Quenching Quality Defects And Control Encyclopedia
After quenching, the strength, hardness and wear resistance of steel parts can be improved, but the original size or shape of the workpiece will undergo undesirable changes during quenching. This change will become a defect that affects product quality, reduce or avoid These defects, first of all, we must know what defects will be produced by quenching, what are the reasons for their formation, and find the corresponding solutions. Quenching quality defects and control are explained from the following aspects.
1. Quenching distortion
The types of quenching distortion can be divided into two categories, namely volume distortion and shape distortion.
The difference in the specific volume of various structures before and after quenching is the main reason for the volume change. The specific volume of martensite → bainite → pearlite → austenite decreases in order. The workpiece whose original structure is pearlite is quenched into martensite, and its volume swells. If the organization has a large amount of retained austenite, it may shrink the volume. Only workpieces with particularly high precision are considered for volumetric changes caused by uniform expansion of the volume.
Changes in the relative position or size of each part of the workpiece, such as the bending of the plate and rod, the expansion and contraction of the inner hole, and the change of the hole spacing, are collectively referred to as shape distortion. The causes of distortion are as follows:
- (1) The heating temperature is uneven, the formed thermal stress causes distortion or the workpiece is placed in the furnace unreasonably, and creep distortion is often caused by its own weight at high temperatures.
- (2) When heating, as the heating temperature increases, the yield strength of the steel decreases. When the residual stress (cold deformation stress, welding stress, machining stress, etc.) inside the workpiece reaches the yield strength at high temperature, it will cause the workpiece Uneven plastic deformation causes shape distortion and residual stress relaxation.
- (3) Thermal stress and organizational stress formed at different times during quenching and cooling cause local plastic deformation of the workpiece. For workpieces with complex shapes, due to the particularity of their structure, during quenching, the heat and cooling speeds are different, which increases its tendency to deform.
2. Ways and methods to reduce quenching distortion
- (1) The use of a reasonable heat treatment process can effectively reduce distortion. Such as lowering the quenching heating temperature; slow heating or preheating of the workpiece; static heating method, extremely slender and extremely thin workpieces, in order to reduce the impact of salt bath magnetic stirring on the workpiece, power-off heating can be used; the cross-sectional size is small For the workpiece, if the core strength is not high, use rapid heating; reasonably bundle and hang the workpiece; use a reasonable quenching method according to the shape of the work; use hierarchical quenching or austempering; according to the shape characteristics and deformation laws of the workpiece, Before quenching, artificially deform the workpiece in the reverse direction to offset the distortion after quenching.
- (2) Reasonably design parts. For example, the shape of the workpiece should be symmetrical to avoid the disparity of the cross section, thereby reducing the distortion caused by uneven cooling; in order to reduce the expansion or shrinkage of the groove, the grooved workpiece or the opening workpiece that is easily distorted should be made into a closed structure before quenching, such as in Increase ribs at the notch and cut it after quenching; lay out process holes to reduce cavity shrinkage; complex parts adopt a combined structure, that is, a complex workpiece is broken down into several simple parts, and then micro-distorted and quenched respectively, and then assembled; correct Steel is used. For tools with high precision and low heat treatment distortion, micro-distortion steel can be used, and pre-hardened steel can also be used for high-precision plastic molds.
- (3) Reasonable forging and preliminary heat treatment. Severe carbide segregation and banded structure make the quenching distortion anisotropic or irregular. Improving the carbide distribution through forging can not only reduce the distortion, but also improve the service life of the workpiece.
3. Correction of distortion
For the distortion of the parts after heat treatment, cold press straightening, hot spot straightening, hot straightening, tempering straightening, counterattack straightening, shrinkage treatment, etc. can be used.
Cold-pressing straightening is to apply external force to the highest point of the bent workpiece to cause plastic deformation. This method is suitable for shaft workpieces with a hardness of less than 35HRC; hot-spot straightening is to heat the convex part with an oxyacetylene flame, and then Use water or oil to cool quickly to make the heated part shrink under the action of thermal stress. This method is suitable for workpieces with a hardness greater than 35-40HRC; while hot straightening is to quench the workpiece to near the Ms temperature, use the good plasticity and plasticity of austenite Phase change superplasticity makes the distortion to be corrected; tempering correction is to apply external force to the workpiece, and then temper, the tempering temperature is higher than 300 ℃; counterattack straightening is to continuously hit the recess with a steel hammer to produce a small area of the workpiece Plastic deformation; Shrinkage treatment is to heat the swollen workpiece after quenching to 600-700℃ to be red. In order to prevent water from entering the hole, two thin plates are used to cover both ends of the workpiece, and the workpiece is quickly thrown into the water for rapid cooling. The hole shrinks, and after one or more repeated operations, the swollen hole can be corrected.
