How to greatly improve the quality of bearing steel by super fast cooling after rolling
Bearings are an important part of mechanical equipment. To a certain extent, the quality of bearings restricts the speed and progress of the national economy, national defense construction and scientific and technological modernization, and the progress of bearing steel production technology directly affects the bearing industry For development, industrially developed countries attach great importance to the research on the quality of bearing steel products.
To improve the quality of bearing steel and ensure that it has higher fatigue strength, compressive strength, surface hardness and good service life, it is necessary to improve the purity of the steel and the uniformity of carbides in the steel, mainly the inclusions in the material. The content, type of inclusions and gas content; and the uniformity of the shape, size and distribution of carbides is another important indicator to measure the quality of bearing steel products.
During the cooling process after hot rolling, the secondary carbides formed have an important impact on the performance of the bearing steel. Therefore, it is required that the network carbide in the bearing steel must be less than 2.5. Too much network carbide will bring serious consequences:
- In the subsequent quenching of the finished product, it cannot be completely eliminated.
- The net-like carbides retained in the bearing steel significantly increase the brittleness of parts and reduce the ability to withstand impact loads.
- Under the action of dynamic load, parts are easy to break along the grain boundary.
- Increase the tendency of quenching cracking.
At present, my country mainly adopts low-temperature rolling process to control the precipitation of bearing steel network carbides, and then supplements with a certain rate of cooling. However, this process depends on the capacity of the rolling mill and requires sufficient controlled cooling capacity before finishing rolling. After the water cooling, there is enough isothermal space before the final rolling. In the continuous rolling production line, low-temperature rolling is realized. Due to the insufficient cooling capacity of the existing cooling equipment, the temperature is difficult to accurately control, especially the large-size bars above Ф30mm, the product quality is unstable, and the network carbide precipitation is serious.
In order to improve the product quality of various specifications of bearing steel and reduce the heavy reliance on rolling mills and other equipment in the production of bearing steel, the State Key Laboratory of Rolling Technology and Continuous Rolling Automation (RAL) of Northeastern University has carried out the ultra-fast cooling technology of bearing steel bars. Research work has been carried out on the precipitation conditions of carbides and the phase transition during continuous cooling.
The micro-hardness of the bearing steel structure and the pearlite lamella spacing are affected by the cooling rate after rolling. As the cooling rate increases after hot rolling, the pearlite lamella spacing decreases while the microhardness value increases, and the smaller lamella spacing is very beneficial for the next spheroidizing annealing.
The control principle is that during the continuous cooling process of the subcooled austenite, the austenite will inevitably appear in the carbon-poor zone and the carbon-rich zone. Once the nucleation conditions are met, while ferrite is constructed in the carbon-poor zone, cementite is also constructed in the carbon-rich zone. The two are synchronized at the same time, eutectoid and symbiosis, forming a pearlite nucleus (ferrite + Cementite), and at the same time new crystal nuclei are produced in other parts and grow up continuously. When pearlite is formed, longitudinal growth means that cementite and ferrite sheets continuously extend into austenite at the same time, while lateral growth means that cementite and ferrite sheets are alternately stacked to increase.
Increasing the continuous cooling rate after deformation will play a role in refining the austenite grains. The size of the austenite grains has no obvious effect on the pearlite lamella spacing, but affects the size of the pearlite pellets. The austenite grains are fine and the grain boundary area per unit volume increases, which will promote the nucleation of pearlite. If the number of nucleation sites of pearlite increases, the diameter of pearlite pellets decreases.
The ultra-rapid cooling technology is applied to the bearing steel mesh carbide control, so that the bearing steel quickly passes through the area where carbide precipitation is strong after rolling, which can significantly reduce or avoid the precipitation of secondary carbides along the grain boundary.
The finite element method is used to simulate and analyze the temperature field of the ultra-fast cooling process of bearing steel of different specifications after rolling, and a reasonable cooling process route is determined. On this basis, an ultra-fast cooling device for bearing steel bars and related Control System.
According to the requirements of ultra-rapid cooling process, combined with actual production conditions, the cooling equipment that meets the requirements of ultra-rapid cooling process of bearing steel after rolling was designed, and an automatic control system was developed, and a complete mathematical model was established to make the temperature control accuracy of bearing steel and Cooling uniformity has been greatly improved
The specifications of bearing steel produced by ultra-fast cooling technology are mainly Ф15.3mm~Ф60mm. The qualification rate of bearing steel mesh carbides of Ф30mm or less and class 2.0 or less has been increased from about 10% to 100%; for Ф30mm~Ф60mm bearing steel mesh carbides, it has been increased from 2.5~4 to 2.0. The following pass rate is more than 95%. For the bearing steel of Ф60mm~Ф120mm, the scratches on the surface after ultra-fast cooling have been significantly improved.
