Low Pressure Casting Technology for Aluminum Alloy Cylinder Head of Passenger Car Engine
Based on the comprehensive consideration of cost and mechanical properties, expanding the application of aluminum alloy is currently the main means of reducing the weight of passenger cars and reducing fuel consumption. For example, the engine cylinder head is now fully made of aluminum alloy. Although there are many production methods for aluminum alloy cylinder heads, the mainstream manufacturing processes are metal mold casting and low pressure casting. Among them, Europe and China mainly use metal molds, while Japan and the United States use low pressure casting more.
Compared with gravity metal mold casting, low pressure casting has the advantages of good forming quality and high process yield due to filling and crystal solidification under pressure, but for cylinder head castings with complex shapes and high performance requirements, there are complex processes , Control requires advanced technical difficulties. Therefore, this article focuses on the low-pressure casting technology of aluminum alloy cylinder heads and the key points of parameter control, in order to give full play to the technical advantages of the low-pressure casting process and produce high-quality cylinder head castings.
The key points of the low pressure casting process of the cylinder head
2.1 Example of gating system
The low-pressure casting process plan of the cylinder head is generally in the form of a riser pipe and multiple gates, which is a form of multi-weight splitting. For example, the four-cylinder cylinder head has two representative gating systems, namely, two or four gates are set on the side of the combustion chamber. Figure 2 is a schematic diagram of the process of two gates. This scheme is suitable for one mold or two molds.
2.2 Alloy materials and melting
The material of aluminum alloy cylinder head generally chooses AI-Si-Cu series alloys such as ZL105 and 107. If elongation and corrosion resistance are required, ZL101 and ZL104 can also be used. In order to obtain high-quality molten metal, the standard operation should use Ar gas rotating blowing refining and adding Sr to modify and AJ-Ti-B to refine the grains.
2.3 Pouring process
2.3.1 Mold maintenance
Regular cleaning and maintenance of the mold is very important for the stable production of high-quality cylinder head castings and prolonging the service life of the mold. Generally, mold maintenance should be carried out after every 500-700 pieces are produced. The main content is to disassemble the mold, clean the surface coating of the cavity with a soft brush, and remove aluminum chips and coating particles that penetrate into the gap between the ejector rod and the exhaust hole. , To ensure the quality of casting shape, smooth ejection and smooth exhaust.
2.3.2 Coating
Before pouring, the mold is preheated to about 200℃ and sprayed with paint. The shape of the cylinder head is complicated, so special attention should be paid to the different thickness of the paint in different parts. The coating thickness of general parts is controlled within 0.1---0.2mm: the precision requirements are high. For example, the surface of the combustion chamber should be coated with fine particles with a thickness of O.OSmn. For gates, risers, inner runners and other locations that need to be slowly solidified, it can be thicker, generally about 0.5-1 mm.
2.3.3 Filter
The purpose of placing the filter is to prevent the oxide impurities in the riser tube from entering the cavity and forming laminar filling. Can be used cheap and effective galvanized metal mesh, the diameter of the wire is .4--0.6mm, 1214 mesh.
2.3.4 Temperature
The temperature of the molten aluminum has a great influence on the internal defects of the cylinder head and the appearance quality. The pouring degree should be within the range of 680-730, and the temperature deviation in actual operation should be controlled within 20°C.
The characteristic of low-pressure casting is to obtain good sequential solidification. After this, it is important to control the temperature of the report to be moderate in the low-pressure casting. The ideal mold temperature distribution is gradually reduced from the gate to the upper mold, and the specific surface control range of each part is modified to obtain. The above-mentioned temperature field and the improvement of the performance of the cylinder head castings and shorten the production cycle must be enforced on the upper mold and the side mold. cool down. Generally divided into water-cooled and air-cooled, using multi-channel settings, each channel is independently automatically controlled (flow and pressure). The water cooling adopts a pressure-feeding water pump to solve the problem of poor water flow caused by high-temperature vaporization inside the mold, and compressed air is used for air cooling.
