Improvement and optimization of ultra-low carbon martensitic stainless steel smelting process
Ultra-low carbon martensitic stainless steel (06Cr13Ni46Mo and 06Cr16Ni46Mo) is an important material usually used for the upper crown, lower ring, blades and guide vanes of important parts of hydraulic turbines. This series of stainless steel materials are difficult in smelting technology and have high requirements for product quality. Especially when manufacturing the Three Gorges hydropower unit, the three major domestic hydropower equipment manufacturing companies have established domestic hydropower manufacturing technologies and standards by introducing domestic and foreign hydropower manufacturing technologies and standards. The Three Gorges standard for key components of hydropower equipment (the material requirements involved in this standard represent the highest level in the domestic industry). The composition requirements of molten steel are: ω(C)≤0.05%, ω(P)≤0.028%, ω(S) ≤0.015%, ω(Si)≤1.00%, ω(Mn)≤1.00%, ω(Cr)≥12.45%, ω(Ni)=3.5~4.5%, ω(Mo)=0.40~1.00%, ω( O)≤80×10-6, ω(N)≤150×10-6, ω(H)≤3×10-6.
In order to produce high-quality stainless steel castings, domestic and foreign manufacturers mainly use electric arc furnace + refining (AOD, VOD, LF, etc.) for production. Among them, the use of AOD to smelt stainless steel has become the leading technology for stainless steel refining. At present, when domestic and foreign manufacturers produce this series of stainless steel materials, cracks are more likely to occur during production and subsequent processing, and cracks occasionally occur during use. Therefore, in order to improve the quality of this series of material castings, it is necessary to improve the overall performance of the castings by improving the inherent quality of molten steel.
The technical personnel of MINGHE Group have addressed the problems of long decarburization time, large oxygen consumption, high bath temperature, and long high temperature residence time in the company's original stainless steel smelting process. Through process improvement and the use of AOD refining furnace, the quality of molten steel has been improved.
As we all know, the key to oxygen blowing and decarburization is to control the reaction of oxygen in molten steel with carbon, chromium, silicon, manganese and other elements. Based on the principle of steel metallurgy, combined with the use of AOD, technicians have improved and optimized the main etching process parameters of the original stainless steel smelting.
The AOD method uses argon and oxygen gas to blow molten steel into the molten pool from the side of the furnace bottom in the form of mixed gas. During the blowing process, the partial pressure of CO is diluted by argon and is reduced, which greatly facilitates the decarburization and chromium preservation of stainless steel during smelting. In the reduction stage of AOD refining, due to the addition of ferrosilicon and limestone slag for deoxidation, and the intense stirring of argon, the molten steel can be deeply desulfurized; the intense stirring of argon during the AOD refining can promote the separation of oxides in the molten steel, Ascending, the cleanliness of the molten steel is improved, so the content of inclusions in the molten steel is small, and there are almost no large-particle inclusions. The main form of inclusions has also changed from electric furnace manganese silicate to calcium silicate.
In addition, the AOD method can also remove lead from steel during the blowing process. Studies have shown that a certain amount of lead in stainless steel will affect its hot workability, but after AOD blowing, the ω (Pb) in the finished steel is less than 10×10-6, which will not affect the performance of the steel at all.
Through process improvement and the use of AOD, high-quality molten steel is obtained. Using Si-Ca and Si-Fe composite deoxidation, molten steel ω(O) is reduced to 80×10-6; activated lime is used to strengthen desulfurization, so that ω(S ) Is reduced to less than 0.015%, which greatly improves the cleanliness of molten steel, and meets the requirements of melting composition and various physical and chemical indicators; the content of harmful gas components and spherical oxide inclusions in molten steel (the spherical oxide rating does not exceed 2.0) is greatly reduced ; The improvement of the purity of molten steel enhances the ability of the casting matrix to resist cracks
Please keep the source and address of this article for reprinting: Improvement and optimization of ultra-low carbon martensitic stainless steel smelting process
Minghe Die Casting Company are dedicated to manufacture and provide quality and high performance Casting Parts(metal die casting parts range mainly include Thin-Wall Die Casting,Hot Chamber Die Casting,Cold Chamber Die Casting),Round Service(Die Casting Service,Cnc Machining,Mold Making,Surface Treatment).Any custom Aluminum die casting, magnesium or Zamak/zinc die casting and other castings requirements are welcome to contact us.
