Hot Compression Deformation Behavior Of Die-Cast AZ91D Magnesium Alloy
Due to its unique properties, the recognition of magnesium alloys in the industry continues to increase, and the scope of application is also expanding. At present, the main forming process of magnesium alloy is die-casting. In actual production, due to the needs of working conditions or process factors, it is often necessary to perform partial or overall plastic machining of magnesium alloy die castings. At the same time, the plastic machining of die castings can eliminate the shrinkage and porosity caused by the die casting process. , Improve the comprehensive mechanical properties of the material. However, magnesium alloys have poor plasticity and are difficult to perform plastic machining at room temperature; die-cast magnesium alloys are particularly difficult to perform plastic machining at room temperature due to the presence of a large number of near-network low-melting phases on the grain boundaries, and generally require thermoplastic machining. This limits the popularization and application of magnesium alloys to a certain extent.
In recent years, there have been many studies on the deformation behavior of magnesium alloys such as AZ31, AZ61, and AZ91 (non-die-cast state), but there are few reports on the deformation behavior of die-cast AZ91D magnesium alloy, especially the hot deformation behavior. In response to the above problems, this paper uses the Geeble-1500D thermal simulator to conduct a hot compression deformation experiment on the die-cast AZ91D magnesium alloy under the conditions of a strain rate of 0.01~10s -1 and a deformation temperature of 50~450℃ to study its Thermal compression deformation behavior; at the same time, the deformation microstructure was studied.
The main research work and results of the thesis are as follows:
- Analyze and process the relevant data obtained from the hot compression experiment, and obtain the die-cast AZ91D magnesium alloy rheological curve; establish the high-temperature plastic deformation constitutive equation described by Zener-Hollomom parameters as έ=1.41×10 12 [sinh(0.014 σ)] 5.295 exp(-159449.509/RT), using hyperbolic sine function to determine the deformation activation energy of the material Q=159.45kJ·mol -1, compared with the gravity casting AZ91D magnesium alloy, its flow stress and deformation activation The lower energy may be caused by the obvious difference between the gravity casting state and the die casting state of the casting process.
- According to the theory of dynamic material model and machining diagram, the power dissipation diagram, instability diagram and machining diagram of the die-cast AZ91D magnesium alloy were carried out using the experimental data of thermal compression and mathematical statistics software at strains of 0.3, 0.5 and 0.7. draw. Through the analysis of the power dissipation coefficient (η) and the instability coefficient (ξ(έ)) in the figure, it is determined that the deformation temperature is 260~350℃, the strain rate is 0.01~1s -1, which is the hot plastic machining of die-cast AZ91D magnesium alloy. The best machining area.
- In the die-cast AZ91D magnesium alloy, there are more second phases distributed on the grain boundaries in a network. These second phases gradually dissolve in the matrix with the increase of the hot compression deformation temperature; the observation of the hot compression deformation structure of the die-cast AZ91D magnesium alloy shows that the deformation temperature, strain rate, and strain affect the hot compression deformation structure Significant; the structure difference in different areas of the same sample is more obvious, the deformation is larger in the center area near the sample, the streamlined band structure perpendicular to the compression direction produced by the structure is more obvious, and dynamic recrystallization occurs on the grain boundary. However, the amount of tissue deformation is small near the edge of the sample deformation, and the tissue grows simply.
- Observation of the morphology of material die-casting defects in the process of hot compression deformation shows that hole-like defects are the main defects of die-cast magnesium alloys, and compression plastic deformation is an effective method to reduce the number of defects.
Please keep the source and address of this article for reprinting: Hot Compression Deformation Behavior Of Die-Cast AZ91D Magnesium Alloy
Minghe Die Casting Company are dedicated to manufacture and provide quality and high performance Casting Parts(metal die casting parts range mainly include Thin-Wall Die Casting,Hot Chamber Die Casting,Cold Chamber Die Casting),Round Service(Die Casting Service,Cnc Machining,Mold Making,Surface Treatment).Any custom Aluminum die casting, magnesium or Zamak/zinc die casting and other castings requirements are welcome to contact us.
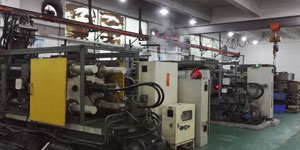
Under the control of ISO9001 and TS 16949,All processes are carried out through hundreds of advanced die casting machines, 5-axis machines, and other facilities, ranging from blasters to Ultra Sonic washing machines.Minghe not only has advanced equipment but also have professional team of experienced engineers,operators and inspectors to make the customer’s design come true.
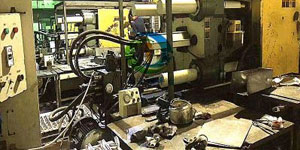
Contract manufacturer of die castings. Capabilities include cold chamber aluminum die casting parts from 0.15 lbs. to 6 lbs., quick change set up, and machining. Value-added services include polishing, vibrating, deburring, shot blasting, painting, plating, coating, assembly, and tooling. Materials worked with include alloys such as 360, 380, 383, and 413.
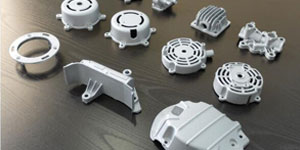
Zinc die casting design assistance/concurrent engineering services. Custom manufacturer of precision zinc die castings. Miniature castings, high pressure die castings, multi-slide mold castings, conventional mold castings, unit die and independent die castings and cavity sealed castings can be manufactured. Castings can be manufactured in lengths and widths up to 24 in. in +/-0.0005 in. tolerance.
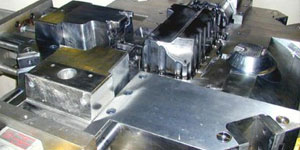
ISO 9001: 2015 certified manufacturer of die cast magnesium, Capabilities include high-pressure magnesium die casting up to 200 ton hot chamber & 3000 ton cold chamber, tooling design, polishing, molding, machining, powder & liquid painting, full QA with CMM capabilities, assembly, packaging & delivery.
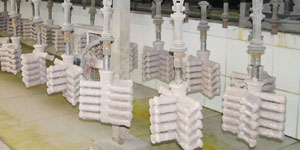
ITAF16949 certified. Additional Casting Service Include investment casting,sand casting,Gravity Casting, Lost Foam Casting,Centrifugal Casting,Vacuum Casting,Permanent Mold Casting,.Capabilities include EDI, engineering assistance, solid modeling and secondary processing.
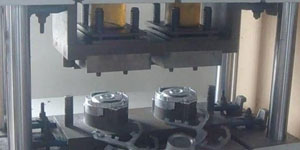
Casting Industries Parts Case Studies for: Cars, Bikes, Aircraft, Musical instruments, Watercraft, Optical devices, Sensors, Models, Electronic devices, Enclosures, Clocks, Machinery, Engines, Furniture, Jewelry, Jigs, Telecom, Lighting, Medical devices, Photographic devices, Robots, Sculptures, Sound equipment, Sporting equipment, Tooling, Toys and more.
What Can we help you do next?
∇ Go To Homepage For Die Casting China
→Casting Parts-Find out what we have done.
→Ralated Tips About Die Casting Services
By Minghe Die Casting Manufacturer |Categories: Helpful Articles |Material Tags: Aluminum Casting, Zinc Casting, Magnesium Casting, Titanium Casting, Stainless Steel Casting, Brass Casting,Bronze Casting,Casting Video,Company History,Aluminum Die Casting |Comments Off