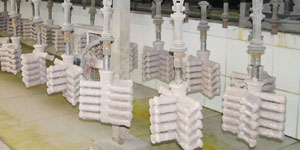
ITAF16949 certified. Additional Casting Service Include investment casting,sand casting,Gravity Casting, Lost Foam Casting,Centrifugal Casting,Vacuum Casting,Permanent Mold Casting,.Capabilities include EDI, engineering assistance, solid modeling and secondary processing.
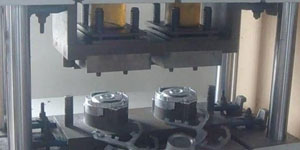
Casting Industries Parts Case Studies for: Cars, Bikes, Aircraft, Musical instruments, Watercraft, Optical devices, Sensors, Models, Electronic devices, Enclosures, Clocks, Machinery, Engines, Furniture, Jewelry, Jigs, Telecom, Lighting, Medical devices, Photographic devices, Robots, Sculptures, Sound equipment, Sporting equipment, Tooling, Toys and more.
What Can we help you do next?
∇ Go To Homepage For Die Casting China
→Casting Parts-Find out what we have done.
→Ralated Tips About Die Casting Services
By Minghe Die Casting Manufacturer |Categories: Helpful Articles |Material Tags: Aluminum Casting, Zinc Casting, Magnesium Casting, Titanium Casting, Stainless Steel Casting, Brass Casting,Bronze Casting,Casting Video,Company History,Aluminum Die Casting |Comments Off