Heat Treatment Process Of Special Aluminum Alloy Shaft Sleeve
The shaft sleeve is one of the main parts of the gear pump. It is installed on the two ends of the high-speed gear to support the bearing. It must have sufficient strength and good wear resistance. In order to ensure the performance requirements of the parts, our factory uses non-standard aluminum-tin alloy, and the role of Cu is to strengthen the matrix. Sn can form a softer, low melting point Al-Sn eutectic and increase wear resistance.
The original heat treatment process is 515℃ solid solution 6h water cooling, 180℃ aging 8h air cooling. There are two problems with this process:
- The Al-Sn eutectic is overfired and tin is added to form an Al-Sn eutectic with a tin content of 99.5%, with a melting point of 229°C. When the workpiece is heated to 515°C, the Al-Sn eutectic is overfired, and remelted pellets are formed when quenched and cooled. In the process of forming remelted pellets, on the one hand, the grain boundaries are oxidized, which reduces the strength of the grains. On the other hand, many microscopic voids are generated, which increase the energy of the grain interface and reduce the strength of the metal, which is easy to pass during use. Early failure.
- The process production time is long, up to 16h, the production efficiency is low, and the energy consumption is large.
It can be seen from the metallographic observation and mechanical property test data that the 250℃×7h treatment process is ideal. The Al-Sn eutectic is distributed along the grain boundary in a broken network. On the one hand, the distribution of the Al-Sn eutectic is relatively uniform to ensure good wear resistance. On the other hand, the Al-Sn eutectic does not have a divided matrix, which makes the alloy better The plasticity and toughness. The higher hardness can be obtained by the 250℃×7h treatment process because the alloy contains less Cu and the metal mold has a fast cooling rate. During the casting cooling process, Cu has been ensured to melt into the solid solution and play a quenching effect. The increase in hardness through natural aging also proves this.
The tensile strength of 250℃×7h air cooling process is 47% higher than that of 515℃×6h water cooling+180℃×8h air cooling process.
The 250℃×7h air cooling process temperature is slightly higher than the melting point of the Al-Sn eutectic, in order to obtain the broken network distribution of the Al-Sn eutectic through a shorter holding time without overburning the eutectic.
On the basis of the process test, a small batch (400 pieces) of trial production was carried out. After the hardness and metallographic inspection and the product delivery test on the test bench, all the products were qualified.
The process was officially put into production in 1996, and hundreds of thousands of shaft sleeves have been produced, all of which are qualified. The work efficiency is increased by 1.3 times, and it can save about 70,000 yuan a year and save more than 80,000 kW.h of electricity.
Please keep the source and address of this article for reprinting:Heat Treatment Process Of Special Aluminum Alloy Shaft Sleeve
Minghe Die Casting Company are dedicated to manufacture and provide quality and high performance Casting Parts(metal die casting parts range mainly include Thin-Wall Die Casting,Hot Chamber Die Casting,Cold Chamber Die Casting),Round Service(Die Casting Service,Cnc Machining,Mold Making,Surface Treatment).Any custom Aluminum die casting, magnesium or Zamak/zinc die casting and other castings requirements are welcome to contact us.
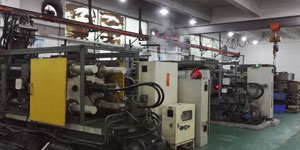
Under the control of ISO9001 and TS 16949,All processes are carried out through hundreds of advanced die casting machines, 5-axis machines, and other facilities, ranging from blasters to Ultra Sonic washing machines.Minghe not only has advanced equipment but also have professional team of experienced engineers,operators and inspectors to make the customer’s design come true.
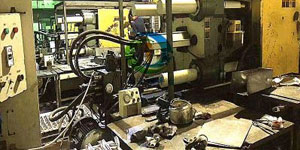
Contract manufacturer of die castings. Capabilities include cold chamber aluminum die casting parts from 0.15 lbs. to 6 lbs., quick change set up, and machining. Value-added services include polishing, vibrating, deburring, shot blasting, painting, plating, coating, assembly, and tooling. Materials worked with include alloys such as 360, 380, 383, and 413.
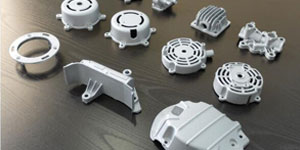
Zinc die casting design assistance/concurrent engineering services. Custom manufacturer of precision zinc die castings. Miniature castings, high pressure die castings, multi-slide mold castings, conventional mold castings, unit die and independent die castings and cavity sealed castings can be manufactured. Castings can be manufactured in lengths and widths up to 24 in. in +/-0.0005 in. tolerance.
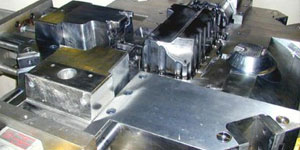
ISO 9001: 2015 certified manufacturer of die cast magnesium, Capabilities include high-pressure magnesium die casting up to 200 ton hot chamber & 3000 ton cold chamber, tooling design, polishing, molding, machining, powder & liquid painting, full QA with CMM capabilities, assembly, packaging & delivery.
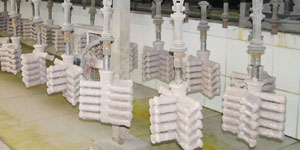
ITAF16949 certified. Additional Casting Service Include investment casting,sand casting,Gravity Casting, Lost Foam Casting,Centrifugal Casting,Vacuum Casting,Permanent Mold Casting,.Capabilities include EDI, engineering assistance, solid modeling and secondary processing.
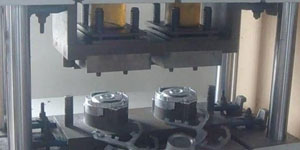
Casting Industries Parts Case Studies for: Cars, Bikes, Aircraft, Musical instruments, Watercraft, Optical devices, Sensors, Models, Electronic devices, Enclosures, Clocks, Machinery, Engines, Furniture, Jewelry, Jigs, Telecom, Lighting, Medical devices, Photographic devices, Robots, Sculptures, Sound equipment, Sporting equipment, Tooling, Toys and more.
What Can we help you do next?
∇ Go To Homepage For Die Casting China
→Casting Parts-Find out what we have done.
→Ralated Tips About Die Casting Services
By Minghe Die Casting Manufacturer |Categories: Helpful Articles |Material Tags: Aluminum Casting, Zinc Casting, Magnesium Casting, Titanium Casting, Stainless Steel Casting, Brass Casting,Bronze Casting,Casting Video,Company History,Aluminum Die Casting |Comments Off