Heat Treatment Process Of Hardened Steel And Pre-Hardened Steel
Different types of steel used as plastic molds have different chemical compositions and mechanical properties, so the manufacturing process routes are different; similarly, different types of plastic mold steels use different heat treatment processes. This section mainly introduces the manufacturing process route and the characteristics of the heat treatment process of the plastic mold.
Manufacturing Process Route Of Plastic Mold
1. Low-carbon steel and low-carbon alloy steel molds
For example, the process route of 20, 20Cr, 20CrMnTi and other steels is: blanking→forging die blank→annealing→mechanical rough machining→cold extrusion forming→recrystallization annealing→mechanical finishing→carburizing→quenching, tempering→grinding and polishing →Assemble.
2. High-alloy carburized steel mold
For example, the process route of 12CrNi3A and 12CrNi4A steel is: blanking→forging die blank→normalizing and high temperature tempering→mechanical rough machining→high temperature tempering→finishing→carburizing→quenching and tempering→grinding and polishing→assembly.
3. Quenched and tempered steel mold
For example, the process route of 45, 40Cr and other steels is: blanking→forging die blank→annealing→mechanical rough machining→tempering and tempering→mechanical finishing→dressing, polishing→assembly.
4. Carbon tool steel and alloy tool steel molds
For example, the process route of T7A~T10A, CrWMn, 9SiCr and other steels is: blanking→forging into die blanks→spheroidizing annealing→mechanical rough machining→stress relief annealing→mechanical semi-finishing→mechanical finishing→quenching, tempering→grinding Polishing → assembly.
5. Pre-hardened steel mold
For example, 5NiSiCa, 3Cr2Mo (P20) and other steels. For those directly processed with bar stocks, they have been pre-hardened due to the supply status, and can be directly processed and formed, then polished and assembled. For those that need to be forged into blanks and then processed into forming, the process route is: blanking→forging→spheroidizing annealing→planing or milling six sides→pre-hardening treatment (34~42HRC)→mechanical roughing→stress relief annealing→ Mechanical finishing → polishing → assembly.
The Heat Treatment Characteristics Of Plastic Molds
(1) Heat treatment characteristics of carburized steel plastic mold
- For plastic molds with high hardness, high wear resistance and high toughness requirements, carburized steel should be used for manufacturing, and carburizing, quenching and low temperature tempering are the final heat treatment.
- Requirements for the carburized layer, generally the thickness of the carburized layer is 0.8 ~ 1.5mm, when pressing plastics containing hard fillers, the mold carburized layer thickness is required to be 1.3 ~ 1.5mm, when pressing soft plastics, the carburized layer The thickness is 0.8~1.2mm. The carbon content of the carburized layer is preferably 0.7% to 1.0%. If carbon and nitrogen co-infiltration are used, the wear resistance, corrosion resistance, oxidation resistance and anti-sticking properties will be better.
- The carburizing temperature is generally 900~920℃, and small molds with complex cavities can take 840~860℃ medium temperature carbonitriding. The carburizing heat preservation time is 5-10h, which should be selected according to the requirements for the thickness of the carburized layer. The carburizing process is suitable to adopt the hierarchical carburizing process, that is, the high temperature stage (900~920℃) is mainly to quickly infiltrate the surface of the part; the medium temperature stage (820~840℃) is mainly to increase the thickness of the carburized layer. A uniform and reasonable carbon concentration gradient distribution is established in the carburized layer, which is convenient for direct quenching.
- The quenching process after carburizing is different according to the steel type. After carburizing, it can be used separately: reheating and quenching; direct quenching after graded carburizing (such as alloy carburized steel); direct quenching after medium temperature carbonitriding (such as industrial Small precision molds formed by cold extrusion of pure iron or low carbon steel); air quenching after carburizing (such as large and medium-sized molds made of high-alloy carburized steel).
(2) Heat treatment of hardened steel plastic mold
- For molds with more complex shapes, heat treatment should be performed after rough machining and then finish machining to ensure the smallest deformation during heat treatment. For precision molds, the deformation should be less than 0.05%.
- The surface requirements of the plastic mold cavity are very strict, so during the quenching and heating process, it is necessary to ensure that the surface of the cavity is not oxidized, decarburized, not corroded, overheated, etc. It should be heated in a protective atmosphere furnace or in a salt bath furnace after strict deoxidation. If a common box-type resistance furnace is used for heating, a protective agent should be applied to the surface of the mold cavity, and the heating rate should be controlled. Cooling medium, control the cooling rate to avoid deformation, cracking and scrapping during the quenching process. Generally, hot bath quenching is better, and pre-cooling quenching can also be used.
