How to control the starting time of self-hardening furan resin sand under low temperature environment
Mainly studied the relationship between furan resin sand's usable time, mold release time and strength under low temperature environment, and determined the appropriate sand temperature and resin curing agent ratio to guide workshop production.
Background
Furan resin no-bake sand is compact and hard, easy to control, and has high dimensional accuracy of castings. Therefore, the current no-bake resin sand process has been used to cast various metal castings, such as machine tools required for machining and gas turbines used in shipbuilding. And other iron castings can be produced by the self-hardening resin sand process. Nowadays, the rapid development of computer automation control has accelerated the development and application of self-setting resin sand technology.
However, furan resin sand has its own shortcomings. The usable time, mold release time and final strength are greatly affected by changes in temperature and humidity, which can easily cause production instability and adversely affect workshop production. According to the casting materials used by the company, this paper studies the curing curve of furan resin and benzenesulfonic acid curing agent in different proportions under low temperature environment, determines the best proportion, and explores the hardening trend of wood mold and metal mold resin sand on this basis. , Put forward the method of accelerating hardening mold release to guide workshop production.
Experimental research
This article uses furan resin, benzene sulfonic acid curing agent and regenerated silica sand used by the company on site as the test materials
Instruments: electronic balance, automatic mixer, compression tester, temperature and humidity meter, thermometer, stopwatch. The ambient temperature is 5℃, the ambient humidity is 30%, and the sand temperature is 15℃. Weigh 1000g of sand with an electronic balance. The resin addition ratio is 0.8% and 1.0% of the sand weight. The curing agent is added to 30%, 35%, 40%, 45%, 50% of the resin weight, respectively. Orthogonal test makes φ40mm×40mm Molding sand test block. At the same time, record the operating time, mold release time and 24h compressive strength.
According to the needs of on-site production, there are the following requirements for molding sand:
- The molding sand must maintain a certain final strength (small castings ≥2.0MPa, large castings ≥3.0MPa) to reduce core deformation and prevent sand inclusion in castings.
- The necessary operating time should be ensured to facilitate the placement of core iron, cold iron and compact operation.
- In order to ensure smooth on-site production, the core ejection time should be as short as possible to improve production efficiency.
- In the case of meeting production requirements, the amount of binder added should be as low as possible, which not only saves costs, but also reduces the gas generated by the combustion of organic binder during pouring, improves the quality of castings, and protects the environment.
Based on the above factors, the best liquid-material ratio of mechanical reclaimed sand is resin 1.0% (accounting for sand weight), curing agent 30% (accounting for resin); the best liquid-material ratio of thermal reclaimed sand is resin 1.0% (accounting for sand weight) ), curing agent 45% (accounting for resin).
Further, taking into account the difference in the ejection time between the wooden mold and the metal mold produced on site, on the basis of the above test, the wooden core box and the metal core box were used to prepare samples, and the compressive strength was measured every 1h, and the strength change trend of the first 6h and 24h were recorded. Final strength
Also under the environment of 5℃, when the resin and curing agent are added in a certain proportion:
- The wooden mold modelling takes about 2 to 3 hours to take out the mold from the mold (1.5MPa), and the mold hardens to achieve sufficient strength without deformation; the metal mold takes 5 hours to take out, and the inner part can be taken out too early. Completely hardened, extrusion deformation will occur, and the final strength is basically the same, about 3MPa.
- Simply increasing the acidity value of the curing agent can not significantly increase the hardening speed and shorten the mold release time.
According to this hardening trend, on-site production can reasonably arrange production according to different models' starting time to avoid premature starting of the mold. Insufficient sand hardening strength in the core will cause core deformation and cracking. The model core has strong strength and is tightly bonded to the mold. , It is difficult to start the mold, resulting in poor surface quality and delaying on-site production.
Conclusion
In the low temperature environment, when furan resin and benzene sulfonic acid curing agent are used as binders, there are three experimental conclusions as follows:
- The best liquid material for mechanical reclaimed sand is resin 1.0% (accounting for sand weight), curing agent 30% (accounting for resin); the best liquid material addition for thermal reclaimed sand is resin 1.0% (accounting for sand weight), curing Agent 45% (accounting for resin).
