GH2909 Alloy For Aero-Engine To Achieve Clearance Control
Mainly used in the manufacture of the fourth-generation engine's turbine middle casing, bearing ring and honeycomb support ring and other gap control parts to reduce air leakage loss, improve efficiency, and reduce fuel consumption. GH2909 is developed by increasing the Si content on the basis of GH2907 alloy and adjusting the heat treatment process. GH2909 is a new type of Fe-Ni-Co-based age-hardening low-expansion high-temperature alloy. It has high strength and plasticity, low thermal expansion coefficient, almost constant elastic modulus, and good oxidation resistance and thermal fatigue resistance at 650℃. Performance, can reduce the gap between rotating parts and static parts, realize gap control, save energy, reduce consumption, and increase engine thrust. It is an ideal high-temperature alloy material for aviation and aerospace engines, so it has been widely used in aircraft engines.
Over the years, due to the limitation of forging equipment conditions: there is only a 2,000-ton fast forging press, so the production of large-size high-temperature alloy forging rods is the short board of a company's high-temperature alloy development. The main problems of GH2909 alloy large-size bars are: (1) The structure is coarse and uneven, which leads to high ultrasonic flaw detection clutter and even serious bottom wave attenuation; (2) Large fluctuations in performance test data. With the improvement of forging equipment conditions: 4,500 tons of fast forging presses and 1,800 tons of precision forging presses have been put into operation, and in order to improve and improve the quality of GH2909 alloy large-size forging materials, the forging process has been carried out to improve the structure and performance of GH2909 alloy large-size bars. Affect the study.
The GH2909 alloy smelting process is vacuum induction + vacuum arc remelting, which remelts Φ440mm electrode vacuum arc into Φ508mm steel ingots. After homogenization heat treatment, the steel ingots are forged to produce large-size high-temperature alloy forgings.
The billet forging adopts a step-by-step cooling and large deformation forging process, and the deformation amount is more than 30% per fire; the heating temperature of the final fire forging: 1000°C; most of the deformation temperature: ≤955°C, the final forging temperature: ≥870°C; and Three forging methods are used respectively: (1) The whole steel ingot is directly drawn by the 2000-ton fast forging press + the middle cutting section + separate one-fire forging; (2) The whole steel ingot 4500-ton fast forging press is two upsetting and two drawing + middle Cut into sections + separately fire 1,800 tons of precision forging machine into material; (3) 4,500 tons of fast forging presses are drawn to length + jaws at both ends + middle cutting sections + two upsets and two draws + 1800 tons of one The fire precision forging machine is finished; then, the center, 1/2R and edge structure and lateral performance samples are respectively taken from the bar, and the microstructure and mechanical properties are observed with an optical microscope. The finished product is inspected by ultrasonic flaw detection after polishing. The results showed that:
- (1) The equipment tonnage limitation of 2000t fast forging press is obvious.
- (2) Method 2 After forging, there is a small amount of mixed crystal structure in the center and 1/2R of the cross section of the bar after forging, and the edge grain reaches 8 grades, and the structure is uniform and fine.
- (3) Method 3 After forging, the cross section of the bar is uniform in the center, 1/2R, and edge structure, and the grains in each part are relatively consistent, and the grain size is about 6. Compared with Method 1, the tensile yield strength and tensile strength at room temperature are increased by more than 70 MPa for method 3, and the tensile ductility at room temperature is also increased significantly, reaching more than 3%; the high temperature tensile yield strength and tensile strength both increase by more than 20 MPa, and the high temperature tensile plasticity Reduced; the endurance life is reduced, and the endurance plasticity is equivalent. The test results of method 3 and method 2 are comparable.
Therefore, Method 3, that is, using a 4,500-ton press for full length drawing + jaws at both ends + mid-cutting sections + two upsetting and two drawing with a leak plate + 1,800 tons of one-fire precision forging machine into a material, can make GH2909 alloy large The structure of the standard bar material is uniform and small, and the good comprehensive performance that meets the requirements of the standard index is obtained.
