Energy-Saving And Efficiency-Increasing Technology For Heavy-Duty Gears Heat Treatment
Energy-saving and efficiency-enhancing is an important topic in the field of gear heat treatment. It is explained with specific cases that process optimization is one of the effective means for heat treatment to save energy and reduce consumption. Under the premise of meeting technical requirements, by tapping the energy-saving potential of heat treatment process, shortening the production cycle, and reducing Energy consumption to achieve economic benefits.
In the field of heavy-duty gears, medium-hard and hard-tooth gears are widely used, and quenching and tempering and carburizing and quenching are the two most commonly used heat treatment methods. Heat treatment is a traditional manufacturing industry. It is a necessary process to improve the strength and toughness of gears. A lot of energy is needed in production to improve the surface and internal structure of gears in order to obtain performance. The energy consumed by products in the machinery industry in my country is generally 65% of the national energy consumption, of which the heat treatment industry accounts for 20% to 30% of the energy consumption in the machinery industry. Due to historical reasons, the overall production efficiency of heat treatment in my country is relatively low, 1/26 that of the United States, and energy consumption is 40% higher than that of the United States. Modern manufacturing technology attaches great importance to the sustainable development of manufacturing, especially in the field of heat treatment. How to reduce energy consumption and achieve energy saving and efficiency enhancement is an important issue in the field of machinery manufacturing.
Heat treatment is the process of heating the parts to a certain temperature, keeping them for a period of time, and then adopting different cooling rates to obtain different organizational structures. Heat treatment only changes the internal structure of the parts, but does not change the shape of the parts. The method of energy saving and efficiency enhancement of heat treatment is to shorten the production cycle, save energy and reduce consumption by changing parameters such as heating temperature, heat preservation time, and cooling method under the premise of ensuring the inherent performance. As a traditional industry, heat treatment is a big energy consumer, which is mainly reflected in the consumption of electricity.
In the field of heavy-duty gear manufacturing, especially carburizing and quenching heat treatment, the hardening layer depth is usually required to be greater than 2mm, and the carburizing time is more than 20h. The energy saving is The most intuitive energy saving direction. Energy saving can be achieved through different measures, such as the use of advanced heat treatment equipment with low energy consumption, continuous production, formulation of a reasonable heat treatment process, and good equipment maintenance. Among the many energy-saving methods, process optimization is one of the effective methods to achieve energy-saving and efficiency-increasing without the need to invest a lot of money. In the following, several energy-saving methods for heat treatment production of heavy-duty gears will be described.
1. Application of salt bath tempering after salt bath quenching
Carburized parts of wind power heavy-duty gears are mainly made of 18CrNiMo7-6 material. After quenching, they must be destressed at 170-200°C to reduce internal stress and improve the strength and plasticity of the gear. For the low-temperature salt bath quenching medium of 50%KNO3+50%NaNO2 formula, the conventional low-temperature tempering at home and abroad is heated by electric furnace, and air is used for heat transfer. The heat transfer in the electric furnace is mainly convection; the workpiece is in the salt bath medium.
When heating, heat conduction is the main component, and both radiation heat transfer and convective heat transfer are combined. Electric furnace heating, air as the heat transfer medium, the tempering time of wind power heavy-duty gear is calculated according to 2.4min per millimeter diameter or thickness, that is, 100mm diameter or thickness is kept for 4h, and the shortest heat preservation time is not less than 2h. For the salt bath medium of 50%KNO3+50%NaNO2 formula, its melting point is 140℃, and the service temperature is 150~550℃. Because the conductivity of the salt bath is much larger than that of the air medium, the heat preservation time of the salt bath tempering is greatly shortened, according to JB /T6048-2004 "Heating and Cooling of Metal Parts in Salt Bath", the tempering holding time is 100mm diameter or thickness holding about 2h. Advantages of salt bath tempering:
- The uniformity of tempering in the salt bath is better than that of the electric furnace, and the surface hardness deviation of a single piece is increased from ±1HRC of the electric furnace to ±0.5HRC.
- Because the heat transfer coefficient of the salt bath medium is much greater than that of air, the tempering time of the salt bath is only 50% of the tempering of the electric furnace for the same gear parts, and the production cycle and heating cost are reduced by 50%.
