Differences In The Solidification Characteristics Of Ductile Iron
Generally speaking, ductile iron castings have a much greater tendency to shrinkage and porosity than gray iron castings. Preventing shrinkage defects is often a very difficult problem in process design. In this regard, the experience summarized from actual production is very inconsistent, and each has its own opinions: some people think that the principle of sequential solidification should be followed, and a large riser should be placed in the final solidification position to supplement the volume generated during the solidification process of the casting. Shrinkage; Some people think that nodular cast iron parts only need small risers, and sometimes sound castings can be produced without risers.
To maximize the production rate of the process while ensuring the quality of castings, it is not enough to control the chemical composition of cast iron. On the basis of understanding the solidification characteristics of ductile iron, it is necessary to effectively control the smelting, spheroidization, inoculation and treatment of cast iron. In the whole process of pouring operation, the rigidity of the mold must be effectively controlled.
1. The Solidification Characteristics Of Ductile Iron
Most of the nodular cast iron used in actual production is close to the eutectic composition. Thick-walled castings use hypoeutectic composition, and thin-walled castings use hypereutectic composition, but they are not far from eutectic composition.
For ductile iron with eutectic and hypereutectic components, small graphite balls are first precipitated from the liquid phase during eutectic solidification. Even for nodular cast iron with hypoeutectic composition, due to the increase in the degree of supercooling of the molten iron after the spheroidization and inoculation treatment, small graphite balls will be precipitated first at a temperature much higher than the equilibrium eutectic transition temperature. The first batch of small graphite spheres have been formed at temperatures of 1300°C or higher.
In the subsequent solidification process, as the temperature decreases, some of the first small graphite spheres grow up, and some are re-dissolved into the molten iron, and new graphite spheres will also be precipitated. The precipitation and growth of graphite spheres are carried out in a wide temperature range.
When the graphite ball grows up, the carbon content in the molten iron around it decreases, and an austenite shell surrounding the graphite ball will be formed around the graphite ball. The formation time of the austenite crust is related to the cooling rate of the casting in the mold: the cooling rate is high, and the carbon in the molten iron does not have time to diffuse uniformly, and the austenite crust is formed earlier; the cooling rate is low, which is beneficial to the cooling rate in the molten iron. The carbon diffuses uniformly, and the austenite crust is formed later.
Before the austenite shell is formed, the graphite ball directly contacts the molten iron with high carbon content, and the carbon in the molten iron is easy to diffuse into the graphite ball, so that the graphite ball grows up. After the austenite shell is formed, the diffusion of carbon in the molten iron to the graphite balls is hindered, and the growth rate of the graphite balls drops sharply. Because the latent heat of crystallization released when graphite is precipitated from molten iron is large, about 3600 J/g, the latent heat of crystallization released when austenite is precipitated from molten iron is less, about 200 J/g, forming an austenite shell around the graphite ball The growth of graphite balls is hindered, which will significantly slow down the release of crystallization latent heat. Under these conditions, the progress of eutectic solidification depends on further lowering the temperature to produce new crystal nuclei. Therefore, the eutectic transformation of spheroidal graphite cast iron has to be completed within a relatively large temperature range, and the solidification temperature range is twice or more than that of gray cast iron, which has typical paste-like solidification characteristics.
In short, the solidification characteristics of ductile iron mainly have the following aspects.
1. Wide solidification temperature range
From the equilibrium diagram of the iron-carbon alloy, the solidification temperature range is not wide near the eutectic composition. In fact, after the spheroidization and inoculation treatment of molten iron, the solidification process deviates far from the equilibrium conditions. At about 150°C above the eutectic transition temperature (1150°C), graphite spheres begin to precipitate, and the temperature at which the eutectic transition ends again It may be about 50°C lower than the equilibrium eutectic transition temperature.
An alloy with such a wide solidification temperature range is solidified in a paste-like solidification manner, and it is difficult to achieve sequential solidification of castings. Therefore, according to the design principle of the riser of the steel castings, the process plan of realizing the sequential solidification of the castings, and setting a large riser at the last solidified hot joint is not very suitable.
Because graphite spheres are precipitated at very high temperatures and eutectic transformation occurs, the liquid-solid two phases coexist for a long time, and liquid shrinkage and solidification shrinkage occur simultaneously during the solidification of molten iron. Therefore, it is impossible to fully supplement the liquid shrinkage through the gating system and riser like steel castings.
