Four Non-Specific Surface Treatments Of Aluminum Alloy Die Castings
In actual production, many aluminum alloy casting companies will encounter the confusion of the ugly or rough surface of the castings. Today, I have sorted out the dry goods skills of the surface treatment of aluminum alloy die castings. Learn the following four tricks. The surface treatment of the castings is easy and simple!
1. Phosphating Aluminum
The effects of accelerators, fluorides, Mn2+, Ni2+, Zn2+, PO4; and Fe2+ on the phosphating process of aluminum were studied in detail by using methods such as SEM, XRD, potential-time curve, and film weight change. Research shows that guanidine nitrate has the characteristics of good water solubility, low dosage and rapid film formation. It is an effective accelerator for aluminum phosphating: fluoride can promote film formation, increase film weight, and refine grains; Mn2+, Ni2+ can be obvious Refine the grains to make the phosphating film uniform and compact and improve the appearance of the phosphating film; when the Zn2+ concentration is low, the film cannot be formed or the film formation is poor. As the Zn2+ concentration increases, the film weight increases; the content of PO4 affects the phosphating film The heavy impact is greater, and the PO4 is increased. The content increases the weight of the phosphating film.
2. Alkaline Electrolytic Polishing Process Of Aluminum
Conducted research on alkaline polishing solution system, compared the effects of corrosion inhibitors, viscosity agents, etc. on the polishing effect, and successfully obtained an alkaline solution system with good polishing effects, and for the first time obtained the ability to reduce the operating temperature and prolong the use of the solution. Additives that improve the longevity and polishing effect at the same time. The experimental results show that adding appropriate additives to the NaOH solution can produce a good polishing effect. Exploratory experiments also found that after DC constant voltage electrolytic polishing with glucose NaOH micro manufacturing solution under certain conditions, the reflectivity of the aluminum surface can reach 90%, but due to the unstable factors in the experiment, further research is needed. The feasibility of using DC pulse electrolytic polishing method to polish aluminum under alkaline conditions is explored. The results show that the pulse electrolytic polishing method can achieve the leveling effect of DC constant voltage electrolytic polishing, but its leveling speed is slow.
3. Environmentally-Friendly Chemical Polishing Of Aluminum And Alloys
It is determined to develop a new environmentally-friendly chemical polishing technology based on phosphoric acid-sulfuric acid as the base fluid. This technology must achieve zero emission of NOx and overcome the quality defects of similar technologies in the past. The key to the new technology is to add some compounds with special effects to the base fluid to replace nitric acid. For this reason, it is necessary to analyze the three-acid chemical polishing process of aluminum, especially the role of nitric acid. The main function of nitric acid in aluminum chemical polishing is to inhibit pitting corrosion and improve polishing brightness. Combined with the chemical polishing test in simple phosphoric acid-sulfuric acid, it is believed that the special substances added in phosphoric acid-sulfuric acid should be able to inhibit pitting corrosion and slow down general corrosion, and must have a good leveling and brightening effect.
4. Electrochemical Surface Strengthening Treatment Of Aluminum And Its alloys
The process, performance, morphology, composition and structure of the ceramic-like amorphous composite conversion coating formed by anodic oxidation and deposition of aluminum and its alloys in a neutral system, and the film formation process and mechanism of the coating were discussed. Process research results show that in the Na_ 2wo 4 neutral mixing system, the concentration of film-forming accelerator is controlled to be 2.5~3.0g/, the concentration of complexing film agent is 1.5~3.0g/, and the concentration of Na 2WO_ 4 is 0.5~0.8g /l, peak current density is 6~12A/dm~2, weak agitation, a complete and uniform gray series inorganic non-metallic film with good gloss can be obtained. The film has a thickness of 5-10μm, a microhardness of 300-540HV, and excellent corrosion resistance. The neutral system has good adaptability to aluminum alloys, and can form a good film on various series of aluminum alloys such as rust-proof aluminum and forged aluminum.
