Effect Of Annealing Temperature On Chilled Low Chromium Molybdenum Ductile Iron Roll
Affected by the casting process, the chilled low chromium molybdenum ductile iron roll has a relatively large casting stress in the as-cast state, so stress relief annealing treatment is required. Practice has shown that the stress relief annealing temperature not only affects the degree of casting stress relief, but also affects the structure and performance of the roll.
Using power frequency induction electric furnace to smelt molten iron, bottom-pouring pouring process, the diameter of the roll working surface is 288mm, and the composition is shown in Table 1. Use a lathe to cut a 20mm thick and 40mm wide (radial dimension) ring from the rolled chilled layer. The ring was cut into several samples, which were annealed and heat treated at different temperatures, and then the metallographic structure and hardness were observed.
Figure 1 shows the metallographic structure of the outside of the roll cut ring (near the cold type) and the inside of the cut ring (near the roll core). Figure 1a and Figure 1b show that the as-cast structure of the roll is pearlite, ledeburite and carbide. The amount of carbides on the outside of the tangent ring is more, and the amount of pearlite is less, and the amount of carbides on the inside of the tangent ring is less, and the amount of pearlite is more. . The test shows that even if the annealing temperature reaches 600°C and the holding time is 4 hours, the roll structure still has no obvious change, as shown in Figure 1c and Figure 1d.
(a) As cast outside (b) As cast inside
(c) The outer side after 600℃×4h heat treatment (d) The inner side after 600℃×4h heat treatment
Figure 1 Roll metallographic structure
Figure 2 shows the hardness at different positions of the cut ring of the roll working layer in the as-cast state and after different heat treatments. The figure shows that the hardness of the roll gradually decreases from the outside to the inside of the cutting ring. After the heat treatment, the hardness of the roll decreases, and the decrease in hardness increases with the increase of the heat treatment temperature. When the heat treatment temperature reaches 600°C, the hardness decreases greatly. According to the customer's requirements on the hardness of the rolls, we choose an annealing temperature of 400℃ in the production.
Discussion
The reduction in roll hardness after heat treatment is caused by three factors. One is that the metallographic structure changes during heat treatment, such as the decomposition of carbides. According to Figure 1, even if the heat treatment temperature reaches 600°C, the roll structure still has no significant change. This result is in line with the ferroalloy phase diagram [1]. It can be seen that the decrease in roll hardness is not caused by changes in the metallographic structure. The second is that the alloying elements diffuse uniformly and the degree of supersaturation is reduced during the heat treatment process, that is, caused by changes in the microstructure. In order to determine the effect of this factor, the experiment measured the microhardness of carbide and pearlite after different heat treatments (see Figure 3). The measurement results show that the microhardness of pearlite and carbides are reduced to varying degrees after heat treatment. This phenomenon must lead to a reduction in the macroscopic hardness of the roll. The third is the reduction of the macroscopic hardness of the roll with the relief of casting stress.
Conclusion
After the chilled low chromium molybdenum ductile iron roll is annealed and heat treated at less than 600°C, the metallographic structure does not change significantly, but the macroscopic hardness is reduced. When the heat treatment temperature is less than 450°C, the co-hardness decreases little, and when the heat treatment temperature is higher than 600°C, the hardness decreases more. The reason for the decrease of macroscopic hardness is the decrease of microhardness and the elimination of casting stress.
Please keep the source and address of this article for reprinting: Effect Of Annealing Temperature On Chilled Low Chromium Molybdenum Ductile Iron Roll
Minghe Die Casting Company are dedicated to manufacture and provide quality and high performance Casting Parts(metal die casting parts range mainly include Thin-Wall Die Casting,Hot Chamber Die Casting,Cold Chamber Die Casting),Round Service(Die Casting Service,Cnc Machining,Mold Making,Surface Treatment).Any custom Aluminum die casting, magnesium or Zamak/zinc die casting and other castings requirements are welcome to contact us.
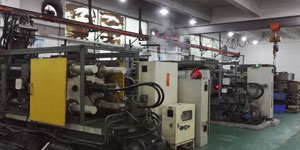
Under the control of ISO9001 and TS 16949,All processes are carried out through hundreds of advanced die casting machines, 5-axis machines, and other facilities, ranging from blasters to Ultra Sonic washing machines.Minghe not only has advanced equipment but also have professional team of experienced engineers,operators and inspectors to make the customer’s design come true.
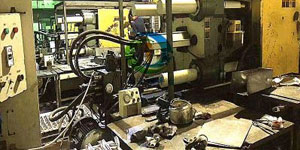
Contract manufacturer of die castings. Capabilities include cold chamber aluminum die casting parts from 0.15 lbs. to 6 lbs., quick change set up, and machining. Value-added services include polishing, vibrating, deburring, shot blasting, painting, plating, coating, assembly, and tooling. Materials worked with include alloys such as 360, 380, 383, and 413.
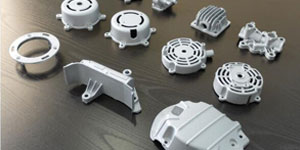
Zinc die casting design assistance/concurrent engineering services. Custom manufacturer of precision zinc die castings. Miniature castings, high pressure die castings, multi-slide mold castings, conventional mold castings, unit die and independent die castings and cavity sealed castings can be manufactured. Castings can be manufactured in lengths and widths up to 24 in. in +/-0.0005 in. tolerance.
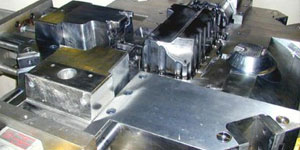
ISO 9001: 2015 certified manufacturer of die cast magnesium, Capabilities include high-pressure magnesium die casting up to 200 ton hot chamber & 3000 ton cold chamber, tooling design, polishing, molding, machining, powder & liquid painting, full QA with CMM capabilities, assembly, packaging & delivery.
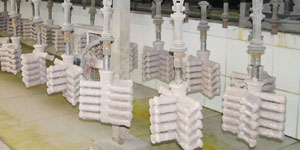
ITAF16949 certified. Additional Casting Service Include investment casting,sand casting,Gravity Casting, Lost Foam Casting,Centrifugal Casting,Vacuum Casting,Permanent Mold Casting,.Capabilities include EDI, engineering assistance, solid modeling and secondary processing.
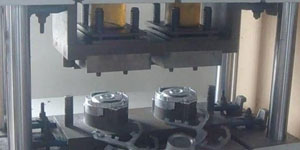
Casting Industries Parts Case Studies for: Cars, Bikes, Aircraft, Musical instruments, Watercraft, Optical devices, Sensors, Models, Electronic devices, Enclosures, Clocks, Machinery, Engines, Furniture, Jewelry, Jigs, Telecom, Lighting, Medical devices, Photographic devices, Robots, Sculptures, Sound equipment, Sporting equipment, Tooling, Toys and more.
What Can we help you do next?
∇ Go To Homepage For Die Casting China
→Casting Parts-Find out what we have done.
→Ralated Tips About Die Casting Services
By Minghe Die Casting Manufacturer |Categories: Helpful Articles |Material Tags: Aluminum Casting, Zinc Casting, Magnesium Casting, Titanium Casting, Stainless Steel Casting, Brass Casting,Bronze Casting,Casting Video,Company History,Aluminum Die Casting |Comments Off