How To Calculate The Price Of Die Casting Parts And Molds
Empirical Calculation Method
Mould price = material cost + design fee + processing fee and profit + value-added tax + mold trial fee + packaging and transportation fee
The Ratios Are Usually:
Material cost: materials and standard parts account for 15%-30% of the total cost of the mold;
Processing fee and profit: 30%-50%;
Design fee: 10%-15% of the total cost of the mold;
Trial mold: large and medium-sized molds can be controlled within 3%, and small precision molds can be controlled within 5%;
Packaging and transportation fees: can be calculated according to the actual or 3%;
VAT: 17%
Material Coefficient Method
According to the mold size and material price, the mold material cost can be calculated.
Mold price=(6~10)*material cost
Forging die, plastic die=6*material cost
Die casting mold=10*material cost
Mould Quotation Estimate
- First of all, we must look at the customer's requirements, because the requirements determine the choice of materials and the heat treatment process.
- Choose a good material, draw out a rough mold plan, and calculate the weight of the mold (calculate the price of the mold core material and the mold base material) and the cost of heat treatment. (Both are raw weight)
- Processing cost. According to the complexity of the mold core, the processing cost is generally 1.5~3:1, and the processing cost of the mold base is generally 1:1.
- The risk cost is 10% of the above total price.
- Tax
- The design cost is 10% of the total price of the mold. Mould quotation strategy and settlement method
The quotation and settlement of the mold is the continuation and result after the evaluation of the mold. From the evaluation of the mold to the quotation of the mold, it is only the first step, and the ultimate goal of the mold is to form the final settlement price of the mold through the settlement after the mold is manufactured and delivered. In this process, people always hope that mold valuation = mold price = mold settlement price. In actual operation, these four prices are not completely equal, and fluctuation error values may occur. This is the issue to be discussed below.
After the mold is evaluated, it needs to be processed appropriately and organized into a mold quotation, which is the basis for signing the mold processing contract. Through repeated negotiations and discussions, a mold price recognized by both parties was finally formed and a contract was signed. Only then can the mold processing be officially started.
1. Mold Valuation And Quotation, Quotation And Mold Price
After the mold is evaluated, it cannot be used as a quotation immediately. Generally speaking, it is necessary to conduct a comprehensive analysis based on market conditions, customer psychology, competitors, status and other factors, to properly organize the valuation, and make the first quotation with an increase of 10-30% on the basis of the valuation. After bargaining, the quotation can be lowered according to the actual situation. However, when the negotiated quotation of the mold is less than 10% of the estimated price, it is necessary to re-improve and refine the estimation of the mold. Under the condition of guaranteeing the profit, the mold processing contract is signed, and the mold price is finally determined. The price of the mold is the price approved by both parties and signed in the contract.
The mold price formed at this time may be higher or lower than the estimated price. When the negotiated mold price is lower than the guaranteed cost of the mold, the mold requirements, conditions, plans, etc. need to be revised to reduce some requirements in order to reduce the mold cost. After re-estimation, the mold price contract can be signed. It should be pointed out that molds are specialized products with high technological content and should not be used at low prices or even at a loss to cater to customers. Instead, it should be high-quality at a better price, and the quality, precision, and life of the mold should be the first priority, and the price of the mold should not be overemphasized, otherwise it will easily cause misleading actions. It is more difficult to guarantee the quality, precision and life of the mold when it is pursued at a low price.
Cheap is generally not what the mold industry does. However, when mold manufacturing and product development and production are the same accounting unit or there is an economic interest relationship, in this case, the price of the mold should be quoted at its cost price. The evaluation of the mold only estimates the basic cost price of the mold, and other costs and profits are not considered for the time being. After the profit of the product production, the additional value of the mold fee will be extracted as compensation. However, the quotation at this time cannot be used as the price of the real mold, but only as the cost of the early development of the mold. In the future, once the product is successfully developed and profits are generated, the added value of the mold fee should be extracted and returned to the mold manufacturer. The two totals can form the price of the mold. The mold price formed at this time may be higher than the mold price in the first case, and even the rate of return is very high, which is dozens of times or hundreds of times higher than the original normal mold price. Of course, it is also possible that the rate of return is equal to zero.
2. Regional And Time Differences In Mold Prices
It should also be pointed out here that the appraisal and price of molds are different in various companies, regions and countries; in different periods and in different environments, their connotations are different, that is, there are regional and time differences. Why is there a price difference? This is because: On the one hand, the mold manufacturing conditions of various companies, regions, and countries are different, and the differences in equipment technology, technology, personnel concepts, and consumption levels are caused by the cost of molds, The profit target and other estimates are different, resulting in different mold price differences. Generally, it is a more developed area, or a large-scale mold company with high technology content, advanced equipment investment, and relatively standardized large-scale mold companies. Their goal is high quality and high price. In some areas with low consumption levels, or low technology content, For small and medium-sized mold companies that invest less in equipment, their estimated mold prices are lower.
