Optimization and Application of Die Casting Scheme of ETC Throttle Aluminum Shell Casting Based on MAGMASOFT
In recent years, with the development of the global economy, the demand for automotive aluminum alloy parts has a great impact on the overall development prospects of the die-casting industry. In the face of increasingly severe industry competition and the ever-shortening of new product development cycles, The delivery of qualified products that meet customer requirements in a short period of time will be a new direction for the development of die-casting enterprises; this article uses the DOE function of MAGMASOFT to carry out simulation analysis and comparison of different casting schemes and various process parameters in the early stage of ETC throttle aluminum shell castings. And optimization, to select the best solution, thereby reducing the development cycle, and ensuring the success of the product's one-time trial and smooth mass production and delivery.
In the face of the worsening global climate crisis and the increasingly severe trend of energy saving, emission reduction and pollution reduction, the automotive industry will also continue to develop in the direction of energy saving, emission reduction and intelligence; and the electronic throttle system was born in this environment (Electronic Throttle Control System for short ETC) is an indispensable and important part of the current automobile engine system. It determines the operating conditions of the engine by controlling the intake air flow of the engine to ensure the best power and fuel of the vehicle. Economical, in order to further control emission requirements. It is foreseeable that the electronic throttle, as one of the key technologies of advanced vehicle control and safety systems, will surely have good application prospects like other advanced vehicle control technologies.
As one of the most important components in the electronic throttle system, ETC throttle aluminum shell castings will definitely affect the feasibility and stability of the system; therefore, the production of ETC throttle aluminum castings that meet the requirements will be It is extremely important. In this paper, with the help of the DOE function of MAGMASOFT, in the early stage of ETC throttle aluminum casing castings, different pouring schemes and various process parameter simulation analysis comparisons and optimizations are carried out to select the best scheme, thereby reducing the development cycle and guaranteeing this product once The success of the trial model and the smooth mass production and delivery.
1 Product structure analysis and technical requirements
The die-casting material grade of the ETC throttle aluminum shell casting studied in this paper is AlSi12Cu1Fe, and its maximum outline dimension is 111mm*109mm*84mm. The average thickness of this casting is 4mm, and the thickness at the maximum wall thickness is 13mm. The overall structure of the product is more complicated. , There are many isolated high ribs, which is not conducive to the orderly filling of the molten aluminum; the wall thickness of some positions differs greatly, and the thin-walled area will first solidify into a solid state, which is equivalent to dividing the molten alloy into many The small enclosed area forms an isolated liquid phase area at the thick wall. When the molten metal solidification and shrinkage process in these isolated liquid phase areas cannot be supplemented, the problem of shrinkage cavities and porosity will inevitably occur inside.
Due to the complicated working environment of ETC throttle aluminum shell castings, shot blasting is required to strengthen the surface quality of the castings and improve its corrosion resistance; the product's matching installation position has higher geometric and dimensional tolerance requirements; Ensure that the leakage volume at the leak test pressure of 3bar is less than or equal to 3cc/min, and the diameter of the shrinkage hole in the local area of the product is not allowed to exceed 0.7mm, the total number does not exceed 5, the spacing is not less than 10mm, and it does not exceed 10% of the total area. ; Therefore, for this die-casting, very high casting process design requirements are required to ensure that the internal quality of the casting can meet the customer's acceptance standard;
2 Product die-casting scheme and process parameter design
2.1 Product die-casting scheme design
The extremely important die-casting gate design link in die-casting production technology determines the quality of die-casting parts, die-casting production efficiency, mold life, trimming and cleaning of die-casting parts, remelting rate of die-casting alloys, and power efficiency of die-casting machines. It has a far-reaching impact; therefore, the design of reasonable gate position, gate thickness and size, and gate quantity are the keys to ensure qualified die casting quality; from the analysis of product structure characteristics and process design experience, the ETC throttle aluminum housing There are three locations for castings that are suitable for the design of the feed inlet; therefore, this article will design three different die-casting pouring schemes. From the theoretical filling path and flow distance, different pouring schemes will produce different filling effects, so they need to be based on MAGMA simulation software results are compared and analyzed for verification;
2.1.1 Pouring plan one design
As shown in the figure, the number of gates in the first pouring scheme is designed as double strands, which are respectively designed in the side wall area of the motor installation position and the valve plate installation position. The injection punch with a diameter of 60mm is selected, and the injection speed ratio is 1:14 ; The advantage of this pouring scheme is that the flow of molten metal is relatively short, which has little effect on the temperature reduction value during the filling process; the design of three flow channels is conducive to the transmission of pressure and the feeding of the molten metal, which is helpful to reduce the later production process The risk of shrinkage defects has a certain positive effect; its disadvantage is that due to product classification and structure reasons, the runner must be designed with certain steps and thin-walled areas. These positions are prone to enveloping gas during the later filling process. In addition, the motor installation position of this product is not processed, and the gate design is here, which is easy to directly wash the inner wall core and the temperature at the gate position. Higher, it is easy to cause the defects of die and erosion in the motor installation position; and the gate position is not processed, which has a certain negative impact on the trimming and cleaning of the later die castings;
