High Vacuum/Strength And Toughness Die Casting Technology
The current status of the development and application of high vacuum die casting technology and high strength and toughness casting alloys
The high vacuum die casting method is to extract the gas in the cavity to keep the filled cavity in a vacuum state, and the molten metal is filled in the vacuum state. Since it is necessary to ensure that less gas can be involved in the filling process, the mechanical properties of the casting are also relatively required. High, which increases the difficulty of casting work forming to a certain extent. Like the ordinary die-casting method, the high-vacuum die-casting method is relatively simple to operate and has a relatively high production efficiency. Therefore, the high-vacuum die-casting method has been widely used since its emergence, and it has also shown a very strong vitality. With the continuous progress and development of science and technology, the continuous optimization of vacuum die-casting technology has made high-vacuum die-casting technology widely used. How to make full use of the cost advantages of high vacuum die-casting technology has attracted widespread attention in the field of technical research and production.
There are many problems in the application of high vacuum die-casting technology. The existence of these problems largely affects the further development of the industry, especially the further development of the foundry industry. The more obvious problem is how to keep the cavity in a vacuum state. Casting molding requires that the cavity must be kept in a vacuum state. The air in the melting furnace must be evacuated. At this stage, the general method is to connect the melting furnace to the riser pipe and the injection chamber. The air in the melting furnace is evacuated, and when the melting furnace reaches the vacuum state, the molten metal is sucked into the injection chamber. When the injection chamber reaches the vacuum state, the die-casting work can be completed. However, in the actual casting process, a common problem is that the melting furnace is difficult to reach the vacuum state, especially when the molten metal is input, air is usually brought in. The existence of air has an extremely adverse effect on the molding of the casting. Ensure the quality of castings. In addition, in the actual application of high vacuum die casting technology, the requirements for the mechanical properties of castings are also relatively high. The mechanical properties refer to the mechanical characteristics of the material under various external loads under different environments. The mechanical properties are difficult to guarantee during the die-casting process. They are affected by brittleness, strength, plasticity, hardness, toughness, fatigue strength, elasticity, The requirements for ductility, rigidity, and yield strength or yield stress have an extremely adverse effect on the full application of high vacuum die casting technology, and also have an adverse effect on the further development of the current foundry industry.
The Prospects for the development and application of high-vacuum die-casting technology and high-strength and toughness cast alloys
With the vigorous development of industry, industry has become an important industry in the country's comprehensive national strength, which is conducive to improving the country's comprehensive economic level, promoting further social and economic development, and providing sufficient impetus for social construction. However, with the vigorous development of the industry, the problems of the industrial casting process have become more and more prominent, which has become one of the important factors affecting the further development of the industry. In order to promote the further development of the industry and continuously expand the application range of die castings, the mechanical properties of the castings must be improved. In the research and development process, the application range must improve the mechanical properties of the castings. In the research and development process, die casting and laminar flow filling methods, etc. The application of these methods in industrial casting has greatly promoted the further development of the industry. However, due to the immaturity of these methods, they also have a very adverse effect on industrial casting. The development and application of high-vacuum die-casting technology and high-strength die-casting aluminum alloy have effectively improved the quality of industrial die-casting and provided sufficient guarantee for the further development of the industrial field.
High-strength die-casting aluminum alloy can meet the requirements of high-vacuum die-casting technology. The use of high-strength and toughness die-casting aluminum alloy can obtain very good quality die-casting parts. It can also effectively reduce the high-temperature melting and volatilization of gas involved in the casting due to the use of organic mold release agents. , So as to improve the quality of castings and realize the important purpose of industrial casting. At this stage, high-vacuum die-casting technology and high-strength die-casting aluminum alloy are mainly used in the production of auto parts. With the rapid development of science and technology and the gradual improvement of people’s living standards, people are increasingly relying on cars for travel, and the emergence of cars It has also improved people's lifestyles to a large extent, and has an extremely important effect on improving people's living standards. High vacuum die-casting technology and high-strength die-casting aluminum alloy technology are applied to the production of auto parts, which are mainly used in the production and manufacture of important security parts of auto parts, such as chassis suspension beams, triangle arms and steering arms. The production is relatively complicated, the manufacturing process and procedures are relatively cumbersome, and the quality is difficult to guarantee. The use of high-vacuum die-casting technology and high-strength die-casting aluminum alloy can effectively improve the quality of castings, simplify the casting procedures and processes to the greatest extent, and provide sufficient guarantee for the casting of auto parts. At the same time, applying high-vacuum die-casting technology and high-strength die-casting aluminum alloy to the production of complex auto parts can effectively improve the quality of auto manufacturing, continuously enhance the competitive advantage and competitiveness of the auto industry, and promote the further development of the auto industry. The application of high-vacuum die-casting technology and high-strength die-casting aluminum alloy in my country's automobile manufacturing industry can improve the competitiveness of my country's automobile industry, fully demonstrate the strength of my country's automobile manufacturing industry, and provide my country's enterprise manufacturing industry to achieve sustainable and stable development goals. Adequate protection.