On the other hand, there is still a time difference in the price of molds, and the immediate effect is poor. Different time requirements produce different mold prices. This time difference has two aspects: one is that a pair of molds have different prices at different times; the other is that different mold manufacturing cycles have different prices.
3. Fill In The Mold Quotation
After the mold price is estimated, it is generally necessary to quote outside in the form of quotation. The main content of the quotation includes: mold quotation, cycle, required mold times (lifetime), technical requirements and conditions for molds, payment methods and settlement methods, and warranty periods.
Whether the quotation strategy of the mold is correct or not directly affects the price of the mold, the level of profit of the mold, and the performance of the mold production technology management used. It is the most important aspect of the mold enterprise management and whether it is successful!
4. Settlement Of Mold Costs
The settlement of the mold is the ultimate goal of mold design and manufacturing. The price of the mold is also subject to the final settlement price, which is the settlement price. Is the final actual mold price.
From the beginning of the mold design and manufacturing, the settlement method of the mold is accompanied by every step of the design and manufacture, each process is running, to what procedure is designed and manufactured, and what method the settlement method runs to. The settlement method will not end until the design, manufacturing, and delivery are completed, and sometimes it will even run for normal hours. All quality and technical issues in design and manufacturing are ultimately transformed into economic settlement. It can be said that economic settlement is the evaluation and affirmation of all technical quality of design and manufacturing.
The settlement method is proposed from the mold quotation, and the mold design and manufacturing start to run synchronously on the day the mold manufacturing contract is signed. Conversely, the difference in settlement methods also reflects the differences and differences in mold design and manufacturing.
Settlement methods vary from region to region and from company to company, but with the gradual improvement of the market economy, certain norms and practices have also formed. By convention, there are generally the following types of settlement methods:
(1) "Five-five" settlement: that is, as soon as the mold contract is signed, 50% of the mold price will be prepaid, and the remaining 50% will be paid after the mold trial is qualified.
This settlement method was more popular in the early mold companies. Its advantages and disadvantages are as follows:
- 1) The 50% advance payment is generally not enough to cover the basic manufacturing cost of the mold, and the manufacturing company has to invest. In other words, the 50% advance payment cannot be synchronized with the operation of the whole payment mold cost. Therefore, there is a certain investment risk for mold manufacturing companies.
- 2) After passing the test and acceptance, the balance will be settled. Make the mold warranty cost irrelevant to the settlement.
- 3) When the balance of 50% is settled, due to the large amount of money and the mold has been basically completed, it is easy to cause settlement arrears.
- 4) In case of mold failure, generally only 50% of the original advance payment will be refunded.
(2) "June 4th" settlement: that is, as soon as the mold contract is signed, 60% of the mold price will be prepaid, and the remaining 40% will be settled after the mold trial is qualified.
This settlement method is basically the same as the first settlement method. It's just an increase of 10% on the advance payment. This is a bit more advantageous than mold manufacturing companies.
(3) "Three, four, three" settlement: that is, as soon as the mold contract is signed, 30% of the mold price is prepaid, and when the mold material is prepared for the design review, another 40% of the mold price is paid when the processing starts. The remaining 30% will be paid within one week after the mold is qualified and delivered for use.
This settlement method is currently a popular one. The main features of this settlement method are as follows:
- 1) 30% of the model price paid in advance as the deposit.
- 2) According to the meeting review, check the progress and reliability, and make the second payment of 40%, which strengthened the supervision of the mold manufacturing progress.
- 3) The remaining amount is 30%. After the mold is accepted, the remaining amount will be settled after a few days of use. In this way, it is basically close to the synchronous operation used in the design and manufacture of the mold.
- 4) In case the mold fails, the mold manufacturer will not only return the full advance payment, but also pay compensation. The compensation is generally 1-2 times of the deposit.
(4) The additional value-added method of mold fee for extracting the production profit of the part: that is, when the mold is designed and manufactured, the mold user only needs to invest a small amount of money to ensure the basic cost of mold manufacturing (or no mold cost at all).
After the mold manufacturing is delivered for use, the production of the parts is started, and a part of the profit is extracted for each part produced and returned to the mold manufacturer as a mold fee.
In this way, the mold manufacturer and the user are organically linked to form a profit integration, investment risks and use benefits are closely linked, and technology and economy, quality and production benefits are completely linked together. It maximizes the value and risk of the mold. This approach is currently a horizontal development trend. Its main characteristics are: give full play to the advantages of mold manufacturers and mold users, and the capital investment is relatively active and reasonable. But for the mold maker, the risk is greater, but the rate of return is also considerable.
