How to improve the casting process measures of the spheroidization rate
The spheroidization level of domestic ordinary spheroidal graphite cast iron castings is required to reach level 4 or above, (that is, the spheroidization rate is 70%), the spheroidization rate achieved by the general foundry is about 85%. In recent years, with the development of nodular cast iron production, especially in industries with high requirements for wind power casting production and casting quality, the spheroidization level is required to reach level 2, that is, the spheroidization rate reaches more than 90%. The author's company analyzed and improved the spheroidization and inoculation process used in QT400-15, as well as the spheroidizing agent and inoculant, so that the spheroidization rate of nodular cast iron reached more than 90%.
1. The original production process
Original production process:
- The smelting equipment adopts 2.0T intermediate frequency furnace and 1.5T industrial frequency furnace;
- The composition of QT400-15 raw iron liquid is ω(C)=3.75%~3.95%, ω(Si)=1.4%~1.7%, ω(Mn)≤0.40%, ω(P)≤0.07%, ω(S) ) ≤0.035%;
- The spheroidizing agent used in the spheroidizing treatment is 1.3% to 1.5% RE3Mg8SiFe alloy;
- The inoculant used in the inoculation treatment is 0.7%~0.9% 75SiFe-C alloy. The spheroidizing treatment adopts two tapping and flushing methods:
First, 55%~60% of iron is produced, then spheroidizing is carried out, then inoculant is added, and then the rest of the iron liquid is added.
Due to the traditional method of spheroidization and inoculation, the spheroidization rate detected by a single cast wedge test block with a thickness of 25 mm is generally around 80%, that is, the spheroidization level is 3rd.
2. Test plan to improve the spheroidization rate
In order to increase the spheroidization rate, the original spheroidization and inoculation process has been improved. The main measures are: increasing the amount of spheroidizing agent and inoculant, purifying molten iron, and desulfurizing treatment. The spheroidization rate is still tested with a single cast wedge test block of 25 mm. The specific plan is as follows:
- (1) Analyze the reason for the low spheroidization rate of the original process. It was thought that the amount of spheroidizing agent was small, so the amount of spheroidizing agent added was increased from 1.3% to 1.4% to 1.7%, but the spheroidizing rate did not meet the requirements. . (2) Another guess is that the low spheroidization rate may be caused by poor gestation or fertility decline. Therefore, the experiment increased the inoculation dose from 0.7% to 0.9% to 1.1%, and the spheroidization rate did not meet the requirements.
- (3) Continue to analyze and believe that there are more inclusions in molten iron and high spheroidization interference elements may be the cause of the low spheroidization rate. Therefore, high-temperature purification of molten iron is carried out. The high-temperature purification temperature is generally controlled at 1500±10°C, but Its spheroidization rate has not exceeded 90%.
- (4) The high amount of ω(S) seriously consumes the spheroidizing dose and accelerates the decline of spheroidization. Therefore, the desulfurization treatment is increased to reduce the original iron liquid ω(S) amount from 0.035% to less than 0.020%, but the spheroidization rate is also Only reached 86%. The test results of the above four schemes are shown in Table 1. The structure and mechanical properties of the wedge-shaped test block did not meet the requirements.
3. The last improvement plan adopted
3.1 Specific improvement measures
- The raw materials are pig iron, rustless or less rusty scrap and reheating materials;
- Desulfurization of raw molten iron by adding soda ash (Na2CO3) to the furnace;
- Use Foseco 390 pretreatment agent to pre-deoxidize in the bag;
- Spheroidizing treatment with Fozco Nodulizer;
- Using silicon carbide and ferrosilicon combined inoculation.
The original molten iron composition control of the new process: ω (C) = (3.70% ~ 3.90%, ω (Si) = 0.80% ~ 1.20% [casting ω (Si final) = 2.60% ~ 3.00%], ω (Mn) ≤ 0.30%, ω(P)≤0.05%, ω(S)≤0.02%. When the original molten iron ω(S) exceeds 0.02%, industrial soda ash is used for desulfurization in front of the furnace, because the desulfurization reaction is an endothermic reaction , The desulfurization temperature is required to be controlled at around 1500°C, and the amount of soda ash added is controlled at 1.5% ~ 2.5% according to the amount of ω (S) during melting in the furnace.
At the same time, the spheroidizing treatment package adopts an ordinary dam type treatment package. First, add 1.7% of Foseco NODALLOY7RE brand spheroidizing agent to the side of the dam at the bottom of the package, flatten and compact, and use 0.2% powdered silicon carbide and 0.3% small The bulk 75SiFe is covered with one layer one after another, and after tamping, it is covered with a pressure iron, and 0.3% Foseke 390 inoculant is added to the other side of the molten iron ladle. When tapping iron, 55%~60% of the total molten iron volume is first flushed. After the spheroidizing reaction is completed, 1.2% 75SiFe-C inoculant is added and the remaining molten iron is flushed, and the slag is poured.
