High Pressure Forming Process In Support Pressure
Internal high pressure forming is also called hydroforming or hydraulic forming. It is a material forming process that uses liquid as a forming medium and controls internal pressure and material flow to achieve the purpose of forming hollow parts. The internal high pressure forming process is divided into conventional internal high pressure forming and supporting pressure internal high pressure forming.
Features of conventional internal high pressure forming:
- The inside of the tube is not pressurized before the mold is closed;
- Pressurize inside the tube after the mold is closed;
- The forming process is after the mold is closed. In most cases, the end material is fed while increasing the pressure;
- There is always an obvious process of expansion during the process;
- The maximum pressure is 100~300MPa.
High pressure forming under support pressure
- Always maintain pressure in the tube before the mold is closed;
- The formation of parts is almost realized under the condition of internal supporting pressure;
- The maximum pressure is to smooth the surface of the part after the mold is closed, and support the punching operation;
- There is basically no swelling part (unless it is possible to extend both ends when necessary, even if the pressure is low);
- The maximum pressure is 50~100MPa.
The high-pressure forming process in the supporting pressure is: first inject the medium inside the part and increase its pressure, and then close the mold, so that during the forming process, wrinkles caused by low expansion can be avoided, and the material in the mold closing process can be optimized distributed. At the same time there are other positive effects. Since there is no significant expansion, there is no work hardening process, and this process can use a lower maximum pressure than conventional internal high pressure forming.
Compared with conventional internal high pressure forming, the advantages and disadvantages of supporting pressure internal high pressure forming are as follows:
1. Advantages
For materials with low formability, it can be formed safely; it can achieve a more consistent wall thickness; there is no risk of part breakage; a small angle radius can be achieved; more and larger holes can be achieved; under normal circumstances, there is no need for lubrication; Combination pressure forming + final forming can be realized; the die load is small, so the volume of the die can be reduced; the tonnage of the press can be smaller; the cycle time may be reduced; the demand for press oil is reduced; the wear of high-pressure parts is reduced; Internal high pressure forming is more economical.
2. Disadvantages
Formed parts have larger tolerances, and the springback problem is serious. The processed parts must have a constant circumference, low work hardening, and are susceptible to the influence of the upstream process and the fluctuation of the tolerance of the fillet radius.
Taking into account the impact of these shortcomings on the quality of parts, it is necessary to determine the appropriate process according to the characteristics of the parts.
Please keep the source and address of this article for reprinting: High Pressure Forming Process In Support Pressure
Minghe Die Casting Company are dedicated to manufacture and provide quality and high performance Casting Parts(metal die casting parts range mainly include Thin-Wall Die Casting,Hot Chamber Die Casting,Cold Chamber Die Casting),Round Service(Die Casting Service,Cnc Machining,Mold Making,Surface Treatment).Any custom Aluminum die casting, magnesium or Zamak/zinc die casting and other castings requirements are welcome to contact us.
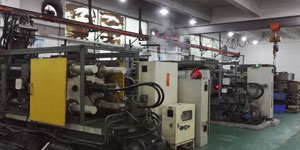
Under the control of ISO9001 and TS 16949,All processes are carried out through hundreds of advanced die casting machines, 5-axis machines, and other facilities, ranging from blasters to Ultra Sonic washing machines.Minghe not only has advanced equipment but also have professional team of experienced engineers,operators and inspectors to make the customer’s design come true.
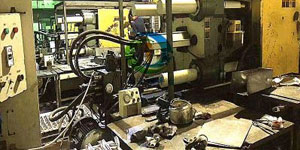
Contract manufacturer of die castings. Capabilities include cold chamber aluminum die casting parts from 0.15 lbs. to 6 lbs., quick change set up, and machining. Value-added services include polishing, vibrating, deburring, shot blasting, painting, plating, coating, assembly, and tooling. Materials worked with include alloys such as 360, 380, 383, and 413.
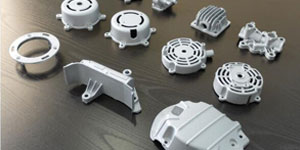
Zinc die casting design assistance/concurrent engineering services. Custom manufacturer of precision zinc die castings. Miniature castings, high pressure die castings, multi-slide mold castings, conventional mold castings, unit die and independent die castings and cavity sealed castings can be manufactured. Castings can be manufactured in lengths and widths up to 24 in. in +/-0.0005 in. tolerance.
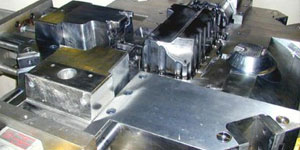
ISO 9001: 2015 certified manufacturer of die cast magnesium, Capabilities include high-pressure magnesium die casting up to 200 ton hot chamber & 3000 ton cold chamber, tooling design, polishing, molding, machining, powder & liquid painting, full QA with CMM capabilities, assembly, packaging & delivery.
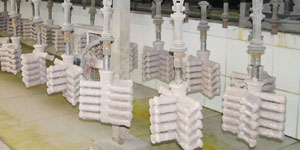
ITAF16949 certified. Additional Casting Service Include investment casting,sand casting,Gravity Casting, Lost Foam Casting,Centrifugal Casting,Vacuum Casting,Permanent Mold Casting,.Capabilities include EDI, engineering assistance, solid modeling and secondary processing.
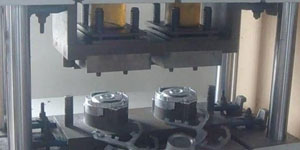
Casting Industries Parts Case Studies for: Cars, Bikes, Aircraft, Musical instruments, Watercraft, Optical devices, Sensors, Models, Electronic devices, Enclosures, Clocks, Machinery, Engines, Furniture, Jewelry, Jigs, Telecom, Lighting, Medical devices, Photographic devices, Robots, Sculptures, Sound equipment, Sporting equipment, Tooling, Toys and more.
What Can we help you do next?
∇ Go To Homepage For Die Casting China
→Casting Parts-Find out what we have done.
→Ralated Tips About Die Casting Services
By Minghe Die Casting Manufacturer |Categories: Helpful Articles |Material Tags: Aluminum Casting, Zinc Casting, Magnesium Casting, Titanium Casting, Stainless Steel Casting, Brass Casting,Bronze Casting,Casting Video,Company History,Aluminum Die Casting |Comments Off