There are many ways to settle the mold, and they are not the same. But they all have one thing in common, that is, efforts to organically combine the technical and economic indicators of the mold to produce mutual benefits for both parties. Make the mold from the evaluation to the quotation, from the quotation to the contract price; from the contract price to the settlement price, the actual mold price is formed. Implement high-quality and preferential prices. Efforts to keep mold prices in line with international practices, and constantly strive to produce high, precise and excellent molds, to form a common good and maximum economic benefit situation. This is the ultimate goal of mold design and manufacturing!
Please keep the source and address of this article for reprinting: How To Calculate The Price Of Die Casting Parts And Molds
Minghe Casting Company are dedicated to manufacture and provide quality and high performance Casting Parts(metal die casting parts range mainly include Thin-Wall Die Casting,Hot Chamber Die Casting,Cold Chamber Die Casting),Round Service(Die Casting Service,Cnc Machining,Mold Making,Surface Treatment).Any custom Aluminum die casting, magnesium or Zamak/zinc die casting and other castings requirements are welcome to contact us.
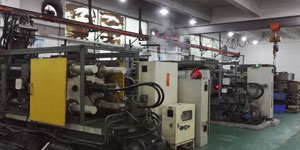
Under the control of ISO9001 and TS 16949,All processes are carried out through hundreds of advanced die casting machines, 5-axis machines, and other facilities, ranging from blasters to Ultra Sonic washing machines.Minghe not only has advanced equipment but also have professional team of experienced engineers,operators and inspectors to make the customer’s design come true.
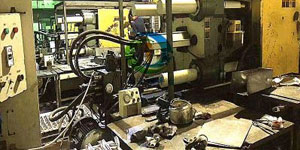
Contract manufacturer of die castings. Capabilities include cold chamber aluminum die casting parts from 0.15 lbs. to 6 lbs., quick change set up, and machining. Value-added services include polishing, vibrating, deburring, shot blasting, painting, plating, coating, assembly, and tooling. Materials worked with include alloys such as 360, 380, 383, and 413.
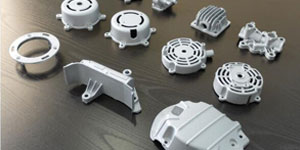
Zinc die casting design assistance/concurrent engineering services. Custom manufacturer of precision zinc die castings. Miniature castings, high pressure die castings, multi-slide mold castings, conventional mold castings, unit die and independent die castings and cavity sealed castings can be manufactured. Castings can be manufactured in lengths and widths up to 24 in. in +/-0.0005 in. tolerance.
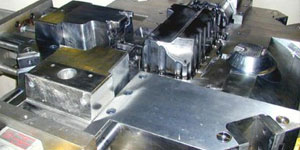
ISO 9001: 2015 certified manufacturer of die cast magnesium, Capabilities include high-pressure magnesium die casting up to 200 ton hot chamber & 3000 ton cold chamber, tooling design, polishing, molding, machining, powder & liquid painting, full QA with CMM capabilities, assembly, packaging & delivery.
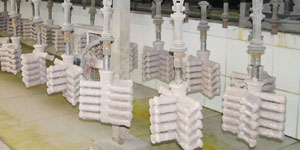
ITAF16949 certified. Additional Casting Service Include investment casting,sand casting,Gravity Casting, Lost Foam Casting,Centrifugal Casting,Vacuum Casting,Permanent Mold Casting,.Capabilities include EDI, engineering assistance, solid modeling and secondary processing.
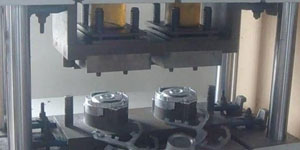
Casting Industries Parts Case Studies for: Cars, Bikes, Aircraft, Musical instruments, Watercraft, Optical devices, Sensors, Models, Electronic devices, Enclosures, Clocks, Machinery, Engines, Furniture, Jewelry, Jigs, Telecom, Lighting, Medical devices, Photographic devices, Robots, Sculptures, Sound equipment, Sporting equipment, Tooling, Toys and more.
What Can we help you do next?
∇ Go To Homepage For Die Casting China
→Casting Parts-Find out what we have done.
→Ralated Tips About Die Casting Services
By Minghe Die Casting Manufacturer |Categories: Helpful Articles |Material Tags: Aluminum Casting, Zinc Casting, Magnesium Casting, Titanium Casting, Stainless Steel Casting, Brass Casting,Bronze Casting,Casting Video,Company History,Aluminum Die Casting |Comments Off