- After quenching, it should be tempered in time, the tempering temperature should be higher than the working temperature of the mold, and the tempering time should be sufficient. The length depends on the mold material and section size, but it should be at least 40-60min.
(3) Heat treatment of pre-hardened steel plastic mold
- The pre-hardened steel is supplied in a pre-hardened state, and generally does not require heat treatment, but sometimes it needs to be modified forging, and the die blank after modified forging must be heat treated.
- The pre-heat treatment of pre-hardened steel usually adopts spheroidizing annealing, the purpose is to eliminate forging stress, obtain uniform spherical pearlite structure, reduce hardness, increase plasticity, and improve the cutting performance or cold extrusion forming performance of the die blank.
- The pre-hardening process of pre-hardened steel is simple, most of which adopt quenching and tempering treatment, and tempered sorbite structure is obtained after quenching and tempering. The high temperature tempering has a wide temperature range that can meet the various working hardness requirements of the mold. Due to the good hardenability of this kind of steel, oil cooling, air cooling or nitrate-salt graded quenching can be used during quenching. Table 3-27 shows the pre-hardening process of some pre-hardened steels for reference.
Table 3-27 Pre-hardening process of some pre-hardened steel
Steel number | Heating temperature/℃ | Cooling Method |
Tempering temperature/℃ |
Pre-hardened hardnessHRC |
3Cr2Mo |
830~840 |
Oil cooling or 160~180℃ nitrate classification |
580~650 |
28~36 |
5NiSCa |
880~930 |
Oil cooler |
550~680 |
30~45 |
8Cr2MnWMoVS |
860~900 |
Oil or air cooling |
550~620 |
42~48 |
P4410 |
830~860 |
Oil cooling or nitrate classification |
550~650 |
35~41 |
SM1 |
830~850 |
Oil cooler |
620~660 |
36~42 |
(4) Heat treatment of age-hardening steel plastic mold
- The heat treatment process of age hardening steel is divided into two basic steps. First, the solution treatment is carried out, that is, the steel is heated to a high temperature, so that various alloying elements are dissolved in the austenite, and after the austenite is completed, the martensite structure is obtained by quenching. The second step is aging treatment, and aging is used to strengthen the mechanical properties that meet the final requirements.
- The solution treatment heating is generally carried out in a salt bath furnace or a box furnace. The heating time can be respectively: 1min/mm, 2~2.5min/mm, quenching adopts oil cooling, and steel with good hardenability can also be air-cooled. If the final forging temperature can be accurately controlled when forging the die blank, solution quenching can be performed directly after forging.
- The aging treatment is best carried out in a vacuum furnace. If it is carried out in a box furnace, in order to prevent the surface of the mold cavity from being oxidized, a protective atmosphere must be passed into the furnace, or aluminum oxide powder, graphite powder, cast iron scraps should be used in the box. Aging under protective conditions. Packing protection heating should appropriately extend the heat preservation time, otherwise it will be difficult to achieve the aging effect. The heat treatment specification of partially age-hardening plastic mold steel can refer to Table 3-28.
Table 3-28 Heat treatment specifications for partially age-hardened steel
Steel number | Solution treatment process | Aging treatment process | Aging hardness HRC |
06Ni6CrMoVTiAl |
800~850℃ oil cooling |
510~530℃×(6~8)h |
43~48 |
PMS |
800~850℃ air cooling |
510~530℃×(3~5)h |
41~43 |
25CrNi3MoAl |
880℃ water quenching or air cooling |
520~540℃×(6~8)h |
39~42 |
SM2 |
900℃×2h oil cooling+700℃×2h |
510℃×10h |
39~40 |
PCR |
1050℃ solid solution air cooling |
460~480℃×4h |
42~44 |
The surface treatment of plastic molds
In order to improve the wear resistance and corrosion resistance of the plastic mold surface, appropriate surface treatment is often applied to it.
- Chromium plating of plastic molds is one of the most widely used surface treatment methods. The chromium plating layer has a strong passivation ability in the atmosphere, can maintain the metallic luster for a long time, and does not react chemically in a variety of acidic media. The coating hardness reaches 1000HV, so it has excellent wear resistance. The chrome-plated layer also has high heat resistance, and its appearance and hardness remain unchanged when heated to 500°C in the air.
