Medium frequency induction heating heat treatment method for steel pipe, petroleum oil well pipe and drill pipe
The present invention is an intermediate frequency induction heating heat treatment method for steel pipes, oil well pipes and drill pipes. The method is divided into: the workpiece is placed on the storage platform; the workpiece is automatically aligned and positioned: the workpiece enters the heating roller table: quenching induction heating: closed loop temperature control system: continuous with the line Spraying makes the workpiece quickly and uniformly and completely quenched: the residual water in the workpiece leaks out of the pipe on the draining table: tempering induction heating: infrared temperature measurement closed-loop control system: removes the oxide scale on the surface of the workpiece; cooling bed: advantages: medium frequency induction heating As a heat source for heat treatment, it has no pollution to the environment, is safe, has less scale and is low in cost. The heating roller table ensures that the workpiece is evenly heated during the heating process.
After the workpiece passes through the roller table, it does not need a straightening machine to straighten it, reducing the cost. The spray quenching device makes the workpiece quickly and uniformly and completely quenched in the continuous spray on the line, and the descaling device makes the surface of the finished workpiece bright to its true color. The draining table makes the water and steam without tempering inside the induction heating coil, and the induction heating coil has a long service life.
The medium frequency induction heating heat treatment method for steel pipes, oil well pipes and drill pipes is characterized in that the process steps of the method are divided into:
- The storage platform on the workpiece: the workpiece steel pipes or oil well pipes or drill pipes are neatly arranged on the storage platform; the storage platform is inclined 2-5 degrees, and the workpiece is hoisted to the storage platform by the crane, automatically in order Neatly arranged: the material storage platform has an eccentric wheel structure. Adjust the eccentric wheel at different angles for φ60~φ139.7, so that the turning device can only turn one material at a time;
- The workpiece is automatically aligned and positioned: the workpiece steel pipe or oil well pipe or drill pipe is sent from the storage platform to the first station-the alignment and positioning roller table, which consists of four rollers and is equipped with a material receiving switch , In which the rollers at both ends are driven by the motor to drive the reducer to align the workpiece;
- The workpiece enters the heating roller table: the workpiece steel pipe or petroleum oil well pipe or drill pipe enters the heating roller table for uniform heating. V-shaped rollers, variable frequency speed control motors, reducers, and V-shaped rollers are installed on the heating roller table obliquely. The rotation speed is adjusted by frequency conversion. The stepping feeder is operated by the sensor to smoothly lift the workpiece on the alignment frame and roll it to the frequency conversion feeder installed at a tilt of 8-20°. The frequency conversion feeder rotates at the set speed. Front feeding, the variable frequency feeder is a single-roller drive, with adjustable speed and height. The workpiece steel pipe or oil well pipe or drill pipe is placed on the V-shaped roller and rotates in the induction heating coil. It is suitable for the workpiece steel pipe or oil well pipe or drill pipe. Heat evenly;
- Quenching induction heating: the workpiece steel pipe or oil well pipe or drill pipe enters the quenching intermediate frequency induction heating zone through the heating roller table. This heating zone is composed of two sets of intermediate frequency power supplies with different powers and multiple sets of heating induction coils to form a quenching induction heating zone. The heating temperature is 850℃-1000℃ to ensure the uniform temperature of the workpiece;
- Closed-loop temperature control: Install a two-color infrared thermometer at the exit of the induction heating coil to monitor the temperature of the workpiece, and feedback the signal to the intermediate frequency power supply to automatically adjust the output power of the intermediate frequency power supply to form a closed-loop control system to control the product process temperature Within the allowable error range;
- Continuous spraying along the line makes the workpiece quickly and uniformly and completely quenched: the heated workpiece steel pipe or oil well pipe or drill pipe enters the spray quenching zone, and the spray quenching device is used to continuously spray water onto the surface of the heated steel pipe. The pipe wall is quenched, and the effect of fast and uniform heat dissipation. Strong spray for 5-30 seconds. Two sets of high-flow and high-pressure water pumps are selected. The pressure is 125 meters. The water circulation rate is 1,000 m ↑ [3]/h. The total power is above 500 kW. , To ensure that the vapor film generated on the surface of the workpiece is destroyed;
