Die casting release agent can improve production efficiency and quality problems
The role of die-casting release agent is to improve the production efficiency and product quality of castings, while minimizing the negative impact of workplaces and wastewater discharge on the environment. From the perspective of demolding, any factor that hinders the smooth demolding of the casting is a problem. Based on our long-term experience in the die casting industry, including the research we did when we were recognized as an industry leader by the Die Casting Research Foundation in the late 1960s, as well as our customers in the workshop, we know that you may encounter The problem. These problems include: adhesion, porosity, scaling in the cavity, carbon deposits, cold barriers, white spots, and environmental challenges.
Sticky mold
The welding on the mold is the result of adhesion between the molten alloy and the mold steel. High temperature and corrosion will exacerbate adhesion problems, which are more common in special areas of the mold. The formation of a barrier coating between the molten metal and the tool steel can prevent mold sticking. Certain alloys are easier to mold. The famous brand release agent adopts advanced technology to develop a variety of die-casting lubricants to meet the requirements of different temperature ranges and alloy materials. The proprietary polymer of the well-known brand release agent ensures excellent die-casting effect under high temperature conditions. Silicone-free series of mold release agents can be applied to mold surfaces with lower temperatures.
Porous
Porosity is the biggest problem in the die casting process. The die casting process is usually used to make lightweight parts using light metals instead of steel or iron parts. Since the inherent strength of light metals is lower than that of steel parts, any reduction in the strength of the parts should be avoided. The small holes in the cross section of the casting have a greater impact on its tensile strength.
There are two main types of stomata, one is stomata. The pores are the result of the process of molten metal being injected into the mold at high speed. However, the presence of moisture in the mold or the decomposition of any organic compounds in the mold or cylinder will aggravate the pore phenomenon. Since all molds and stamping lubricants may contain moisture, organic matter, or both, these substances may cause porosity problems. The well-designed product of the famous brand release agent produces only a small amount of decomposition products, and all the water has been evaporated or blown dry before the molten metal is injected into the mold, so it can minimize the phenomenon of pores.
Porosity can also be minimized by providing overflow ports and exhaust ports. These two methods allow the air in the mold cavity and any decomposition products to escape from the casting before the metal solidifies. The proper cylinder size and filling speed can minimize the blowhole phenomenon, but the correct position of the exhaust hole and the size of the exhaust slag bag are essential for the production of high-quality castings. In addition, the choice of die-casting release agent will also affect the effect of exhaust. Die-casting lubricant is usually sprayed into the mold cavity, but no matter what the operation, the sprayed release agent may exceed the target area, such as spraying on the exhaust port. This is what we usually call overspray.
Overspray on the mold As the water evaporates, a lubricating film is formed on the surface of the vent. Unlike the lubricating film in the mold cavity, the lubricating film formed on the surface of the vent hole cannot be completely removed when the casting is separated from the mold. Over time, it will obstruct the flow path of the escape gas. The well-known mold release agent brand has recently focused on this field. Our latest die-casting release agent can minimize the overspray of general die-casting release agent, thereby further improving the quality of castings.
The reason for the shrinkage is that the liquid density of most cast metals is slightly lower than the solid density. This means that the volume of the metal will decrease during the solidification process. As long as the liquid metal can enter the casting before solidification, the shrinkage cavity will be minimized.
Unfortunately, due to the large number of cross-sections of castings, "mold hot spots" are inevitable. This part of the casting remains liquid after the other parts are solidified, so shrinkage cavities will be formed during solidification. The best way to solve the shrinkage problem is to improve the cavity design and strengthen the pressure and metal temperature. The brand-name mold release agent die casting mold release agent controls the generation of "overheating zone" by improving the cooling performance, thereby helping to solve the above-mentioned problems.