Because the cylinder head has multiple gates, the short distance between the two gates will cause the temperature of the casting part between the gates to rise, and the solidification sequence of the gate and this part will be reversed. Therefore, local forced cooling must be set in this part to obtain the required temperature gradient.
Considering mold life and safety, indirect cooling should be the main method of cooling, and direct cooling can be used where the thickness of local castings is large. There are two methods for cooling intensity: time control and temperature control. Time control is to control the time of passing water or air. This method is simple and easy to implement, but the accuracy is not high. Temperature control is to set up a thermocouple at the cooling position, and the PC will turn on or off the cooling water or air according to the temperature measured by the thermocouple. The control accuracy is relatively high.
In recent years, the development of solidification numerical simulation technology has provided a good reference for the optimization of the low-pressure casting process of cylinder heads. It can fully grasp the solidification test results under different conditions, strengthen the control of the casting process, and ensure the quality of castings.
2.3.5 Pressurization time
The time from filling to solidification of the gate is called press time, which is greatly affected by temperature. Under stable production conditions, although the pressurization time varies with the weight of the cylinder head, it is generally controlled at 2-8min. From the perspective of improving production efficiency, methods such as one mold, two parts, two-stage pressurization, etc. can be used to shorten the time.
2.3.6 Mold release time
Like the pressurization time, it changes due to changes in temperature. When the time is short, the casting is easy to deform; when the time is too long, the casting is easy to get stuck in the mold and cannot be taken out. Therefore, it is generally controlled at about 1/3 of the pressurizing time. In order to increase the cooling rate of the casting, the side mold with low mold release resistance can be opened first when the mold is drawn, and the upper mold can be opened after cooling for a certain period of time.
2.3.7 Pressure curve
The pressurizing pressure directly affects the fluid filling performance and feeding effect of the molten metal, and the pressurizing curve is an important part of low-pressure casting process control. The pressurizing pressure can be calculated by the following formula:
P=γx(1+S/A) x ΔH x 10-2
In the above formula, P-pressure (MPa), γ-aluminum liquid specific gravity (2.4-2.5), ΔH-aluminum liquid rising height (m), S-lift pipe cross-sectional area (m2), A-cavity cross-sectional area ( m2)o
The feed pressure of the riser is generally about 0.005-0.01MPa. Although the effect of high pressure is good, if the pressure exceeds 0.01 Mpa, it will cause the paint to peel off, the aluminum liquid will block the mold vent and penetrate into the sand core. It is very necessary to discharge the gas generated by the combustion of the sand core in time during the pouring process, but because the sand core used in the cylinder head has a complex structure and the largest number, it is difficult to set a large number of vent holes in the mold. At this time, increasing the feeder pressure of the feeder to near the upper limit can effectively prevent the gas from being involved in the casting.
The change of the liquid level in the citrus cave affects the repeatability of the pressure curve, so the pressure in the citrus disaster should be automatically compensated. For cylinder head castings, sensors can be set to accurately control the zero point I81 of the pressure curve.
In addition, if the interval between the lower end of the riser pipe and the bottom of the orange crutch is too short, the solution will easily produce turbulent flow. Therefore, without affecting the use of the solution, the distance between the lower end of the riser pipe and the bottom of the orange pot is about 200mm.
Casting defects and countermeasures
Table 1 lists the common defects of low-pressure casting and the measures to be taken. For a complex part such as a cylinder head, the fluctuation of various parameters may affect the quality of the casting. Therefore, it is necessary to carry out detailed analysis and investigation on various aspects such as process plan, stencil design, casting process, etc. to clarify the various causes of defects, and take corresponding measures on this basis.
Conclusion
So far, aluminum alloy cylinder heads are one of the few limited auto parts suitable for low-pressure casting. Therefore, they give full play to the advantages of high production rate and good internal quality to expand the production and application of domestic low-pressure casting technology in aluminum alloy cylinder heads. To adapt to the rapid development of my country's car technology.