- The other conditions remain unchanged. Simply increasing the total acidity of the curing agent cannot significantly shorten the mold release time. The internal reaction and hardening can be accelerated by increasing the temperature of the model, the temperature of the cold iron and the tooling.
- When the conditions are the same, the ejection time of the wooden mold is greatly reduced compared with the metal mold, and the former is 1/2 of the latter.
Please keep the source and address of this article for reprinting: How to control the starting time of self-hardening furan resin sand under low temperature environment
Minghe Die Casting Company are dedicated to manufacture and provide quality and high performance Casting Parts(metal die casting parts range mainly include Thin-Wall Die Casting,Hot Chamber Die Casting,Cold Chamber Die Casting),Round Service(Die Casting Service,Cnc Machining,Mold Making,Surface Treatment).Any custom Aluminum die casting, magnesium or Zamak/zinc die casting and other castings requirements are welcome to contact us.
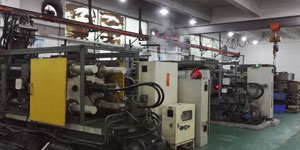
Under the control of ISO9001 and TS 16949,All processes are carried out through hundreds of advanced die casting machines, 5-axis machines, and other facilities, ranging from blasters to Ultra Sonic washing machines.Minghe not only has advanced equipment but also have professional team of experienced engineers,operators and inspectors to make the customer’s design come true.
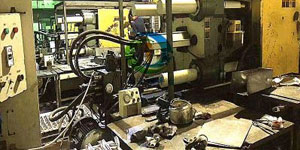
Contract manufacturer of die castings. Capabilities include cold chamber aluminum die casting parts from 0.15 lbs. to 6 lbs., quick change set up, and machining. Value-added services include polishing, vibrating, deburring, shot blasting, painting, plating, coating, assembly, and tooling. Materials worked with include alloys such as 360, 380, 383, and 413.
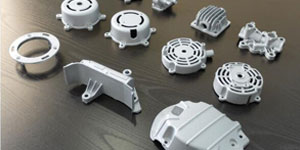
Zinc die casting design assistance/concurrent engineering services. Custom manufacturer of precision zinc die castings. Miniature castings, high pressure die castings, multi-slide mold castings, conventional mold castings, unit die and independent die castings and cavity sealed castings can be manufactured. Castings can be manufactured in lengths and widths up to 24 in. in +/-0.0005 in. tolerance.
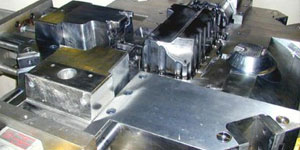
ISO 9001: 2015 certified manufacturer of die cast magnesium, Capabilities include high-pressure magnesium die casting up to 200 ton hot chamber & 3000 ton cold chamber, tooling design, polishing, molding, machining, powder & liquid painting, full QA with CMM capabilities, assembly, packaging & delivery.
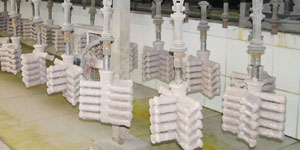
ITAF16949 certified. Additional Casting Service Include investment casting,sand casting,Gravity Casting, Lost Foam Casting,Centrifugal Casting,Vacuum Casting,Permanent Mold Casting,.Capabilities include EDI, engineering assistance, solid modeling and secondary processing.
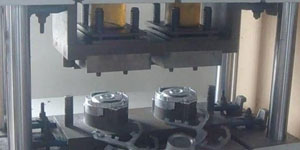
Casting Industries Parts Case Studies for: Cars, Bikes, Aircraft, Musical instruments, Watercraft, Optical devices, Sensors, Models, Electronic devices, Enclosures, Clocks, Machinery, Engines, Furniture, Jewelry, Jigs, Telecom, Lighting, Medical devices, Photographic devices, Robots, Sculptures, Sound equipment, Sporting equipment, Tooling, Toys and more.
What Can we help you do next?
∇ Go To Homepage For Die Casting China
→Casting Parts-Find out what we have done.
→Ralated Tips About Die Casting Services
By Minghe Die Casting Manufacturer |Categories: Helpful Articles |Material Tags: Aluminum Casting, Zinc Casting, Magnesium Casting, Titanium Casting, Stainless Steel Casting, Brass Casting,Bronze Casting,Casting Video,Company History,Aluminum Die Casting |Comments Off