Die Casting- A Typical Digital Industry Case Sharing
Die casting, also known as high pressure casting, is a near net shape technology that has been widely used in the automotive, aerospace, and electronics industries in recent years. In the die-casting process, molten metal (usually light alloy) fills the cavity at high pressure and high speed under the action of the punch, and cools quickly to form the final casting.
Die-casting is generally divided into cold-chamber die-casting and hot-chamber die-casting. Cold-chamber die-casting is mainly used in the production of large parts, such as auto parts, communication base station cooling components, etc.; hot-chamber die-casting is widely used in the production of small electronics or 3C products Process, such as USB connector, laptop case, etc.
1. Die Casting Has A Good Foundation For Automation
Compared with the ordinary casting process, die casting is characterized by high speed and high pressure. The products produced are generally light alloy thin-walled parts, but die casting technology is also applied to the production of pure copper rotors. Unlike aluminum and magnesium alloys, pure copper The melting point is very high, so short die life in the pure copper die-casting process is a big problem.
Among all casting technologies, die casting has the highest degree of automation. Modern die-casting companies adopt automated die-casting island technology, which highly integrates die-casting machines (generally dozens or even hundreds) to form a fully automated production process. At the same time, the intelligent factory technology is adopted to monitor the production process of the die-casting machine, and the performance and status of each die-casting machine can be grasped in real time. Through big data measurement and real-time feedback, the production process of the die-casting machine can be adjusted in time to ensure The final quality of the product.
The real-time control of die-casting mold temperature is a simple example:
Take cold chamber die-casting as an example. In the production process, the mold temperature is continuously increased due to the high-temperature liquid metal continuously filling the cavity. At this time, in order to ensure that the mold temperature is not overheated, cooling water is generally used to pass into the mold for cooling. If the cooling water pipeline design is reasonable, generally speaking, we can ensure that the mold temperature reaches the so-called thermal balance by controlling the temperature and flow rate of the cooling water. From this point of view, we can design a cooling water feedback system. After knowing the actual value of the mold temperature, the temperature and flow rate of the cooling water can be controlled through calculation and an instant feedback system, and finally the temperature of the mold can be controlled. This is a typical application of the die-casting smart factory at this stage.
In fact, the above-mentioned case of intelligent control is only a small application scenario in the "smart factory". Realizing a true "smart factory" requires the collection of a large amount of real-time production data, among which data related to product quality plays a decisive role , Such as density, porosity and oxidized inclusions, because these data are the indicators that customers care about most, and they are also the core indicators to measure whether a casting is qualified. At this stage, these most critical indicators are the most difficult to obtain, because for metal alloy products, we cannot directly observe the internal structure of the product. The method adopted by most manufacturers is to spot check castings, cut in key areas clearly defined by the customer, and then directly observe whether there are problems; another method is to use two-dimensional X-ray inspection technology to scan and scan the local positions of the sampled castings. Observation, the biggest problem with this method is that the three-dimensional casting information is compressed onto two-dimensional slices, and the information obtained by observation cannot fully reflect the actual situation.
2. Internal Quality Control Of Castings
With the continuous development of the automobile industry, the requirements for the quality of parts and components are getting higher and higher. Large automobile manufacturers continue to formulate requirements for the internal quality of parts and components, and quantitatively specify the standards that can exist for internal defects in parts. In this case, component suppliers must be able to detect and calibrate the distribution of defects in all castings in real time during the production process, and compare standards to assess whether the castings meet the requirements.
So how to correctly observe and record the defects inside the casting? The best technology in the existing technology is computer tomography, which is what we commonly call CT technology. CT technology has been widely used in the medical field, and the application of CT technology to industrial inspection is still a technology that has just emerged in recent years.
To apply CT technology to the inspection of the internal quality of castings, the following requirements must be met:
- The inspection speed must be high enough to match the real-time production process of castings;
- The quality of the image obtained by the detection must be good enough to cooperate with the accurate recognition of the image by the subsequent software;
- In the case of ensuring accuracy, the software or algorithm that recognizes the image must be fast enough so as not to delay the production schedule.
