How To Determine The Quality Of Casting Coatings
1. Main technical indicators of foundry coatings
density
The density of the casting coating reflects the amount of solid particles in the coating. If the density of the casting coating is too small, the thickness of the coating layer formed on the sand mold and sand core surface will be insufficient each time it is painted, and it is difficult to play a protective role. Therefore, in general, the density of the casting coating is good; but the density of the coating;The bigger the better, if the density is too high, it will be difficult to apply the paint, which will cause problems such as uneven surface of the coating, local accumulation, etc., and will also adversely affect the quality of the casting. There is a certain relationship between paint density and concentration. The density of the casting coating can be measured with a graduated cylinder weighing method or by a Baumemeter, but the reading of the Baumemeter is greatly affected by the viscosity of the casting coating.
Conditional viscosity
No. 4 and No. 1 viscosity cups are commonly used in casting production to determine the conditional viscosity of coatings. The purpose of measuring the viscosity is to control the paintability, the depth of penetration into the sand mold and core surface, and the thickness of the coating. Generally, foundry coating manufacturers have recommended coating condition viscosity.
Suspension
Suspension is an important performance of casting coatings. The general measurement methods include relative height sedimentation method (graduated cylinder method), sedimentation meter method and sedimentation rate method. Among them, the measuring cylinder method is the simplest and most practical method.
Paintability
Generally judged by the experience of the operator, a more objective method is to determine the apparent viscosity of the casting coating at different shear rates. The ratio of the apparent viscosity of the paint at low rotation speed (6r/min) and high rotation speed (60r/min) is the painting index M.
Leveling
When brushing or flowing paint on the surface of sand molds or sand cores, the coating is built up after brushing or flowing, and the surface often has grooves and brush marks. These grooves and brush marks may disappear in a short time or may remain . The ability to automatically disappear the brush marks or grooves on the surface of the wet paint layer is called leveling.
Flowability
Due to the influence of gravity, the casting coating has a tendency to flow down on the vertical surface of the mold (core), and the thickness of the lower coating is greater than the thickness of the upper coating, and even a phenomenon of accumulation at the bottom of the mold (core). This property is called flow Sex.
Permeability
Casting coating permeability refers to the ability of the coating to penetrate into the pores of the sand mold. The casting coating has a large penetration rate, which can enhance the adhesion of the coating to the sand mold, and at the same time, it can reinforce the sand mold and improve the sand resistance of the sand mold. The penetration depth of the coating can be tested by dipping a standard sand block.
Coating pH value: Generally, the pH value of casting coatings varies from 4 to 11, but alkaline casting coatings are more commonly used, usually in the range of 8 to 10. The pH value is not only used as an indicator of the performance of casting coatings, but also as a method to monitor the performance of coatings during use and storage. It is a process monitoring indicator for the production and use of coatings. Usually paint can be measured by colorimetric method and potentiometer method.
Coating breathability
The coating forms an isolation layer between the metal and the surface of the sand mold (core). The coating is required to be dense. Except for the lost foam coating, the air permeability should be low. Air permeability can be measured by using a certain amount of air under a certain pressure through a standard cylindrical sample.
Anti-friction strength of coating
After the sand mold and sand core are coated, they must go through the processes of handling, drying, removing the surface dust and matching the box without being damaged. Therefore, the coating after drying and curing must have a certain surface strength-resistance to abrasion . The more accurate methods for measuring the anti-scratch strength of the coating include the scratching method, the pressure method, the mechanical scrubbing method, the falling sand method, and the vibration method.
.
The paint application manufacturer can determine the anti-scratch strength of the coating by hand-scratching. This method can divide the anti-scratch strength of the coating into four levels:
- 1. Good: Use fingernails to draw the paint layer hard to not drop the powder;
- 2. Better: Use your fingernails to scratch the paint layer and drop the powder;
- 3. Yes: Use your fingers to rub the paint layer hard to drop the powder;
- 4. Poor: The powder will fall off when you touch the paint layer with your fingers.
The surface strength of the coating measured by the hand-scratching method is related to the type and amount of the attached binder. As the amount of binder increases, the surface strength of the coating increases. This shows that the main factor that affects the surface strength of the coating is the amount and type of binder. When considering the surface strength, the main consideration is the influence of the adhesive.
