Process Improvement For Loose Thin-Walled Castings And Under-Casting Defects
The wall thickness of the regulating piece and sealing piece of high-temperature alloy castings is changed from 1.1mm to 0.8mm, which leads to faster solidification of the castings. The original casting process cannot effectively fill and feed the edges of the castings, resulting in insufficient casting and looseness. defect. In this regard, on the basis of the original process plan, the method of wrapping asbestos in the thin-walled area is adopted to slow down the cooling of the mold shell and prolong the solidification time of the thin-walled area, so that the alloy liquid can effectively fill the mold and feed the edge of the casting to eliminate undercasting, Loose defects.
Regulating piece and sealing piece high-temperature alloy castings (as shown in the figure above), the wall thickness of more than 90% of the area is required to be 0.8mm, and the wall thickness of the castings is cast according to the upper deviation (+0.3), and the casting molding effect and metallurgical quality are good. The process plan is basically mature, but the weight exceeds the design requirements; after the wall thickness is changed to 0.8mm, the original process plan is still produced. Almost 100% of the casted castings are loose, and the loose defects are concentrated on the edges of both sides of the casting floor. Location (as shown in the figure below). In addition, more than 40% of the castings are under-casting, and slag inclusion defects have also increased significantly.
The Analysis Of Porosity Defects
The cross-sectional view of the edges on both sides of the casting bottom plate is shown in the figure below. There are reinforcing ribs on the edges. The design requirements for the wall thickness of the ribs and the bottom plate are shown in the figure below. In the initial design of the mold, the wall thickness of the rib and the bottom plate shall be 1.1mm, that is, equal wall thickness. The joint between the rib plate and the bottom plate wall forms a casting hot node; compared to the bottom plate, the modulus of the hot node is not much different. In addition, the hot node is on the edge of the casting, cooling and solidifying relatively fast, and the alloy liquid can heat through the bottom plate The nodes are fed without loose defects.
After the wall thickness of the bottom plate was changed to 0.8 mm, the modulus of the bottom plate was reduced by nearly 1/3, and the cooling and solidification speed of the bottom plate was accelerated; while the wall thickness of the ribs did not change, the modulus of the hot node remained basically unchanged, and the cooling and solidification speeds were basically unchanged. As a result, the alloy liquid cannot effectively feed the hot nodes through the bottom plate, resulting in looseness.
The Analysis Of Undercasting Defects
The casting is a plate-like structure as a whole, with thin wall thickness and large area. In order to ensure the casting molding, the mold shell needs to be filled with sand and preheated. During the preheating process, the mold shell is heated and softened and its strength is reduced. As shown in the figure below, the inner cavity becomes narrower, and the wall thickness of the casting is slightly smaller. After the bottom plate wall thickness is changed to 0.8 mm, the actual wall thickness will be smaller. In addition, the cooling and solidification speed will increase. The location alloy liquid has solidified before it can flow, resulting in under-casting defects.
After the bottom plate wall thickness is changed to 0.8 mm, the cooling and solidification speed is accelerated, and the slag inclusions in the alloy liquid have no time to float or sink, and the alloy liquid has solidified and stayed in the casting to form slag inclusion defects.
Improvement Measures For Loose And Under-Casting Defects Of Regulating Piece And Sealing Piece Castings
In the process, asbestos is wrapped on the mold shell (as shown in following figure), that is, asbestos is pasted on the bottom plate (preserving the hot node), and the casting is poured out, and the hot node is placed.
No porosity was found, and no porosity was seen on the bottom plate, and the lack of casting defects was also increased by 80%.
Process Improvement Effect Analysis
When smelting pouring castings, during the vacuuming process, the temperature of the mold shell in the melting furnace will drop. After the bottom plate is wrapped with asbestos, the asbestos will heat the mold shell, slowing down the cooling rate of the bottom plate and prolonging the solidification time of the bottom plate, thereby ensuring the alloy The liquid effectively feeds the hot nodes through the bottom plate, and also effectively ensures the bottom plate filling.
Asbestos is a soft material. After asbestos is wrapped, asbestos slows down the extrusion of sand on the mold shell, reduces the deformation of the mold shell, indirectly increases the wall thickness of the bottom plate, and prolongs the filling time of the bottom plate.
After the asbestos is wrapped, the solidification time of the bottom plate is prolonged, so that the inclusions in the alloy liquid can fully float or sink, and the tendency of casting slag inclusion is virtually reduced.
Conclusion
The method of using the mold shell to wrap the asbestos can hinder the extrusion of the mold shell by the sand, reduce the cooling rate of the mold shell, and extend the filling and solidification time of the bottom plate, thereby effectively feeding the hot nodes at the edge of the casting and improving the porosity tendency.
