Influence of the phase structure of converter dephosphorization slag on dephosphorization
Since the smelting of ultra-low phosphorus steels such as 9Ni has strict requirements for the final phosphorus content of the converter steelmaking, it is generally necessary to achieve a final phosphorus content of 40×10-6 in the converter. Therefore, Nangang takes pipeline steel as the research object and adopts In the double slag + slag smelting process, the phosphorus in the molten steel is mainly removed during the dephosphorization period (one pour).
The dephosphorization effect at the end of smelting is directly determined by the dephosphorization effect in the early stage of smelting. The change in the composition and phase structure of the slag during the entire smelting process of the converter reflects the melting status and slagging effect of the slag.
Scholars from University of Science and Technology Beijing used thermodynamic software Factsage6.4, SEM, EDS, XRD, combined with infrared and Raman experimental methods to analyze and study the phase structure of primary slag and terminal slag. The results showed that the viscosity of the first slag and the final slag decreased with the increase of temperature. At the same temperature, the viscosity of the first slag was higher, but the melting point was lower than that of the final slag.
There are more liquid phases formed at low temperature, which is more conducive to the progress of the dephosphorization reaction. The slag Si, Ca, P element enriched area, the main mineral phase formed is 2CaO•SiO2-3CaO•P2O5 solid solution phase, which is more beneficial to dephosphorization; while the Fe, Mn, Mg and O element enriched area is formed The main phases are iron oxide and RO phase, and the dephosphorization ability of slag is poor. Infrared and Raman analysis results show that both the first slag and the final slag form SiO4 tetrahedral units, the first slag is mainly composed of Si-O-Si bonds, and the final slag is mainly composed of P-O-P bonds. The more silicate network unit structure is, the more beneficial it is for dephosphorization.
Please keep the source and address of this article for reprinting: Influence of the phase structure of converter dephosphorization slag on dephosphorization
Minghe Die Casting Company are dedicated to manufacture and provide quality and high performance Casting Parts(metal die casting parts range mainly include Thin-Wall Die Casting,Hot Chamber Die Casting,Cold Chamber Die Casting),Round Service(Die Casting Service,Cnc Machining,Mold Making,Surface Treatment).Any custom Aluminum die casting, magnesium or Zamak/zinc die casting and other castings requirements are welcome to contact us.
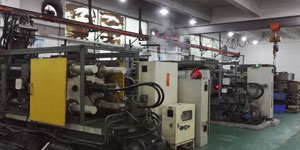
Under the control of ISO9001 and TS 16949,All processes are carried out through hundreds of advanced die casting machines, 5-axis machines, and other facilities, ranging from blasters to Ultra Sonic washing machines.Minghe not only has advanced equipment but also have professional team of experienced engineers,operators and inspectors to make the customer’s design come true.
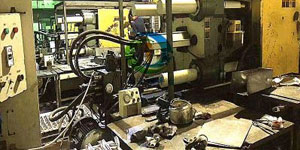
Contract manufacturer of die castings. Capabilities include cold chamber aluminum die casting parts from 0.15 lbs. to 6 lbs., quick change set up, and machining. Value-added services include polishing, vibrating, deburring, shot blasting, painting, plating, coating, assembly, and tooling. Materials worked with include alloys such as 360, 380, 383, and 413.
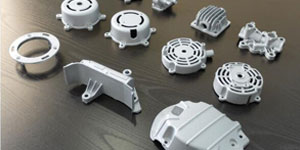
Zinc die casting design assistance/concurrent engineering services. Custom manufacturer of precision zinc die castings. Miniature castings, high pressure die castings, multi-slide mold castings, conventional mold castings, unit die and independent die castings and cavity sealed castings can be manufactured. Castings can be manufactured in lengths and widths up to 24 in. in +/-0.0005 in. tolerance.
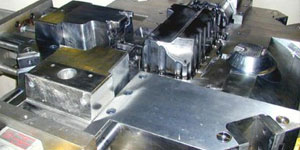
ISO 9001: 2015 certified manufacturer of die cast magnesium, Capabilities include high-pressure magnesium die casting up to 200 ton hot chamber & 3000 ton cold chamber, tooling design, polishing, molding, machining, powder & liquid painting, full QA with CMM capabilities, assembly, packaging & delivery.
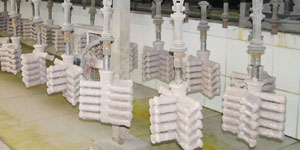
ITAF16949 certified. Additional Casting Service Include investment casting,sand casting,Gravity Casting, Lost Foam Casting,Centrifugal Casting,Vacuum Casting,Permanent Mold Casting,.Capabilities include EDI, engineering assistance, solid modeling and secondary processing.
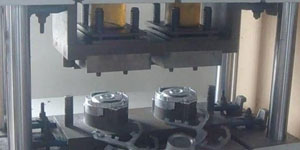
Casting Industries Parts Case Studies for: Cars, Bikes, Aircraft, Musical instruments, Watercraft, Optical devices, Sensors, Models, Electronic devices, Enclosures, Clocks, Machinery, Engines, Furniture, Jewelry, Jigs, Telecom, Lighting, Medical devices, Photographic devices, Robots, Sculptures, Sound equipment, Sporting equipment, Tooling, Toys and more.
What Can we help you do next?
∇ Go To Homepage For Die Casting China
→Casting Parts-Find out what we have done.
→Ralated Tips About Die Casting Services
By Minghe Die Casting Manufacturer |Categories: Helpful Articles |Material Tags: Aluminum Casting, Zinc Casting, Magnesium Casting, Titanium Casting, Stainless Steel Casting, Brass Casting,Bronze Casting,Casting Video,Company History,Aluminum Die Casting |Comments Off