Paint moisture absorption
Sand molds and sand cores coated with water-based coatings will absorb moisture from the air after drying, which will deteriorate their performance, reduce their strength, and rapidly increase their air volume. In severe cases, they can cause defects such as sand sticking, loose structure and pores in the castings. . The hygroscopicity of the coating is mainly related to the adhesive, and the water-soluble adhesive has strong hygroscopicity. For long-term storage of sand molds and sand cores coated with paint before casting, the moisture absorption of the coating must be tested.
The basic method for determining the moisture absorption of the coating is to place the coating sample in a constant humidity box with a certain humidity for a certain period of time, and then weigh the sample before and after the maintenance.
Coating thermal conductivity
The thermal insulation and chilling properties of casting coatings are particularly important for the selection of metallic coatings. Chilling coating is used in the thick wall of the casting to accelerate the cooling of the casting, and the thermal insulation coating is used in the thin wall to cool the casting slowly. The thermal conductivity of the coating can be measured by the immersion melt method.
The so-called gas evolution refers to the volume of gas produced by a unit mass fraction of paint at high temperatures, expressed in mL/g, and measured with a special gas emission meter.
Ignition loss
Ignition loss is the percentage of the original weight of the paint sample dried at 105-110°C. After being burned in a non-oxidizing atmosphere gradually heated to 950-1000°C for 1 hour, the weight loss of the sample is the percentage of the original weight.
Paint sintering point
The sintering point of the foundry coating indicates the temperature at which the surface of the coating refractory filler particles or the inter-particle mixture starts to melt. There are SJY image type sintering point tester method and tube furnace sintering method to determine the few contact points of paint. A five-level evaluation method is used for evaluation.
Coating refractoriness
Refers to the melting point or softening point of the refractory powder in the casting coating, that is, its ability to withstand high temperatures.
Coating heat exposure and crack resistance
The thermal cracking resistance of casting coatings refers to the ability of the coating layer to resist cracks and peeling caused by high-temperature heating. The four-level evaluation method is used for the determination.
- Level 1: The surface is smooth and has no cracks, or there are only very fine cracks, and there is no peeling phenomenon between the coating and the substrate;
- Level 2: There are small dendritic or net-like cracks on the surface, the crack width is less than 0.5mm, and there is no peeling between the paint and the substrate;
- Level 3: There are dendritic or reticulated cracks on the coating surface, the crack width is less than 1mm, the crack is deep, there is no through-thick crack along the horizontal or vertical direction, and there is no obvious peeling between the coating and the substrate;
- Level 4: There are dendritic or reticulated cracks on the surface, the width is greater than 1mm, there are through cracks in the longitudinal or transverse direction, and there is peeling between the paint and the substrate.
It can be seen from the above performance indicators that, as a special coating category, the basic requirements of foundry coatings are not much different from those of commonly used coatings. It is nothing more than consideration from the three aspects of coating, coating, and use effect. If high-temperature performance is not considered, the average civil paint researcher can fully understand and intervene in the research of this type of paint. The existing foundry coating level in our country, including the more powerful ones such as sinking and casting, also has a big gap with foreign products. The author believes that if they are willing, the majority of foundry coating researchers will definitely be able to contribute to the development of our country in this field, and then to the development of our country's foundry industry.
2. Inspection method of casting coating index
- 1. Viscosity:Take 120 ml from the produced product and add it to the viscosity cup to prepare for timing. Open the opening of the viscosity cup. When the paddle is left to 100 ml in the graduated cylinder, write down the time. How many seconds it takes for each 100 ml drop like a graduated cylinder, that is The viscosity of the paint.
- 2. Density:Weigh the weight of the 100 ml graduated cylinder with a balance, and then subtract the mass of the empty graduated cylinder to get the specific gravity.
- 3. Suspended:From the calculation of the time when the slurry is added to the graduated cylinder, every 8 hours, 12 hours, and 24 hours, observe the sedimentation of the slurry, and what is the scale of the corresponding graduated cylinder to obtain the suspension value.
- 4. Solid content:According to the added amount of dry material and the volatilization amount of wet material, calculate the solid content by referring to the formula.
- 5. Leveling:Attach the slurry to the foundry sand mold by dipping, brushing, spraying, or flow coating, and observe the dripping on the surface of the sand mold, and whether there are accumulated brush marks or flow marks. Generally, the leveling property is good and there are few flow marks. .
