Nodular cast iron smelting treatment process and matters needing attention
The alloying treatment of cast iron can be traced back to the 1930s and 1940s. The alloying treatment has made a qualitative leap in the properties of cast iron. At the same time, some special purpose cast irons such as wear resistance, corrosion resistance and heat resistance have been born. The use of inoculation to produce cast iron was also produced during this period. In the late 1940s, cast iron with spherical graphite after inoculation replaced the usual flake graphite cast iron. We call this type of cast iron nodular cast iron.
The classification of spheroidization and despheroidization elements
Spheroidizing elements are generally divided into three groups according to their spheroidizing effect.
- First group: Mg, Y, Ce, La, Pr, Sm, Dy, Ho, Er.
- The second group: Ba, Li, Cs, Rb, Sr, Th, K, Na.
- The third group: Al, Zn, Cd, Sn.
- The first group has the strongest spheroidizing ability, the second group is second, and the third group is the weakest.
- When magnesium is used as the spheroidizing element, the third group of elements tends to produce de-spheroidizing effect.
Despheroidizing elements: Sulfur and oxygen are common despheroidizing elements in cast iron. In addition, Ti, Al, B, As, Pb, Sn, Sb, Bi, Te, Se, etc. are common despheroidizing elements in molten iron . The attached table is classified according to its mechanism of action.
How to choose spheroidizing agent
Nodulizers and inoculants are the most important materials in the spheroidization process. In addition to stable quality, the following factors need to be considered when choosing a suitable nodulizer.
- Spheroidizing temperature: If the spheroidizing temperature is greater than 1480℃, the spheroidizing reaction will be more intense, resulting in a lower magnesium absorption rate. In order to make the spheroidizing reaction stable, a spheroidizing agent with a relatively high calcium content can be selected. If the spheroidizing temperature is less than 1480°C, a spheroidizing agent with a relatively low calcium content can be used.
- Treatment bag size: If the height to diameter ratio of the treatment bag is 1:1, the loss of magnesium vapor will reduce the magnesium absorption rate. It is recommended to use a spheroidizing agent with a higher calcium content. If the height-to-diameter ratio of the treatment package is 2:1, the spheroidization reaction will be relatively stable, the magnesium vapor will diffuse into the molten iron, and the magnesium absorption rate will be improved.
- Spheroidization process: If the cover method is not used, the smoke generated by the spheroidization reaction will enter the atmosphere and produce dazzling white light. In order to make the spheroidizing reaction stable, a spheroidizing agent with low magnesium and high calcium can be used. If you use the cap-and-wrap process, the molten iron will not splash and produce less smoke. You can use a high-magnesium and low-calcium spheroidizing agent to reduce the amount and reduce the cost of spheroidization.
- Processing weight: If the weight of the molten iron to be processed is less than 500kg, then a spheroidizing agent with a smaller particle size can be used, and a spheroidizing agent with a particle size of 12mm or less is recommended. If the weight of the molten iron is 500~1000kg, a spheroidizing agent with a larger particle size can be used, such as a spheroidizing agent with a particle size of 3-25mm. If the weight of the molten iron is more than 1000kg, the spheroidizing agent of 4~32mm can be used.
- Silicon content: If the casting product has a low process yield or a high scrap rate, it is desirable to add more furnace material and scrap steel for smelting, and the final casting has strict requirements on the silicon content of the molten iron. Under the premise that the inoculation volume cannot be further reduced, a low-silicon spheroidizing agent can be used for treatment, so that 8% to 15% of the reheating material can be added, which can reduce the production cost of the foundry.
Sulfur content of raw iron liquid: If the sulfur content of the raw iron liquid is high, if the desulfurization treatment is not carried out, a high-magnesium, high-rare earth nodulizer is required, and the addition amount will be higher. The spheroidizing agent with low magnesium and rare earth can be used, and the added amount will be lower, and the cost of the spheroidizing agent with low magnesium and rare earth will be cheaper.
Different spheroidization methods
At present, the commonly used spheroidization methods are as follows: in-pack processing method (including straight-punching method, sandwich method and cover method), type inner spheroidization method, flow method, pure magnesium treatment process (including sub-packing method and core-packing method) Line method). The advantages and disadvantages of these spheroidization methods are briefly introduced as follows.
- In-package treatment method: This is the most common spheroidization process, and it has a wide range of applications. This process can be used for automotive parts as small as a few kilograms and wind power parts as large as tens of tons. Magnesium absorption rate is highest in the cover method, followed by the sandwich method. The disadvantage is that the current degree of automation is not high, and some domestic equipment factories are developing automatic feeding systems.
- Type internal spheroidization method: There are not many foundries using this process, because the shortcomings of this process are obvious. The slag produced by the spheroidization process sometimes enters the cavity, causing slag inclusion defects and producing waste products. In addition, this spheroidizing process has higher requirements on the temperature and flow rate of the molten iron, otherwise the spheroidization will be uneven.
- Flow method: As the name implies, the flow method is spheroidizing by flowing molten iron through a spheroidizing chamber filled with a spheroidizing agent. At present, this process is not used too much. The advantage is that the degree of automation is relatively high; the disadvantage is that it has strict requirements on the temperature and flow rate of the molten iron.
- Pure magnesium spheroidization process: sometimes called high-magnesium spheroidization process, currently there are two main forms, subcontracting method and cored wire method. The advantage of this method is that it has a higher degree of automation and is also conducive to environmental protection; the disadvantage is that the magnesium absorption rate is low, and it produces more smoke and slag.
The attached picture compares various spheroidizing processes in terms of smoke, slag, and magnesium absorption rate..