3.2 Test results
The composition of the original molten iron before and after desulfurization, the mechanical properties and metallographic structure of the 25mm single cast wedge-shaped test block, and the evaluation method of the spheroidization rate in the metallographic structure are automatically detected by the metallographic image analysis system.
4. Result analysis
4.1 The influence of main elements on the spheroidization rate
- C, Si: C can promote graphitization and reduce the tendency of white mouth, but a high amount of ω (C) will make the CE too high and easily cause graphite to float, generally controlled at 3.7%~3.9%. Si can strengthen graphitization ability and eliminate cementite. When Si is added as an inoculant, it can greatly reduce the supercooling ability of molten iron.In order to improve the inoculation effect, the amount of ω (Si) in the original molten iron was reduced from 1.3% to 1.5% to 0.8% to 1.2%, and the amount of ω (final Si) was controlled at 2.60% to 3.00%.
- Mn: During the crystallization process, Mn increases the tendency of cast iron to overcool and promotes the formation of carbides (FeMn) 3C. In the eutectoid transformation process, Mn reduces the eutectoid transformation temperature, stabilizes and refines pearlite. Mn does not have much influence on the spheroidization rate. Due to the influence of raw materials, generally control ω(Mn)<0.30%.
- P: When ω(P)<0.05%, it is solid-soluble in Fe, and it is difficult to form a phosphorus eutectic, which has little effect on the spheroidization rate of ductile iron.
- S: S is a despheroidizing element. S consumes Mg and RE in the spheroidizing agent during the spheroidizing reaction, hindering graphitization and reducing the spheroidizing rate. Sulfide slag will also return to sulfur before the molten iron solidifies, again consuming spheroidizing elements, accelerating the decline of spheroidization, and further affecting the spheroidizing rate. In order to achieve a high spheroidization rate, the amount of ω(S) in the raw iron should be reduced to less than 0.02%.
4.2 Desulfurization treatment
After the charge is melted, take samples and analyze the chemical composition. When the amount of ω (S) is higher than 0.02%, desulfurization is required.
The principle of soda ash desulfurization is: put a certain amount of soda ash in the ladle, use molten iron flow to flush and stir, soda ash decomposes at high temperature, the reaction formula is Na2CO3=Na2O+CO2↑: the generated Na2O is in the molten iron again Sulfuration and formation of Na2S, (Na2O) + [FeS] = (Na2S) + (FeO).
Na2CO3 separates and resolves CO2, causing violent agitation of molten iron, which promotes the desulfurization process. Soda ash slag is easy to flow and float quickly, and the desulfurization reaction time is very short. After desulfurization, the slag should be removed in time, otherwise it will return to sulfur. 4.3 Pre-deoxidation treatment, spheroidization treatment and inoculation treatment Foseke 390 pretreatment agent plays the role of pre-deoxidation treatment in the bag, and at the same time increases the graphite nucleation core and the number of graphite spheres per unit area, and can also increase the absorption rate of Mg. Significantly improve the ability to resist recession and increase the spheroidization rate. Fochke inoculant contains ω (Si) = 60% ~ 70%, ω (Ca) = 0.4% ~ 2.0%, ω (Ba) = 7% ~ 11%, of which Ba can extend the effective incubation time. The NODALLOY7RE grade of Fozco Nodulizer is selected, and its ω(Si)=40%~50%, ω(Mg)=7.0%~8.0%, ω(RE)=0.3%~1.0%, ω(Ca)=1.5 %~2.5%, ω(Al)<1.0%. Since the molten iron undergoes desulfurization and pre-deoxidation treatments, the elements that consume nodulizers in the molten iron are greatly reduced, so a nodulizer with a low amount of ω (RE) is selected to reduce the deterioration of the spheroidal graphite morphology by RE; The main element of action is Mg; Ca and Al can play a role in strengthening the incubation. Using silicon carbide and ferrosilicon combined inoculation treatment, the melting point of silicon carbide is about 1600°C, and graphite crystal nucleus is increased during solidification, and large doses of ferrosilicon are used for inoculation, which can prevent spheroidization from declining.
5 Conclusion
In the production of ferritic nodular cast iron, when the spheroidization rate is required to reach more than 90%, the following measures can be adopted:
- (1) Choose high-quality charge to reduce the de-spheroidization elements in the charge.