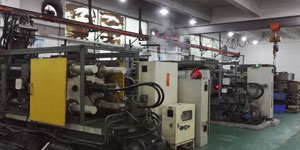
Under the control of ISO9001 and TS 16949,All processes are carried out through hundreds of advanced die casting machines, 5-axis machines, and other facilities, ranging from blasters to Ultra Sonic washing machines.Minghe not only has advanced equipment but also have professional team of experienced engineers,operators and inspectors to make the customer’s design come true.
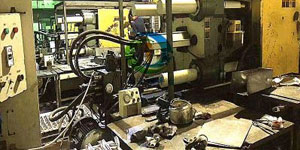
Contract manufacturer of die castings. Capabilities include cold chamber aluminum die casting parts from 0.15 lbs. to 6 lbs., quick change set up, and machining. Value-added services include polishing, vibrating, deburring, shot blasting, painting, plating, coating, assembly, and tooling. Materials worked with include alloys such as 360, 380, 383, and 413.
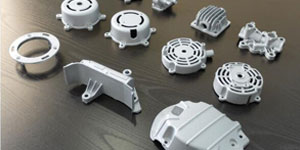
Zinc die casting design assistance/concurrent engineering services. Custom manufacturer of precision zinc die castings. Miniature castings, high pressure die castings, multi-slide mold castings, conventional mold castings, unit die and independent die castings and cavity sealed castings can be manufactured. Castings can be manufactured in lengths and widths up to 24 in. in +/-0.0005 in. tolerance.
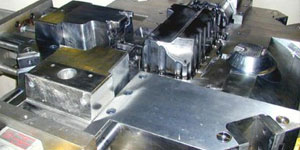
ISO 9001: 2015 certified manufacturer of die cast magnesium, Capabilities include high-pressure magnesium die casting up to 200 ton hot chamber & 3000 ton cold chamber, tooling design, polishing, molding, machining, powder & liquid painting, full QA with CMM capabilities, assembly, packaging & delivery.
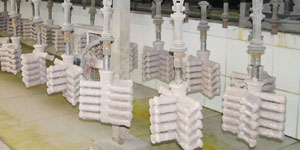
ITAF16949 certified. Additional Casting Service Include investment casting,sand casting,Gravity Casting, Lost Foam Casting,Centrifugal Casting,Vacuum Casting,Permanent Mold Casting,.Capabilities include EDI, engineering assistance, solid modeling and secondary processing.
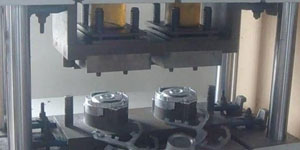
Casting Industries Parts Case Studies for: Cars, Bikes, Aircraft, Musical instruments, Watercraft, Optical devices, Sensors, Models, Electronic devices, Enclosures, Clocks, Machinery, Engines, Furniture, Jewelry, Jigs, Telecom, Lighting, Medical devices, Photographic devices, Robots, Sculptures, Sound equipment, Sporting equipment, Tooling, Toys and more.
What Can we help you do next?
∇ Go To Homepage For Die Casting China
→Casting Parts-Find out what we have done.
→Ralated Tips About Die Casting Services
By Minghe Die Casting Manufacturer |Categories: Helpful Articles |Material Tags: Aluminum Casting, Zinc Casting, Magnesium Casting, Titanium Casting, Stainless Steel Casting, Brass Casting,Bronze Casting,Casting Video,Company History,Aluminum Die Casting |Comments Off