Conditions for the realization of nodular cast iron casting without riser
1 The solidification characteristics of ductile iron
The different solidification methods of nodular cast iron and gray cast iron are caused by the different growth methods of nodular graphite and flake graphite.
In hypoeutectic gray iron, graphite begins to precipitate at the edge of primary austenite. The two sides of the graphite sheet are surrounded by austenite and absorb graphite from the austenite to thicken. The tip of the graphite sheet is in the liquid. It grows by absorbing graphite.
In nodular cast iron, because graphite is spherical, graphite balls begin to absorb graphite around after precipitation. The surrounding liquid becomes solid austenite and surrounds the graphite balls because of the decrease in the amount of w(C); Surrounded by austenite, the only carbon that can be absorbed from the austenite is relatively limited, while the carbon in the liquid diffuses slowly into the graphite ball through the solid, and being surrounded by austenite limits its growth; so Even though the carbon equivalent of nodular cast iron is much higher than that of gray cast iron, the graphitization of nodular cast iron is more difficult, so there is not enough graphitization expansion to offset the solidification shrinkage; therefore, nodular cast iron is prone to shrinkage.
In addition, the thickness of the austenite layer that wraps the graphite ball is generally 1.4 times the diameter of the graphite ball. That is to say, the larger the graphite ball, the thicker the austenite layer, and the more difficult it is for the carbon in the liquid to transfer to the graphite ball through austenite. Great [1].
The fundamental reason why low-silicon ductile iron is prone to white mouth is also the solidification method of ductile iron. As mentioned above, due to the difficulty of graphitization of ductile iron, there is not enough latent heat of crystallization generated by graphitization to be released into the mold, which increases the degree of supercooling, and the graphite does not have time to precipitate to form cementite. In addition, spheroidal graphite cast iron has a rapid growth and decline, which is also one of the factors that are extremely prone to overcooling [1].
2 Conditions for nodular cast iron without riser casting
It is not difficult to see from the solidification characteristics of ductile iron that it is more difficult to achieve riser-free casting for ductile iron parts. Based on my many years of practical experience in production, the author has made some generalizations and summaries about the conditions required for nodular cast iron to realize the riser-free casting process, and share it with colleagues here.
2.1 Selection of molten iron composition
2.1.1 Carbon equivalent (CE)
Under the same conditions, tiny graphite is easy to dissolve in molten iron and is not easy to grow; as the graphite grows, the growth rate of graphite also becomes faster, so the primary graphite is produced before the eutectic in the molten iron to promote the solidification of the eutectic Graphitization is very advantageous. The molten iron with hypereutectic composition can meet such conditions, but the excessively high CE value causes the graphite to grow up before the eutectic solidifies, and when it grows to a certain size, the graphite starts to float, causing graphite floating defects. At this time, the volume expansion caused by graphitization will only cause the molten iron level to rise, which is not only meaningless to the feeding of the casting, but also because the graphite absorbs a large amount of carbon when it is in the liquid state, it will cause the molten iron to solidify when the eutectic is solidified. The low amount of w(C) in the medium cannot produce enough eutectic graphite, and it cannot offset the shrinkage caused by eutectic solidification. Practice has proved that it is ideal to be able to control the CE value between 4.30% and 4.50%.
2.1.2 Silicon (Si)
It is generally believed that in Fe-C-Si alloys, Si is a graphitizing element, and a high amount of w (Si) is beneficial to graphitization expansion and can reduce the occurrence of shrinkage cavities. Few people know that Si hinders eutectic solidification graphitization. Therefore, no matter from the perspective of feeding or preventing the generation of fragmented graphite, as long as the white mouth can be prevented by measures such as strengthening inoculation, the amount of w (Si) must be reduced as much as possible.
2.1.3 Carbon (C)
Under the condition of reasonable CE value, increase the amount of w(C) as much as possible. Facts have proved that the w(C) content of ductile iron is controlled at 3.60%~3.70%, and the casting has the smallest shrinkage rate.
2.1.4 Sulfur (S)
S is the main element that hinders the spheroidization of graphite. The main purpose of spheroidization is to remove S. However, the rapid growth and decline of nodular cast iron is directly related to the low amount of w (S); therefore, an appropriate amount of w (S) is necessary . The amount of w(S) can be controlled at about 0.015%, and the nucleation effect of MgS can be used to increase the graphite core particles to increase the number of graphite spheres and reduce the decline [2].
