Knowledge of using recarburizers in induction furnaces
1. Graphitization of unmelted particles in the recarburizer
In the molten iron, in addition to the carbon that has been dissolved in the molten iron, the recarburizer also has residual, undissolved carbon in the form of graphite, which is drawn into the stirred liquid stream in granular form. Most of the unmelted and coarse graphite particles are suspended on the surface of the molten iron near the furnace wall when energized, and some are attached to the middle of the furnace wall, which is equivalent to the dead corner of stirring. At this time, once the energization stops, these coarse graphite particles will be slowly suspended due to buoyancy. Very small particles beyond the observation range of the optical microscope can be suspended in the molten iron not only when the power is turned on, but also when the power is stopped during the melting of graphite.
According to reports, the closer to the material that constitutes the eutectic nucleus, even if the added graphite and eutectic graphite have a slightly different crystallinity, compared with other materials that can be inferred to form the graphite core, it is bound to have a greater degree of misfortune. From this point of view, it can be considered that the suspended fine graphite particles are conducive to the formation of graphite cores and can prevent the cast iron from overcooling and whitening.
2 The effect of the particle size of the recarburizer on the recarburization effect
2.1 The effect of the particle size of the recarburizer on the recarburization time
The particle size of the recarburizer is the main factor that affects the melting of the recarburizer into the molten iron. The A, B, and C recarburizers with roughly the same composition but different particle sizes in Table 1 were used for the recarburization effect test. The results are shown in Figure 1. Although the carburization rate after 15 minutes is the same, the carburization time to reach 90% carburization rate is quite different. It takes 13 minutes to use the C recarburizer without particle size treatment, 8 minutes to remove the fine powder A recarburizer, and only 6 minutes to remove the fine powder and coarse grain B recarburizer. This shows that the particle size of the recarburizer has a greater impact on the recarburization time, and it is not good to mix fine powder and coarse particles, especially when the content of fine powder is high.
2.2 The influence of the particle size of the recarburizer on the recarburizer
Japan’s Nakae and Mochizuki have tested the recarburizer with a mass fraction of 99.8% C and 0.023% S with a particle size distribution as shown in Table 2. The test results are shown in Figure 2. It can be seen from the figure that the recarburizing effect of the recarburizer E with a particle size biased toward fine powder is extremely poor, and the recarburizing effect of the recarburizer G with a coarser particle size is better; while the fine powder and coarse-grained recarburizers are properly removed A has the best carbon increasing effect.
The above facts prove that in order to improve the recarburization effect, the recarburizer should be processed to remove fine powder and coarse particles.
3 The influence of the chemical composition of molten iron on the recarburization effect of the recarburizer
3.1 The influence of silicon on the recarburization effect of recarburizers
The silicon in the molten iron has a great influence on the recarburization effect. Liquid iron with high silicon content is not good for carburization. Someone changed the mass fraction of Si in the molten iron in the range of 0.6% to 2.1%, and added two recarburizers A and B as shown in Table 1, and observed the difference in recarburization time after adding the recarburizer. The result is shown in Figure 3. When the mass fraction of Si in the molten iron is high, the carbon increase rate is slow.
3.2 The effect of sulfur on the recarburization effect of recarburizers
Just as the mass fraction of silicon in the molten iron affects the recarburization effect, the sulfur content also has a certain effect on the recarburization. Use the A recarburizer in Table 2, add the iron sulfide for the reagent before adding it, and observe the effect of the mass fraction of S on the recarburization. When iron sulfide is added and the mass fraction of S in the molten iron is 0.045%, comparing it with the low-sulfur iron liquid phase without the addition of iron sulfide and the mass fraction of S in the molten iron is 0.0014%, the carbon increase rate is much slower .
4 Recarburizer selection and adding method
4.1 Recarburizers with low nitrogen content should be selected
The mass fraction of nitrogen in molten cast iron is usually below 100 ppm. If the nitrogen content exceeds this concentration (150-200 ppm or higher), it is easy to cause cracks, shrinkage or porosity in the castings, and thick-walled castings are more likely to occur. This is caused by increasing the amount of recarburizer added when the proportion of scrap steel is increased. Coke-based recarburizers, especially pitch coke, contain a large amount of nitrogen. The mass fraction of nitrogen in electrode graphite is below 0.1% or a very small amount, while the mass fraction of pitch pyronitrogen is about 0.6%. If 2% of the recarburizer with a mass fraction of 0.6% nitrogen is added, this alone will increase the mass fraction of nitrogen by 120 ppm. A large amount of nitrogen is not only easy to produce casting defects, but also nitrogen can promote the densification of pearlite, hardening of ferrite, and a strong increase in strength.
4.2 How to add recarburizer
The stirring of molten iron can promote recarburization. Therefore, the medium frequency induction electric furnace with weak stirring power is much more difficult than the power frequency induction electric furnace with strong stirring power. Therefore, the medium frequency induction electric furnace has carbon increase and cannot keep up with the melting rate of the metal charge. Possibility.
