Measures to reduce the content of hydrogen, oxygen and nitrogen in steel
Generally, clean steel refers to a steel grade that has a low content of five major impurity elements (S, P, H, O, N) in steel, and strictly controls non-metallic inclusions (oxides, sulfides) in the steel. The general measures to reduce the content of [H], [O] and [N] in steel include:
1, [H] content
(1) Vacuum degassing
"Reducing PH2 can reduce the solubility of hydrogen in steel, so vacuum degassing can be used to reduce the content of [H] in steel.
(2) Reduce the moisture content of the material
80% of the hydrogen in molten steel comes from raw materials, refractory materials and moisture in the atmosphere. Attention should be paid to the baking of ladle, tundish, ferroalloy, auxiliary materials, especially lime.
In addition, the direct contact of molten steel with the atmosphere should be reduced: the molten steel after vacuum treatment should avoid powering up again, and the argon pressure should be controlled to prevent the molten steel from being exposed; at the same time, protection should be done during pouring.
2, [N] content
is similar to the method of reducing [N] content in steel. In the control to reduce the [N] content in steel, in addition to vacuum treatment of molten steel and reducing the contact of molten steel with the atmosphere, the focus is on the control of alloy content.
During operation, the elements that reduce the nitrogen content in steel (Si, Ni) are increased to the upper limit of the specification, and the elements that increase the nitrogen content in steel (Mn, Cr, Mo, V, Nb) are controlled within a certain range as far as possible to reduce Its negative effects.
3, [O] content
(1) Out-of-furnace refining of molten steel
The refining process can remove about 80% of the inclusions in the molten steel.
(2) Improve the control accuracy of the C content at the end point of the electric furnace
Try to improve the end point control accuracy when blowing oxygen in the electric furnace to reduce overblowing.
(3) Prevent slagging
The technology of slag flowing before tapping, eccentric bottom tapping and sufficient molten steel reserved in the furnace is adopted to prevent slagging.
(4) Deoxidizer control
A. Reasonable order of joining. The order of adding deoxidizer is as follows: before tapping, add a small amount of Fe-Mn in the ladle, add Fe-Si after tapping, and use a wire feeder to feed Al when refining outside the refining station.
B. Appropriate Mn/Si ratio. When Mn/Si>2.5, typical MnO-SiO2 is formed and easily rises.
C. Appropriate Al content range. When [Al] = 00.01-0.02%, the corresponding T[O] is the lowest.
D, final deoxygenation. In order to strengthen deoxidation, Si-Ca is used for final deoxidation after refining.
(5) Control the slag well
Control the slag composition, temperature, and slag amount to improve the ability of inclusions to dissolve in the slag phase.
(6) Suitable stirring intensity
Appropriate agitation is used to emphasize that inclusions can be removed without involving steel slag in molten steel. In addition, soft argon blowing can be used before the refining is finished.
Please keep the source and address of this article for reprinting: Measures to reduce the content of hydrogen, oxygen and nitrogen in steel
Minghe Die Casting Company are dedicated to manufacture and provide quality and high performance Casting Parts(metal die casting parts range mainly include Thin-Wall Die Casting,Hot Chamber Die Casting,Cold Chamber Die Casting),Round Service(Die Casting Service,Cnc Machining,Mold Making,Surface Treatment).Any custom Aluminum die casting, magnesium or Zamak/zinc die casting and other castings requirements are welcome to contact us.
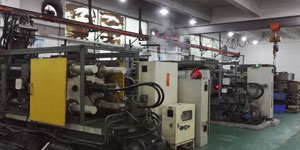
Under the control of ISO9001 and TS 16949,All processes are carried out through hundreds of advanced die casting machines, 5-axis machines, and other facilities, ranging from blasters to Ultra Sonic washing machines.Minghe not only has advanced equipment but also have professional team of experienced engineers,operators and inspectors to make the customer’s design come true.
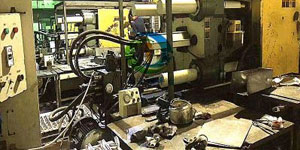
Contract manufacturer of die castings. Capabilities include cold chamber aluminum die casting parts from 0.15 lbs. to 6 lbs., quick change set up, and machining. Value-added services include polishing, vibrating, deburring, shot blasting, painting, plating, coating, assembly, and tooling. Materials worked with include alloys such as 360, 380, 383, and 413.
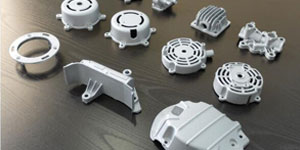
Zinc die casting design assistance/concurrent engineering services. Custom manufacturer of precision zinc die castings. Miniature castings, high pressure die castings, multi-slide mold castings, conventional mold castings, unit die and independent die castings and cavity sealed castings can be manufactured. Castings can be manufactured in lengths and widths up to 24 in. in +/-0.0005 in. tolerance.
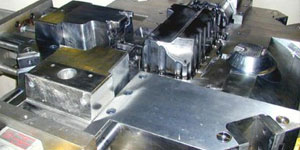
ISO 9001: 2015 certified manufacturer of die cast magnesium, Capabilities include high-pressure magnesium die casting up to 200 ton hot chamber & 3000 ton cold chamber, tooling design, polishing, molding, machining, powder & liquid painting, full QA with CMM capabilities, assembly, packaging & delivery.
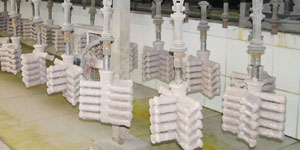
ITAF16949 certified. Additional Casting Service Include investment casting,sand casting,Gravity Casting, Lost Foam Casting,Centrifugal Casting,Vacuum Casting,Permanent Mold Casting,.Capabilities include EDI, engineering assistance, solid modeling and secondary processing.
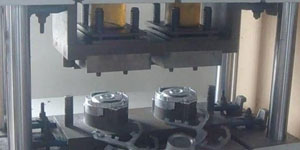
Casting Industries Parts Case Studies for: Cars, Bikes, Aircraft, Musical instruments, Watercraft, Optical devices, Sensors, Models, Electronic devices, Enclosures, Clocks, Machinery, Engines, Furniture, Jewelry, Jigs, Telecom, Lighting, Medical devices, Photographic devices, Robots, Sculptures, Sound equipment, Sporting equipment, Tooling, Toys and more.
What Can we help you do next?
∇ Go To Homepage For Die Casting China
→Casting Parts-Find out what we have done.
→Ralated Tips About Die Casting Services
By Minghe Die Casting Manufacturer |Categories: Helpful Articles |Material Tags: Aluminum Casting, Zinc Casting, Magnesium Casting, Titanium Casting, Stainless Steel Casting, Brass Casting,Bronze Casting,Casting Video,Company History,Aluminum Die Casting |Comments Off