Please keep the source and address of this article for reprinting:Four Non-Specific Surface Treatments Of Aluminum Alloy Die Castings
Minghe Die Casting Company are dedicated to manufacture and provide quality and high performance Casting Parts(metal die casting parts range mainly include Thin-Wall Die Casting,Hot Chamber Die Casting,Cold Chamber Die Casting),Round Service(Die Casting Service,Cnc Machining,Mold Making,Surface Treatment).Any custom Aluminum die casting, magnesium or Zamak/zinc die casting and other castings requirements are welcome to contact us.
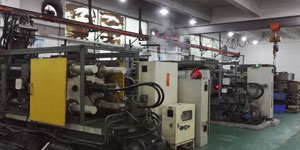
Under the control of ISO9001 and TS 16949,All processes are carried out through hundreds of advanced die casting machines, 5-axis machines, and other facilities, ranging from blasters to Ultra Sonic washing machines.Minghe not only has advanced equipment but also have professional team of experienced engineers,operators and inspectors to make the customer’s design come true.
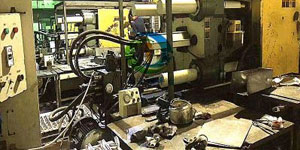
Contract manufacturer of die castings. Capabilities include cold chamber aluminum die casting parts from 0.15 lbs. to 6 lbs., quick change set up, and machining. Value-added services include polishing, vibrating, deburring, shot blasting, painting, plating, coating, assembly, and tooling. Materials worked with include alloys such as 360, 380, 383, and 413.
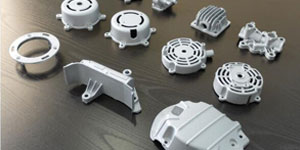
Zinc die casting design assistance/concurrent engineering services. Custom manufacturer of precision zinc die castings. Miniature castings, high pressure die castings, multi-slide mold castings, conventional mold castings, unit die and independent die castings and cavity sealed castings can be manufactured. Castings can be manufactured in lengths and widths up to 24 in. in +/-0.0005 in. tolerance.
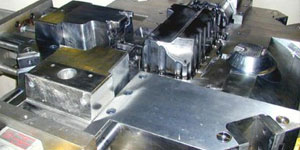
ISO 9001: 2015 certified manufacturer of die cast magnesium, Capabilities include high-pressure magnesium die casting up to 200 ton hot chamber & 3000 ton cold chamber, tooling design, polishing, molding, machining, powder & liquid painting, full QA with CMM capabilities, assembly, packaging & delivery.
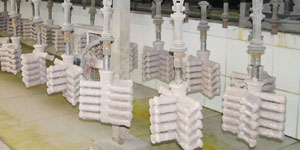
ITAF16949 certified. Additional Casting Service Include investment casting,sand casting,Gravity Casting, Lost Foam Casting,Centrifugal Casting,Vacuum Casting,Permanent Mold Casting,.Capabilities include EDI, engineering assistance, solid modeling and secondary processing.
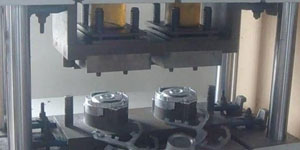
Casting Industries Parts Case Studies for: Cars, Bikes, Aircraft, Musical instruments, Watercraft, Optical devices, Sensors, Models, Electronic devices, Enclosures, Clocks, Machinery, Engines, Furniture, Jewelry, Jigs, Telecom, Lighting, Medical devices, Photographic devices, Robots, Sculptures, Sound equipment, Sporting equipment, Tooling, Toys and more.
What Can we help you do next?
∇ Go To Homepage For Die Casting China
→Casting Parts-Find out what we have done.
→Ralated Tips About Die Casting Services
By Minghe Die Casting Manufacturer |Categories: Helpful Articles |Material Tags: Aluminum Casting, Zinc Casting, Magnesium Casting, Titanium Casting, Stainless Steel Casting, Brass Casting,Bronze Casting,Casting Video,Company History,Aluminum Die Casting |Comments Off