- Draining table on the workpiece: remove the water left in the pipe after quenching the workpiece steel pipe or oil well pipe or drill pipe and bring it into the tempering coil. Use the draining table to tilt in two directions to achieve the purpose of water removal. The workpiece steel pipe or petroleum oil well pipe or drill pipe is automatically shifted, and the other direction is inclined by 2-5° in the axial direction of the workpiece steel pipe or petroleum oil well pipe or drill pipe, so that the workpiece steel pipe or petroleum oil well pipe or drill pipe is automatically moved on the drain table. When in position, make the water in the workpiece steel pipe or oil well pipe or drill pipe run out, and after a few minutes, it will be lifted by the pneumatic feeder onto the tempering line roller table;
Petroleum steel pipe heat treatment furnace
With the increasing difficulty of oil extraction and deepening of well depths, the requirements for the strength grade of oil well pipes are getting higher and higher. The J55 steel grade tubing and casing has gradually been unable to meet the requirements of use, and the N80 steel grade has become a conventional steel grade. Q125 and other steel grades are more and more widely used, and the pipe market mostly provides J55 steel grade steel pipes, and it is very difficult to purchase N80, P110, and Q125 grade steel pipes. This has brought great difficulties for petroleum steel pipe manufacturers to manufacture high-steel grade tubing and casing. The construction of a petroleum steel pipe heat treatment production line can increase the easy-to-purchase low-grade J55 pipes to N80, P110, and Q125 steel grades through heat treatment, which solves the difficulty of purchasing high-steel pipes and meets the requirements of petroleum steel pipe oil manufacturers to manufacture high-grade steel. The demand for grade tubing and casing meets the ever-increasing difficulty of oil exploration.
The steel pipes are hung and arranged on the inclined loading platform on the upper surface of the quenching furnace. The feeding roller table outside the furnace is equipped with a stopper and a material pulling device. The material pulling device pulls a steel pipe from the loading platform to On the feed roller table outside the quenching furnace. At the time of the feeding cycle, the door of the quenching furnace's feeding furnace is opened, and the feeding roller table outside the quenching furnace and the cantilever roller table inside the furnace rotate rapidly at the same time to send the steel pipe into the quenching furnace. The positioning of the steel pipe to the quenching furnace is controlled by the steel pipe positioning device and PLC. The steel pipe positioning device is generally composed of two photoelectric switches, which and PLC complete the length measurement and speed measurement of the steel pipe and the positioning in the furnace.
The steel pipe enters the furnace in place, and the feeding roller table inside and outside the furnace stops rotating. At this time, the movable beam of the walking mechanism in the furnace rises, lifting the steel pipe on the cantilever roller table in the furnace by 180mm, and the movable beam moves forward 140mm horizontally, and then descends by 180mm , Place the steel pipe on the inclined surface of the fixed beam tooth socket in the furnace and rotate a certain angle to fall in the tooth socket. The movable beam is then returned to the original position by 140mm horizontally to complete a forward stepping action. In this way, every other feeding beat, the walking beam completes a forward movement. The steel pipe is moved forward on the fixed beam by a pitch of 180mm and turned over a certain angle. The steel pipe is heated and held in the quenching furnace to the process quenching temperature requirement. The walking beam supports the steel pipe to the outgoing cantilever roller table in the quenching furnace, the discharge furnace door is opened, and the outgoing cantilever roller in the quenching furnace and the outgoing roller table outside the quenching furnace rotate rapidly at the same time (frequency conversion speed regulation maximum 2m/S). The steel pipe is conveyed to the roller table outside the furnace, and then to the quenching machine receiving roller table through the high-pressure water descaling device. The quenching machine receiving roller table is equipped with two photoelectric switches. The head of the steel pipe blocks the first photoelectric switch, and the roller table slows down. Block the second photoelectric switch roller table to stop, and the steel pipe lightly leans against the fixed baffle. At this time, the loading mechanism of the quenching furnace (a set of Sweeten levers) puts the steel pipe support on a set of rotating quenching support wheels. Corresponding to a set of pressing