Please keep the source and address of this article for reprinting:GH2909 Alloy For Aero-Engine To Achieve Clearance Control
Minghe Die Casting Company are dedicated to manufacture and provide quality and high performance Casting Parts(metal die casting parts range mainly include Thin-Wall Die Casting,Hot Chamber Die Casting,Cold Chamber Die Casting),Round Service(Die Casting Service,Cnc Machining,Mold Making,Surface Treatment).Any custom Aluminum die casting, magnesium or Zamak/zinc die casting and other castings requirements are welcome to contact us.
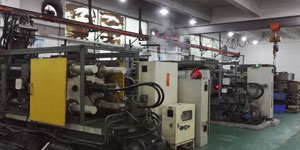
Under the control of ISO9001 and TS 16949,All processes are carried out through hundreds of advanced die casting machines, 5-axis machines, and other facilities, ranging from blasters to Ultra Sonic washing machines.Minghe not only has advanced equipment but also have professional team of experienced engineers,operators and inspectors to make the customer’s design come true.
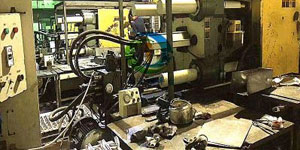
Contract manufacturer of die castings. Capabilities include cold chamber aluminum die casting parts from 0.15 lbs. to 6 lbs., quick change set up, and machining. Value-added services include polishing, vibrating, deburring, shot blasting, painting, plating, coating, assembly, and tooling. Materials worked with include alloys such as 360, 380, 383, and 413.
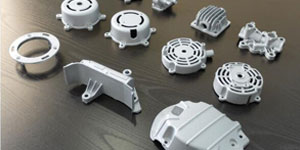
Zinc die casting design assistance/concurrent engineering services. Custom manufacturer of precision zinc die castings. Miniature castings, high pressure die castings, multi-slide mold castings, conventional mold castings, unit die and independent die castings and cavity sealed castings can be manufactured. Castings can be manufactured in lengths and widths up to 24 in. in +/-0.0005 in. tolerance.
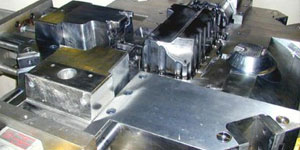
ISO 9001: 2015 certified manufacturer of die cast magnesium, Capabilities include high-pressure magnesium die casting up to 200 ton hot chamber & 3000 ton cold chamber, tooling design, polishing, molding, machining, powder & liquid painting, full QA with CMM capabilities, assembly, packaging & delivery.
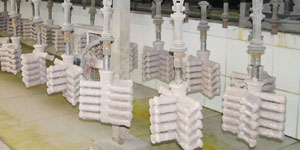
ITAF16949 certified. Additional Casting Service Include investment casting,sand casting,Gravity Casting, Lost Foam Casting,Centrifugal Casting,Vacuum Casting,Permanent Mold Casting,.Capabilities include EDI, engineering assistance, solid modeling and secondary processing.
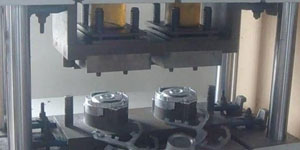
Casting Industries Parts Case Studies for: Cars, Bikes, Aircraft, Musical instruments, Watercraft, Optical devices, Sensors, Models, Electronic devices, Enclosures, Clocks, Machinery, Engines, Furniture, Jewelry, Jigs, Telecom, Lighting, Medical devices, Photographic devices, Robots, Sculptures, Sound equipment, Sporting equipment, Tooling, Toys and more.
What Can we help you do next?
∇ Go To Homepage For Die Casting China
→Casting Parts-Find out what we have done.
→Ralated Tips About Die Casting Services
By Minghe Die Casting Manufacturer |Categories: Helpful Articles |Material Tags: Aluminum Casting, Zinc Casting, Magnesium Casting, Titanium Casting, Stainless Steel Casting, Brass Casting,Bronze Casting,Casting Video,Company History,Aluminum Die Casting |Comments Off