2. The precipitation of graphite during the eutectic transformation leads to volume expansion
Near the eutectic temperature, the density of austenite is about 7.3g/cm3, and the density of graphite is about 2.15g/cm3. During the solidification of the casting, the precipitation of graphite will cause the volume expansion of the system. About 1% (mass fraction) of graphite precipitated can produce 3.4% volume expansion.
Proper use of the graphitization expansion in cast iron can effectively compensate for the volume shrinkage during solidification. Under certain conditions, sound castings can be produced without risers.
It should be emphasized that both gray cast iron and nodular cast iron precipitate graphite during the eutectic transformation process and undergo volume expansion. However, due to the different graphite morphology and growth mechanism in the two cast irons, the effect of graphitization expansion on the casting performance of cast iron It's also very different.
For the flake graphite in the eutectic cluster of gray cast iron, the tip that is in direct contact with the molten iron preferentially grows. Most of the volume expansion caused by the growth of graphite acts on the molten iron in contact with the graphite tip, which is beneficial to forcing it to fill with austenite branches. The gap between them makes the casting more dense.
The graphite in nodular cast iron is grown under the condition of being surrounded by an austenite shell. The volume expansion that occurs when the graphite ball grows up is mainly through the austenite shell acting on the adjacent eutectic clusters, which may be Squeezing out expands the gap between the eutectic clusters, and it is easy to act on the mold walls of the mold through the eutectic clusters, causing the mold walls to move.
3. Graphitization expansion during the solidification of the casting is easy to cause the mold to move in the wall
Nodular cast iron solidifies in a paste-like solidification method. When the casting starts to solidify, the outer surface layer of the casting at the mold-metal interface is much thinner than gray cast iron, and it grows slowly. Even after a long time, the surface layer is still strong. Thin shell with low rigidity. When graphitized expansion occurs inside, the outer shell may move outwards if it is not strong enough to withstand the expansion force. If the rigidity of the mold is poor, the wall motion will occur and the cavity will expand. As a result, not only the dimensional accuracy of the casting is affected, but the shrinkage after graphitization expansion cannot be supplemented, and defects such as shrinkage cavity and porosity will be generated inside the casting.
4. The carbon content in eutectic austenite is higher than that in gray cast iron
According to a research report by R. W. Heine in the United States, during the eutectic solidification of ductile iron, the carbon content of austenite is higher than that of gray cast iron.
When gray cast iron eutectic solidifies, the graphite flakes in the eutectic cluster are in direct contact with both austenite and molten iron with high carbon content. The carbon in the molten iron not only diffuses into graphite through austenite, but also directly Diffusing into the graphite flakes, so the carbon content in the austenite at the molten iron-austenite interface is relatively low, about 1.55%.
When nodular cast iron is eutectic solidified, the graphite balls in the eutectic cluster only contact with the austenite shell, not with the molten iron. When the graphite balls grow up, the carbon in the molten iron diffuses into the graphite balls through the austenite shell. Therefore, the carbon content in the austenite at the molten iron-austenite interface is relatively high, reaching about 2.15%.
During eutectic solidification of ductile iron, the carbon content in austenite may be higher. Under the same conditions of carbon and silicon content, if the same cooling rate is maintained, the amount of graphite precipitated will be less. Therefore, when the eutectic solidifies The volume shrinkage will be slightly larger than that of gray cast iron. This is also one of the reasons why nodular iron castings are more prone to shrinkage and porosity. Maintaining a low cooling rate during the solidification process is a factor conducive to graphite charging analysis.
Under the conditions that can make graphitization sufficient, the carbon content in eutectic austenite (that is, the maximum solid solubility of carbon in austenite) is related to the silicon content in cast iron, and can generally be calculated by the following formula.
The maximum solid solubility of carbon in austenite CE=2.045-0.178 Si
2. Volume change during solidification of ductile iron castings
From the moment the molten iron is poured into the mold, to the end of the eutectic solidification and the complete solidification of the casting, the cast iron in the cavity will undergo liquid shrinkage, volume expansion caused by the precipitation of primary graphite, and solidification shrinkage caused by the precipitation of eutectic austenite , Several volume changes such as volume expansion caused by precipitation of eutectic graphite. In order to facilitate the description of the volume change during the solidification of ductile iron, it is necessary to refer to the simplified phase diagram shown in FIG. 2.