wheels are driven by hydraulic cylinders to press the steel pipes. The steel pipe is driven by the rotating support wheel to rotate at a higher speed. At this time, the outer spray water baffle is removed by the oil cylinder, the outer spray water is showered down, the inner spray three-way valve is reversed, and the inner spray water is sprayed from the inner hole of one end of the steel pipe. It is quenched by external shower and internal spray rotation. The quenching time can be arbitrarily set within 6-30 seconds according to the material and wall thickness of the steel pipe. After quenching, the water baffle will block the outside water from the quenching area and fall into the pit below, and the internal spray three-way valve will switch to the internal spray water to flow into the pit through the bypass. The pressing wheel is moved away, and the material pulling mechanism pulls out the steel pipe and slides it onto the air-water device, and one end of the air-water device is lifted. At the same time, compressed air blows water from the nozzle. After the water is empty, the empty water device is dropped and reset, and the steel pipe is pulled out by the feeding stop device and sent to the feeding roller table outside the tempering furnace. When the feeding rhythm is reached, the door of the tempering furnace is opened, and the steel pipe is sent to the tempering furnace by the roller table. The transmission mode is the same as that of the quenching furnace. The steel pipe is heated step by step in the tempering furnace to the process temperature. The discharge furnace door of the tempering furnace is opened, and the steel pipe is conveyed to the outside of the furnace by the discharge roller table of the tempering furnace, and is connected to the feeding roller table before the straightening machine through the connecting roller table. The steel pipe is cooled to 450- by a small cooling bed in front of the straightening machine. At about 500 degrees, the steel pipe is pulled onto the forwarding roller table of the straightening machine and sent to the straightening machine for straightening. The straightening machine is required to have a quick opening function to adapt to the straightening of steel pipes with upsetting at both ends.
This kind of furnace can well realize the heat treatment of steel pipes.
Design of heat treatment production line in continuous steel tube mill
This heat treatment line is mainly used for heat treatment of oil and casing, according to API 5CT—2001 standard. To produce high value-added tubing and casing to improve economic benefits. After heat treatment, the tubing and casing have higher strength, toughness and corrosion resistance, and reach the international standard, and are in a leading position in China.
The design is carried out according to the following process flow: the steel pipes to be heat treated from the intermediate warehouse are placed on the loading platform with a crane, and then enter the quenching furnace, after being discharged as required, the high-pressure water dephosphorization is carried out, and the water quenching device is transported by the rotating roller table. Use multiple sets of compaction rollers to compress the steel pipe and make it rotate. The outer wall of the pipe is quenched immediately under the water at room temperature above, and the pipe nozzle is aligned with the inner spray nozzle to quench the inner wall of the pipe until the temperature of the steel pipe reaches the required structure transformation.
At this time, the conveyor is lifted, and the steel pipe is transported to the drainage area by the shifter, and then into the tempering furnace. After the steel pipe comes out of the tempering furnace, it enters the cooling bed through the sizing machine and the hot straightening machine, and then conducts non-destructive inspection after cooling. , And enter the intermediate warehouse after being qualified. The key technologies and innovations of this production line are:
- Use system engineering principles and process requirements to optimize the process flow, so that the whole line has four heat treatment functions, while giving consideration to primary and secondary, smooth flow, high efficiency and low consumption.
- The use of external showering and internal spraying technology, coupled with steel pipe water quenching process expert system software, ensures the reasonable and reliable process parameters when processing seamless steel pipes of various steel grades, thereby ensuring the quality of heat-treated products.
- Fully automatic control, computerized information management, and whole-process quality monitoring to improve labor productivity and management level.
- Changing oil quenching to water quenching greatly reduces environmental pollution, saves oil, and improves production safety.
- Optimize the investment portfolio and equipment selection, and save more than 100 million yuan in construction investment compared with the entire line of equipment imports.
