Metal Oxide Film Influence On The Quality Of Aluminum Alloy Castings
"Casting" is a liquid metal forming process. It is well known that liquid metal at high temperature will be oxidized on the surface in the atmosphere and produce an oxide film.
However, for a long time, the impact of this oxide film on the quality of aluminum alloy castings has basically only considered the problem of non-metallic inclusions in the molten metal, and no further discussion has been made.
J. Campbell of the University of Birmingham, UK, based on years of research, found that folded bi-films have a very important impact on the quality of aluminum alloy castings from the macro and micro aspects. Campbell et al. believe that the understanding of bi-films is the most exciting discovery. At present, we temporarily refer to the preliminary conclusions and insights obtained by Campbell and others as the "bi-films theory".
After the interlayer of the oxide film involved in the liquid aluminum alloy, its influence on the quality of the casting can be roughly divided into two aspects:
One is the macroscopic aspect. In addition to cutting the metal matrix to reduce the mechanical properties, it also induces casting defects such as porosity and small shrinkage;
The other is the microscopic aspect, which has an important influence on the grain size, the distance between dendrites, and the modification effect of Na and Sr in the aluminum-silicon alloy.
1. The characteristics of the oxide film on the surface of liquid metal
Analyzing the characteristics of the oxide film, the density and melting point of the metal mother liquid on which it is attached cannot be considered at the same time. In terms of steel and iron, take the production of steel castings as an example. The FeO produced by the oxidation of molten steel has a melting point and density much lower than that of molten steel, and is very active at high temperatures, and it is basically impossible to exist alone. FeO can combine with SiO2 to form low melting point FeO.SiO2, which can react with silicon and manganese in steel to form MnO and SiO2 and then combine to form MnO.SiO2. It can also react with carbon in steel to form CO, and there will be a small part of it. Dissolved in molten steel. If the deoxidation treatment is improper, or the molten steel is oxidized twice after tapping, it will increase the number of non-metallic inclusions in the steel, or cause defects such as pores or slag inclusion on the surface of the casting. However, the oxides produced on the surface of the molten steel have melting points lower than the temperature of the molten steel and can only accumulate. They cannot be folded into an oxide film interlayer and suspended in the molten steel, so there will be no problems caused by the oxide film interlayer. .
The situation of aluminum alloys and magnesium alloys is completely different. A brief description of aluminum alloys is as follows: Aluminum is very active in the liquid state, and the surface of molten aluminum can easily react with oxygen in the atmosphere to form Al2O3 films. The melting point of Al2O3 is much higher than that of liquid aluminum alloy, and it is very stable. The density of Al2O3 is slightly higher than that of molten aluminum. Therefore, the Al2O3 film is easy to suspend in the aluminum liquid and will not aggregate and separate from the aluminum liquid. When the aluminum alloy liquid is disturbed, the Al2O3 film on the surface will fold into a sandwich and be drawn into the molten metal, causing many unique problems of aluminum alloy.
2. The formation of oxide film interlayer and its harmful effects
The aluminum alloy liquid will be strongly disturbed during the smelting process, when pouring out from the melting furnace, during the metamorphic treatment, when spraying and purifying at high air velocity, and during the pouring process. The disturbance of the surface of the liquid metal will pull the oxide film on its surface, causing it to expand, fold, and break. The clean alloy liquid surface exposed at the disconnection of the oxide film will be oxidized to produce a new oxide film. The folding of the oxide film will make the dry surfaces on the side facing the atmosphere adhere to each other, and a small amount of air will be wrapped between the two dry surfaces to become an "oxide film sandwich". The oxide film interlayer is easily involved in the molten metal, and will be squeezed into small clumps under the action of the disturbed molten metal.