4. Quenching cracking
Quenching cracking is a cracking phenomenon caused by heat treatment stress exceeding the fracture strength of the material. The cracks are distributed intermittently in series, with traces of quenching oil or salt water on the fracture, no oxidation color, and no decarburization on both sides of the crack. The occasions and reasons for quenching cracks are as follows:
- (1) Material management is chaotic, and high-carbon steel or high-carbon alloy steel is mistakenly used as low- and medium-carbon steel, and water quenching is used.
- (2) Improper cooling. The rapid cooling below the Ms temperature will cause cracking due to high tissue stress. Such as water-oil dual-medium quenching, the residence time in water is long, and the quenching oil contains too much water.
- (3) When the core hardness of the unhardened workpiece is 36~45HRC, quenching cracks are formed at the junction of the hardened layer and the non-hardened layer. The core hardness is less than 36HRC, and the tensile strength at the junction is reduced. The core hardness is greater than 45HRC, indicating that there is a martensite structure, the peak tensile stress is reduced, and the cracking tendency is reduced.
- (4) The workpiece with the most dangerous quenching crack size is prone to quenching cracks. When the workpiece is fully quenched, there is the most dangerous size of quenching cracks, its diameter is: 8-15mm when quenching in water; 25-40mm when quenching in oil. When the size is smaller than the most dangerous quenching cracking size, the temperature difference between the core and the surface is small, the hardening force is small, and it is not easy to crack. On the contrary, it increases, but the tensile stress peak is far away from the surface, and the quenching cracking tendency decreases instead.
- (5) Severe surface decarburization is easy to form network cracks. The martensite of the decarburized layer has a small specific volume and is liable to form network cracks under tensile stress.
- (6) For deep-hole workpieces with smaller inner diameters, the inner surface is cooled much less than the outer surface, and the residual thermal stress is small. The residual tensile stress is larger than the outer surface, and the inner wall is easy to form parallel longitudinal cracks.
- (7) Quenching heating temperature is too high, causing coarsening of crystal grains, weakening of grain boundaries, reduced brittle strength of steel, and easy cracking during quenching.
- (8) Without intermediate annealing before repeated quenching, the tendency of overheating is high, the quenching stress of the previous item cannot be completely eliminated, and the surface decarburization caused by repeated heating will promote quenching cracking.
- (9) Large-section high-alloy steel workpieces are not preheated or heated too fast during quenching and heating, and the thermal stress or structural stress during heating increases, causing cracking.
- (10) Poor original structure, such as poor quality of high-carbon steel spheroidizing annealing, its structure is lamellar or punctate pearlite, with high thermal tendency; grain coarsening, high martensite content, and high quenching cracking tendency.
- (11) Raw material microcracks, non-metallic inclusions, and severe carbide segregation tend to increase quenching cracking. For example, non-metallic impurities or severe carbides form a strip along the rolling direction. Due to the anisotropy of mechanical properties, their transverse properties are 30% to 50% lower than their longitudinal properties. The distribution direction of metal inclusions or carbides is longitudinal cracks.
- (12) Forging cracks expand during quenching. When quenching and heating in the flexible furnace, the cracked fracture surface has black oxide scale, and there is a decarburized layer on both sides of the crack.
- (13) Overburning cracks. The cracks are mostly networked, and the grain boundaries are oxidized and melted.
- (14) For steel with low hardenability, when clamped and quenched with pliers, the clamped part is quenched slowly and has a non-martensitic structure. The jaws are located at the junction of the hardened layer and the non-hardened layer, and the tensile stress Large and easy to crack.
- (15) High-speed steel and high-chromium steel are quenched in stages, and the workpiece is not cooled to room temperature, and it is eager to clean (because of rapid cooling below Ms) causing cracking.
