How To Find The Best Position Of Vacuum Valve In The Die Cast Tooling?
Compared with sand mold and gravity casting, the microstructure of traditional die castings is not satisfactory. The main reason is that the injection of high-speed metal flow at the gate is easier to contact the cavity than when the metal is slowly fed into the sand or metal mold cavity air. The focus of the vacuum die-casting process is to minimize this gas-liquid contact. Therefore, effectively exhausting the gas in the cavity is the key to the design of the vacuum die-casting mold.
For die-casting molds, there is no essential difference between traditional exhaust design and vacuum exhaust design. The only way to exhaust is that the former is passive exhaust, which uses metal flow to exhaust gas, which is the so-called positive pressure injection; the latter is active Exhaust, that is, by using a vacuum device to extract the gas in the cavity, it is also called negative pressure injection. As far as the exhaust effect is concerned, there is a big difference between the two. The correct vacuum exhaust application will greatly reduce the gas content in the cavity, thereby effectively improving the quality of the product.
This article combines the China Die Casting Cloud Computing Platform to discuss the location of the vacuum valve involved in the design of the vacuum mold scheme, focusing on whether the vacuum valve should be farther away from the inner gate or closer?
In the process of vacuum die-casting mold design, the position of the vacuum valve should be able to keep the vacuum valve open for a long time, so as to extract as much gas as possible.
The vacuum valve must be set at the position where the alloy melt is filled last, but this position may be counterintuitive, as shown in Figure 3: Like conventional die-casting, vacuum die-casting presents an atomized flow. If the vacuum valve is set at the farthest from the gate Position, the vacuum valve may be closed earlier in the cavity filling process.
In order to vividly illustrate the above point of view, two targeted models are hereby designed, as shown in Figures 5 and 6 below. Die-casting mold filling simulation is carried out through the Chinese die-casting cloud computing platform to observe the flow of alloy melt in the cavity and understand intuitively The difference between the two vacuum valve positions in the actual die-casting process.
Comparison of China Cloud Simulation Results
In the example on the left, when the vacuum valve is located far away from the gate, the vacuum valve is blocked at the beginning of filling;
In the example on the right, when the vacuum valve is located close to the gate, the vacuum valve will continue to function during the filling process
It can be seen that the design of the vacuum valve in Figure 5 is indeed counter-intuitive. When the molten metal is filled, the vacuum valve is already blocked, and the vacuum valve in Figure 6 can maintain the maximum unobstructed flow, which is valuable for vacuum exhaust. Time (approximately 40ms in this example). Of course, this model example is relatively simple. In actual design and development work, the position design of the vacuum valve can use the powerful die-casting simulation capabilities of the China Die-casting cloud computing platform to determine its best position.
Please keep the source and address of this article for reprinting:How To Find The Best Position Of Vacuum Valve In The Die Cast Tooling?
Minghe Die Casting Company are dedicated to manufacture and provide quality and high performance Casting Parts(metal die casting parts range mainly include Thin-Wall Die Casting,Hot Chamber Die Casting,Cold Chamber Die Casting),Round Service(Die Casting Service,Cnc Machining,Mold Making,Surface Treatment).Any custom Aluminum die casting, magnesium or Zamak/zinc die casting and other castings requirements are welcome to contact us.
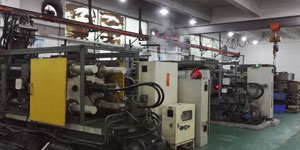
Under the control of ISO9001 and TS 16949,All processes are carried out through hundreds of advanced die casting machines, 5-axis machines, and other facilities, ranging from blasters to Ultra Sonic washing machines.Minghe not only has advanced equipment but also have professional team of experienced engineers,operators and inspectors to make the customer’s design come true.
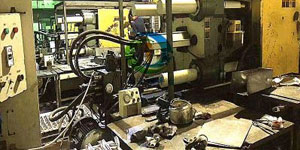
Contract manufacturer of die castings. Capabilities include cold chamber aluminum die casting parts from 0.15 lbs. to 6 lbs., quick change set up, and machining. Value-added services include polishing, vibrating, deburring, shot blasting, painting, plating, coating, assembly, and tooling. Materials worked with include alloys such as 360, 380, 383, and 413.
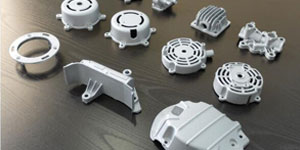
Zinc die casting design assistance/concurrent engineering services. Custom manufacturer of precision zinc die castings. Miniature castings, high pressure die castings, multi-slide mold castings, conventional mold castings, unit die and independent die castings and cavity sealed castings can be manufactured. Castings can be manufactured in lengths and widths up to 24 in. in +/-0.0005 in. tolerance.
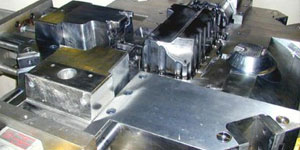
ISO 9001: 2015 certified manufacturer of die cast magnesium, Capabilities include high-pressure magnesium die casting up to 200 ton hot chamber & 3000 ton cold chamber, tooling design, polishing, molding, machining, powder & liquid painting, full QA with CMM capabilities, assembly, packaging & delivery.
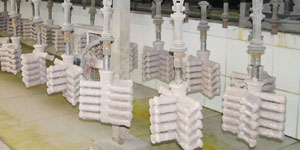
ITAF16949 certified. Additional Casting Service Include investment casting,sand casting,Gravity Casting, Lost Foam Casting,Centrifugal Casting,Vacuum Casting,Permanent Mold Casting,.Capabilities include EDI, engineering assistance, solid modeling and secondary processing.
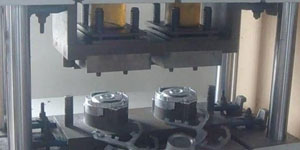
Casting Industries Parts Case Studies for: Cars, Bikes, Aircraft, Musical instruments, Watercraft, Optical devices, Sensors, Models, Electronic devices, Enclosures, Clocks, Machinery, Engines, Furniture, Jewelry, Jigs, Telecom, Lighting, Medical devices, Photographic devices, Robots, Sculptures, Sound equipment, Sporting equipment, Tooling, Toys and more.
What Can we help you do next?
∇ Go To Homepage For Die Casting China
→Casting Parts-Find out what we have done.
→Ralated Tips About Die Casting Services
By Minghe Die Casting Manufacturer |Categories: Helpful Articles |Material Tags: Aluminum Casting, Zinc Casting, Magnesium Casting, Titanium Casting, Stainless Steel Casting, Brass Casting,Bronze Casting,Casting Video,Company History,Aluminum Die Casting |Comments Off