Because the melting point of Al2O3 is more than one thousand degrees Celsius higher than the temperature of the aluminum alloy liquid, and it has a high degree of chemical stability, the small clusters will not fuse and will not dissolve in the aluminum alloy. Although the density of Al2O3 is slightly higher than that of aluminum alloy liquid, the density of the oxide film interlayer wrapped in air is relatively close to that of aluminum alloy liquid. Therefore, in addition to the possibility of sinking of the oxide film interlayer during long-term standing in a large holding furnace, it will be more stably suspended in the aluminum alloy liquid under general casting production conditions. The aluminum alloy liquid that has suspended oxide film interlayers will produce more oxide film interlayers when it is disturbed again. During the production process of castings, the smelting of the alloy, pouring from the furnace, modification treatment, purification treatment, pouring and other operations will cause strong disturbances in the aluminum alloy liquid. In addition to retaining the original oxide film interlayer, the aluminum alloy liquid will also cause It is disturbed again and new oxide film interlayers are continuously added. Therefore, the molten metal entering the cavity contains a large number of tiny oxide film interlayers. After the molten metal fills the cavity, it is in a static state, and the interlayer of the oxide film that is squeezed into a cluster will gradually stretch into a small piece. After the molten metal is cooled below the liquidus line, the nucleation and growth of dendrites are also factors that promote the stretching of the oxide film interlayer that is squeezed into agglomerates.
After the casting is solidified, a large number of small flaky oxide film interlayers are themselves small cracks, which play the role of cutting the metal matrix. Of course, the mechanical properties of the alloy will be reduced, but the more harmful is the induction of pores and small shrinkage holes. As the temperature of the liquid metal gradually decreases, the solubility of hydrogen in the molten metal continues to decrease, but it is very difficult for hydrogen to precipitate from the liquid metal in the form of pores. When another new phase (gas phase) is produced in a homogeneous liquid phase, it is always formed by the aggregation of a few atoms or molecules first, and its volume is small. This tiny new phase has a very large specific surface area (that is, the surface area per unit volume). To produce a new interface, work needs to be done on it. This is the interface energy of the new phase, that is, its surface area and surface tension. The product of. It is practically impossible to obtain such a large amount of energy during the cooling process of aluminum alloy liquid. Even if the core of the new phase is produced, it needs a lot of energy to grow up, and it is possible to grow up only when the size of the new phase exceeds a certain critical value. The core of the new phase with a size smaller than the critical value cannot grow up and will only disappear on its own. In theory, it is very difficult for the gas phase to nucleate and grow up in the liquid phase. Actually. If there are no other inducing factors, under the condition that the hydrogen content is basically normal, it is impossible to produce pores in a homogeneous aluminum alloy due to the precipitation of hydrogen.
When the molten metal contains a large amount of suspended oxide film interlayers, the situation is quite different. Most of the oxide film interlayer is covered with a small amount of air. When the temperature of the molten metal decreases and the solubility of hydrogen in it decreases, the small air bubbles in the oxide film interlayer are vacuum for hydrogen, and the hydrogen dissolved in the molten metal will move toward the air bubbles. Medium diffusion is very convenient. The hydrogen diffuses into the small air bubbles, which expands the oxide film interlayer, and creates pores in the casting. If the purification treatment of the aluminum alloy liquid is good and the hydrogen content in the molten metal is very low, there will be few pores in the casting. However, if there is no oxide film interlayer in the molten metal, even if the hydrogen content in the molten metal is high, the hydrogen can only be dissolved in the alloy in a supersaturated state during solidification, and it is impossible to produce pores. If the feeding condition of the casting is not good, shrinkage cavities will occur in the process of solidification and shrinkage. Since the interlayer of the oxide film is hollow, it is easy to pull apart, and shrinkage cavities are mostly formed at the interlayer of the oxide film. In this case, the hydrogen dissolved in the molten metal will also diffuse into it, causing the pores to expand.
In summary, it can be considered that for aluminum alloy castings, the oxide film interlayer is the main reason for the deterioration of the mechanical properties of the material and the pinhole and pore defects of the casting. In order to improve the mechanical properties of the material and increase the density of the casting, it is more important to take measures to eliminate the oxide film interlayer than to strengthen the degassing and purification operation.
