Quick Identification Method Of Nodular Cast Iron Spheroidizing Quality
Inspection before furnace
The inspection before the furnace of ductile iron is an indispensable part of the production process, and it is directly related to the quality of ductile iron parts. The spheroidization of molten iron can be judged timely and accurately, and measures can be taken quickly to control the quality of nodular cast iron. Misjudgment in front of the furnace will cause a large number of castings to be scrapped and waste molding man-hours. Therefore, timely and accurate judgment of spheroidization in front of the furnace is much more important than inspection after the furnace. There are several methods commonly used in actual production to check the spheroidization of molten iron before the furnace.
1 Surface crust and flame judgment method
Rare earth magnesium nodular cast iron has low magnesium content and rare earth elements. The surface of molten iron is different from pure magnesium nodular cast iron. There is not so much oxide scale on the surface, and the flame is not so powerful and powerful. However, when 1/3 of the molten iron is added, magnesium light and white flame will escape from the liquid surface, which is like a candle. According to the number and height of the flame, the spheroidization situation and the residual amount of magnesium are judged. The higher the flame and the more powerful, it indicates that the spheroidization is good. Especially when pouring, the hot metal can be seen from the molten iron flow, if the height reaches 25~ffice:smarttags" />50mm, the spheroidization is good; if the flame is less than 15mm, the spheroidization is poor. From processing On the surface of the molten nodular cast iron, an oxide film is formed and there are silver-white rolling bright spots, which means that the spheroidization is good. But if the oxide film is too thick, it means that the temperature of the molten iron is low.
2 Triangular test block method
At present, it is a commonly used method to judge the spheroidization by observing the test block. The test blocks used by various factories have many shapes and different sizes, and most factories use triangular test blocks. According to the production characteristics of our factory, the size and thickness of the castings, the cross-sectional area size of the triangular test block is 12.5mm (bottom) × 50mm ((height). Some factories use round test blocks, such as Ф15mm, Ф25mm, Ф30mm. Iron. After liquid treatment is completed, use a sampling spoon to discharge the liquid from the surface of the molten iron 200mm below the surface and pour it into a test block and cool it to dark red before water quenching. The outer circle of the good ball is much larger than the gray cast iron. The appearance is clean, bright and very sandy. The vertical cast triangle test block has shrinkage on both sides of the horizontal cast block top surface or the shrinkage test block on both sides. After cooling and knocking off, the spheroidization is good, and it is silver-white or silver-gray porcelain. The tip is clear and the white mouth is loose in the middle. Silver-white color with radial pattern, high spheroidizing agent will produce more carbides. At this time, when the test block is put in, it will make a "patting" crackling sound. The test piece will break when lightly tapped and the newly tapped calcium carbide will have a very thick mouth. Odor, therefore, it is best to float silicon during pouring. If the mouth is silver-grey and there are evenly distributed small black spots, it is colored crystal if broken.
Note:
- 1) The spheroidized triangle test block will have the smell of calcium carbide immediately after being interrupted by quenching.
- 2) The depth of the white mouth is related to the type and type of ductile iron and the composition of molten iron. Therefore, no data is given in the table. The white mouth depth of rare earth magnesium ductile iron is not very obvious.
3 Judgment of the pouring process
- (1) After the molten ductile cast iron is poured into the mold, if the sprue cup has been recessed downwards and the surface is very smooth, it indicates that the spheroidization is good; if the upper part of the sprue cup has a hard shell, it will also be recessed. The molten iron temperature is low.
- (2) During the pouring process, there are pits (pits) in the round lentils splashed on the surface of the sand mold, indicating that the spheroidization is good.
4 Black edge identification method
After the ball is processed, use a sample spoon to pour a test block with a thickness of about 10mm, and cool it to dark red. After quenching and breaking, if a black edge is found on the upper surface of the test block, it means that the spheroidization is not good, and the thicker the black edge, the ball The worse the melting, the recession will occur. At this time, if the temperature of the molten iron is high, the alloy can be added. It can also be seen from the test block that if the periphery of the test block is arc-shaped with a depression in the middle, and some wrinkles are present, it also indicates that the spheroidization is good; if there are wheat-skin-like dots on the upper surface of the test block, it indicates The molten iron is oxidized and is easy to decay. In this case, the furnace should be modified.
5 Observe the solidification status of molten iron
After the spheroidization is completed, take out a small amount of molten iron and pour it into a Ф30mm cylindrical metal mold. Observe the appearance of molten iron from the surface during solidification, and judge the spheroidization of the molten iron according to the amount of molten iron. Good spheroidized molten iron exhibits a large graphite expansion force during solidification. The surface of the molten iron drops a little at the beginning of solidification, and a small amount of molten iron gushes out of the case after the surface is encrusted; while the poorly spheroidized molten iron The number of gushes from the surface is small.
6 Quick metallographic observation in front of the furnace
The above-mentioned methods all use certain characteristics of ductile iron to indirectly judge the spheroidization, but the various conditions in production vary greatly, and the methods described have limitations, and the rapid metallographic observation in front of the furnace can avoid many factors. Interference, directly observe the spheroidization situation.