1. Liquid shrinkage of molten iron
After the molten iron enters the mold, the volume shrinks as the temperature decreases. The amount of liquid shrinkage of molten iron will vary due to its chemical composition and processing conditions, but this is usually ignored. Generally, the volume shrinkage of 1.5% for every 100°C drop in temperature is considered. The temperature range where liquid shrinkage occurs is calculated based on the drop from the casting temperature to the equilibrium eutectic transition temperature (1150°C). When the ductile iron parts are poured at several different pouring temperatures, the liquid shrinkage is shown in Table 1.
Table 1 Liquid shrinkage of ductile iron castings when pouring at different temperatures
Pouring temperature (℃) | 1400 | 1350 | 1300 |
Liquid shrinkage (%) | 3.75 | 3.00 | 2.25 |
2. Volume expansion caused by the precipitation of primary graphite
Although hypoeutectic spheroidal graphite cast iron will precipitate small graphite spheres above the liquidus temperature, the amount is very small and usually negligible.
As mentioned earlier, every 1% (mass fraction) of graphite precipitated can produce a volume expansion of 3.4%. Therefore, the volume expansion caused by the precipitation of primary graphite is equal to 3.4G.
Table 2 shows the volume expansion caused by the precipitation of primary graphite from several nodular cast irons with different carbon and silicon contents.
Although the precipitated primary graphite can compensate for the liquid shrinkage during the solidification of cast iron, for castings with a wall thickness of more than 40mm, defects such as graphite inclusions or graphite floating are likely to occur. In this case, special attention should be paid to controlling the carbon and silicon content.
Table 2 Volume expansion caused by the precipitation of primary graphite in several nodular cast irons
- Carbon content of cast iron (%):3.6/3.5/3.6/3.7/3.6/3.7/3.8
- Silicon content of cast iron (%):2.2/2.4/2.4/2.4/2.6/2.6/2.6
- Eutectic carbon content CC (%)/3.54/3.47/3.47/3.47/3.40/3.40/3.40
- Precipitation amount of primary graphite G initial (%)/0.06/0.03/0.13/0.24/0.21/0.31/0.41
- Volume expansion caused by precipitation of primary graphite (%):0.21/0.10/0.44/0.82/0.71/1.05/1.39
3. Volume shrinkage caused by precipitation of eutectic austenite
To calculate the volume shrinkage caused by the precipitation of eutectic austenite, the mass fraction of the eutectic liquid phase (hereinafter referred to as the "eutectic liquid phase amount"), the amount of liquid shrinkage, and the eutectic austenite precipitated from the unit eutectic liquid phase should be considered Volume and solidification shrinkage. The calculation of liquid shrinkage has been described above. The solidification shrinkage of austenite precipitated from the eutectic liquid phase is generally 3.5%.
Table 3 shows the volume shrinkage caused by the precipitation of eutectic austenite in several nodular cast irons with different carbon and silicon contents.
Table 3 Volume shrinkage caused by precipitation of eutectic austenite in several nodular cast irons
- Carbon content of cast iron (%) 3.6/3.5/3.6/3.7/3.6/3.7/3.8
- Silicon content of cast iron (%)/2.2/2.4/2.4/2.4/2.6/2.6/2.6
- Amount of eutectic liquid phase (%) 99.94/99.97/99.87/99.76/99.79/99.69/99.59
- The amount of austenite precipitated in the unit eutectic liquid phase (%)~98.1
- Volume shrinkage of austenite when pouring at 1400℃ (%)/3.30/3.30/3.30/3.30/3.30/3.29/3.29
- Volume shrinkage of austenite when pouring at 1350℃ (%)/3.33/3.33/3.33/3.32/3.32/3.32/3.32
- Volume shrinkage of austenite when pouring at 1300℃ (%) 3.35/3.35/3.35/3.35/3.35/3.34/3.34
For several commonly used nodular cast irons, keep the pouring temperature below 1350℃. Under the condition of no wall movement of the mold, the volume expansion caused by graphitization during the solidification of the casting can compensate for the liquid shrinkage and solidification shrinkage. It is possible to produce sound castings without setting risers. When the pouring temperature is 1400℃, if a higher carbon equivalent is selected for cast iron, graphitization expansion can also compensate for various volume shrinkage, but this method is only suitable for thin-walled castings, thicker-walled castings are prone to graphite inclusion and slag Graphite floating defects.