- Nitriding has the advantages of low processing temperature (generally 550~570℃), little mold deformation and high hardness of the infiltrated layer (up to 1000~1200HV), so it is also very suitable for surface treatment of plastic molds. Steel grades containing alloying elements such as chromium, molybdenum, aluminum, vanadium and titanium have better nitriding performance than carbon steel. Nitriding treatment when used as a plastic mold can greatly improve wear resistance.
Surface treatment methods suitable for plastic molds include: nitrocarburizing, electroless nickel plating, ion plating titanium nitride, titanium carbide or titanium carbonitride, PVD, CVD method deposition of hard film or super hard film, etc.
Please keep the source and address of this article for reprinting: Heat Treatment Process Of Hardened Steel And Pre-Hardened Steel
Minghe Die Casting Company are dedicated to manufacture and provide quality and high performance Casting Parts(metal die casting parts range mainly include Thin-Wall Die Casting,Hot Chamber Die Casting,Cold Chamber Die Casting),Round Service(Die Casting Service,Cnc Machining,Mold Making,Surface Treatment).Any custom Aluminum die casting, magnesium or Zamak/zinc die casting and other castings requirements are welcome to contact us.
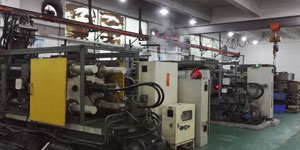
Under the control of ISO9001 and TS 16949,All processes are carried out through hundreds of advanced die casting machines, 5-axis machines, and other facilities, ranging from blasters to Ultra Sonic washing machines.Minghe not only has advanced equipment but also have professional team of experienced engineers,operators and inspectors to make the customer’s design come true.
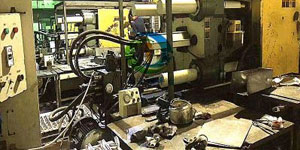
Contract manufacturer of die castings. Capabilities include cold chamber aluminum die casting parts from 0.15 lbs. to 6 lbs., quick change set up, and machining. Value-added services include polishing, vibrating, deburring, shot blasting, painting, plating, coating, assembly, and tooling. Materials worked with include alloys such as 360, 380, 383, and 413.
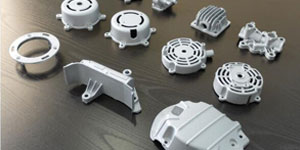
Zinc die casting design assistance/concurrent engineering services. Custom manufacturer of precision zinc die castings. Miniature castings, high pressure die castings, multi-slide mold castings, conventional mold castings, unit die and independent die castings and cavity sealed castings can be manufactured. Castings can be manufactured in lengths and widths up to 24 in. in +/-0.0005 in. tolerance.
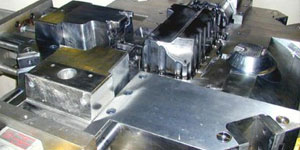
ISO 9001: 2015 certified manufacturer of die cast magnesium, Capabilities include high-pressure magnesium die casting up to 200 ton hot chamber & 3000 ton cold chamber, tooling design, polishing, molding, machining, powder & liquid painting, full QA with CMM capabilities, assembly, packaging & delivery.
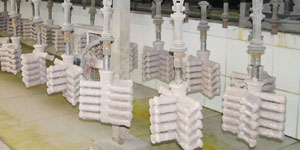
ITAF16949 certified. Additional Casting Service Include investment casting,sand casting,Gravity Casting, Lost Foam Casting,Centrifugal Casting,Vacuum Casting,Permanent Mold Casting,.Capabilities include EDI, engineering assistance, solid modeling and secondary processing.
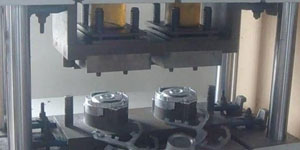
Casting Industries Parts Case Studies for: Cars, Bikes, Aircraft, Musical instruments, Watercraft, Optical devices, Sensors, Models, Electronic devices, Enclosures, Clocks, Machinery, Engines, Furniture, Jewelry, Jigs, Telecom, Lighting, Medical devices, Photographic devices, Robots, Sculptures, Sound equipment, Sporting equipment, Tooling, Toys and more.
What Can we help you do next?
∇ Go To Homepage For Die Casting China
→Casting Parts-Find out what we have done.
→Ralated Tips About Die Casting Services
By Minghe Die Casting Manufacturer |Categories: Helpful Articles |Material Tags: Aluminum Casting, Zinc Casting, Magnesium Casting, Titanium Casting, Stainless Steel Casting, Brass Casting,Bronze Casting,Casting Video,Company History,Aluminum Die Casting |Comments Off