Among them, the first two requirements are for the CT detection itself, and the last one is for the detection software or algorithm. Taking an overview of the current CT technology, we will find that the most promising inspection instrument is the Speed-Scan CT equipment (Speed-Scan) produced by General Electric, and this equipment has been used by Volkswagen in Germany for actual castings. Detected. However, looking at the domestic die-casting industry, the use of real-time CT technology to control the quality of castings is severely challenging from an operational perspective. The biggest constraint is cost-the cost of CT inspection equipment is extremely high, and it is used for The production line generally requires a large amount of CT inspection equipment, which cannot be afforded by most domestic enterprises. With the continuous development of the industry and the continuous improvement of casting quality requirements, the use of CT technology to detect the internal quality of castings in real time will be a general requirement for suppliers of OEMs in the future.
3. Process Feedback And Adjustment
Under the premise that the casting is inspected by CT and the three-dimensional solid data is obtained, we assume that there is an algorithm that can analyze the data in a very efficient manner and give all the information about the internal defects of the casting, including type, size and Distribution, etc., then we can use this information to adjust and modify the production process itself, and finally obtain qualified castings without excessive defects. This process-the process of obtaining casting information and revising the process, we call it the process of process feedback and adjustment. Of course, we can't just complete this process based on the information of one casting. The most normal situation should be to obtain information about a large number of castings, and solve the defects of castings through statistical analysis and process-related methods.
The next question is, even if we obtain a large amount of information on the distribution of defects inside the casting, how can we adjust the process parameters to avoid unqualified defects? The most powerful analysis tool available is computer numerical simulation, which is also known as computer-aided engineering (CAE) technology.
Using computer simulation technology, we can realize virtual production in a local sense. Especially for die casting, we can directly simulate the filling and solidification process by studying the velocity, pressure, flow pattern, and splashing of the fluid filling cavity. To judge whether there is entrainment in the filling process; to judge and study the potential hot spots, casting defects (shrinkage cavity, shrinkage porosity) and heat balance behavior of the die casting by calculating the temperature changes of the casting and the mold under different die casting cycle conditions . Through this kind of numerical simulation technology, based on certain analysis conditions, we can judge and avoid the internal defects of the casting to a large extent, improve the performance of the casting and greatly increase the production efficiency, and achieve the process feedback and correction we discussed before. purpose.
We string together the whole process: use digital technology (CT) to detect the three-dimensional defect data of the product in real time, and if the product is unqualified, the data will be transmitted to the CAE analysis center, and the analog simulation technology will be used to analyze and produce defect problem solutions, and solution feedback Go to the front end of the production and process to execute and re-obtain the product. The product continues to undergo digital inspection and obtain three-dimensional defect data. If the product is qualified, the iteration ends, otherwise it continues.
4. Master The Core Digital Technology
It can be seen that CAE analysis plays a key role in this process, and the effectiveness of the proposed solution will have an impact on the efficiency of the entire process. In fact, whether you can master the core of CAE technology and whether you can well apply numerical simulation technology in actual production can measure the technical capabilities of a die-casting company to a large extent, because digital technology is a must for the company Road, the sooner you master the core of digital technology on this road, the more you can stand out in the future corporate competition.
Therefore, if the digital inspection technology and CAE analysis technology are well applied to the existing die-casting enterprises, we can see a complete and typical digital factory scene. Among them, digital detection technology realizes the digitization of physical entities, while CAE analysis technology transforms the digital information obtained from detection into problem solutions based on virtual production. In this process, digital detection is actually a fully automated process, while CAE analysis is still Need human participation. If CAE analysis can be solidified into an algorithm and fully automated, then this is the embryonic form of the future intelligent digital factory.
Related Page: die casting consultation/die casting services/die casting video/die casting products
Related Articles:
- What Is Mold Trial For Die Casting
- The Quality Control of Die Casting Aluminum Alloy Parts
- What Is Pressure Die Casting?