However, the information listed in Table 5 is obtained from the equilibrium diagram, and it is based on the premise that the ‘potentially precipitated carbon’ is completely precipitated by graphite crystals during the solidification process. In actual production, of course, it must be based on effective spheroidization and inoculation treatment, and sufficient graphitization is essential. For castings with high cooling rates and thin-walled castings, due to insufficient graphitization during eutectic solidification, the volume expansion caused by the precipitation of eutectic graphite is less than the above-mentioned calculated value, and it is still easy to produce defects such as shrinkage cavities and shrinkage porosity. .
At the same time, the stiffness of the mold is also a very important factor. If the rigidity of the casting mold is not high, and the wall movement occurs during graphitization and expansion, the shrinkage after expansion cannot be supplemented, and there will be defects such as shrinkage cavity and shrinkage porosity inside the casting.
3. Conditions for realizing no-riser casting
From the completion of pouring to the end of solidification, liquid shrinkage and solidification shrinkage will occur in the casting. Moreover, because ductile iron is solidified in a paste-like solidification method, it is difficult to fully supplement the liquid shrinkage by the pouring system to achieve riser-free casting. The liquid shrinkage and solidification shrinkage of cast iron should be compensated by the volume expansion when graphite crystals are precipitated. For this, the following conditions must be met.
The metallurgical quality of molten iron is good
Under normal circumstances, the carbon equivalent is better to choose 4.3 or 4.4, and the carbon equivalent can be appropriately increased for thin-walled castings. In order to increase the amount of graphite precipitated, if the carbon equivalent is kept the same, it is more advantageous to increase the carbon content than to increase the silicon content.
The spheroidizing operation should be strictly controlled. Under the condition of ensuring the globalization of graphite, the amount of residual magnesium should be reduced as much as possible, and the mass fraction of residual magnesium should be kept at about 0.06%.
The inoculation treatment should be adequate. In addition to the inoculation treatment carried out at the same time as the spheroidization treatment, instant inoculation should also be carried out during pouring. Thin-walled castings are best to be pre-inoculated before the molten iron is released.
The cooling rate during solidification of the casting should not be too high
If the cooling rate of the casting is too high, the graphite cannot be fully analyzed during the solidification process, and the graphitization expansion is not enough to compensate for the shrinkage of the cast iron, and thus riser-free casting cannot be realized.
Low temperature pouring
In order to reduce liquid shrinkage, the casting temperature is best controlled below 1350℃, usually 1320±20℃.
Using flake-shaped inner gate
In order to avoid squeezing out the molten iron from the inner gate during graphitization and expansion, the inner gate must be solidified quickly after the molten iron is filled with the mold. Therefore, when the riserless casting scheme is adopted, a thin and wide inner gate should be used. , The ratio of the width to the thickness is generally 4 to 5. In the selection of the thickness of the inner gate, the pouring temperature should also be considered, and the inner gate should not be solidified during the pouring process.
Improve the rigidity of the mold
In order to avoid the expansion of the cavity during graphitization expansion, improving the stiffness of the mold is one of the important conditions to ensure the quality of the casting. Regardless of the use of clay wet sand modeling or various self-setting sand modeling, no matter how much emphasis is placed on "pounding solid", it will not be excessive.
When making larger castings with self-hardening sand, chilled iron or graphite blocks should be placed on the surface of the mold corresponding to some thick parts on the casting. Cold iron and graphite blocks, of course, have a chilling effect, but they should also have a correct understanding of their role in improving the rigidity of the mold. In some cases, using refractory bricks instead of chilled iron or graphite blocks, the main function of which is to increase the rigidity of the mold.
4.The setting principle of the riser when using high-rigidity molds
When using various self-setting sand molding processes, shell molding processes or core assembly molding processes to produce ductile iron parts, the rigidity of the mold is relatively high, which is convenient to use graphitization expansion to supplement the liquid shrinkage and solidification shrinkage of the cast iron. If properly controlled, there will be It is possible to use a riserless process to produce sound castings. If the non-riser process is not suitable for various reasons, a narrow-necked riser can be used.
Casting process without riser
Under the conditions of high mold rigidity and good metallurgical quality of molten iron, keeping the cooling rate of castings low, so that graphite can fully crystallize out, is an important condition for realizing riser-free casting.
According to a research report by Goto et al., the solidification time of ductile iron castings is more than 20 minutes, and the amount of graphite precipitation can reach the saturation value.