Minghe Die Casting Company Is Custom manufacturer of precision & non-ferrous die castings. Products include aluminum & zinc die castings. Aluminum die castings are available in alloys including 380 & 383. Specifications include plus /- 0.0025 tolerances & maximum molding weight of 10 lbs. Zinc die casting parts are available in standard alloys such as Zamak no. 3, Zamak no. 5 & Zamak no. 7 & hybrid alloys such as ZA-8 & ZA-27. Specifications include plus /- 0.001 tolerances & maximum molding weight of 4.5 lbs.
Please keep the source and address of this article for reprinting: Process Improvement For Loose Thin-Walled Castings And Under-Casting Defects
Minghe Die Casting Company are dedicated to manufacture and provide quality and high performance Casting Parts(metal die casting parts range mainly include Thin-Wall Die Casting,Hot Chamber Die Casting,Cold Chamber Die Casting),Round Service(Die Casting Service,Cnc Machining,Mold Making,Surface Treatment).Any custom Aluminum die casting, magnesium or Zamak/zinc die casting and other castings requirements are welcome to contact us.
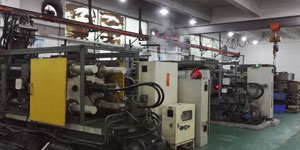
Under the control of ISO9001 and TS 16949,All processes are carried out through hundreds of advanced die casting machines, 5-axis machines, and other facilities, ranging from blasters to Ultra Sonic washing machines.Minghe not only has advanced equipment but also have professional team of experienced engineers,operators and inspectors to make the customer’s design come true.
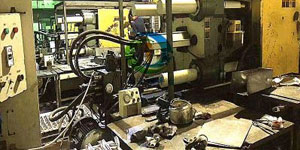
Contract manufacturer of die castings. Capabilities include cold chamber aluminum die casting parts from 0.15 lbs. to 6 lbs., quick change set up, and machining. Value-added services include polishing, vibrating, deburring, shot blasting, painting, plating, coating, assembly, and tooling. Materials worked with include alloys such as 360, 380, 383, and 413.
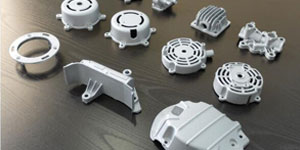
Zinc die casting design assistance/concurrent engineering services. Custom manufacturer of precision zinc die castings. Miniature castings, high pressure die castings, multi-slide mold castings, conventional mold castings, unit die and independent die castings and cavity sealed castings can be manufactured. Castings can be manufactured in lengths and widths up to 24 in. in +/-0.0005 in. tolerance.
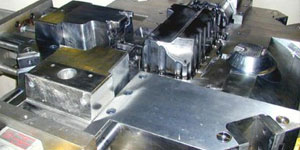
ISO 9001: 2015 certified manufacturer of die cast magnesium, Capabilities include high-pressure magnesium die casting up to 200 ton hot chamber & 3000 ton cold chamber, tooling design, polishing, molding, machining, powder & liquid painting, full QA with CMM capabilities, assembly, packaging & delivery.
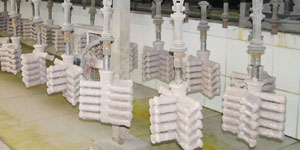
ITAF16949 certified. Additional Casting Service Include investment casting,sand casting,Gravity Casting, Lost Foam Casting,Centrifugal Casting,Vacuum Casting,Permanent Mold Casting,.Capabilities include EDI, engineering assistance, solid modeling and secondary processing.
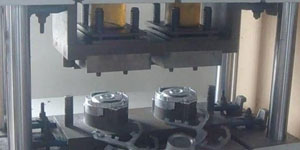
Casting Industries Parts Case Studies for: Cars, Bikes, Aircraft, Musical instruments, Watercraft, Optical devices, Sensors, Models, Electronic devices, Enclosures, Clocks, Machinery, Engines, Furniture, Jewelry, Jigs, Telecom, Lighting, Medical devices, Photographic devices, Robots, Sculptures, Sound equipment, Sporting equipment, Tooling, Toys and more.
What Can we help you do next?
∇ Go To Homepage For Die Casting China
→Casting Parts-Find out what we have done.
→Ralated Tips About Die Casting Services
By Minghe Die Casting Manufacturer |Categories: Helpful Articles |Material Tags: Aluminum Casting, Zinc Casting, Magnesium Casting, Titanium Casting, Stainless Steel Casting, Brass Casting,Bronze Casting,Casting Video,Company History,Aluminum Die Casting |Comments Off