High-vacuum die-casting technology and high-strength die-casting aluminum alloy as a very advanced die-casting technology, fully applied in my country's industrial casting, can effectively improve the quality of my country's industrial casting, promote the further development of our country's industry, and further enhance our country's comprehensive national strength.
Conclusion
The development and application of high-vacuum die-casting technology and high-strength die-casting aluminum alloys have very good prospects, which can promote the further development of my country's industry, enhance the competitiveness and competitive advantages of my country's industries, and thereby enhance China's comprehensive national strength. Therefore, it is necessary to strengthen the optimization of high-vacuum die-casting technology and high-strength and toughness die-casting aluminum alloy at this stage.
Please keep the source and address of this article for reprinting:High Vacuum/Strength And Toughness Die Casting Technology
Minghe Die Casting Company are dedicated to manufacture and provide quality and high performance Casting Parts(metal die casting parts range mainly include Thin-Wall Die Casting,Hot Chamber Die Casting,Cold Chamber Die Casting),Round Service(Die Casting Service,Cnc Machining,Mold Making,Surface Treatment).Any custom Aluminum die casting, magnesium or Zamak/zinc die casting and other castings requirements are welcome to contact us.
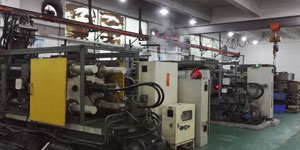
Under the control of ISO9001 and TS 16949,All processes are carried out through hundreds of advanced die casting machines, 5-axis machines, and other facilities, ranging from blasters to Ultra Sonic washing machines.Minghe not only has advanced equipment but also have professional team of experienced engineers,operators and inspectors to make the customer’s design come true.
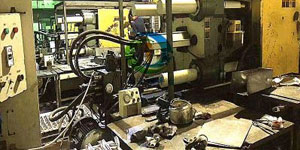
Contract manufacturer of die castings. Capabilities include cold chamber aluminum die casting parts from 0.15 lbs. to 6 lbs., quick change set up, and machining. Value-added services include polishing, vibrating, deburring, shot blasting, painting, plating, coating, assembly, and tooling. Materials worked with include alloys such as 360, 380, 383, and 413.
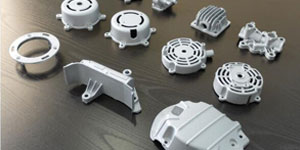
Zinc die casting design assistance/concurrent engineering services. Custom manufacturer of precision zinc die castings. Miniature castings, high pressure die castings, multi-slide mold castings, conventional mold castings, unit die and independent die castings and cavity sealed castings can be manufactured. Castings can be manufactured in lengths and widths up to 24 in. in +/-0.0005 in. tolerance.
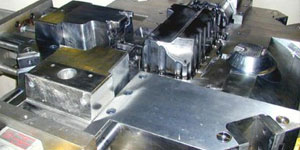
ISO 9001: 2015 certified manufacturer of die cast magnesium, Capabilities include high-pressure magnesium die casting up to 200 ton hot chamber & 3000 ton cold chamber, tooling design, polishing, molding, machining, powder & liquid painting, full QA with CMM capabilities, assembly, packaging & delivery.
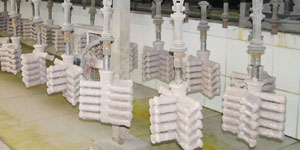
ITAF16949 certified. Additional Casting Service Include investment casting,sand casting,Gravity Casting, Lost Foam Casting,Centrifugal Casting,Vacuum Casting,Permanent Mold Casting,.Capabilities include EDI, engineering assistance, solid modeling and secondary processing.
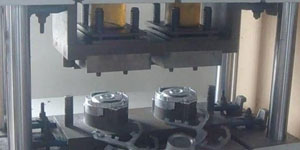
Casting Industries Parts Case Studies for: Cars, Bikes, Aircraft, Musical instruments, Watercraft, Optical devices, Sensors, Models, Electronic devices, Enclosures, Clocks, Machinery, Engines, Furniture, Jewelry, Jigs, Telecom, Lighting, Medical devices, Photographic devices, Robots, Sculptures, Sound equipment, Sporting equipment, Tooling, Toys and more.
What Can we help you do next?
∇ Go To Homepage For Die Casting China
→Casting Parts-Find out what we have done.
→Ralated Tips About Die Casting Services
By Minghe Die Casting Manufacturer |Categories: Helpful Articles |Material Tags: Aluminum Casting, Zinc Casting, Magnesium Casting, Titanium Casting, Stainless Steel Casting, Brass Casting,Bronze Casting,Casting Video,Company History,Aluminum Die Casting |Comments Off