S. I. Karsay believes that: the average modulus of castings is not less than 25mm is one of the conditions for realizing riser-free casting. Specifically, the average wall thickness of plate castings should not be less than 50mm.
The opinions expressed by Goto et al. and Karsay are different, and from the analysis of the cooling rate, they are actually the same.
Under the condition that the metallurgical quality of the molten iron is good (such as the use of pre-inoculation treatment or dynamic inoculation treatment and other measures), some thin-walled castings can also be cast without risers.
When adopting the riserless casting process, the design of the gating system can refer to the following opinions.
(1) About the runner
The runner should be larger and taller. Generally speaking, the ratio of the cross-sectional area of the sprue, the cross-sectional area of the runner, and the cross-sectional area of the inner gate can be 4:8:3. The ratio of the cross-section height to the width of the runner can be taken as (1.8~2):1.
In this way, the gating system has a better effect of supplementing the liquid shrinkage of the casting.
(2) About the inner gate
In order to prevent the pressure generated by the volumetric expansion of the casting in the cavity from causing the molten iron to flow back into the pouring system from the inner gate, a thin-shaped inner gate must be used, and its thickness is selected to ensure that the inner gate will not be prevented during the pouring process. The principle is to solidify and solidify soon after the cavity is filled. Generally speaking, the ratio of the section thickness to the width of the inner gate can be 1:4.
Because the inner gate is thin and the cross-sectional area is small, in order to ensure that the cavity is filled quickly, multiple inner gates should be provided for larger castings. In this way, there is also the effect of equalizing the temperature of the casting and reducing hot spots.
2. Use thin neck riser
If there are the following situations, the use of a riser-free casting scheme cannot guarantee the quality of the castings, you can consider using a narrow-necked riser:
- L The wall of the casting is thin, and the graphitization is insufficient during solidification;
- L There are scattered hot nodes on the casting, and no shrinkage defects are allowed inside;
- L The pouring temperature is higher (over 1350℃).
The main function of the narrow neck riser is to provide a partial supplement for the liquid shrinkage of the casting, so as to obtain a casting without shrinkage or porosity. The narrow neck connected with the casting should be solidified before the casting begins to solidify to prevent molten iron from entering the riser during graphitization and expansion. The thickness of the joint between the riser neck and the casting is the smallest, and the thickness is gradually increased at the transition section leading to the riser to facilitate the replenishment of molten iron to the casting.
The thickness of the riser neck can generally be 0.4 to 0.6 of the thickness of the feeding part of the casting.
If possible, it is best to connect the runner with the riser, and the molten iron is filled through the neck of the riser without an inner gate.
5.The setting principle of the riser when using the clay wet sand type
The rigidity of the clay green sand mold is poor, and it is easy to expand the cavity volume due to the movement of the mold wall. The expansion of the cavity volume is affected by many factors, such as the quality of the molding sand, the compactness of the mold, the pouring temperature, and the mold. The static pressure head of the molten iron in the cavity, etc., the actual volume expansion can be between 2-8%.
Since the volume expansion of the cavity varies greatly, the principle of setting the riser is of course different depending on the specific situation.
Thin-walled castings
Castings with a wall thickness of less than 8mm generally do not have obvious wall movement, and the liquid shrinkage after the molten iron is filled with the mold is not too large, and the riserless casting process can be used. The design of the gating system can refer to the previous section.
Castings with a wall thickness of 8-12mm
For this type of castings, if the wall thickness is uniform and there are no big hot spots, as long as the low temperature pouring is strictly controlled, the riserless casting process can also be used.
If there is a hot joint, and shrinkage holes and shrinkage are not allowed inside, a narrow-necked riser should be set according to the size of the hot joint.
Castings with wall thickness above 12mm
In the production of such castings with clay green sand molds, the wall movement is quite large, and it is more difficult to manufacture castings with no internal defects. When formulating the process plan, consider the use of a narrow-necked riser first, and strictly control the low-temperature pouring. If this solution cannot solve the problem, a special riser must be designed.
Use clay wet sand to produce ductile iron parts. If you want to install a riser, it is best to do:
- L A thin inner gate is used to make it solidify after the mold is filled. After the inner gate is solidified, the casting and the riser form a whole, which is not connected with the gating system;
- L When the casting undergoes liquid shrinkage, the riser replenishes the molten iron to the casting;
- L When the casting is graphitized and expanded, the molten iron flows to the riser to release the pressure in the cavity. Reduce its effect on the mold wall;
- L When the casting body undergoes secondary shrinkage after graphitization and expansion, the riser can provide feeding iron liquid to the casting.