- (16) The thermal stress and the structural stress formed by the cryogenic treatment due to the rapid cooling and heating are relatively large, and the brittle strength of the low-temperature material is low, which is easy to produce quenching cracking.
- (17) If it is not tempered in time after quenching, the micro-cracks inside the workpiece expand to form macro-cracks under the action of quenching stress.
5. Measures to prevent quenching cracking
- (1) Improve the structure of the workpiece. Strive to be uniform in cross-section, and there should be rounded transitions at different cross-sections to minimize non-through holes and sharp corners to avoid cracking caused by stress concentration.
- (2) Reasonably choose steel. The workpiece with complex shape and easy to crack should be made of alloy steel with high hardenability, so that the quenching medium with slow cooling rate can be used to reduce the quenching stress.
- (3) The raw materials should avoid micro cracks and serious segregation of non-metallic inclusions and carbides.
- (4) Pre-heat treatment should be carried out correctly to avoid normalizing and annealing structure defects.
- (5) Correctly select heating parameters.
- (6) Reasonable selection of quenching medium and quenching method.
- (7) Partially bandage the easily cracked parts of the workpiece, such as sharp corners, thin walls, holes, etc.
- (8) After quenching, the easily cracked workpiece should be tempered in time or tempered with temperature.
6. Insufficient hardness
The surface hardness of the workpiece after quenching is lower than the quenching hardness value of the steel used, which is called insufficient hardness.
Reasons For Insufficient Quenching Hardness
- The cooling capacity of the medium is poor, and the surface of the workpiece has non-martensitic structures such as ferrite and troostite
- The quenching heating temperature is low, or the pre-cooling time is long, the quenching cooling rate is low, and the non-martensitic structure appears
- Insufficient heating of hypoeutectoid steel has undissolved ferrite
- When carbon steel or low-alloy steel is quenched with water-oil dual medium, the residence time in water is insufficient, or the residence time in the air is too long after the parts are lifted out of the water
- The hardenability of steel is poor, and the size of the working section is not large, and it cannot be hardened.
- High-carbon high-alloy steel has high quenching temperature and excessive retained austenite
- The isothermal time is too long, causing austenite to stabilize
- Surface decarburization
- The moisture content in the nitrate or alkaline bath is too small, and non-martensite such as troostite is formed during stage cooling
- The alloying elements are internally oxidized, the surface hardenability is reduced, and non-martensite such as troostite appears while the internal structure is martensite
Control Measures
- Use quenching medium with faster cooling; appropriately increase the quenching heating temperature
- Under the premise of ensuring normal quenching heating temperature; reduce pre-cooling time
- Strictly control heating temperature, moisturizing time and furnace temperature uniformity
- Strictly control the staying time of parts in the water and operating specifications
- Use steel with good hardenability
- Reduce the quenching heating temperature or adopt cryogenic treatment
- Strictly control the classification or isothermal time
- Use controllable atmosphere heating or other anti-decarbonization measures
- Strictly control the moisture in the salt bath and alkaline bath
- Reduce the content of oxidizing components in the furnace atmosphere; select quenching medium with fast cooling speed.
7. Soft Spots
After quenching, the phenomenon of low hardness in the local area of the workpiece surface is called soft spot. Carbon steel and low alloy steel are usually prone to quenching soft spot due to poor hardenability.
Causes Of Soft Spots
- The bubbles on the surface of the workpiece were not broken in time during quenching, resulting in a decrease in the cooling rate at the bubbles and a non-martensite structure
- The local oxide scale, rust spots or other attachments (paint) on the working surface did not peel off during quenching, so that the cooling rate was reduced
- The original structure is not uniform, with serious band-like structure or carbide segregation
Control Measures
- Increase the relative movement of the medium and the workpiece; control the water temperature and impurities in the water
- Clean the surface of the workpiece before quenching
- Raw materials are forged and pre-heated to homogenize the structure
8. Surface corrosion-pitting
After the workpiece is quenched, pickled or sandblasted, the surface shows dense dot-like pits called pits, which are formed by corrosion of the medium. The pits make the workpiece lose its luster and affect the surface finish.