Please keep the source and address of this article for reprinting: Medium frequency induction heating heat treatment method for steel pipe, petroleum oil well pipe and drill pipe
Minghe Die Casting Company are dedicated to manufacture and provide quality and high performance Casting Parts(metal die casting parts range mainly include Thin-Wall Die Casting,Hot Chamber Die Casting,Cold Chamber Die Casting),Round Service(Die Casting Service,Cnc Machining,Mold Making,Surface Treatment).Any custom Aluminum die casting, magnesium or Zamak/zinc die casting and other castings requirements are welcome to contact us.
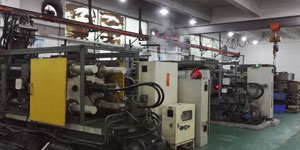
Under the control of ISO9001 and TS 16949,All processes are carried out through hundreds of advanced die casting machines, 5-axis machines, and other facilities, ranging from blasters to Ultra Sonic washing machines.Minghe not only has advanced equipment but also have professional team of experienced engineers,operators and inspectors to make the customer’s design come true.
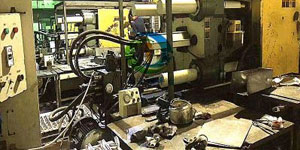
Contract manufacturer of die castings. Capabilities include cold chamber aluminum die casting parts from 0.15 lbs. to 6 lbs., quick change set up, and machining. Value-added services include polishing, vibrating, deburring, shot blasting, painting, plating, coating, assembly, and tooling. Materials worked with include alloys such as 360, 380, 383, and 413.
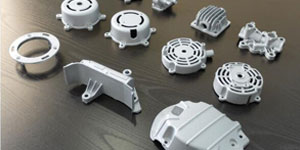
Zinc die casting design assistance/concurrent engineering services. Custom manufacturer of precision zinc die castings. Miniature castings, high pressure die castings, multi-slide mold castings, conventional mold castings, unit die and independent die castings and cavity sealed castings can be manufactured. Castings can be manufactured in lengths and widths up to 24 in. in +/-0.0005 in. tolerance.
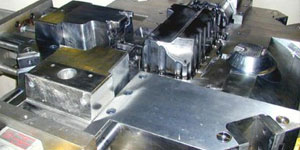
ISO 9001: 2015 certified manufacturer of die cast magnesium, Capabilities include high-pressure magnesium die casting up to 200 ton hot chamber & 3000 ton cold chamber, tooling design, polishing, molding, machining, powder & liquid painting, full QA with CMM capabilities, assembly, packaging & delivery.
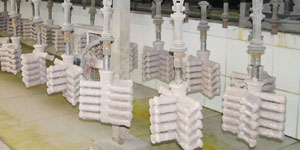
ITAF16949 certified. Additional Casting Service Include investment casting,sand casting,Gravity Casting, Lost Foam Casting,Centrifugal Casting,Vacuum Casting,Permanent Mold Casting,.Capabilities include EDI, engineering assistance, solid modeling and secondary processing.
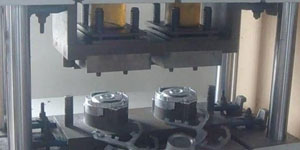
Casting Industries Parts Case Studies for: Cars, Bikes, Aircraft, Musical instruments, Watercraft, Optical devices, Sensors, Models, Electronic devices, Enclosures, Clocks, Machinery, Engines, Furniture, Jewelry, Jigs, Telecom, Lighting, Medical devices, Photographic devices, Robots, Sculptures, Sound equipment, Sporting equipment, Tooling, Toys and more.
What Can we help you do next?
∇ Go To Homepage For Die Casting China
→Casting Parts-Find out what we have done.
→Ralated Tips About Die Casting Services
By Minghe Die Casting Manufacturer |Categories: Helpful Articles |Material Tags: Aluminum Casting, Zinc Casting, Magnesium Casting, Titanium Casting, Stainless Steel Casting, Brass Casting,Bronze Casting,Casting Video,Company History,Aluminum Die Casting |Comments Off