- (2) Choose a spheroidizing agent with a low amount of ω (RE) to reduce the deteriorating effect of RE on the morphology of spheroidal graphite.
- (3) The ω (S) content of the original molten iron should be less than 0.020%, which can reduce the consumption of nodulizers, especially the nodulized elements consumed by the secondary sulfurization of the sulfide slag.
- (4) Pre-deoxidize the molten iron, increase the number of graphite spheres per unit area, increase the spheroidization rate, greatly improve the ability to resist recession, and extend the effective incubation time.
- (5) Reduce the amount of ω (Si) in the original molten iron, increase the amount of spheroidizing agent, inoculant and various pretreatment agents, and strengthen the inoculation treatment.
Please keep the source and address of this article for reprinting: How to improve the casting process measures of the spheroidization rate
Minghe Die Casting Company are dedicated to manufacture and provide quality and high performance Casting Parts(metal die casting parts range mainly include Thin-Wall Die Casting,Hot Chamber Die Casting,Cold Chamber Die Casting),Round Service(Die Casting Service,Cnc Machining,Mold Making,Surface Treatment).Any custom Aluminum die casting, magnesium or Zamak/zinc die casting and other castings requirements are welcome to contact us.
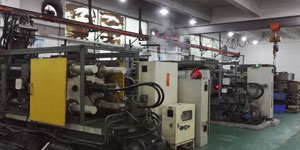
Under the control of ISO9001 and TS 16949,All processes are carried out through hundreds of advanced die casting machines, 5-axis machines, and other facilities, ranging from blasters to Ultra Sonic washing machines.Minghe not only has advanced equipment but also have professional team of experienced engineers,operators and inspectors to make the customer’s design come true.
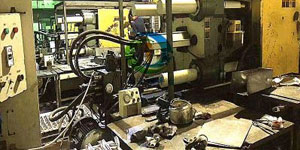
Contract manufacturer of die castings. Capabilities include cold chamber aluminum die casting parts from 0.15 lbs. to 6 lbs., quick change set up, and machining. Value-added services include polishing, vibrating, deburring, shot blasting, painting, plating, coating, assembly, and tooling. Materials worked with include alloys such as 360, 380, 383, and 413.
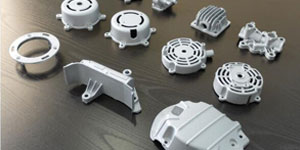
Zinc die casting design assistance/concurrent engineering services. Custom manufacturer of precision zinc die castings. Miniature castings, high pressure die castings, multi-slide mold castings, conventional mold castings, unit die and independent die castings and cavity sealed castings can be manufactured. Castings can be manufactured in lengths and widths up to 24 in. in +/-0.0005 in. tolerance.
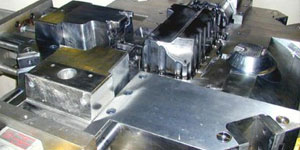
ISO 9001: 2015 certified manufacturer of die cast magnesium, Capabilities include high-pressure magnesium die casting up to 200 ton hot chamber & 3000 ton cold chamber, tooling design, polishing, molding, machining, powder & liquid painting, full QA with CMM capabilities, assembly, packaging & delivery.
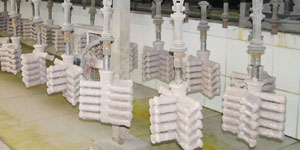
ITAF16949 certified. Additional Casting Service Include investment casting,sand casting,Gravity Casting, Lost Foam Casting,Centrifugal Casting,Vacuum Casting,Permanent Mold Casting,.Capabilities include EDI, engineering assistance, solid modeling and secondary processing.
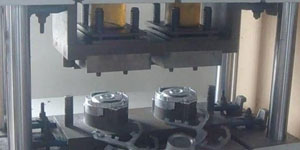
Casting Industries Parts Case Studies for: Cars, Bikes, Aircraft, Musical instruments, Watercraft, Optical devices, Sensors, Models, Electronic devices, Enclosures, Clocks, Machinery, Engines, Furniture, Jewelry, Jigs, Telecom, Lighting, Medical devices, Photographic devices, Robots, Sculptures, Sound equipment, Sporting equipment, Tooling, Toys and more.
What Can we help you do next?
∇ Go To Homepage For Die Casting China
→Casting Parts-Find out what we have done.
→Ralated Tips About Die Casting Services
By Minghe Die Casting Manufacturer |Categories: Helpful Articles |Material Tags: Aluminum Casting, Zinc Casting, Magnesium Casting, Titanium Casting, Stainless Steel Casting, Brass Casting,Bronze Casting,Casting Video,Company History,Aluminum Die Casting |Comments Off