Effect of Solution Temperature on Microstructure and Mechanical Properties of 254SMo
254SMo is a super austenitic stainless steel with high chromium, nickel, molybdenum and ultra-low carbon. Since the 1980s, the stainless steel has been widely used in seawater desalination, pulp bleaching, chemical and chemical industries due to its excellent corrosion resistance and high strength.
With the urgent demand for localization of 254SMo in recent years, a lot of research has been conducted in China, but most of them are concentrated on the corrosion resistance research after heat treatment, and there are few basic researches on the solution treatment stage. Since solution treatment is essential for obtaining complete austenite structure of 254SMo, it is important to determine the subsequent processing technology and obtain better corrosion resistance. For this reason, this article studies the effect of solution treatment on the structure and mechanical properties of 254SMo.
In this experiment, 254SMo super austenitic stainless steel smelted in large-scale production was used to forge and extrude into blanks. Its microstructure is complete austenite, and its chemical composition is (mass fraction, %): 0.014C, 19.70Cr, 18.31 Ni, 6.08Mo, 0.19N, 0.66Cu, 0.59Mn, 0.55Si, 0.014P, 0.0008S, the balance is Fe. The billet was subjected to solution treatment at different temperatures (900, 950, 1000, 1050, 1100, 1150, 1200, 1250 and 1300°C) in a muffle furnace, and kept at each solution temperature for 1 hour, and then water quenched.
Solution treatment has a great influence on the grain size of 254SMo. During the solution treatment within the test temperature range, the grains grow up normally, and the activation energy for grain growth is 152kJ/mol. When the solution temperature is lower than 1100°C, σ phase is found in the 254SMo structure. With the decrease of the solid solution temperature, the σ phase increases rapidly, and the χ phase and other phases also begin to appear, causing the plastic and toughness of the steel to drop sharply; when the solid solution temperature exceeds 1150°C, the precipitated phase disappears. When the solid solution temperature is higher than 1150℃, the mechanical properties of 254SMo are stable. Considering the influence of 254SMo solid solution degree, grain size, mechanical properties and other factors, it is recommended that the best solution temperature of 254SMo is 1150~1250℃.
Please keep the source and address of this article for reprinting: Effect of Solution Temperature on Microstructure and Mechanical Properties of 254SMo
Minghe Die Casting Company are dedicated to manufacture and provide quality and high performance Casting Parts(metal die casting parts range mainly include Thin-Wall Die Casting,Hot Chamber Die Casting,Cold Chamber Die Casting),Round Service(Die Casting Service,Cnc Machining,Mold Making,Surface Treatment).Any custom Aluminum die casting, magnesium or Zamak/zinc die casting and other castings requirements are welcome to contact us.
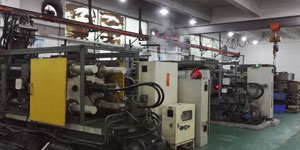
Under the control of ISO9001 and TS 16949,All processes are carried out through hundreds of advanced die casting machines, 5-axis machines, and other facilities, ranging from blasters to Ultra Sonic washing machines.Minghe not only has advanced equipment but also have professional team of experienced engineers,operators and inspectors to make the customer’s design come true.
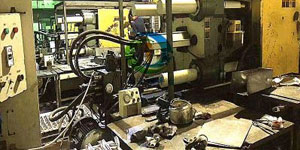
Contract manufacturer of die castings. Capabilities include cold chamber aluminum die casting parts from 0.15 lbs. to 6 lbs., quick change set up, and machining. Value-added services include polishing, vibrating, deburring, shot blasting, painting, plating, coating, assembly, and tooling. Materials worked with include alloys such as 360, 380, 383, and 413.
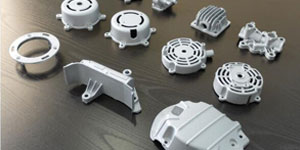
Zinc die casting design assistance/concurrent engineering services. Custom manufacturer of precision zinc die castings. Miniature castings, high pressure die castings, multi-slide mold castings, conventional mold castings, unit die and independent die castings and cavity sealed castings can be manufactured. Castings can be manufactured in lengths and widths up to 24 in. in +/-0.0005 in. tolerance.
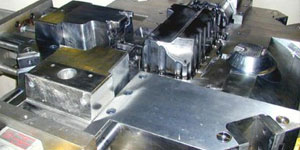
ISO 9001: 2015 certified manufacturer of die cast magnesium, Capabilities include high-pressure magnesium die casting up to 200 ton hot chamber & 3000 ton cold chamber, tooling design, polishing, molding, machining, powder & liquid painting, full QA with CMM capabilities, assembly, packaging & delivery.
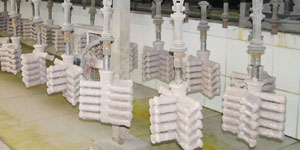
ITAF16949 certified. Additional Casting Service Include investment casting,sand casting,Gravity Casting, Lost Foam Casting,Centrifugal Casting,Vacuum Casting,Permanent Mold Casting,.Capabilities include EDI, engineering assistance, solid modeling and secondary processing.
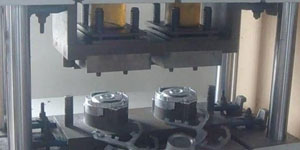
Casting Industries Parts Case Studies for: Cars, Bikes, Aircraft, Musical instruments, Watercraft, Optical devices, Sensors, Models, Electronic devices, Enclosures, Clocks, Machinery, Engines, Furniture, Jewelry, Jigs, Telecom, Lighting, Medical devices, Photographic devices, Robots, Sculptures, Sound equipment, Sporting equipment, Tooling, Toys and more.
What Can we help you do next?
∇ Go To Homepage For Die Casting China
→Casting Parts-Find out what we have done.
→Ralated Tips About Die Casting Services
By Minghe Die Casting Manufacturer |Categories: Helpful Articles |Material Tags: Aluminum Casting, Zinc Casting, Magnesium Casting, Titanium Casting, Stainless Steel Casting, Brass Casting,Bronze Casting,Casting Video,Company History,Aluminum Die Casting |Comments Off