Optimization of heat treatment process for GH690 alloy pipe
The 690 alloy tube used for the steam generator heat transfer tube of nuclear power plant bears the corrosion of high temperature, high pressure and water medium, alloy grain size, intergranular Cr depletion, intergranular carbide and its force on stress concentration.
The academic effect is an important factor that affects the intergranular corrosion and stress corrosion resistance of materials. In addition to strictly controlling the composition, a reasonable heat treatment process can eliminate the influence of these factors on the material properties.
The benefit and impact aspect is crucial.
Taking the microstructure of the foreign Inconel 690 finished pipe as the reference object, the solution treatment and isothermal heat treatment (TT treatment) process of the domestic GH690 alloy pipe under different process conditions are carried out.
Research has been done; the effects of process parameters on its grain size, grain boundary carbide morphology and Cr-poor zone are analyzed by characterization methods such as OM, SEM and TEM. the result shows:
(1) The grain distribution of finished Inconel 690 tubes abroad is uneven, the average grain size is about 23μm, and the number of grains with a grain size of 7 to 10 is the largest. Grain boundary carbides are mainly fine.
TiN particles are distributed semi-continuously and there are many large-size TiN particles. There is a Cr-poor region with a width of about 200nm near the grain boundary.
(2) During the solution treatment process of domestic GH690 alloy tube, as the solution temperature increases, the crystal grains continue to grow, and the growth activation energy is 265kJ/mol. When the solid solution temperature exceeds 1100℃.
At this time, the grain growth is more obvious, and the effect of holding time on the grain size also becomes significant.
(3) After the domestic GH690 alloy tube is treated with TT under different process conditions, the grain boundary carbides mainly appear as fine and dispersed, fine and semi-continuous, coarse and semi-continuous, and coarse and dispersed.
Kind of distribution status. When the process parameters of TT treatment are 680℃/10~20h, 715℃/10~20h, 750℃/5~15h, the grain boundary carbides are distributed in fine semi-continuous.
(4) The average grain size and grain size distribution of domestic GH690 alloy pipe after solution treatment at 1090~1110℃/5min are close to those of foreign Inconel 690 finished pipe. After 715℃/10h or 15h
After the TT treatment, the grain boundary carbide morphology and Cr-poor zone evolution characteristics of the domestic GH690 alloy tube are similar to those of the foreign Inconel 690 finished tube, but the size and quantity of TiN particles are significantly smaller and less.
In the latter, and its lowest Cr concentration is higher than the latter, it helps to improve the pitting corrosion resistance and intergranular corrosion resistance of the alloy. The overall microstructure of domestic GH690 alloy tube is better than that of foreign Inconel 6
90 finished tubes.
(5) Comprehensive comparison of the structural characteristics of 690 alloy pipes at home and abroad, and taking into account the cost issues in actual production, it is recommended that the heat treatment optimization process of domestic GH690 alloy pipe is 1090~111
0℃/5min+715℃/10~15h.
Please keep the source and address of this article for reprinting: Optimization of heat treatment process for GH690 alloy pipe
Minghe Die Casting Company are dedicated to manufacture and provide quality and high performance Casting Parts(metal die casting parts range mainly include Thin-Wall Die Casting,Hot Chamber Die Casting,Cold Chamber Die Casting),Round Service(Die Casting Service,Cnc Machining,Mold Making,Surface Treatment).Any custom Aluminum die casting, magnesium or Zamak/zinc die casting and other castings requirements are welcome to contact us.
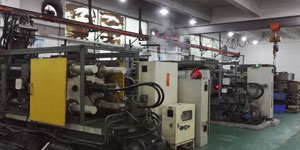
Under the control of ISO9001 and TS 16949,All processes are carried out through hundreds of advanced die casting machines, 5-axis machines, and other facilities, ranging from blasters to Ultra Sonic washing machines.Minghe not only has advanced equipment but also have professional team of experienced engineers,operators and inspectors to make the customer’s design come true.
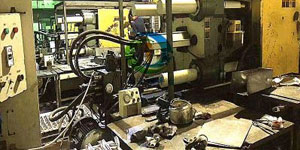
Contract manufacturer of die castings. Capabilities include cold chamber aluminum die casting parts from 0.15 lbs. to 6 lbs., quick change set up, and machining. Value-added services include polishing, vibrating, deburring, shot blasting, painting, plating, coating, assembly, and tooling. Materials worked with include alloys such as 360, 380, 383, and 413.
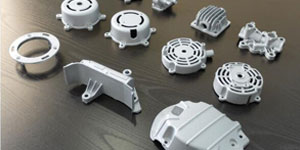
Zinc die casting design assistance/concurrent engineering services. Custom manufacturer of precision zinc die castings. Miniature castings, high pressure die castings, multi-slide mold castings, conventional mold castings, unit die and independent die castings and cavity sealed castings can be manufactured. Castings can be manufactured in lengths and widths up to 24 in. in +/-0.0005 in. tolerance.
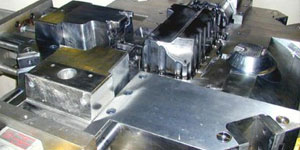
ISO 9001: 2015 certified manufacturer of die cast magnesium, Capabilities include high-pressure magnesium die casting up to 200 ton hot chamber & 3000 ton cold chamber, tooling design, polishing, molding, machining, powder & liquid painting, full QA with CMM capabilities, assembly, packaging & delivery.
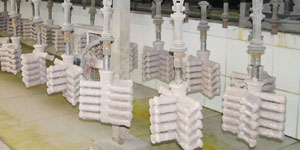
ITAF16949 certified. Additional Casting Service Include investment casting,sand casting,Gravity Casting, Lost Foam Casting,Centrifugal Casting,Vacuum Casting,Permanent Mold Casting,.Capabilities include EDI, engineering assistance, solid modeling and secondary processing.
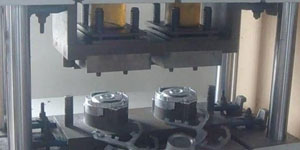
Casting Industries Parts Case Studies for: Cars, Bikes, Aircraft, Musical instruments, Watercraft, Optical devices, Sensors, Models, Electronic devices, Enclosures, Clocks, Machinery, Engines, Furniture, Jewelry, Jigs, Telecom, Lighting, Medical devices, Photographic devices, Robots, Sculptures, Sound equipment, Sporting equipment, Tooling, Toys and more.
What Can we help you do next?
∇ Go To Homepage For Die Casting China
→Casting Parts-Find out what we have done.
→Ralated Tips About Die Casting Services
By Minghe Die Casting Manufacturer |Categories: Helpful Articles |Material Tags: Aluminum Casting, Zinc Casting, Magnesium Casting, Titanium Casting, Stainless Steel Casting, Brass Casting,Bronze Casting,Casting Video,Company History,Aluminum Die Casting |Comments Off