Scaling/carbon in the cavity
Carbon or dark impurities in the cavity are called "carbon" or accumulation in the cavity. This is very different from welding, because these impurities are not attached to the metal, but a thin film layer attached to the surface, which can be removed without chemically dissolving the alloy. When the die-casting release agent is sprayed on the surface of the mold, only a laminated cast release agent film is left after the moisture evaporates, which helps to release the mold and avoid welding. The film is usually removed when the casting is released. In some cases, especially when the mold temperature is lower than the rated temperature, this layer of lubricating film cannot be completely removed, so scaling will occur in the mold cavity. The best solution is to reduce the amount of die-casting release agent. However, because the local temperature of each part of a complex mold may vary greatly, in order to reduce fouling, reducing the amount of die-casting release agent may cause welding. The famous brand release agent die casting release agent can form a perfectly balanced film on the surface of the high temperature and low temperature mold, thereby alleviating the above problems while forming a unified protection.
The main cause of cavity fouling is the water that dilutes the release agent. Under normal circumstances, it is recommended to use softened water to dilute the die-casting release agent. If hard water is used, the dissolved calcium and magnesium salts will precipitate after the water evaporates. These components cannot be decomposed by molten metal, so deposits are easily formed in the cavity. The chemical composition analysis of the residue in the cavity usually indicates the presence of die-casting release agent, but the root cause of the solid salt is the water that dilutes the release agent. Disturbances in the water softening system can cause solid deposits in the mold cavity.
Cold barrier
The surface of the casting sometimes shows dark traces left by the flow path of the molten metal. This situation is particularly obvious in the cross-section of magnesium alloys and thin-walled castings. In extreme cases, the casting cannot even be completely filled. In other cases, similar cracks will appear on the surface of the casting, which is actually a trace left by the two layers of metal surfaces that are not completely fused during solidification. This condition is sometimes referred to as "cold isolation". This situation indicates that the casting has begun to solidify when the filler is not full. This may be caused by too low mold temperature, too low melting temperature or excessive cooling. You can use the famous brand release agent die casting release agent to adjust the heat transfer rate of the mold, so as to effectively avoid the problems that may be caused by the unsatisfactory casting material.
White dot
Example of "fish eye" paint defect A common concern for die-casting release agents is the possible negative impact on the castings during operations such as coating, plating or gluing. Since the main function of the release agent is to prevent adhesion between the casting and the mold surface, the use of the release agent may affect the adhesion or plating of the coating. If the release agent is not completely removed during the cleaning process, "white spots" may occur. . It can be easily cleaned with alkaline lotion before spraying or electroplating process.
Environmental challenge
The first release agent developed was an oil agent, which was manually used in hot molds before injecting molten metal. This will cause major harm to human health and safety, Famous brand of release agent took the lead in developing a safer alternative release agent. Today's water-based die-casting release agents can be used in most die-casting operations.
Water-based lubricants are usually concentrated emulsions, which are diluted with water at the die casting site before use. As a leading company in the industry, Famous brand of release agent has always been committed to developing unique new formulas to meet the technical challenges faced by the continuous development of the industry. In the past ten years, we have continuously improved the quality of our products by increasing the dilution ratio and reducing the environmental impact.
The recently developed innovative products can not only be used in extremely high temperature molds, but also can greatly reduce the fouling caused by overspray on the mold surface and significantly improve the production efficiency of die-casting operations. To understand the tangible benefits of our die-casting processing aids for production, please refer to the following case studies: Auxiliary products increase value, product innovation improves production efficiency and product performance saves operating costs.
The use of dilution water will produce a large amount of liquid water. To solve this problem, Famous brand of release agent has developed a series of dry powder die-casting release agents, which can rely on static electricity or air to adhere to the mold surface. Such products will melt and flow over the mold surface after contact with the hot mold surface, thereby forming a thin protective film on the mold surface. The dry powder die-casting release agent will not cause thermal shock to the mold surface, so it can minimize metal fatigue and extend the life of the mold.
Famous brand of release agent has also developed a series of solvent-based die-casting release agents for applications with shorter cycle times and lower mold temperatures. In the effective application process, the low frequency application and low operating temperature of such products can not only minimize the risk of fire, but also produce clean and bright castings.