Please keep the source and address of this article for reprinting:How to greatly improve the quality of bearing steel by super fast cooling after rolling
Minghe Die Casting Company are dedicated to manufacture and provide quality and high performance Casting Parts(metal die casting parts range mainly include Thin-Wall Die Casting,Hot Chamber Die Casting,Cold Chamber Die Casting),Round Service(Die Casting Service,Cnc Machining,Mold Making,Surface Treatment).Any custom Aluminum die casting, magnesium or Zamak/zinc die casting and other castings requirements are welcome to contact us.
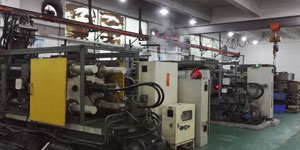
Under the control of ISO9001 and TS 16949,All processes are carried out through hundreds of advanced die casting machines, 5-axis machines, and other facilities, ranging from blasters to Ultra Sonic washing machines.Minghe not only has advanced equipment but also have professional team of experienced engineers,operators and inspectors to make the customer’s design come true.
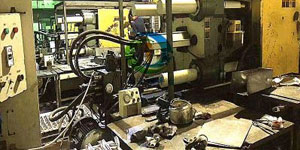
Contract manufacturer of die castings. Capabilities include cold chamber aluminum die casting parts from 0.15 lbs. to 6 lbs., quick change set up, and machining. Value-added services include polishing, vibrating, deburring, shot blasting, painting, plating, coating, assembly, and tooling. Materials worked with include alloys such as 360, 380, 383, and 413.
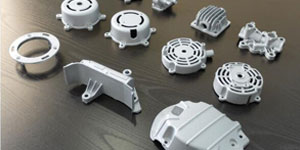
Zinc die casting design assistance/concurrent engineering services. Custom manufacturer of precision zinc die castings. Miniature castings, high pressure die castings, multi-slide mold castings, conventional mold castings, unit die and independent die castings and cavity sealed castings can be manufactured. Castings can be manufactured in lengths and widths up to 24 in. in +/-0.0005 in. tolerance.
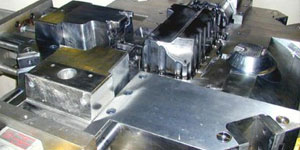
ISO 9001: 2015 certified manufacturer of die cast magnesium, Capabilities include high-pressure magnesium die casting up to 200 ton hot chamber & 3000 ton cold chamber, tooling design, polishing, molding, machining, powder & liquid painting, full QA with CMM capabilities, assembly, packaging & delivery.
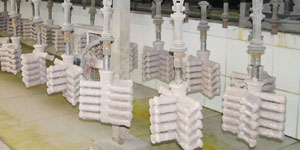
ITAF16949 certified. Additional Casting Service Include investment casting,sand casting,Gravity Casting, Lost Foam Casting,Centrifugal Casting,Vacuum Casting,Permanent Mold Casting,.Capabilities include EDI, engineering assistance, solid modeling and secondary processing.
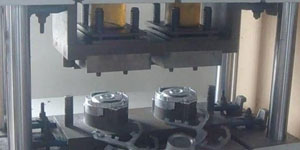
Casting Industries Parts Case Studies for: Cars, Bikes, Aircraft, Musical instruments, Watercraft, Optical devices, Sensors, Models, Electronic devices, Enclosures, Clocks, Machinery, Engines, Furniture, Jewelry, Jigs, Telecom, Lighting, Medical devices, Photographic devices, Robots, Sculptures, Sound equipment, Sporting equipment, Tooling, Toys and more.
What Can we help you do next?
∇ Go To Homepage For Die Casting China
→Casting Parts-Find out what we have done.
→Ralated Tips About Die Casting Services
By Minghe Die Casting Manufacturer |Categories: Helpful Articles |Material Tags: Aluminum Casting, Zinc Casting, Magnesium Casting, Titanium Casting, Stainless Steel Casting, Brass Casting,Bronze Casting,Casting Video,Company History,Aluminum Die Casting |Comments Off