Even with a power frequency induction furnace with strong stirring power, the recarburization operation cannot be ignored. This is because, from the principle diagram of the induction electric furnace smelting, it can be seen that there are agitating iron flows separated up and down in the induction electric furnace, and there are dead corners near the furnace wall at the boundary. The graphite masses staying and adhering to the furnace wall cannot be melted into the molten iron without excessive heating and long-term heat preservation of the molten iron. Excessive temperature rise and long-term heat preservation of molten iron will increase the degree of subcooling of the molten iron and increase the tendency of cast iron to turn white. In addition, for an intermediate frequency induction electric furnace that generates a strong induction current near the furnace wall, if molten iron is drilled between the graphite masses attached to the furnace wall, the drilled metal will be melted during the next furnace smelting, resulting in corrosion And damage the furnace wall. Therefore, when the proportion of scrap steel is high and there are many recarburizers added, more attention should be paid to adding recarburizers.
The addition time of the recarburizer cannot be ignored. If the recarburizer is added too early, it will easily adhere to the bottom of the furnace, and the recarburizer attached to the furnace wall will not be easily melted into the molten iron. On the contrary, if the addition time is too late, the opportunity to increase carbon will be lost, resulting in slow smelting and heating time. This not only delays the time of chemical composition analysis and adjustment, but also may cause harm due to excessive heating. Therefore, it is better to add the recarburizer little by little during the process of adding the metal charge.
Please keep the source and address of this article for reprinting: Knowledge of using recarburizers in induction furnaces
Minghe Die Casting Company are dedicated to manufacture and provide quality and high performance Casting Parts(metal die casting parts range mainly include Thin-Wall Die Casting,Hot Chamber Die Casting,Cold Chamber Die Casting),Round Service(Die Casting Service,Cnc Machining,Mold Making,Surface Treatment).Any custom Aluminum die casting, magnesium or Zamak/zinc die casting and other castings requirements are welcome to contact us.
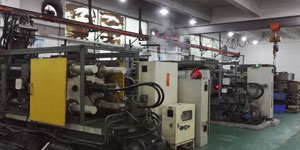
Under the control of ISO9001 and TS 16949,All processes are carried out through hundreds of advanced die casting machines, 5-axis machines, and other facilities, ranging from blasters to Ultra Sonic washing machines.Minghe not only has advanced equipment but also have professional team of experienced engineers,operators and inspectors to make the customer’s design come true.
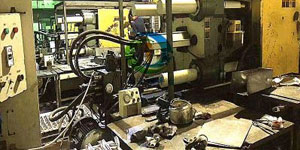
Contract manufacturer of die castings. Capabilities include cold chamber aluminum die casting parts from 0.15 lbs. to 6 lbs., quick change set up, and machining. Value-added services include polishing, vibrating, deburring, shot blasting, painting, plating, coating, assembly, and tooling. Materials worked with include alloys such as 360, 380, 383, and 413.
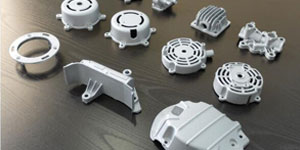
Zinc die casting design assistance/concurrent engineering services. Custom manufacturer of precision zinc die castings. Miniature castings, high pressure die castings, multi-slide mold castings, conventional mold castings, unit die and independent die castings and cavity sealed castings can be manufactured. Castings can be manufactured in lengths and widths up to 24 in. in +/-0.0005 in. tolerance.
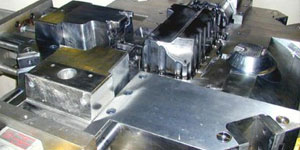
ISO 9001: 2015 certified manufacturer of die cast magnesium, Capabilities include high-pressure magnesium die casting up to 200 ton hot chamber & 3000 ton cold chamber, tooling design, polishing, molding, machining, powder & liquid painting, full QA with CMM capabilities, assembly, packaging & delivery.
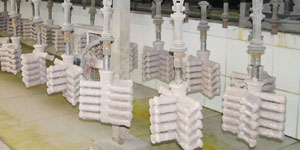
ITAF16949 certified. Additional Casting Service Include investment casting,sand casting,Gravity Casting, Lost Foam Casting,Centrifugal Casting,Vacuum Casting,Permanent Mold Casting,.Capabilities include EDI, engineering assistance, solid modeling and secondary processing.
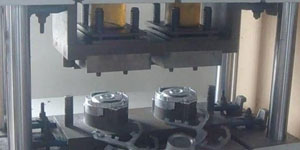
Casting Industries Parts Case Studies for: Cars, Bikes, Aircraft, Musical instruments, Watercraft, Optical devices, Sensors, Models, Electronic devices, Enclosures, Clocks, Machinery, Engines, Furniture, Jewelry, Jigs, Telecom, Lighting, Medical devices, Photographic devices, Robots, Sculptures, Sound equipment, Sporting equipment, Tooling, Toys and more.
What Can we help you do next?
∇ Go To Homepage For Die Casting China
→Casting Parts-Find out what we have done.
→Ralated Tips About Die Casting Services
By Minghe Die Casting Manufacturer |Categories: Helpful Articles |Material Tags: Aluminum Casting, Zinc Casting, Magnesium Casting, Titanium Casting, Stainless Steel Casting, Brass Casting,Bronze Casting,Casting Video,Company History,Aluminum Die Casting |Comments Off