Precautions for the production of ductile iron
Now briefly summarize the matters needing attention in the production of ductile iron.
- The sulfur content and other trace elements of the raw iron liquid should not be too high. If the sulfur content and the content of other trace elements in the original molten iron are too high, more spheroidizing agent is required or a spheroidizing agent with a higher rare earth content is required, so that the cost of the spheroidizing agent will increase, and excessive spheroidizing The agent will cause more slag, which is not conducive to the stability of casting quality. Too much rare earth content will easily produce fragmented graphite on large-section castings.
- The stability of spheroidization. The spheroidizing process is a key process in the production of nodular cast iron. Only when the spheroidizing process is stable can the quality of the castings be stable. For different products, different raw iron liquid sulfur content, how much spheroidizing agent, inoculant, etc. should be added, must be written in the work instruction and strictly implemented.
- Avoid long waiting times. After the spheroidization inoculation treatment, pouring should be carried out immediately. Because over time, the residual magnesium will burn and the inoculation effect will decline.
- Avoid excessively high residual magnesium content. Higher residual magnesium content will increase the shrinkage tendency of castings. For general ductile iron, the residual magnesium content (mass fraction) should be controlled within 0.035%~0.045%, and for high-nickel ductile iron, the residual magnesium content should be controlled within 0.06% ~0.07%.
- Use better inoculants for castings with higher requirements. For wind power parts and high-speed rail parts with higher requirements, the flow inoculant with strong inoculation effect (such as patented Ultraseed/Ce) should be selected. Its characteristic is that it can significantly increase the number of graphite spheres, and the graphite spheres are rounded.
Please keep the source and address of this article for reprinting:Nodular cast iron smelting treatment process and matters needing attention
Minghe Die Casting Company are dedicated to manufacture and provide quality and high performance Casting Parts(metal die casting parts range mainly include Thin-Wall Die Casting,Hot Chamber Die Casting,Cold Chamber Die Casting),Round Service(Die Casting Service,Cnc Machining,Mold Making,Surface Treatment).Any custom Aluminum die casting, magnesium or Zamak/zinc die casting and other castings requirements are welcome to contact us.
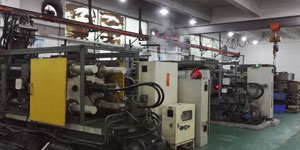
Under the control of ISO9001 and TS 16949,All processes are carried out through hundreds of advanced die casting machines, 5-axis machines, and other facilities, ranging from blasters to Ultra Sonic washing machines.Minghe not only has advanced equipment but also have professional team of experienced engineers,operators and inspectors to make the customer’s design come true.
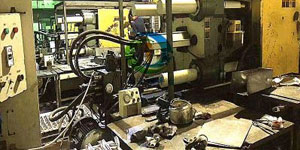
Contract manufacturer of die castings. Capabilities include cold chamber aluminum die casting parts from 0.15 lbs. to 6 lbs., quick change set up, and machining. Value-added services include polishing, vibrating, deburring, shot blasting, painting, plating, coating, assembly, and tooling. Materials worked with include alloys such as 360, 380, 383, and 413.
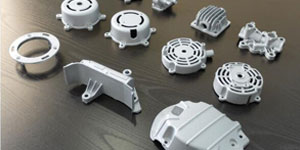
Zinc die casting design assistance/concurrent engineering services. Custom manufacturer of precision zinc die castings. Miniature castings, high pressure die castings, multi-slide mold castings, conventional mold castings, unit die and independent die castings and cavity sealed castings can be manufactured. Castings can be manufactured in lengths and widths up to 24 in. in +/-0.0005 in. tolerance.
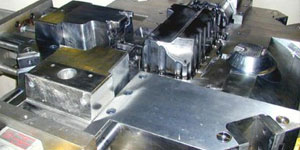
ISO 9001: 2015 certified manufacturer of die cast magnesium, Capabilities include high-pressure magnesium die casting up to 200 ton hot chamber & 3000 ton cold chamber, tooling design, polishing, molding, machining, powder & liquid painting, full QA with CMM capabilities, assembly, packaging & delivery.
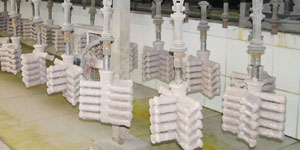
ITAF16949 certified. Additional Casting Service Include investment casting,sand casting,Gravity Casting, Lost Foam Casting,Centrifugal Casting,Vacuum Casting,Permanent Mold Casting,.Capabilities include EDI, engineering assistance, solid modeling and secondary processing.
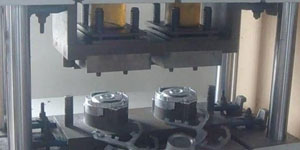
Casting Industries Parts Case Studies for: Cars, Bikes, Aircraft, Musical instruments, Watercraft, Optical devices, Sensors, Models, Electronic devices, Enclosures, Clocks, Machinery, Engines, Furniture, Jewelry, Jigs, Telecom, Lighting, Medical devices, Photographic devices, Robots, Sculptures, Sound equipment, Sporting equipment, Tooling, Toys and more.
What Can we help you do next?
∇ Go To Homepage For Die Casting China
→Casting Parts-Find out what we have done.
→Ralated Tips About Die Casting Services
By Minghe Die Casting Manufacturer |Categories: Helpful Articles |Material Tags: Aluminum Casting, Zinc Casting, Magnesium Casting, Titanium Casting, Stainless Steel Casting, Brass Casting,Bronze Casting,Casting Video,Company History,Aluminum Die Casting |Comments Off