How To Remove Mold Dents
Causes of dents
- The thickness of each part of the product is different
- Insufficient pressure inside the mold
- Insufficient mold cooling
- Deformation due to insufficient cooling time
Related knowledge
- In the process of producing products, dents are the most frequent occurrence of undesirable phenomena. The plastic injected into the mold shrinks in volume when it is cooled. The early cooling part, that is, the surface hardens first, and bubbles will be generated inside. The so-called dents are The slow cooling part produces a conspicuous concave surface in the direction of the bubble shrinkage.
- Materials with large shrinkage are also prone to dents. When changing the molding conditions to eliminate dents, the setting conditions should be set in the direction where the shrinkage is small. That is, the mold temperature and barrel temperature decrease, and the injection pressure increases, but it should be noted that this may cause residual internal stress.
- Because the dents are better to be inconspicuous, if they do not affect the appearance, they are deliberately processed into a corroded pattern on the mold, such as grains, grains, etc. Also, if the molding material is HIPS, it is also effective to lower the mold temperature to reduce the finish. However, once dents occur in these methods, it is difficult to repair polished products.
The Solution
- Instant: Increase injection pressure, extend injection holding time, reduce barrel temperature and mold temperature, and force cooling where dents are generated.
- Short-term: Fill up the flow edge where the dent is generated (Figure A). When there is a narrow place on the edge of the material where the dent is generated, make this part thick (Figure B).
- Long-term: The thickness difference of the designed product should be completely avoided. Reinforcing ribs that are prone to dents, the long and narrow shape should be as short as possible
The difference in materials
Materials with large molding shrinkage have large dents. For example, PE, PP, even if only a slight reinforcement ribs, will produce dents.
References
- When the temperature is lowered to the point that no dents are produced, if the material in the cavity is still under pressure, it should be considered that no dents will be produced. The pressure in the mold of the material surrounding the mold is the static pressure, which is not always the same everywhere. The pressure of the part close to the gate is high. If the material has a wide through edge, because of the transmission of pressure to each corner, the pressure difference between the part near the gate and the place far away from the gate is very small compared with the overall pressure, and no depression will occur. It is also possible to obtain products without residual internal stress. When part of the material flows into a difficult place, this place has high pressure, and the pressure in other places is reduced, which will cause dents. This part of the residual high pressure is the internal stress of the product. In an ideal state, the material temperature rises with the mold temperature, the material fluidity is better, and the injection becomes bottom in the static pressure state.
- When changing the molding conditions, the combination of temperature, pressure, and time should be prepared in advance, and the results can be known early by proceeding in order. First of all, after the time has become very long, it is easy to know every small change in pressure. It should be noted that the result when the temperature changes is obtained, and the result should be the result when the temperature drops after the injection of the material.
Please keep the source and address of this article for reprinting: How To Remove Mold Dents
Minghe Die Casting Company are dedicated to manufacture and provide quality and high performance Casting Parts(metal die casting parts range mainly include Thin-Wall Die Casting,Hot Chamber Die Casting,Cold Chamber Die Casting),Round Service(Die Casting Service,Cnc Machining,Mold Making,Surface Treatment).Any custom Aluminum die casting, magnesium or Zamak/zinc die casting and other castings requirements are welcome to contact us.
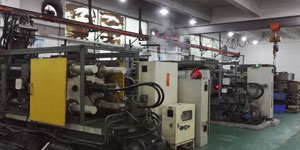
Under the control of ISO9001 and TS 16949,All processes are carried out through hundreds of advanced die casting machines, 5-axis machines, and other facilities, ranging from blasters to Ultra Sonic washing machines.Minghe not only has advanced equipment but also have professional team of experienced engineers,operators and inspectors to make the customer’s design come true.
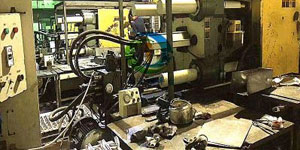
Contract manufacturer of die castings. Capabilities include cold chamber aluminum die casting parts from 0.15 lbs. to 6 lbs., quick change set up, and machining. Value-added services include polishing, vibrating, deburring, shot blasting, painting, plating, coating, assembly, and tooling. Materials worked with include alloys such as 360, 380, 383, and 413.
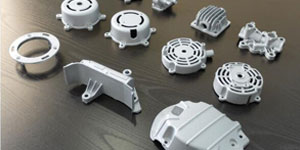
Zinc die casting design assistance/concurrent engineering services. Custom manufacturer of precision zinc die castings. Miniature castings, high pressure die castings, multi-slide mold castings, conventional mold castings, unit die and independent die castings and cavity sealed castings can be manufactured. Castings can be manufactured in lengths and widths up to 24 in. in +/-0.0005 in. tolerance.
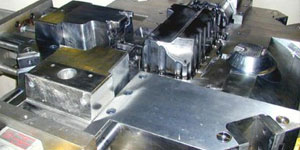
ISO 9001: 2015 certified manufacturer of die cast magnesium, Capabilities include high-pressure magnesium die casting up to 200 ton hot chamber & 3000 ton cold chamber, tooling design, polishing, molding, machining, powder & liquid painting, full QA with CMM capabilities, assembly, packaging & delivery.
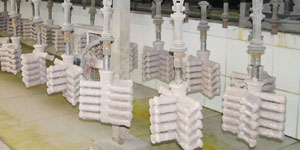
ITAF16949 certified. Additional Casting Service Include investment casting,sand casting,Gravity Casting, Lost Foam Casting,Centrifugal Casting,Vacuum Casting,Permanent Mold Casting,.Capabilities include EDI, engineering assistance, solid modeling and secondary processing.
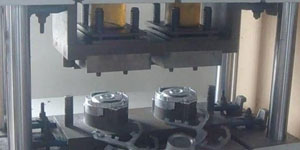
Casting Industries Parts Case Studies for: Cars, Bikes, Aircraft, Musical instruments, Watercraft, Optical devices, Sensors, Models, Electronic devices, Enclosures, Clocks, Machinery, Engines, Furniture, Jewelry, Jigs, Telecom, Lighting, Medical devices, Photographic devices, Robots, Sculptures, Sound equipment, Sporting equipment, Tooling, Toys and more.
What Can we help you do next?
∇ Go To Homepage For Die Casting China
→Casting Parts-Find out what we have done.
→Ralated Tips About Die Casting Services
By Minghe Die Casting Manufacturer |Categories: Helpful Articles |Material Tags: Aluminum Casting, Zinc Casting, Magnesium Casting, Titanium Casting, Stainless Steel Casting, Brass Casting,Bronze Casting,Casting Video,Company History,Aluminum Die Casting |Comments Off