- The Process Analysis of New Type Die Casting Automotive Parts
Please keep the source and address of this article for reprinting:Die Casting- A Typical Digital Industry Case Sharing
Minghe Die Casting Company are dedicated to manufacture and provide quality and high performance Casting Parts(metal die casting parts range mainly include Thin-Wall Die Casting,Hot Chamber Die Casting,Cold Chamber Die Casting),Round Service(Die Casting Service,Cnc Machining,Mold Making,Surface Treatment).Any custom Aluminum die casting, magnesium or Zamak/zinc die casting and other castings requirements are welcome to contact us.
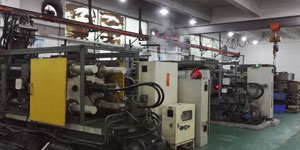
Under the control of ISO9001 and TS 16949,All processes are carried out through hundreds of advanced die casting machines, 5-axis machines, and other facilities, ranging from blasters to Ultra Sonic washing machines.Minghe not only has advanced equipment but also have professional team of experienced engineers,operators and inspectors to make the customer’s design come true.
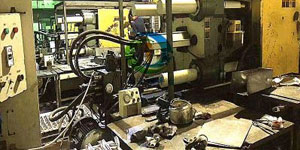
Contract manufacturer of die castings. Capabilities include cold chamber aluminum die casting parts from 0.15 lbs. to 6 lbs., quick change set up, and machining. Value-added services include polishing, vibrating, deburring, shot blasting, painting, plating, coating, assembly, and tooling. Materials worked with include alloys such as 360, 380, 383, and 413.
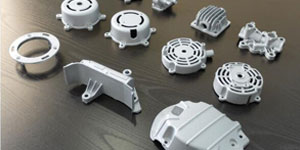
Zinc die casting design assistance/concurrent engineering services. Custom manufacturer of precision zinc die castings. Miniature castings, high pressure die castings, multi-slide mold castings, conventional mold castings, unit die and independent die castings and cavity sealed castings can be manufactured. Castings can be manufactured in lengths and widths up to 24 in. in +/-0.0005 in. tolerance.
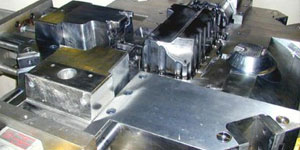
ISO 9001: 2015 certified manufacturer of die cast magnesium, Capabilities include high-pressure magnesium die casting up to 200 ton hot chamber & 3000 ton cold chamber, tooling design, polishing, molding, machining, powder & liquid painting, full QA with CMM capabilities, assembly, packaging & delivery.
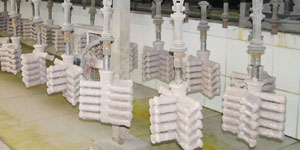
ITAF16949 certified. Additional Casting Service Include investment casting,sand casting,Gravity Casting, Lost Foam Casting,Centrifugal Casting,Vacuum Casting,Permanent Mold Casting,.Capabilities include EDI, engineering assistance, solid modeling and secondary processing.
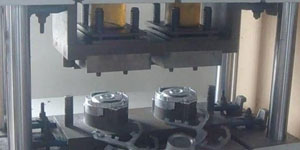
Casting Industries Parts Case Studies for: Cars, Bikes, Aircraft, Musical instruments, Watercraft, Optical devices, Sensors, Models, Electronic devices, Enclosures, Clocks, Machinery, Engines, Furniture, Jewelry, Jigs, Telecom, Lighting, Medical devices, Photographic devices, Robots, Sculptures, Sound equipment, Sporting equipment, Tooling, Toys and more.
What Can we help you do next?
∇ Go To Homepage For Die Casting China
→Casting Parts-Find out what we have done.
→Ralated Tips About Die Casting Services
By Minghe Die Casting Manufacturer |Categories: Helpful Articles |Material Tags: Aluminum Casting, Zinc Casting, Magnesium Casting, Titanium Casting, Stainless Steel Casting, Brass Casting,Bronze Casting,Casting Video,Company History,Aluminum Die Casting |Comments Off