2.1.5 Magnesium (Mg)
Mg is also an element that hinders graphitization, so under the premise that the spheroidization rate can reach more than 90%, Mg should be as low as possible. Under the condition that the original molten iron w(O) and w(S) are not high, the residual w(Mg) content can be controlled within 0.03%~0.04% is the most ideal.
2.1.6 Other elements
Mn, P, Cr and other elements that hinder graphitization are as low as possible.
Pay attention to the influence of trace elements, such as Ti. When the amount of w (Ti) is low, it is an element that strongly promotes graphitization. At the same time, Ti is an element that forms carbides and an element that affects spheroidization and promotes the production of vermicular graphite. Therefore, the lower the amount of w (Ti), the better . The author’s company once had a very mature non-riser casting process. Due to a temporary shortage of raw materials, pig iron with a w(Ti) content of 0.1% was used. Not only did the castings produced have surface shrinkage, but also concentrated types appeared inside after processing. Shrinkage.
In short, pure raw materials are beneficial to improve the self-feeding ability of ductile iron.
2.2 Pouring temperature
Experiments have shown that the pouring temperature of ductile iron from 1 350 ℃ to 1500 ℃ has no obvious effect on the shrinkage volume of the casting, but the morphology of shrinkage cavity gradually transitions from concentrated type to dispersed type. The size of graphite balls gradually increases with the increase of pouring temperature, and the number of graphite balls gradually decreases. Therefore, there is no need to demand a too low pouring temperature. As long as the mold is strong enough to resist the static pressure of the molten iron, the pouring temperature can be higher. The molten iron is used to heat the mold to reduce the degree of undercooling during the eutectic solidification, so that the graphitization has sufficient time to proceed. However, the pouring speed should be as fast as possible to minimize the temperature difference of the molten iron in the mold [3].
2.3 Cold iron
Based on the author's experience in using cold iron and the above theoretical analysis, the claim that cold iron can eliminate shrinkage defects is not accurate. On the one hand, the local use of cold iron (such as perforated parts) can only transfer the shrinkage cavity rather than eliminate it; on the other hand, the use of cold iron on a large area can achieve the effect of reducing feeding or no riser. Unconsciously increasing the mold strength instead of cold iron reduces the liquid or eutectic solidification shrinkage. In fact, if the cold iron is used too much, it will affect the growth of the graphite ball and the degree of graphitization, on the contrary it will aggravate the shrinkage.
2.4 Mould strength and stiffness
Since ductile iron mostly chooses eutectic or hypereutectic composition, it takes a longer time for the molten iron to cool to the eutectic temperature in the mold, that is, the hydrostatic pressure of the mold is longer than that of the eutectic composition. If the gray cast iron is longer, the mold is more prone to compressive deformation. When the volume increase caused by graphitization expansion cannot offset the liquid shrinkage + solidification shrinkage + mold deformation volume, shrinkage cavities are inevitable. Therefore, sufficient mold rigidity and compressive strength are important conditions for realizing riser-free casting. There are many sand-coated iron casting processes to realize riser-free casting is the proof of this theory.
2.5 Inoculation treatment
The powerful inoculant and the instant delay inoculation process can not only give the molten iron a large amount of core particles, but also prevent the inoculation from declining, and can ensure that the ductile iron has enough graphite balls during the eutectic solidification; the large and small graphite balls reduce The transfer distance of C in the liquid to the graphite core speeds up the graphitization speed. In a short time, a large amount of eutectic solidification can release more latent heat of crystallization, reduce the degree of supercooling, and prevent the generation of white mouths, but also Can strengthen graphitization expansion. thus. Strong inoculation is essential to improve the self-feeding ability of ductile iron.
2.6 Liquid iron filtration
After the molten iron is filtered, some oxidized inclusions are filtered out, so that the micro-fluidity of the molten iron is enhanced, and the probability of microscopic shrinkage can be reduced.
2.7 Casting modulus
Since as-cast pearlitic ductile iron needs to add elements that hinder graphitization, this will affect the degree of graphitization and have a certain impact on the realization of self-feeding of the castings. Therefore, there are data introductions. Riser-free casting is suitable for ductile graphites below QT500. cast iron. In addition, the modulus determined by the shape and size of the casting should be at least 3.1 cm.