Please keep the source and address of this article for reprinting: Low Pressure Casting Technology for Aluminum Alloy Cylinder Head of Passenger Car Engine
Minghe Die Casting Company are dedicated to manufacture and provide quality and high performance Casting Parts(metal die casting parts range mainly include Thin-Wall Die Casting,Hot Chamber Die Casting,Cold Chamber Die Casting),Round Service(Die Casting Service,Cnc Machining,Mold Making,Surface Treatment).Any custom Aluminum die casting, magnesium or Zamak/zinc die casting and other castings requirements are welcome to contact us.
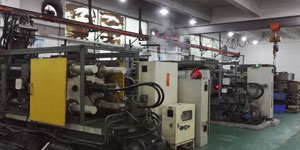
Under the control of ISO9001 and TS 16949,All processes are carried out through hundreds of advanced die casting machines, 5-axis machines, and other facilities, ranging from blasters to Ultra Sonic washing machines.Minghe not only has advanced equipment but also have professional team of experienced engineers,operators and inspectors to make the customer’s design come true.
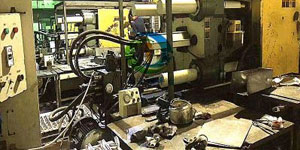
Contract manufacturer of die castings. Capabilities include cold chamber aluminum die casting parts from 0.15 lbs. to 6 lbs., quick change set up, and machining. Value-added services include polishing, vibrating, deburring, shot blasting, painting, plating, coating, assembly, and tooling. Materials worked with include alloys such as 360, 380, 383, and 413.
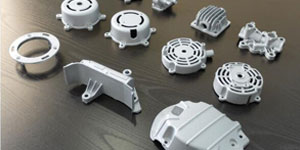
Zinc die casting design assistance/concurrent engineering services. Custom manufacturer of precision zinc die castings. Miniature castings, high pressure die castings, multi-slide mold castings, conventional mold castings, unit die and independent die castings and cavity sealed castings can be manufactured. Castings can be manufactured in lengths and widths up to 24 in. in +/-0.0005 in. tolerance.
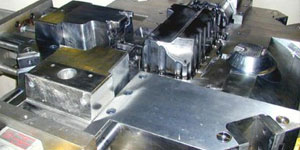
ISO 9001: 2015 certified manufacturer of die cast magnesium, Capabilities include high-pressure magnesium die casting up to 200 ton hot chamber & 3000 ton cold chamber, tooling design, polishing, molding, machining, powder & liquid painting, full QA with CMM capabilities, assembly, packaging & delivery.
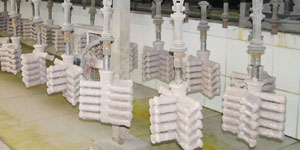
ITAF16949 certified. Additional Casting Service Include investment casting,sand casting,Gravity Casting, Lost Foam Casting,Centrifugal Casting,Vacuum Casting,Permanent Mold Casting,.Capabilities include EDI, engineering assistance, solid modeling and secondary processing.
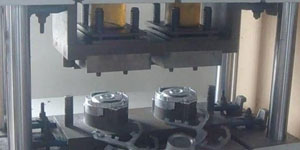
Casting Industries Parts Case Studies for: Cars, Bikes, Aircraft, Musical instruments, Watercraft, Optical devices, Sensors, Models, Electronic devices, Enclosures, Clocks, Machinery, Engines, Furniture, Jewelry, Jigs, Telecom, Lighting, Medical devices, Photographic devices, Robots, Sculptures, Sound equipment, Sporting equipment, Tooling, Toys and more.
What Can we help you do next?
∇ Go To Homepage For Die Casting China
→Casting Parts-Find out what we have done.
→Ralated Tips About Die Casting Services
By Minghe Die Casting Manufacturer |Categories: Helpful Articles |Material Tags: Aluminum Casting, Zinc Casting, Magnesium Casting, Titanium Casting, Stainless Steel Casting, Brass Casting,Bronze Casting,Casting Video,Company History,Aluminum Die Casting |Comments Off