2.1.2 Design of the second pouring scheme
As shown in the figure, the number of gates in the second pouring scheme is designed to be one, and the position is designed in the side circular hole area of the valve plate installation position. The injection punch with a diameter of 60mm is selected, and the injection speed ratio is 1:30; this pouring The advantage of the solution is that the runner can be designed with a relatively smooth transition, which is beneficial to the filling of the molten metal and reduces the phenomenon of gas enveloping during the filling process, and reduces the defects caused by the gas brought by the runner; the gate is designed at the position of the processing surface. Reduce the workload of trimming and cleaning die castings, and reduce production costs; single-strand gate can prevent multiple strands of molten metal from entering the cavity and causing vortex, entrainment, and oxidation. The disadvantage is that it is at the far end of the gate. The feeding effect of the hot spot position is basically lacking, and other auxiliary feeding schemes need to be considered; and the molten metal flow is relatively long, which has a certain negative impact on the molten metal temperature during the filling process, and cold material defects may occur in local locations. ;
2.1.3 Design of the third pouring scheme
As shown in the figure, the number of three gates in the pouring scheme is designed to be one, and the position is set in the side circular hole area of the valve plate installation position. The injection punch with a diameter of 60mm is selected, and the injection speed ratio is 1:30; The advantage of the gate is that the gate is designed in the position of the processing surface, which can reduce the workload of trimming and cleaning of the die-casting machine, and reduce the production cost. The gate is designed with a linear filling style, which can reduce the filling stroke of the molten aluminum and the temperature loss of the molten aluminum. The amount is reduced; the distance between the punch and the gate is short, which can ensure the effective transmission of the punch pressure; the disadvantage is that the flexibility of the later production adjustment parameters is poor, and the product quality cannot be improved by adjusting the die casting parameters.
2.2 Product process parameter design
According to the structural analysis and quality requirements of ETC throttle aluminum shell castings, this product uses 350T die casting machine, one mold and one cavity design, and the casting pressure is set to 100MPa to ensure sufficient feeding efficiency and reduce the appearance of shrinkage defects in the later period. ; The pouring temperature is designed to be 660-680℃, and the moving and fixed mold cores are preheated to 180-200℃; during filling, the low speed is set to 0.25m/s, the high speed is set to 3m/s, and the high-speed switching points are tested at 340mm and 350mm respectively. The position is used to determine the most stable filling state of the molten metal and the least eddy current and entrainment phenomenon; at the same time, the temperature control system of line cooling and point cooling is used to ensure a good thermal balance of the mold;
3. Numerical simulation and comparative analysis of one-click import
The filling and solidification process control of the casting has a decisive influence on the quality of the die casting, but since these two processes are completed in a closed and invisible cavity during the production process, it is impossible to observe and analyze directly or indirectly, so the previous value Simulation is particularly important; by using the MAG code DOE function, one-click import of the above three injection schemes and two test high-speed switching positions, one-time calculation of multiple schemes, the fastest prediction of the defect location, and find the best Plan to improve the internal quality of products, reduce development cycles, and reduce production costs.
3.1 Simulation and analysis of filling process
As shown in Figure 3, the simulation result of the first row of the picture is the filling time. The high-speed switching position of the first three schemes is 340mm, and the filling time is short. The high-speed switching position of the last three schemes is 350mm, and the filling time is long. The bright color position is the last filling position of the three injection schemes;
The result of the second row of the picture is the maximum air pressure result. The bright color of the simulation result is the high air pressure position, and the risk of stomata is high. Through comparison, it is found that the air pressure value of Scheme 2 and Scheme 5 is relatively low, and the risk of stoma is relatively small;
The result of the third row of the picture is the result of the filling volume. The simulation result has a high air content in the bright position and a high risk of leakage. Through comparison, it is found that the value of the second and fifth volumes of the scheme is relatively low, and the risk of leakage is relatively small;
Comprehensive analysis of the simulation results of the filling process shows that the air pressure and entrainment of the second and fifth options are relatively low, and the second high-speed switching position is forward, and the filling time is short, so the overall formability is good.
3.2 Simulation and analysis of solidification process
As shown in Figure 4, the result of the first row of the picture is the freezing temperature field. The simulation results show that the solidification time of the inner gate of the scheme 3 and the scheme 6 is the longest, and the pressure feeding time is the longest; the scheme 1 and scheme 4 are the second, and the pressure feeding time is the middle; the solidification time of the inner gate of the scheme 2 and scheme 5 The shortest and the shortest time for pressure supply;
The result of the second row is the effective feeding time of the hot joint, and the bright color of the simulation result is the position of the hot joint of the product, which is the position where the product structure is relatively thick and finally solidified. The locations of programs 1, 2, 4, and 5 are basically the same. Scheme 3 and Scheme 6 have relatively thick inner gates, so if the two hot spots at the inner gate are connected together, the hot spots will increase;
The result of the third row is the shrinkage result. Because of the pressure feeding, the shrinkage state of scheme 3 and scheme 6 is the smallest, and the shrinkage of the other four schemes is basically the same. In comparison, scheme 2 and scheme 5 are relatively small some.