- It shows the residual stress distribution curve of the surface layer of the carburized part after electric furnace heating and salt bath heating and tempering. Figures 4 and 5 show the carburized layer structure after electric furnace heating and salt bath heating and tempering. The body level is the same, it can be seen that the residual stress of the salt bath tempering and the results of the organization performance test can achieve the effect of the electric furnace tempering.
- The salt bath quenching medium cannot be agglomerated and must be permanently insulated. After salt bath quenching, the idle heat source is used for tempering to save energy and increase efficiency.
Please keep the source and address of this article for reprinting: Energy-Saving And Efficiency-Increasing Technology For Heavy-Duty Gears Heat Treatment
Minghe Die Casting Company are dedicated to manufacture and provide quality and high performance Casting Parts(metal die casting parts range mainly include Thin-Wall Die Casting,Hot Chamber Die Casting,Cold Chamber Die Casting),Round Service(Die Casting Service,Cnc Machining,Mold Making,Surface Treatment).Any custom Aluminum die casting, magnesium or Zamak/zinc die casting and other castings requirements are welcome to contact us.
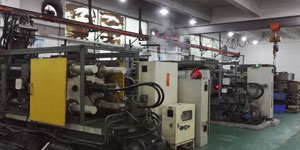
Under the control of ISO9001 and TS 16949,All processes are carried out through hundreds of advanced die casting machines, 5-axis machines, and other facilities, ranging from blasters to Ultra Sonic washing machines.Minghe not only has advanced equipment but also have professional team of experienced engineers,operators and inspectors to make the customer’s design come true.
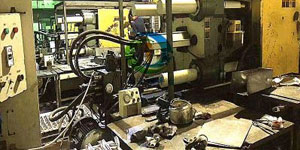
Contract manufacturer of die castings. Capabilities include cold chamber aluminum die casting parts from 0.15 lbs. to 6 lbs., quick change set up, and machining. Value-added services include polishing, vibrating, deburring, shot blasting, painting, plating, coating, assembly, and tooling. Materials worked with include alloys such as 360, 380, 383, and 413.
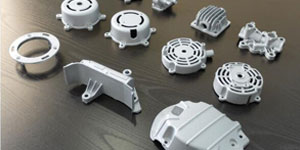
Zinc die casting design assistance/concurrent engineering services. Custom manufacturer of precision zinc die castings. Miniature castings, high pressure die castings, multi-slide mold castings, conventional mold castings, unit die and independent die castings and cavity sealed castings can be manufactured. Castings can be manufactured in lengths and widths up to 24 in. in +/-0.0005 in. tolerance.
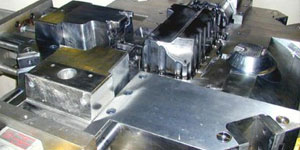
ISO 9001: 2015 certified manufacturer of die cast magnesium, Capabilities include high-pressure magnesium die casting up to 200 ton hot chamber & 3000 ton cold chamber, tooling design, polishing, molding, machining, powder & liquid painting, full QA with CMM capabilities, assembly, packaging & delivery.
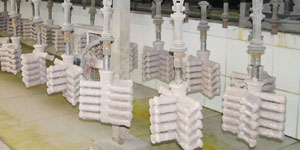
ITAF16949 certified. Additional Casting Service Include investment casting,sand casting,Gravity Casting, Lost Foam Casting,Centrifugal Casting,Vacuum Casting,Permanent Mold Casting,.Capabilities include EDI, engineering assistance, solid modeling and secondary processing.
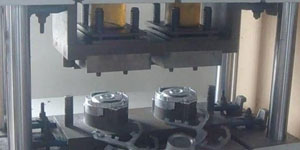
Casting Industries Parts Case Studies for: Cars, Bikes, Aircraft, Musical instruments, Watercraft, Optical devices, Sensors, Models, Electronic devices, Enclosures, Clocks, Machinery, Engines, Furniture, Jewelry, Jigs, Telecom, Lighting, Medical devices, Photographic devices, Robots, Sculptures, Sound equipment, Sporting equipment, Tooling, Toys and more.
What Can we help you do next?
∇ Go To Homepage For Die Casting China
→Casting Parts-Find out what we have done.
→Ralated Tips About Die Casting Services
By Minghe Die Casting Manufacturer |Categories: Helpful Articles |Material Tags: Aluminum Casting, Zinc Casting, Magnesium Casting, Titanium Casting, Stainless Steel Casting, Brass Casting,Bronze Casting,Casting Video,Company History,Aluminum Die Casting |Comments Off