Please keep the source and address of this article for reprinting: Metal Oxide Film Influence On The Quality Of Aluminum Alloy Castings
Minghe Die Casting Company are dedicated to manufacture and provide quality and high performance Casting Parts(metal die casting parts range mainly include Thin-Wall Die Casting,Hot Chamber Die Casting,Cold Chamber Die Casting),Round Service(Die Casting Service,Cnc Machining,Mold Making,Surface Treatment).Any custom Aluminum die casting, magnesium or Zamak/zinc die casting and other castings requirements are welcome to contact us.
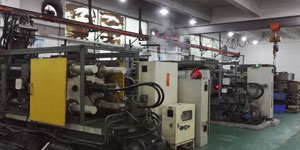
Under the control of ISO9001 and TS 16949,All processes are carried out through hundreds of advanced die casting machines, 5-axis machines, and other facilities, ranging from blasters to Ultra Sonic washing machines.Minghe not only has advanced equipment but also have professional team of experienced engineers,operators and inspectors to make the customer’s design come true.
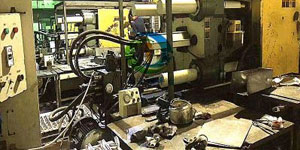
Contract manufacturer of die castings. Capabilities include cold chamber aluminum die casting parts from 0.15 lbs. to 6 lbs., quick change set up, and machining. Value-added services include polishing, vibrating, deburring, shot blasting, painting, plating, coating, assembly, and tooling. Materials worked with include alloys such as 360, 380, 383, and 413.
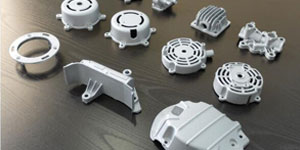
Zinc die casting design assistance/concurrent engineering services. Custom manufacturer of precision zinc die castings. Miniature castings, high pressure die castings, multi-slide mold castings, conventional mold castings, unit die and independent die castings and cavity sealed castings can be manufactured. Castings can be manufactured in lengths and widths up to 24 in. in +/-0.0005 in. tolerance.
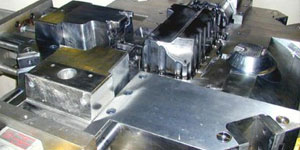
ISO 9001: 2015 certified manufacturer of die cast magnesium, Capabilities include high-pressure magnesium die casting up to 200 ton hot chamber & 3000 ton cold chamber, tooling design, polishing, molding, machining, powder & liquid painting, full QA with CMM capabilities, assembly, packaging & delivery.
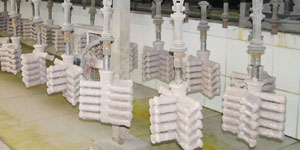
ITAF16949 certified. Additional Casting Service Include investment casting,sand casting,Gravity Casting, Lost Foam Casting,Centrifugal Casting,Vacuum Casting,Permanent Mold Casting,.Capabilities include EDI, engineering assistance, solid modeling and secondary processing.
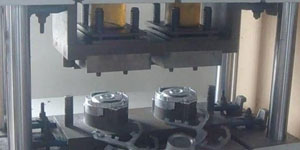
Casting Industries Parts Case Studies for: Cars, Bikes, Aircraft, Musical instruments, Watercraft, Optical devices, Sensors, Models, Electronic devices, Enclosures, Clocks, Machinery, Engines, Furniture, Jewelry, Jigs, Telecom, Lighting, Medical devices, Photographic devices, Robots, Sculptures, Sound equipment, Sporting equipment, Tooling, Toys and more.
What Can we help you do next?
∇ Go To Homepage For Die Casting China
→Casting Parts-Find out what we have done.
→Ralated Tips About Die Casting Services
By Minghe Die Casting Manufacturer |Categories: Helpful Articles |Material Tags: Aluminum Casting, Zinc Casting, Magnesium Casting, Titanium Casting, Stainless Steel Casting, Brass Casting,Bronze Casting,Casting Video,Company History,Aluminum Die Casting |Comments Off