Please keep the source and address of this article for reprinting: Die casting release agent can improve production efficiency and quality problems
Minghe Die Casting Company are dedicated to manufacture and provide quality and high performance Casting Parts(metal die casting parts range mainly include Thin-Wall Die Casting,Hot Chamber Die Casting,Cold Chamber Die Casting),Round Service(Die Casting Service,Cnc Machining,Mold Making,Surface Treatment).Any custom Aluminum die casting, magnesium or Zamak/zinc die casting and other castings requirements are welcome to contact us.
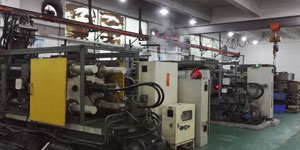
Under the control of ISO9001 and TS 16949,All processes are carried out through hundreds of advanced die casting machines, 5-axis machines, and other facilities, ranging from blasters to Ultra Sonic washing machines.Minghe not only has advanced equipment but also have professional team of experienced engineers,operators and inspectors to make the customer’s design come true.
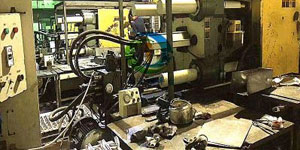
Contract manufacturer of die castings. Capabilities include cold chamber aluminum die casting parts from 0.15 lbs. to 6 lbs., quick change set up, and machining. Value-added services include polishing, vibrating, deburring, shot blasting, painting, plating, coating, assembly, and tooling. Materials worked with include alloys such as 360, 380, 383, and 413.
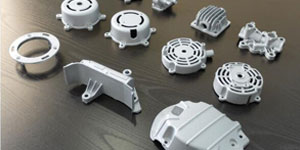
Zinc die casting design assistance/concurrent engineering services. Custom manufacturer of precision zinc die castings. Miniature castings, high pressure die castings, multi-slide mold castings, conventional mold castings, unit die and independent die castings and cavity sealed castings can be manufactured. Castings can be manufactured in lengths and widths up to 24 in. in +/-0.0005 in. tolerance.
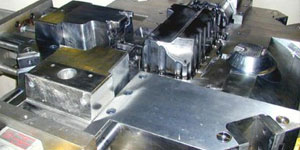
ISO 9001: 2015 certified manufacturer of die cast magnesium, Capabilities include high-pressure magnesium die casting up to 200 ton hot chamber & 3000 ton cold chamber, tooling design, polishing, molding, machining, powder & liquid painting, full QA with CMM capabilities, assembly, packaging & delivery.
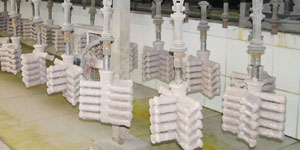
ITAF16949 certified. Additional Casting Service Include investment casting,sand casting,Gravity Casting, Lost Foam Casting,Centrifugal Casting,Vacuum Casting,Permanent Mold Casting,.Capabilities include EDI, engineering assistance, solid modeling and secondary processing.
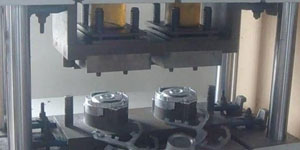
Casting Industries Parts Case Studies for: Cars, Bikes, Aircraft, Musical instruments, Watercraft, Optical devices, Sensors, Models, Electronic devices, Enclosures, Clocks, Machinery, Engines, Furniture, Jewelry, Jigs, Telecom, Lighting, Medical devices, Photographic devices, Robots, Sculptures, Sound equipment, Sporting equipment, Tooling, Toys and more.
What Can we help you do next?
∇ Go To Homepage For Die Casting China
→Casting Parts-Find out what we have done.
→Ralated Tips About Die Casting Services
By Minghe Die Casting Manufacturer |Categories: Helpful Articles |Material Tags: Aluminum Casting, Zinc Casting, Magnesium Casting, Titanium Casting, Stainless Steel Casting, Brass Casting,Bronze Casting,Casting Video,Company History,Aluminum Die Casting |Comments Off