- 6. Strength:Dry the coated sand mold, touch it with your fingers, scratch it, observe the peeling of the coating, break the sand mold, observe the thickness of the coating, and the thickness that penetrates into the sand mold.
- 7. Gas volume:The gas evolution test shall be carried out in accordance with GB/T 2684 "Test Method for Foundry Sand and Mixtures".
Please keep the source and address of this article for reprinting:How To Determine The Quality Of Casting Coatings
Minghe Die Casting Company are dedicated to manufacture and provide quality and high performance Casting Parts(metal die casting parts range mainly include Thin-Wall Die Casting,Hot Chamber Die Casting,Cold Chamber Die Casting),Round Service(Die Casting Service,Cnc Machining,Mold Making,Surface Treatment).Any custom Aluminum die casting, magnesium or Zamak/zinc die casting and other castings requirements are welcome to contact us.
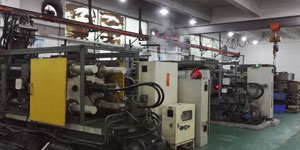
Under the control of ISO9001 and TS 16949,All processes are carried out through hundreds of advanced die casting machines, 5-axis machines, and other facilities, ranging from blasters to Ultra Sonic washing machines.Minghe not only has advanced equipment but also have professional team of experienced engineers,operators and inspectors to make the customer’s design come true.
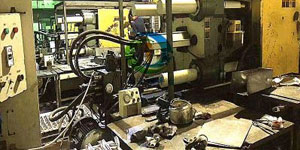
Contract manufacturer of die castings. Capabilities include cold chamber aluminum die casting parts from 0.15 lbs. to 6 lbs., quick change set up, and machining. Value-added services include polishing, vibrating, deburring, shot blasting, painting, plating, coating, assembly, and tooling. Materials worked with include alloys such as 360, 380, 383, and 413.
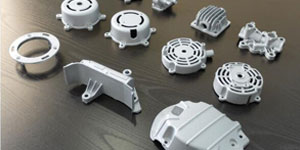
Zinc die casting design assistance/concurrent engineering services. Custom manufacturer of precision zinc die castings. Miniature castings, high pressure die castings, multi-slide mold castings, conventional mold castings, unit die and independent die castings and cavity sealed castings can be manufactured. Castings can be manufactured in lengths and widths up to 24 in. in +/-0.0005 in. tolerance.
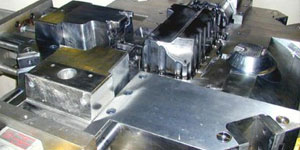
ISO 9001: 2015 certified manufacturer of die cast magnesium, Capabilities include high-pressure magnesium die casting up to 200 ton hot chamber & 3000 ton cold chamber, tooling design, polishing, molding, machining, powder & liquid painting, full QA with CMM capabilities, assembly, packaging & delivery.
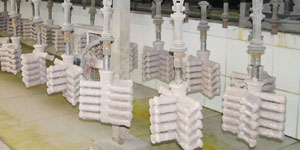
ITAF16949 certified. Additional Casting Service Include investment casting,sand casting,Gravity Casting, Lost Foam Casting,Centrifugal Casting,Vacuum Casting,Permanent Mold Casting,.Capabilities include EDI, engineering assistance, solid modeling and secondary processing.
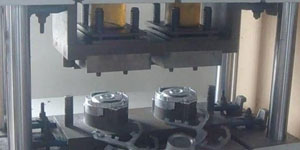
Casting Industries Parts Case Studies for: Cars, Bikes, Aircraft, Musical instruments, Watercraft, Optical devices, Sensors, Models, Electronic devices, Enclosures, Clocks, Machinery, Engines, Furniture, Jewelry, Jigs, Telecom, Lighting, Medical devices, Photographic devices, Robots, Sculptures, Sound equipment, Sporting equipment, Tooling, Toys and more.
What Can we help you do next?
∇ Go To Homepage For Die Casting China
→Casting Parts-Find out what we have done.
→Ralated Tips About Die Casting Services
By Minghe Die Casting Manufacturer |Categories: Helpful Articles |Material Tags: Aluminum Casting, Zinc Casting, Magnesium Casting, Titanium Casting, Stainless Steel Casting, Brass Casting,Bronze Casting,Casting Video,Company History,Aluminum Die Casting |Comments Off