It is worth noting that it is difficult to achieve riser-free casting of plate castings with a thickness of less than 50 mm.
There are also information that the condition for realizing the riser-free casting process for nodular cast iron above QT500 is that its modulus should be greater than 3.6 cm.
Please keep the source and address of this article for reprinting: Conditions for the realization of nodular cast iron casting without riser
Minghe Die Casting Company are dedicated to manufacture and provide quality and high performance Casting Parts(metal die casting parts range mainly include Thin-Wall Die Casting,Hot Chamber Die Casting,Cold Chamber Die Casting),Round Service(Die Casting Service,Cnc Machining,Mold Making,Surface Treatment).Any custom Aluminum die casting, magnesium or Zamak/zinc die casting and other castings requirements are welcome to contact us.
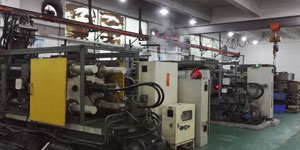
Under the control of ISO9001 and TS 16949,All processes are carried out through hundreds of advanced die casting machines, 5-axis machines, and other facilities, ranging from blasters to Ultra Sonic washing machines.Minghe not only has advanced equipment but also have professional team of experienced engineers,operators and inspectors to make the customer’s design come true.
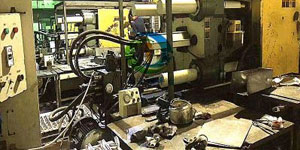
Contract manufacturer of die castings. Capabilities include cold chamber aluminum die casting parts from 0.15 lbs. to 6 lbs., quick change set up, and machining. Value-added services include polishing, vibrating, deburring, shot blasting, painting, plating, coating, assembly, and tooling. Materials worked with include alloys such as 360, 380, 383, and 413.
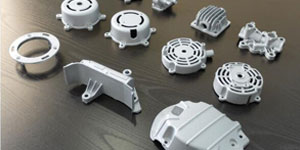
Zinc die casting design assistance/concurrent engineering services. Custom manufacturer of precision zinc die castings. Miniature castings, high pressure die castings, multi-slide mold castings, conventional mold castings, unit die and independent die castings and cavity sealed castings can be manufactured. Castings can be manufactured in lengths and widths up to 24 in. in +/-0.0005 in. tolerance.
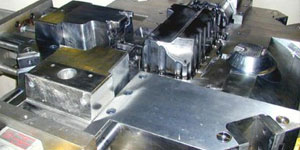
ISO 9001: 2015 certified manufacturer of die cast magnesium, Capabilities include high-pressure magnesium die casting up to 200 ton hot chamber & 3000 ton cold chamber, tooling design, polishing, molding, machining, powder & liquid painting, full QA with CMM capabilities, assembly, packaging & delivery.
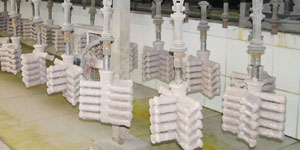
ITAF16949 certified. Additional Casting Service Include investment casting,sand casting,Gravity Casting, Lost Foam Casting,Centrifugal Casting,Vacuum Casting,Permanent Mold Casting,.Capabilities include EDI, engineering assistance, solid modeling and secondary processing.
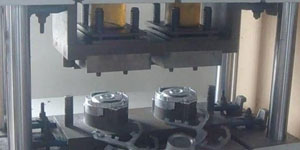
Casting Industries Parts Case Studies for: Cars, Bikes, Aircraft, Musical instruments, Watercraft, Optical devices, Sensors, Models, Electronic devices, Enclosures, Clocks, Machinery, Engines, Furniture, Jewelry, Jigs, Telecom, Lighting, Medical devices, Photographic devices, Robots, Sculptures, Sound equipment, Sporting equipment, Tooling, Toys and more.
What Can we help you do next?
∇ Go To Homepage For Die Casting China
→Casting Parts-Find out what we have done.
→Ralated Tips About Die Casting Services
By Minghe Die Casting Manufacturer |Categories: Helpful Articles |Material Tags: Aluminum Casting, Zinc Casting, Magnesium Casting, Titanium Casting, Stainless Steel Casting, Brass Casting,Bronze Casting,Casting Video,Company History,Aluminum Die Casting |Comments Off