Metallographic inspection after furnace
- (1) The post-metallographic inspection mainly observes the microstructure such as graphite morphology and sub-featured metal matrix structure inclusions. Through metallographic analysis, the amount of broken parts can be used as a basis for improving the casting quality.
- (2) The chemical composition analysis of rare earth magnesium spheroidal graphite cast iron can also be said to be a detection method. If a problem is found, the batching personnel can make appropriate adjustments to avoid major quality problems. In addition, there are testing of mechanical properties and non-destructive testing of ductile iron parts.
Conclusion
For the inspection of ductile iron, the traditional inspection method of "after-furnace analysis" should be changed to "real-time online inspection." As a large and medium-sized enterprise, the use of advanced inspection methods at home and abroad to accurately determine the spheroidization situation is a reliable guarantee for the improvement of casting quality. However, for small enterprises, especially the rapidly emerging township enterprises, it is still of practical significance to use a certain characteristic of ductile iron to indirectly judge the spheroidization.
Please keep the source and address of this article for reprinting: Quick Identification Method Of Nodular Cast Iron Spheroidizing Quality
Minghe Die Casting Company are dedicated to manufacture and provide quality and high performance Casting Parts(metal die casting parts range mainly include Thin-Wall Die Casting,Hot Chamber Die Casting,Cold Chamber Die Casting),Round Service(Die Casting Service,Cnc Machining,Mold Making,Surface Treatment).Any custom Aluminum die casting, magnesium or Zamak/zinc die casting and other castings requirements are welcome to contact us.
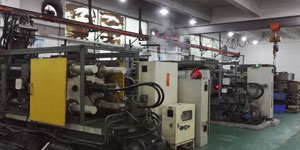
Under the control of ISO9001 and TS 16949,All processes are carried out through hundreds of advanced die casting machines, 5-axis machines, and other facilities, ranging from blasters to Ultra Sonic washing machines.Minghe not only has advanced equipment but also have professional team of experienced engineers,operators and inspectors to make the customer’s design come true.
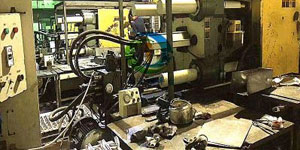
Contract manufacturer of die castings. Capabilities include cold chamber aluminum die casting parts from 0.15 lbs. to 6 lbs., quick change set up, and machining. Value-added services include polishing, vibrating, deburring, shot blasting, painting, plating, coating, assembly, and tooling. Materials worked with include alloys such as 360, 380, 383, and 413.
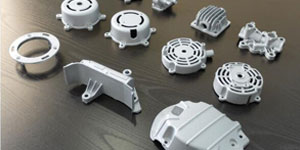
Zinc die casting design assistance/concurrent engineering services. Custom manufacturer of precision zinc die castings. Miniature castings, high pressure die castings, multi-slide mold castings, conventional mold castings, unit die and independent die castings and cavity sealed castings can be manufactured. Castings can be manufactured in lengths and widths up to 24 in. in +/-0.0005 in. tolerance.
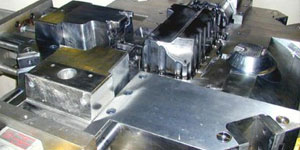
ISO 9001: 2015 certified manufacturer of die cast magnesium, Capabilities include high-pressure magnesium die casting up to 200 ton hot chamber & 3000 ton cold chamber, tooling design, polishing, molding, machining, powder & liquid painting, full QA with CMM capabilities, assembly, packaging & delivery.
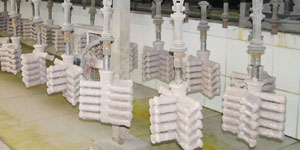
ITAF16949 certified. Additional Casting Service Include investment casting,sand casting,Gravity Casting, Lost Foam Casting,Centrifugal Casting,Vacuum Casting,Permanent Mold Casting,.Capabilities include EDI, engineering assistance, solid modeling and secondary processing.
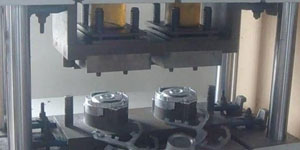
Casting Industries Parts Case Studies for: Cars, Bikes, Aircraft, Musical instruments, Watercraft, Optical devices, Sensors, Models, Electronic devices, Enclosures, Clocks, Machinery, Engines, Furniture, Jewelry, Jigs, Telecom, Lighting, Medical devices, Photographic devices, Robots, Sculptures, Sound equipment, Sporting equipment, Tooling, Toys and more.
What Can we help you do next?
∇ Go To Homepage For Die Casting China
→Casting Parts-Find out what we have done.
→Ralated Tips About Die Casting Services
By Minghe Die Casting Manufacturer |Categories: Helpful Articles |Material Tags: Aluminum Casting, Zinc Casting, Magnesium Casting, Titanium Casting, Stainless Steel Casting, Brass Casting,Bronze Casting,Casting Video,Company History,Aluminum Die Casting |Comments Off