Laser-Arc Hybrid Welding Technology For Ship Use Steel
Welding production efficiency and welding quality directly affect the production cycle, cost and hull quality of ship processing and manufacturing, so welding technology has become a key technology in ship processing and manufacturing and the development of the shipbuilding industry. Compared with traditional welding methods, laser welding has many advantages such as high efficiency, cleanliness, narrow heat-affected zone, and small joint deformation. This is because the laser beam energy density is extremely high, the power density is 106~108W/cm2, the aspect ratio is large, and it has a good welding effect on difficult-to-weld materials such as high melting point metals; at the same time, the laser welding speed is fast and the heat input is small. , So that the heat-affected zone is small, material deformation and residual stress are small. However, laser welding applications also have certain limitations, which are mainly manifested in high welding costs and low energy conversion efficiency. This situation has promoted the development of laser-arc hybrid welding technology.
Laser-arc hybrid welding combines the advantages of the two independent heat sources of laser and arc: laser heat source has high energy density, while arc plasma has high heat-electric conversion efficiency, low equipment cost and operating cost; To a large extent, the shortcomings of the two are avoided, such as the laser energy loss caused by the high reflectivity of the metal material to the laser, the lower energy density of the arc heat source, and the poor discharge stability during high-speed movement. The organic combination of the two forms its outstanding advantages: high energy density, high energy utilization, high arc stability, etc., making it a new welding technology with great application prospects.
The basic principle of laser-arc hybrid welding is: during the welding process, the laser beam and the arc act on the same position on the metal surface at the same time. The photo-induced plasma cloud generated by the laser action will reduce the laser energy utilization rate. After the arc is added, the arc plasma will cause The laser-induced plasma dilution improves the efficiency of laser energy transmission; at the same time, the arc increases the temperature of the base material, and the absorption rate of the base material to the laser is also improved. At the same time, the laser melting metal provides free electrons for the arc, which reduces the resistance of the arc channel, so that the energy utilization rate of the arc is also improved, thereby increasing the total energy utilization rate. The laser beam also has a focusing and guiding effect on the arc, which makes the arc more stable during the welding process.
A large number of test results show that under the same welding specification, compared with traditional single heat source welding, laser-arc hybrid welding can significantly increase the penetration depth. Since the same effect can be obtained at a smaller laser power, it is reduced to a certain extent. Cost. Laser-arc hybrid welding can also reduce the occurrence of welding defects such as pores, cracks, and undercuts, improve the wettability of molten metal and solid base metal, eliminate weld undercuts, and reduce the processing and assembly labor of welds. Improve production efficiency.
It is particularly worth pointing out that welding deformation is one of the main problems that need to be solved in the shipbuilding industry. In the hull manufacturing process, welding man-hours and welding costs account for a large part of the total man-hours and total cost of hull construction, and the cost increase caused by welding deformation accounts for a considerable proportion. Laser-arc hybrid welding has a very small amount of deformation, and the post-welding trimming workload is greatly reduced, which further reduces the cost of shipbuilding, saves time and improves efficiency. At present, some shipyards in Europe, America and Japan have adopted laser-arc hybrid welding technology. For example, the Meyer shipyard in Germany has all adopted laser-arc hybrid welding for ships. Studies have confirmed that the welding speed of steel plates with a thickness of less than 15 mm and a length of less than 20 meters can reach 3 meters per minute.
Please keep the source and address of this article for reprinting: Laser-Arc Hybrid Welding Technology For Ship Use Steel
Minghe Die Casting Company are dedicated to manufacture and provide quality and high performance Casting Parts(metal die casting parts range mainly include Thin-Wall Die Casting,Hot Chamber Die Casting,Cold Chamber Die Casting),Round Service(Die Casting Service,Cnc Machining,Mold Making,Surface Treatment).Any custom Aluminum die casting, magnesium or Zamak/zinc die casting and other castings requirements are welcome to contact us.
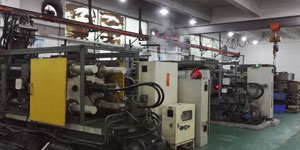
Under the control of ISO9001 and TS 16949,All processes are carried out through hundreds of advanced die casting machines, 5-axis machines, and other facilities, ranging from blasters to Ultra Sonic washing machines.Minghe not only has advanced equipment but also have professional team of experienced engineers,operators and inspectors to make the customer’s design come true.
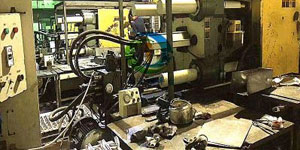
Contract manufacturer of die castings. Capabilities include cold chamber aluminum die casting parts from 0.15 lbs. to 6 lbs., quick change set up, and machining. Value-added services include polishing, vibrating, deburring, shot blasting, painting, plating, coating, assembly, and tooling. Materials worked with include alloys such as 360, 380, 383, and 413.
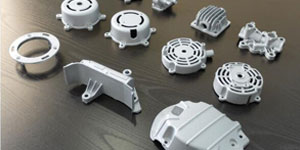
Zinc die casting design assistance/concurrent engineering services. Custom manufacturer of precision zinc die castings. Miniature castings, high pressure die castings, multi-slide mold castings, conventional mold castings, unit die and independent die castings and cavity sealed castings can be manufactured. Castings can be manufactured in lengths and widths up to 24 in. in +/-0.0005 in. tolerance.
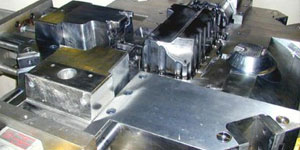
ISO 9001: 2015 certified manufacturer of die cast magnesium, Capabilities include high-pressure magnesium die casting up to 200 ton hot chamber & 3000 ton cold chamber, tooling design, polishing, molding, machining, powder & liquid painting, full QA with CMM capabilities, assembly, packaging & delivery.
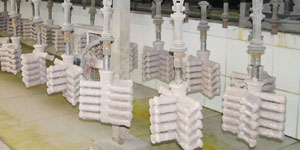
ITAF16949 certified. Additional Casting Service Include investment casting,sand casting,Gravity Casting, Lost Foam Casting,Centrifugal Casting,Vacuum Casting,Permanent Mold Casting,.Capabilities include EDI, engineering assistance, solid modeling and secondary processing.
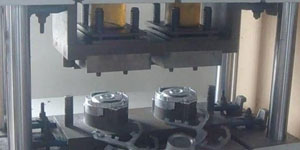
Casting Industries Parts Case Studies for: Cars, Bikes, Aircraft, Musical instruments, Watercraft, Optical devices, Sensors, Models, Electronic devices, Enclosures, Clocks, Machinery, Engines, Furniture, Jewelry, Jigs, Telecom, Lighting, Medical devices, Photographic devices, Robots, Sculptures, Sound equipment, Sporting equipment, Tooling, Toys and more.
What Can we help you do next?
∇ Go To Homepage For Die Casting China
→Casting Parts-Find out what we have done.
→Ralated Tips About Die Casting Services
By Minghe Die Casting Manufacturer |Categories: Helpful Articles |Material Tags: Aluminum Casting, Zinc Casting, Magnesium Casting, Titanium Casting, Stainless Steel Casting, Brass Casting,Bronze Casting,Casting Video,Company History,Aluminum Die Casting |Comments Off