Based on the analysis of the simulation results of the solidification process, the shrinkage cavity of the scheme 3 and the scheme 6 is the smallest, but the hot joint at the inner gate is the largest, and the heat joint and shrinkage results of the scheme 2 and the scheme 5 are relatively better.
4. Production verification
Comprehensive simulation analysis, the second casting method is used for production. Figure 5 shows the production picture of ETC throttle aluminum casing castings; through product inspection and X-ray inspection, the castings did not show pores and shrinkage defects that exceeded the customer's quality requirements; also Passed the side leakage requirements, no leakage occurred; the surface of the casting was bright, no obvious defects of cold material and insufficient pouring appeared, the overall effect fully met the customer's quality inspection requirements, and smooth mass production.
Please keep the source and address of this article for reprinting:Optimization and Application of Die Casting Scheme of ETC Throttle Aluminum Shell Casting Based on MAGMASOFT
Minghe Die Casting Company are dedicated to manufacture and provide quality and high performance Casting Parts(metal die casting parts range mainly include Thin-Wall Die Casting,Hot Chamber Die Casting,Cold Chamber Die Casting),Round Service(Die Casting Service,Cnc Machining,Mold Making,Surface Treatment).Any custom Aluminum die casting, magnesium or Zamak/zinc die casting and other castings requirements are welcome to contact us.
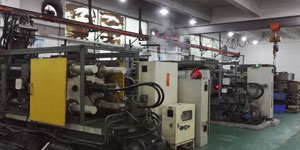
Under the control of ISO9001 and TS 16949,All processes are carried out through hundreds of advanced die casting machines, 5-axis machines, and other facilities, ranging from blasters to Ultra Sonic washing machines.Minghe not only has advanced equipment but also have professional team of experienced engineers,operators and inspectors to make the customer’s design come true.
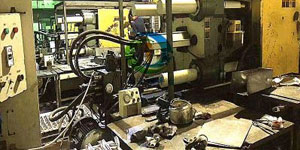
Contract manufacturer of die castings. Capabilities include cold chamber aluminum die casting parts from 0.15 lbs. to 6 lbs., quick change set up, and machining. Value-added services include polishing, vibrating, deburring, shot blasting, painting, plating, coating, assembly, and tooling. Materials worked with include alloys such as 360, 380, 383, and 413.
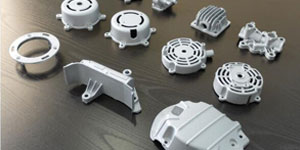
Zinc die casting design assistance/concurrent engineering services. Custom manufacturer of precision zinc die castings. Miniature castings, high pressure die castings, multi-slide mold castings, conventional mold castings, unit die and independent die castings and cavity sealed castings can be manufactured. Castings can be manufactured in lengths and widths up to 24 in. in +/-0.0005 in. tolerance.
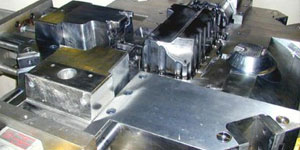
ISO 9001: 2015 certified manufacturer of die cast magnesium, Capabilities include high-pressure magnesium die casting up to 200 ton hot chamber & 3000 ton cold chamber, tooling design, polishing, molding, machining, powder & liquid painting, full QA with CMM capabilities, assembly, packaging & delivery.
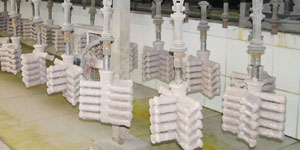
ITAF16949 certified. Additional Casting Service Include investment casting,sand casting,Gravity Casting, Lost Foam Casting,Centrifugal Casting,Vacuum Casting,Permanent Mold Casting,.Capabilities include EDI, engineering assistance, solid modeling and secondary processing.
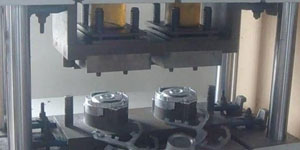
Casting Industries Parts Case Studies for: Cars, Bikes, Aircraft, Musical instruments, Watercraft, Optical devices, Sensors, Models, Electronic devices, Enclosures, Clocks, Machinery, Engines, Furniture, Jewelry, Jigs, Telecom, Lighting, Medical devices, Photographic devices, Robots, Sculptures, Sound equipment, Sporting equipment, Tooling, Toys and more.
What Can we help you do next?
∇ Go To Homepage For Die Casting China
→Casting Parts-Find out what we have done.
→Ralated Tips About Die Casting Services
By Minghe Die Casting Manufacturer |Categories: Helpful Articles |Material Tags: Aluminum Casting, Zinc Casting, Magnesium Casting, Titanium Casting, Stainless Steel Casting, Brass Casting,Bronze Casting,Casting Video,Company History,Aluminum Die Casting |Comments Off