It doesn't seem complicated to say it, but in fact, many influencing factors must be considered in the design of the riser, and so far, no effective specific scheme has been seen, and there is no easy-to-use complete set of data. In production, it is necessary to take into account the quality of castings and the rate of process yield, and often have to explore and experiment.
Please keep the source and address of this article for reprinting: Differences In The Solidification Characteristics Of Ductile Iron
Minghe Die Casting Company are dedicated to manufacture and provide quality and high performance Casting Parts(metal die casting parts range mainly include Thin-Wall Die Casting,Hot Chamber Die Casting,Cold Chamber Die Casting),Round Service(Die Casting Service,Cnc Machining,Mold Making,Surface Treatment).Any custom Aluminum die casting, magnesium or Zamak/zinc die casting and other castings requirements are welcome to contact us.
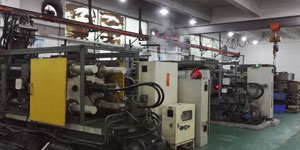
Under the control of ISO9001 and TS 16949,All processes are carried out through hundreds of advanced die casting machines, 5-axis machines, and other facilities, ranging from blasters to Ultra Sonic washing machines.Minghe not only has advanced equipment but also have professional team of experienced engineers,operators and inspectors to make the customer’s design come true.
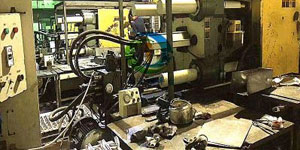
Contract manufacturer of die castings. Capabilities include cold chamber aluminum die casting parts from 0.15 lbs. to 6 lbs., quick change set up, and machining. Value-added services include polishing, vibrating, deburring, shot blasting, painting, plating, coating, assembly, and tooling. Materials worked with include alloys such as 360, 380, 383, and 413.
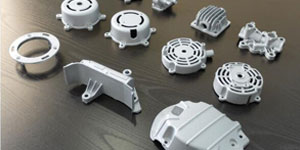
Zinc die casting design assistance/concurrent engineering services. Custom manufacturer of precision zinc die castings. Miniature castings, high pressure die castings, multi-slide mold castings, conventional mold castings, unit die and independent die castings and cavity sealed castings can be manufactured. Castings can be manufactured in lengths and widths up to 24 in. in +/-0.0005 in. tolerance.
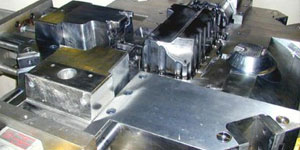
ISO 9001: 2015 certified manufacturer of die cast magnesium, Capabilities include high-pressure magnesium die casting up to 200 ton hot chamber & 3000 ton cold chamber, tooling design, polishing, molding, machining, powder & liquid painting, full QA with CMM capabilities, assembly, packaging & delivery.
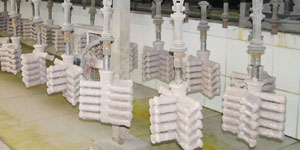
ITAF16949 certified. Additional Casting Service Include investment casting,sand casting,Gravity Casting, Lost Foam Casting,Centrifugal Casting,Vacuum Casting,Permanent Mold Casting,.Capabilities include EDI, engineering assistance, solid modeling and secondary processing.
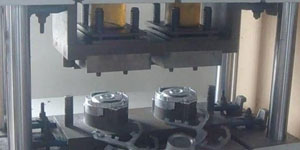
Casting Industries Parts Case Studies for: Cars, Bikes, Aircraft, Musical instruments, Watercraft, Optical devices, Sensors, Models, Electronic devices, Enclosures, Clocks, Machinery, Engines, Furniture, Jewelry, Jigs, Telecom, Lighting, Medical devices, Photographic devices, Robots, Sculptures, Sound equipment, Sporting equipment, Tooling, Toys and more.
What Can we help you do next?
∇ Go To Homepage For Die Casting China
→Casting Parts-Find out what we have done.
→Ralated Tips About Die Casting Services
By Minghe Die Casting Manufacturer |Categories: Helpful Articles |Material Tags: Aluminum Casting, Zinc Casting, Magnesium Casting, Titanium Casting, Stainless Steel Casting, Brass Casting,Bronze Casting,Casting Video,Company History,Aluminum Die Casting |Comments Off