There are many reasons for the formation of pitting, but we can reduce this defect during work, such as reducing the sulfate content in the salt bath to avoid corrosion of the matrix; also reducing the nitrate temperature; the high temperature quenching heating workpiece is pre-cooled Then put it into the solution to avoid the decomposition of nitrate; when the high temperature is locally heated, the non-heated part is salt-immersed to coat it with a solid salt shell to prevent pitting corrosion.
Please keep the source and address of this article for reprinting:Quenching Quality Defects And Control Encyclopedia
Minghe Die Casting Company are dedicated to manufacture and provide quality and high performance Casting Parts(metal die casting parts range mainly include Thin-Wall Die Casting,Hot Chamber Die Casting,Cold Chamber Die Casting),Round Service(Die Casting Service,Cnc Machining,Mold Making,Surface Treatment).Any custom Aluminum die casting, magnesium or Zamak/zinc die casting and other castings requirements are welcome to contact us.
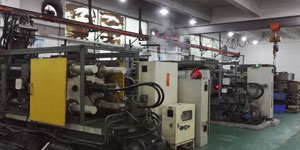
Under the control of ISO9001 and TS 16949,All processes are carried out through hundreds of advanced die casting machines, 5-axis machines, and other facilities, ranging from blasters to Ultra Sonic washing machines.Minghe not only has advanced equipment but also have professional team of experienced engineers,operators and inspectors to make the customer’s design come true.
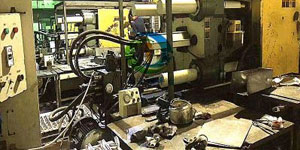
Contract manufacturer of die castings. Capabilities include cold chamber aluminum die casting parts from 0.15 lbs. to 6 lbs., quick change set up, and machining. Value-added services include polishing, vibrating, deburring, shot blasting, painting, plating, coating, assembly, and tooling. Materials worked with include alloys such as 360, 380, 383, and 413.
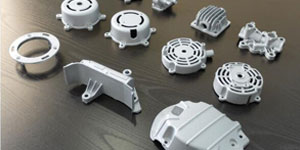
Zinc die casting design assistance/concurrent engineering services. Custom manufacturer of precision zinc die castings. Miniature castings, high pressure die castings, multi-slide mold castings, conventional mold castings, unit die and independent die castings and cavity sealed castings can be manufactured. Castings can be manufactured in lengths and widths up to 24 in. in +/-0.0005 in. tolerance.
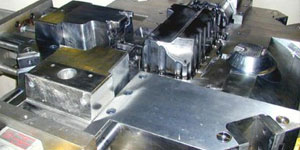
ISO 9001: 2015 certified manufacturer of die cast magnesium, Capabilities include high-pressure magnesium die casting up to 200 ton hot chamber & 3000 ton cold chamber, tooling design, polishing, molding, machining, powder & liquid painting, full QA with CMM capabilities, assembly, packaging & delivery.
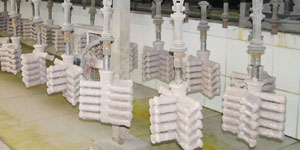
ITAF16949 certified. Additional Casting Service Include investment casting,sand casting,Gravity Casting, Lost Foam Casting,Centrifugal Casting,Vacuum Casting,Permanent Mold Casting,.Capabilities include EDI, engineering assistance, solid modeling and secondary processing.
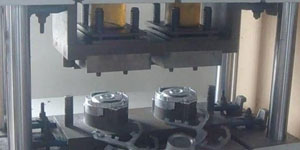
Casting Industries Parts Case Studies for: Cars, Bikes, Aircraft, Musical instruments, Watercraft, Optical devices, Sensors, Models, Electronic devices, Enclosures, Clocks, Machinery, Engines, Furniture, Jewelry, Jigs, Telecom, Lighting, Medical devices, Photographic devices, Robots, Sculptures, Sound equipment, Sporting equipment, Tooling, Toys and more.
What Can we help you do next?
∇ Go To Homepage For Die Casting China
→Casting Parts-Find out what we have done.
→Ralated Tips About Die Casting Services
By Minghe Die Casting Manufacturer |Categories: Helpful Articles |Material Tags: Aluminum Casting, Zinc Casting, Magnesium Casting, Titanium Casting, Stainless Steel Casting, Brass Casting,Bronze Casting,Casting Video,Company History,Aluminum Die Casting |Comments Off